丰田式生产管理精要 1.由人和机器的组合来做工作,并经由此种方式掌握生产性是主要的重点 2.现场的作业必需让外行人也能进行作业,现场不需要专业人员,因为不能依靠专业人员的技术力量来推动现场. 3.那时以少数的人员而增加生产力一事,是丰田实力得以提高的重要理由. 4.人是不容易纳别人的意见的,不过对于有实际绩效的事却极易听取. 5.将泰勒与福特两个方式重新组合后称为[丰田生产方式] 7.所谓教导,不是只问部属是否了解而已,看了部属的动作却无法立即判断是不可以的,在改善方面,改善过一次的地方再做一次改善是很重要的. 8.阅读仍是有用的,但要试着去执行. 9.特别是脚的动作非常重要.若脚只是随兴地走动时,作业的执行方式一定会错误,总之若有什么疑问,对什么感到困惑,或想到什么重要的线索时,最好立即到现在去.因为现场的确是学习研究的好地方!看了现场之后,即能判断所考虑的事什么是好的,什么是不好的;这些又会再次成为新的问题点,所谓工作,不外乎就是这么一回事. 10.现今学者都称丰田生产方式是属于[后工程领取方式],但是实上,当初是为了想买东西才有这种想法出现,为了要以[广告牌]来取代金钱,所以有[广告牌方式]的诞生. 11.同时进行的事称同步化,广告牌称为SMC 12.某条生产线非常忙碌,但隔壁的生产线却没有做事,这种情形到底是那里出了问题呢?这就是平准化思想的出现. 13.变换程序要花很多时间是因为最初是以斥责的方式,想要员工照着去做,可是老板向来被认为是很可怕的,再加上教导的方式很糟糕,所以一直无法达成(微笑),我想大概就是那个时候,听说新乡重夫老师的教学方式很好,所以也有请他来教. 14.即使只有总公司的工厂将所有的机器时间改为单一程序,也要花上数年的时间, 15.所谓[自动].,即是指[附有停止,动作的自动机器].带有人字旁的自动化,使自动停止装置的意义得以廓清,实在相当了不起 16.现在已经不再是物质缺乏的时代,就必须将生产系统从过去那种以生产为中心的观念,并逆转生产流程,偏偏一般人仍无法理解此一概念. 17.只在需要时,必要地制造顾客所需要的产品----这种观念无法获得普遍的了解. 18.若不从根本上改变旧想法,而只是套用新想法的话,是不会有结果的,特别是经营者的态度,常能决定结果的好坏. 丰田生产方式是企业永远的课题 1.目前各家企业正拼命为保住人力而头破血流,但事实上,工作现场却仍旧存在着相当多的多余能力,问题就出现在那些不知活用人力的监督人员身上.”工作的流畅感,作业一贯化. 2.令人无法理解的最大问题则是大家只将目光集中在现状的问题上,而忘了丰田生产方式的本质,认为在多种少量的时代里,就推进丰田生产方式;物质充裕时代里,就学习丰田生产方式,好像只要这样就准没错一样. 3.丰田生产方式目标,我们实在不该将广告牌方式与丰田生产方式当做单纯的手法,而应该确实掌握住大野先生的思想以及潜在丰田生产方式中,可以用来维持企业发展的原点. 4.丰田生产方式,一开始就要付诸行动,不管你做了多少时间观测,苦心地研究各种作业动作,只在缺乏对浪费应有的认识,便会阻碍了现场的改革作业.一旦发现了浪费便要有因应的意识,并且立即采取行动.只想在教室里学习,宛如岸上练游泳一般,只会有不切实的认识罢了. 5.已从经营学中消失的[库存管理]与[交期管理] 观念:彻底理解丰田生产方式的字典 1.制造技术,是指综合所有的技术,包括基材的选择方法,生产流程(生产线,设计),加工的方法,作业程序,设备等,以提高经营效率的生产现场技术;并以此技术如何做出符合客户所要求的质量且又能降低生产成本的一种挑战. 2.丰田生产方式:JIT 3.动作:在现场作业里,像先拿好东西,改装,找东西等动作,与提高附加价值这件事并无关联.我们将这些动作简单地称之为[动作].日常执行的生产作业分为[浪费的作业]和[有价值的作业. 4.工作:能提高附加价值的人类动作.动作=动作+人类的智慧 5.