笔者近年来参与了大量的螺纹钢轧钢设备的制造,对这些设备的工作原理很了解,通过对不同机型实现原理的工作机构进行比较,发现716B-390短应力轧机在消除轧辊径向间隙方面采用液压缸方案(附图1)很不合理,该轧钢机机型最早从达涅利公司引进,后慢慢经过国产化改造,形成了现在以国产件为主,进口件为辅的新机型,大大降低了生产成本。同时为轧钢厂节约了大量设备采购资金,成为了此类生产线的优选设备。 一、液压缸制造存在的缺点 该设备的轧辊轴消除径向间隙采用液压缸机构来实现,成了一个短板。据客户反映,该液压缸连续作业半年左右,就会出现漏油,缸壁拉伤的现象,严重时只能将整机报废。本人听到客户反馈的信息后,开始着手对该设备进行改造,以期能彻底解决这一问题。经分析发现,采用液压缸机构存在以下缺点; 设备制造工艺方面。 制造工艺受机架空间限制,该液压缸为非独立机构,缸体材料与机架相同,为20钢,受材料及加工工艺限制,缸体硬度和光洁度都难达到要求,后来我们就给该缸体内部镶嵌了一个壁厚为3mm材料为40Cr的薄壁套,虽使得使用寿命有所延长,但薄壁套的加工和镶嵌又是一个难题。成功率比较小,效果不是很理想。 使用环境方面。由于轧钢机在高温,高湿,振动大的工作条件下进行连续作业。因此密封件受高温,腐蚀环境很容易老化。振动使得活塞杆与导向套及缸体内壁不均匀磨损增大,导致缸体拉伤。 二、 液压缸制造改进方法 有没有一种更好的办法呢?把弹性胶体平衡装置应用到该设备上成了目前最好的办法。弹性胶体最显著的优点为:在一个单件装置内,弹性胶体能够按照所需比例来提供能量消耗和能量储存,从而消除了振动,吸收了外部冲击能量。它具有显著的热稳定性和化学稳定性,不容易老化。结构紧凑,承载能力大,操作方便,不需要调整和维修,不需要液压设备,也就省去了液压系统维修的工作量。此方案一经提出,得到了客户和领导的一致肯定。 怎样利用机架现有空间对在线生产设备进行改造呢?首先要计算每一个平衡装置的平衡力,通常轧辊和轴承座的组合重量由4个平衡装置支撑。计算方法为:Fmin=K×(G1+G2),其中Fmin为每个弹性胶体平衡装置所需承受的最小反力,K为平衡系数,一般取1.2~1.5;G1为上工作辊及轴承座装配总重量;G2为传动端接轴的总重量。经计算,每个平衡装置的最小反力为400kgf。再充分利用空间结构我们设计了一种弹性胶体平衡装置。(如图2) 后与北京一家专门生产弹性胶体平衡装置的厂家联系,希望能按我们提供的图纸生产出样品以供试用,该厂家积极配合对他们的一款产品进行了改造,制造出了符合图2所示的平衡装置样品提供给我方试用。 将图1中液压缸部分的活塞杆、端盖及油路部分全部拆掉,将该平衡装置安装于机架原来液压缸移走后深度为99、直径为φ40的孔内,如下图3
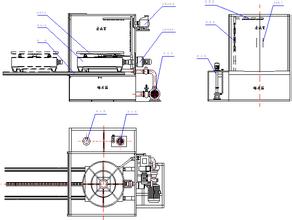
该装置在生产现场试车时,随着上轴承座向上移动,弹性胶体平衡装置按位移逐步伸长支撑上轴承座,直至到达最大行程。随着上轴承座下移,平衡装置逐渐被压缩直至达到最小行程。始终使轧辊保持工作辊缝,消除了辊箱径向间隙。经反复试验在空载状态下完全达到了使用要求,效果非常好。通常该装置的使用年限为1~2年。大大延长了轧机的使用寿命。 当然随着该类型轧机的改造力度增大,这种弹性胶体平衡装置的制造成本就会下降,有利于进一步普及使用。