五. 物料控制:独立需求库存的补充新物品的首次订货是库存管理的特殊情形。这类物料管理的原理与技法在第6
章讨论。本章讨论常规使用中的物料被不断地补充或定期成批地补充的情形。
第3章的EOQ概念回答每一次发出补充订单应订货多少的问题。回答这一问
题中,订货成本要同库存持有成本相平衡以给出最小的总成本。在库存控制中,另
一必须回答的基本问题是该补充订单必须在何时发出。回答这个问题中,库存投资
成本必须同所希望的客户服务水平或缺货成本相平衡。显然,如果补货订单不能及
时发出,物料将不会及时到货,在新批收到之前就会把剩余物料用完。反之,如果
订单发出过早,库存将过高。
由于重订货技法的选择最终地确定所提供的客户服务水平,这一决定通常对管
理人员比批量的决定要重要得多。不良的客户服务通常比订货或库存成本更快而且
更有力地引起管理人员的注意。实际上,这一事实的后果是作出的决定往往以高库
存为代价大大地偏向于客户服务。
原理15.正确地回答一物品何时需要的问题比确定要订多少货重要得多。
任何库存控制系统,不管多么简陋,总有一些内在的决策规则。每周购买一次
食品的主妇按照告诉她们何时重新订货的直觉规则来确定她的购物单。其中有些规
则是相当切合实际的。主妇多半能相当准确地预报每餐要使用的肉类的数量,并多
半在需要重新购买时用完上周的肉类的最后余量。另一方面,化妆纸可能服从一非
常无规律的需求──也许取决于家中有无某一成员伤风感冒。主妇可能决定在衣橱
里应当常备一盒擦面纸。当这一盒被打开时,她将在每周购物时购买另一盒。香草
精难得一用,当用完时,该主妇可能决定暂时不买直到下次计划烘烤什么时再说。
减价出售的廉价货的采购则要受有没有钱的限制,也要受水箱、冷冻室或食品柜存
储容量的限制。
这些是实际上很有效的简单规则,虽然它们可能甚至得不到始终如一的应用。
在购买食品与杂货时,主妇通常不注意库存(食品与杂货)的投资同缺货的机会之
间的平衡。倘若她偶而让一常用物品用光了,由于商店就在邻近或可从邻居暂借一
下,这不方便通常是小的。
对大多数日常生活中作出的库存决定这是真的。这类日常用的重订货系统可以
非常松弛,因为其提前时间短库存投资小,即使缺货时所带来的不方便也较小。在
企业中有许多库存──例如办公用品──可以相当成功地用类似的简单决策规则来
加以控制。
然而,还有许多其它物品,它们涉及巨额的库存投资,万一缺货要付出极高代
价或补货提前时间很长。为了恰当地控制这些库存,可以用一些高效率的重订货方
法。它们有许多形式,但通常同下列五种方法之一有关:
1、两箱法:
此系统中,一特定物品的存货以某一预先确定的数量被放在一边(往往放在分
开的第二个箱子中)不予接触,直到该物品的主要存货被用完。当后备供应量被打
开时,即有通知书被送到库存控制办公室并发出一补货订单。(详见“两种简单订
货方法”)
2、目视评审法:
定期地用目视法核对存货水平,每次评审后在需把存货水平恢复到某一预先确
定的现有库存与已定购量之和的最大值的场合就发出补货订单。(详见“两种简单
订货方法”)
3、订货点法(固定订货量──可变订货周期制):
当提货使一物品在永续盘存记录上的库存下降到一预先确定的叫做订货点的水
平时,发出补货订单(通常订货量为预先计算好的EOQ)
4、定期评审法(固定周期──可变订货量制):
在定期评审中,库存记录被定期地评审,也许每周一次或每月一次,并定期地
订货使现有库存加上已订货量的库存总量恢复到预先确定的最高水平。(详见“定
期评审技法”)。
5、物料需求计划(MRP):
在MRP中,物料按能满足使用物料的物品的预先制订的生产计划所需的数
量与交货日程来订货。(详见第6章)。