五次为什么:5W1H(when,why,who,what,How)什么人,什么时候,在什么地方,做什么,怎么做,为什么要做,花多少钱. 6.工数减低和偷工减料:所谓工数低减是从制造方法中省略不必要的动作,而偷工减料则是指应该做的事却不去做. 7.目视管理:企业经营所需要的所有东西,很清楚的区分为是正常的还是异常,以便将现场的所有东西都能够标准化.要达到目视管理标准化的工具而言,有4S,警示灯,生产管理板,工程进度表,标准作业组合票. 8.平准化: 9.周期表. 10.单品流程:为达成及时生产是,在统一加工上是无法符合每位客户之需求的..从材料到制品,尽可能地将每个流程都要标明出来,以考虑微少快速的工程制作方法. 11.整流,乱流:整流是指制造过程非常清楚,产品依序生产,没有停滞情形,之后即使发现有不良产生,也能了解是在什么时候,哪里,为什么发生的生产线.乱流是指因制造途中的堆积,使得生产线的制造顺序絮乱不清. 12.大量生产:将同样的品种在同一个时候集中生产的量称为生产单位,在生产时,尽可能地将生产单位放大,生产效率会愈好谓之[大量生产],小量生产:生产单位过大,在平准化生产时便会有困难,因为大量生产,无法满足客户的要求,所以尽可能地将生产单位放小;可能的话,一个一个去做更好谓之[小量生产]. 13.50*1-1*50:50*1的意思是指将生产50个的东西,集中一次办完.1*50是意思是指将生产相同50个的东西,不集中办理,而分为50次逐一生产. 14.稼动率:在一天的时间内,使用此机械机小时所生产东西的比率,如A机器一天8小时中有做100个零件的加工能力,但结果只做了70个,那么机器的稼动率只有70%. 15.可动率:在想要使用机器,设备的时候,经常都能保持正常运转的状态的比率谓之可动率. 需要时立即运转=可动率100% 16.个别的效率 17.全体的效率 18.真正的能率:只做能销售出去的. 19.表面上的能率:制造出多于客户所需要更多的仓库了. 改善:彻底理解丰田生产方式的字典 1.分析手法:工程分析----路径分析----流程分析----要素作业分析----动作分析----设备要因分析 2.浪费:丰田生产方式,简言之是种彻底排除浪费的方式,由于做到无浪费,结果自然可提高生产性. 3.库存的浪费,生产过剩的浪费:过度的生产造成库成的浪费在丰田生产方式里被称为最恶劣的浪费. 4.空间的浪费:
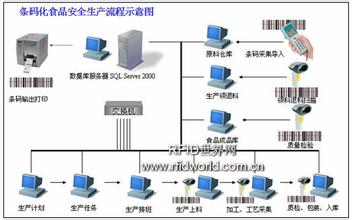
5.搬运的浪费:可以说所有作业始于搬运. 6.工作物(加工)的浪费:当你认为目前的作法是最理想时,可能其中就有浪费的成份. 7.动作的浪费:在制造过程没有附加价值的动作,设备,机器运转等都是. 8.改善的程序:循着发现间题,改善,标准作业而形成一个[改善的循环]. 9.显在浪费与潜在浪费:空闲与加工疏漏等这种一看就知道的浪费,称为显在的浪费.另一种是乍看好像在工作的样子,细看却是一些无关紧要的作业,称为潜在的浪费. 10.表准作业:巨细不遗的将事实作一正确的记录,这件事对丰田来说,是相当受到重视的,简称为[表准化]. 11.标准作业:为了制造出物廉价美的物品而设的一种基准. 12.标准作业的条件:(1)以人的动作为中心.(2).重复的进行作业. 13.循环时间----标准作业三要素之一. 14.作业顺序----标准作业三要素之二 15.标准间隔----标准作业三要素之三 16.工程别能力表现:标准作业组合表 17.标准作业与作业标准 18.标准作业表 19.标准作业的制作程序:(1)设备能力,(2)作业研究就非常的重要,(3)零件别能力表,(4)日产必要量与循环时间,及循环时间内人与机械的动作应如何分配的问题,(5)标准作业组合表.(6)以人的动作为中心制作标准作业表. 20.标准作业指导书 21.作业的教法 22.标准作业与改善 23.标准作业与质量不良. 24.作业改善与设备改善.