所有这些方法在概念上都是紧密联系的。显然,例如两箱法,虽然它并无库存
记录,却同订货点法非常相似,因为第二只箱子里存放的就是订货点数量。同样地,
众所周知的极小与极大法只是订货点法的一种变态。该极小值实际上就是订货点,
而极大值就是订货点加上订货量。然而,订货点法在工业的库存控制中并未获得普
遍的应用。事实上,这一技法──以及刚才列出的第1到第4种有关的方法──对
成品库存与库存中持有的维修零件有极好的应用,例如,在该物品的需求倾向于连
续的而且不依赖于任何其它库存物品的场合。然而,在需求倾向于间歇的而且需求
量的变化取决于一更高层装配件的需求水平的场合,补充这种组件与子装配件的库
存,通常以使用MRP更为有效。上述重订货技法都将进一步讨论,本章讨论前4
种。
订货点法被深入地讨论,因为它为用来对付重订货系统中不确定性的方法
提供了最好的例子。MRP将在第6章叙述。
在所有这些讨论中,需求是指在一给定期间中对一物品的总需要量。提前期是
从确定必须发放一份补货订单起到该订单中的物料被收进存货并可供使用为止所经
历的时间。这是一物品最易受缺货伤害的期间,因为库存正处于最低点。
订货点法的基础
订货点法,包括对提前期中需求的估计,加上一些储备存货用来对付无论需求还是提前期都不能被肯定地预报这一事实。假设使用率是固定的
,库存将沿着斜线下降,达到订货点时发出一补货订单,订货量为EOQ,如垂直
的虚线所示。在提前期中,库存继续下降,到提前期末,收到了补充订货;于是库
存增加了EOQ,库存的升降循环又重新开始。另一必要的假设是补货是即时完成
的。
不幸的是,在大多数实际的库存情况中,无论提前期还是需求都不能准确地预
报。其结果是,简单地根据提前期中的平均需求来确定的订货点将不能为防止缺货
提供足够存货,因为需求的波动有一半时间要超过平均值。于是,一个主要问题就
是在订货点法中需要配备多大的储备存货。
头两个周期都未触及储备存货。然而,在第三个周期,使用率变大了,如图中
更陡的斜线所示。由于这一较高的需求,在收进新的供应量之前,库存掉进了储备
存货。倘若需求增长得更多或提前期变得更长,则库存可能降低到零──这就会产
生缺货。
这一技法有下列注意事项:
1、订货量(诸EOQ)通常是固定的,而且仅当预期有显著的需求变化时才
被重新计算。
2、实际上,订货点在太多的情况下是固定的而且难得被核对。本章在后面将
提出以每周或更长的间隔来更新订货点的技法,以保持它们同预期的需求或提前期
的变化相协调。
3、两次补货订货之间的间隔期不是常数,它随使用率而变:需求越高,订货
间隔期短(因此得名为固定订货量──可变周期)。
4、库存的储备存货部份通常被认为平均起来一年到头都是现有库存。
5、库存的相当于满订货量的周期性存货部份只有在它刚刚被收进时才是现有
库存。平均起来,只有订货量的一半将一年到头在库,因为假设使用率是均匀的。
6、平均总库存的计划量等于订货量的一半加上储备存货。
用目视法寻找订货点
在一物品的平均需求是每周100件与预期的提前期为6周的情况下,通过察看过去的活动──如库存记录所示──可能发现由于提前期比预期的要长或需求比
预期的要高而使提前期中的需求有时可高达800件。如果这样的查看表明提前期
中的需求难得超过800件,则把订货点设在800件就可获得成功的服务。这在
事实上已建立了200件的储备存货用来对付需求与提前期二者的变化。
该订货点是两个要素之和:提前期中的预期需求与储备存货。前节所讨论的例
中: 订货点=600件+200件=800件
虽然用查看法确定订货点是简单而吸引人的,但有一个主要的实际问题。为了
通过观察来确定订货点必须有大量的数据;但在典型的商业情况中,数据越老,它
们对当前情况的代表性就越差,对将来可能发生什么的代表性就更差。
确定一个订货点要求对其两个构成因素提前期中的需求与储备存货量作出估计。
一个期间的预期需求必须通过某种预测来确定,其技法已在第4章中讨论过。然后
必须把这一需求量扩展到提前期上,提前期通常不同于预测期间。其技法在本章后
面讨论。
确定恰当的储备存货是一个困难问题,并无容易的解法。应用经验法则将造成
许多物品的库存过多而另一些物品库存不足。更为严格的方法也最多只能稍微减少
这些过多或不足。所要求的储备存货量是主要由下列要素构成的一个函数:
1、准确地预测需求的能力
2、提前期的长度
3、准确地预测或控制提前期的能力
4、订货量的大小
5、所希望的服务水平
某些统计技法──以不受清规戒律拘束的实用观点与方法去应用时──可以相
当有效地用于实际去确定有用的储备存货。本章下面几节讨论的方法在工业中有着
广泛的应用并对专业经理是有帮助的。
原理16.由于不确定性不能被消除,订货点法要求有储备存货。
预测误差的估计
图5-2所示为2个物品,物品T与物品V的10周销售史。物品T的数据表明,虽然预测每周1000件,而且平均销售量1020非常接近预测值,但实际
销售量曾高达1400,而且另有二周是1200。物品T合理的订货点将是12
00件,预期当一周的补货期中的需求超过1200时将有时出现缺货。
该订货点构成如下:
订货点=提前期中的预期需求+储备存货 (5-1)
=1000+200=1200
如果不允许缺货,则订货点将必须设在1400以上。当然,不能保证在未来
销售量有时不会大大超过1400──因为一个10周的销售史是相当小的一个样
本。
┏━━━━┳━━━━━━━┳━━━━━━━┓
┃第 几 周┃ 物 品 T ┃ 物 品 V ┃
┣━━━━╋━━━━━━━╋━━━━━━━┫
┃ 1 ┃ 1200 ┃ 400 ┃
┣━━━━╋━━━━━━━╋━━━━━━━┫
┃ 2 ┃ 1000 ┃ 600 ┃
┣━━━━╋━━━━━━━╋━━━━━━━┫
┃ 3 ┃ 800 ┃ 1600 ┃
┣━━━━╋━━━━━━━╋━━━━━━━┫
┃ 4 ┃ 900 ┃ 1200 ┃
┣━━━━╋━━━━━━━╋━━━━━━━┫
┃ 5 ┃ 1400 ┃ 200 ┃
┣━━━━╋━━━━━━━╋━━━━━━━┫
┃ 6 ┃ 1200 ┃ 1000 ┃
┣━━━━╋━━━━━━━╋━━━━━━━┫
┃ 7 ┃ 1100 ┃ 1500 ┃
┣━━━━╋━━━━━━━╋━━━━━━━┫
┃ 8 ┃ 700 ┃ 800 ┃
┣━━━━╋━━━━━━━╋━━━━━━━┫
┃ 9 ┃ 1000 ┃ 1400 ┃
┣━━━━╋━━━━━━━╋━━━━━━━┫
┃ 10 ┃ 900 ┃ 1100 ┃
┣━━━━╋━━━━━━━╋━━━━━━━┫
┃ 总 计 ┃ 10,200 ┃ 9800 ┃
┣━━━━┻━━━━━━━┻━━━━━━━┫
┃ 1、两物品的每周预测均为1000件 ┃
┃ 2、订货量为1000件 ┃
┃ 3、提前期为一周 ┃
┗━━━━━━━━━━━━━━━━━━━━┛
图5-2 10周的销售史
物品V表现出更为不规则的需求;事实上,如果物品V的订货点设在1200,
则将发生三次缺货,因为有三周提前期中的需求超过了订货点。这种情况在工业中
是常见的;对于低量物品或当订货的客户较少时,通常其需求的变动性较大。许多
公司,除了直接把产品卖给消费者之外,还要以稍有不同的配置为邮购商店或其它
大分销商供货。他们通常发现直接卖给许多客户的物品具有更为可预报的模式,而
较少的大量需求趋向于小得多的可预报性。为了保持同样的服务水平,物品V的订
货点将显然要比物品T高许多。这两种物品倘若采用相等的储备存货将使物品T持
有过多库存或使物品V给出较差的服务。
可用信息的小样本也带来严重的问题,因为没有保证物品V的销售量有时不会
高达2200件或物品T不可能有高达1900件的销售量。因此,在订货点概念
的实际应用中需有某种相当可靠而始终一贯的方法根据小样本数据来确定储备存货
。对于许多物品,处理这种计算的一个非常有用的概念是正态分布。
正态分布是最著名的统计关系之一──大多数人都熟悉钟形曲线。
计算订货点时,对正态分布的两个特征有兴趣:
1、中值或平均值
它相当于钟形曲线的最高点,它是最可能发生的值。
2、标准偏差,它度量值围绕平均值的变化或分散。
这相当于钟形曲线的宽度,它度量这些个别值如何紧紧地围绕平均值而分布。
要应用正态分布必须满足下列条件:
1、需求数据是单峰的
这只是说该需求趋向于分布在一个平均值的周围。如果需求可能接近每周500
件或约每周1500 件但不大可能取二者中间的任何值, 则该需求将具有两种最
频繁地出现过的状态,正态分布将不能恰当地描述为样的需求数据。
2、假设该需求数据的分布是对称的
换句话说,该分布中需求小于预测200件与大于预测200件的可能性是刚
好一样的。这一假设在计算订货点时有一些实际问题。例如,倘若预测的需求是每
周20件,它不可能少于零,然而可能多达100件或150件。换句话说,平均
值离地板很近,而离天花板很远。有两种办法来处理这一问题:
a、当预测值如此之低,以致正的变差将比负的变差大得多时,可忽略所有负
的变差,而在标准偏差或平均绝对偏差的计算中则包括正的变差。
b、对小量需求的某些类型,另一特殊的叫做泊桑分布的统计分布往往给出好
的结果。详见本章后面。
3、使用正态分布时,假设实际平均值将等于预测的平均值(即假设预测是准
确的)。最好的保险是使用一种技法,例如使用指数平滑法,定期地去更新预测并
使用一跟踪信号去指示何时此预测正在工作得不能令人满意,详见本章后面。
图5-4所示为图5-2中物品T的预测误差的标准偏差的计算
┏━━━━━━━━━━━━━━━━━━━━━━━━━━━━━━━━━━━┓
┃ 物 品 T ┃
┣━━━┳━━━━━━┳━━━━━━━┳━━━━━┳━━━━━━━━━━┫
┃第几周┃ 预 测 ┃ 销 售 量 ┃ 偏 差 D ┃ D2 ┃
┣━━━╋━━━━━━╋━━━━━━━╋━━━━━╋━━━━━━━━━━┫
┃ 1 ┃ 1000┃ 1200 ┃-200 ┃ 40,000 ┃
┣━━━╋━━━━━━╋━━━━━━━╋━━━━━╋━━━━━━━━━━┫
┃ 2 ┃ 1000┃ 1000 ┃-----┃ ----- ┃
┣━━━╋━━━━━━╋━━━━━━━╋━━━━━╋━━━━━━━━━━┫
┃ 3 ┃ 1000┃ 800 ┃ 200 ┃ 40,000 ┃
┣━━━╋━━━━━━╋━━━━━━━╋━━━━━╋━━━━━━━━━━┫
┃ 4 ┃ 1000┃ 900 ┃ 100 ┃ 10,000 ┃
┣━━━╋━━━━━━╋━━━━━━━╋━━━━━╋━━━━━━━━━━┫
┃ 5 ┃ 1000┃ 1400 ┃-400 ┃ 160,000 ┃
┣━━━╋━━━━━━╋━━━━━━━╋━━━━━╋━━━━━━━━━━┫
┃ 6 ┃ 1000┃ 1200 ┃-200 ┃ 40,000 ┃
┣━━━╋━━━━━━╋━━━━━━━╋━━━━━╋━━━━━━━━━━┫
┃ 7 ┃ 1000┃ 1100 ┃-100 ┃ 10,000 ┃
┣━━━╋━━━━━━╋━━━━━━━╋━━━━━╋━━━━━━━━━━┫
┃ 8 ┃ 1000┃ 700 ┃ 300 ┃ 90,000 ┃
┣━━━╋━━━━━━╋━━━━━━━╋━━━━━╋━━━━━━━━━━┫
┃ 9 ┃ 1000┃ 1000 ┃-----┃ ----- ┃
┣━━━╋━━━━━━╋━━━━━━━╋━━━━━╋━━━━━━━━━━┫
┃10 ┃ 1000┃ 900 ┃ 100 ┃ 10,000 ┃
┣━━━╋━━━━━━╋━━━━━━━╋━━━━━╋━━━━━━━━━━┫
┃总 计┃10,000┃10,200 ┃1600* ┃ 400,000 ┃
┣━━━┻━━━━━━┻━━━━━━━┻━━━━━┻━━━━━━━━━━┫
┃D2的均值=400,000÷10=40,000 *忽视正负号 ┃
┃ ──── ┃
┃σ=√40,000 =200=标准偏差 ┃
┃另一种方法: ┃
┃ 平均绝对偏差(MAD)=D的均值=1600÷10=160 ┃
┃ σ=MAD×1.25=160×1.25=200 ┃
┗━━━━━━━━━━━━━━━━━━━━━━━━━━━━━━━━━━━
图5-4 标准偏差的计算
计算预测误差的标准偏差要使用下列步骤:
1、从预测值减去每周的实际销售量得出偏差值
2、将偏差值平方
3、对偏差的平方求和
4、确定偏差平方的均值
5、将偏差平方的均值开方,就得出标准偏差
标准偏差的精确计算要求将偏差平方的和数除以(n-1),其中n是观察的
次数。本章为了简化,用n代替了(n-1)。详见任何统计学教科书。
当需求量小于平均值时,实际工作者在设置订货点时并不关心提前期间。只有
当需求大于平均值时,才需有后备存货来满足这些期间。如果预测相当准确而且经
常得到更新,长期看来约有50%的时间需求将小于平均值,而且实际工作者可以
期望不用后备来给出50%的服务。如果他在预测的平均值1000之外再加一个
标准偏差或200件的后备存货(使订货点为1200件),该实际工作者将在补
货期间有足够库存去满足另外34%的需求(1个标准偏差=34%的事件);因
此他可以期望以一个含有一个标准偏差后备存货的订货点去给出84%(50%+
34%)的服务。订货点为1200件时,该实际工作者从长远看约有十分之二的
机会在补货期间遇到缺货。看看图5-4中物品T的销售量,这一结果看来并非太
不合理的。
如果在提前期间的平均需求1000件之上再加两个标准偏差或400件,该
订货点变成1400件。该第二个标准偏差将满足另外14%的事件,给出总计约
为98%(84%+14%)的服务。订货点为1400件,提前期中需求超过1
400件的机会将只有百分之二。从物品T的数据看,这看来也是合理的。
标准偏差虽然在库存控制中是个很有用的度量,但它包含许多计算,有些麻烦。
如图5-4中所示,它可用更简的方法通过MAD来确定。MAD是预测值与实际
销售量之间差异(绝对偏差)的平均值。MAD与标准偏差的近似关系是
σ=1.25×MAD (5-2)
图5-4说明用此法计算标准偏差时要先求出MAD等于160。虽然此法不
能永远得出如此接近于直接计算法的结果,通常它对于大多数实际的库存控制应用
还是足够接近的。使用MAD可省去许多计算。此外,MAD有助于定期地更新,
这对良好的库存控制是不可缺少的;这一技法将在本章后面叙述。MAD也指出如
果没有安全库存,缺货将有多大平均数,并显示下一预测期间的预期误差。
图5-5说明计算物品V的MAD的方法。物品V的需求变化比物品T的显然
要大。这里MAD是380,标准偏差是475,比物品T的增1倍还多。对物品
V,具有98%服务订货点可构筑如下:
物 品 V
第几周 预测 销售 偏差
───────────────────────────
1 1000 400 600
2 1000 600 400
3 1000 1600 -600
4 1000 1200 -200
5 1000 200 800
6 1000 1000 ---
7 1000 1500 -500
8 1000 800 200
9 1000 1400 -400
10 1000 1100 -100
──── ──────
总 计 9800 3800*
MAD=3800÷10=380 *忽视正负号
σ= 380×1.25=475
───────────────────────────
图5-5 用MAD计算σ
订货点=提前期中预期需求+后备存货
提前期中预期需求=1000件
相当于98%服务的后备存货=2σ=2×475=950件
100次中约2次缺货,需求有可能超过一周1950件,根据可用数据是小
样本,看来是合理的。
为了计算后备存货,使用MAD是一种实用的技法,它可以按每一个别物品的
特征来量体裁衣。这样算得的后备存货对具有较大的需求变动性的物品将较大,而
对具有较稳定需求的物品将较小。这一技法假设实际的平均需求等于预测的需求,
这不一定永远成立的。
可用图5-6来说明这一问题,图中物品W的预测是每周1000件,平均绝
对偏差为160件(与图5-4中物品T相同)。但物品W的销售量在大多数时间
里超过了预测,指示预测应当增加到大约1100件。这将降低偏离量,从而使库
存中必须持有的后备存货降低。
┏━━━━━━━━━━━━━━━━━━━━━━━━━━━━━━━━┓
┃ 物 品 W ┃
┣━━━┳━━━━┳━━━━━━━┳━━━━┳━━━━━━━━━━┫
┃第几周┃ 预测 ┃ 销 售 ┃ 偏 差 ┃预测误差的代数和RSFE┃
┣━━━╋━━━━╋━━━━━━━╋━━━━╋━━━━━━━━━━┫
┃ 1 ┃1000┃ 1200 ┃-200┃ - 200 ┃
┣━━━╋━━━━╋━━━━━━━╋━━━━╋━━━━━━━━━━┫
┃ 2 ┃1000┃ 1000 ┃----┃ - 200 ┃
┣━━━╋━━━━╋━━━━━━━╋━━━━╋━━━━━━━━━━┫
┃ 3 ┃1000┃ 1200 ┃-200┃ - 400 ┃
┣━━━╋━━━━╋━━━━━━━╋━━━━╋━━━━━━━━━━┫
┃ 4 ┃1000┃ 900 ┃+100┃ - 300 ┃
┣━━━╋━━━━╋━━━━━━━╋━━━━╋━━━━━━━━━━┫
┃ 5 ┃1000┃ 1400 ┃-400┃ - 700 ┃
┣━━━╋━━━━╋━━━━━━━╋━━━━╋━━━━━━━━━━┫
┃ 6 ┃1000┃ 1200 ┃-200┃ - 900 ┃
┣━━━╋━━━━╋━━━━━━━╋━━━━╋━━━━━━━━━━┫
┃ 7 ┃1000┃ 1100 ┃-100┃ -1000 ┃
┣━━━╋━━━━╋━━━━━━━╋━━━━╋━━━━━━━━━━┫
┃ 8 ┃1000┃ 1300 ┃-300┃ -1300 ┃
┣━━━╋━━━━╋━━━━━━━╋━━━━╋━━━━━━━━━━┫
┃ 9 ┃1000┃ 1000 ┃----┃ -1300 ┃
┣━━━╋━━━━╋━━━━━━━╋━━━━╋━━━━━━━━━━┫
┃10 ┃1000┃ 900 ┃+100┃ -1200 ┃
┣━━━╋━━━━╋━━━━━━━╋━━━━╋━━━━━━━━━━┫
┃ ┃ 总 计 ┃11,200 ┃1600┃ ┃
┣━━━┻━━━━┻━━━━━━━┻━━━━┻━━━━━━━━━━┫
┃ MAD =1600÷10=160 ┃
┃ 跟踪信号=RSFE÷MAD ┃
┃ =1200÷160 ┃
┃ =7.5 ┃
┗━━━━━━━━━━━━━━━━━━━━━━━━━━━━━━━━┛
图5-6 跟踪信号的确定
只看物品W的预测值与MAD,会认为其需求特征与物品T是相同的,但可以
计算出一个跟踪信号,它将立即揭露出事实上预测误差正在分布的一侧积累着。在
这一特例中,预测在大多数周是低于实际的。对预测误差求代数和(叫Running
Sum of Forecast Error,简写为RSFE),然后除以MAD就可得出实际值与预测值
之间一贯性差值的一种度量,叫做跟踪信号。图中根据10周的数据,可以算出物
品W的跟踪信号是7.5,它很高,指示销售始终超过了预测。在一实际的库存系
统中,该预测将被指数平滑法更新,其结果是该跟踪信号将度量这一不断地被更新
着的预测的有效度。在本例中为了避免过多的计算使用的是固定的预测1000件。
倘若预测误差趋向于互相抵消(如在物品T的例子中),跟踪信号将保持低值,表
明预测相当成功,不需修改。
跟踪信号可接收的最大值在4与8之间,取决于该信号是如何使用的。对一高
价物品,可用4为跟踪信号的最大值以及早触发预测的修改,从而避免由于等待过
久而持有过多库存或危害服务。对于一低值物品,可用相当高的跟踪信号(也许用
7或8),因为低值物品的预测误差可以较高而且大多数公司对较不通用的物品较
少强调要保持良好的服务。第4章中也讲到过跟踪信号的使用。
第4章中指数平滑法预测公式中的加权因子是对趋势反应太慢与对随机事件反
应过头之间的折衷;跟踪信号也属这类工具。跟踪信号定得太低,会为了抓住少数
不成功的预测而去要求评审系统为之工作得成功的许多物品。跟踪信号定得太高则
可能拖延评审从而引起不良的服务或库存过多。然而,有一个跟踪信号在起作用确
实提供一种例外技法用来指出某一特定预测需要评审,所以它应是每一完整系统的
一部份。理想地,它将召唤人们注意人们能够在一次有效的评审中把握的物品数。
订货点的计算
知道了正态分布的一般统计性质并已算出了预测误差的标准偏差或平均绝对偏差MAD,订货点的计算就简单了。本章前面讨论过在提前期中预期需求之上加一
个标准偏差是以给出84%的服务为目标,加2个标准偏差则将服务水平提高到
98%。服务水平直接地同作为后备或安全存货的标准偏差数有关;这一数目通常
称为安全因子。
图5-7是正态分布下不同服务水平的安全因子表,安全因子可用标准偏差数
或MAD数表示。由于MAD总是小于标准偏差,所以所用的MAD数总比所要的
标准偏差数要多些。例如服务水平为84.13%时,安全存货要用1个标准偏差
或1.25个MAD。
┏━━━━━━━━━━━━━┳━━━━━━━━━━━━━┓
┃ 服务水平 (%)┃ 安全因子用: ┃
┃ ┃标准偏差 平均绝对偏差┃
┣━━━━━━━━━━━━━╋━━━━━━━━━━━━━┫
┃ 50.00 ┃0.00 0.00 ┃
┃ 75.00 ┃0.67 0.84 ┃
┃ 80.00 ┃0.84 1.05 ┃
┃ 84.13 ┃1.00 1.25 ┃
┃ 85.00 ┃1.04 1.30 ┃
┃ 89.44 ┃1.25 1.56 ┃
┃ 90.00 ┃1.28 1.60 ┃
┃ 93.32 ┃1.50 1.88 ┃
┃ 94.00 ┃1.56 1.95 ┃
┃ 94.52 ┃1.60 2.00 ┃
┃ 95.00 ┃1.65 2.06 ┃
┃ 96.00 ┃1.75 2.19 ┃
┃ 97.00 ┃1.88 2.35 ┃
┃ 97.72 ┃2.00 2.50 ┃
┃ 98.00 ┃2.05 2.56 ┃
┃ 98.61 ┃2.20 2.75 ┃
┃ 99.00 ┃2.33 2.91 ┃
┃ 99.18 ┃2.40 3.00 ┃
┃ 99.38 ┃2.50 3.13 ┃
┃ 99.50 ┃2.57 3.20 ┃
┃ 99.60 ┃2.65 3.31 ┃
┃ 99.70 ┃2.75 3.44 ┃
┃ 99.80 ┃2.88 3.60 ┃
┃ 99.86 ┃3.00 3.75 ┃
┃ 99.90 ┃3.09 3.85 ┃
┃ 99.93 ┃3.20 4.00 ┃
┃ 99.99 ┃4.00 5.00 ┃
┗━━━━━━━━━━━━━┻━━━━━━━━━━━━━┛
图5-7 正态分布下的安全因子表
此表可用来计算各种服务水平的安全存货。例如假设物品X的数据如下:
每周预测=500件
提前期= 1周
MAD=200件
希望的服务= 98%
订货量=500件
由于此物品的每周需求是500件,而提前期是一周,则提前期中的需求就是
500件。
MAD是200件。如果希望达到98%的服务水平,图5-7指出安全 因
子应为2.56个MAD。
故后备存货=安全因子×MAD
=2.56×200=512件
而订货点=提前期中的需求+后备存货
=500+512=1012件
这个订货点(据表)应给出98%的服务水平──但在此项计算中“服务”的
意思是什么?它的意思是在补货期间的百分之多少的时间内需求不应超过订货点量。
订货点是设计得用来复盖提前期中的需求,从而该物料的一份补货订单可以及时发
出使得该物料在全部存货被提取完毕之前交货到存贮之中。此补货提前期的终点是
一物品可能用完到缺货的关键时刻。一物品可能缺货的“曝光”次数就等于发出补
货订单的次数,当然它要取决于订货量的大小。订货量较大的物品将要求较少的每
年补货订单数,因而比更加频繁地订货的物品要较少地曝光于缺货。
订货量与安全存货之间的这一关系可通过先确定将发生的补货期间数(曝光到
缺货的次数),然后计算以不希望发生缺货的补货期间数来表示的所希望的服务水
平的办法来考虑进去。
可用物品X的数据来说明这种计算。此物品的周预测是500件,提前期为1
周,MAD是200件,所希望的服务水平是98%。如果此服务水平用每年缺货
1次来表示(由于1/52=1.9%,它粗略地相当于98%的服务水平),而
且如果订货量是2600件,则:
年需求量=500×52=26,000件/年
每年曝光次数=26,000/2600=10个补货期间
要求的服务水平是缺货1次=9/10或90%
安全因子=1.60×MAD(从图5-7,服务水平90%时)
订货点=500+(1.60×200)=500+320=820
这一订货点比上次为物品X计算的订货量为500件时的订货点要低得多。因
为500件的订货量要有52次曝光于缺货,98%的服务水平要求有2.56×
MAD的安全存货,订货点将为1012件=500+2.56×200。
由于订货量、曝光次数与后备存货货之间的相互作用,订货点与EOQ的简单、
独立算法并不一定给出最经济的总库存水平。进一步的计算往往将揭示增加订货量
将减少曝光对任一给定服务水平所要求的总库存,因为它将减少次数,从而减少了
所要求的后备存货。在某些情况下,后备存货的减少量将大于所要求的批量的增量。
这一关系将在附录Ⅳ中用例子说明。对价值最高的A类物品,这一统计技法的精益
求精可能是非常值得的,但对大多数物品这是不得的;所得的节约比起所化的力气
来将是太小了。
预测间隔与提前期差别的调整
在实践中计算统计的后备存货时常遇的另一问题是预测间隔不同于提前期间。通常库存中包含的许多物品具有差别很大的提前时间,为了确定这些不同物品在提
前期中需求的变化并计算后备存货必须去测定它们在各各不同的提前期上的预测误
差,这将是非常不方便的。必须使用某种其它方法去调整预测误差以补偿不同的提
前时间。
如果物品X的提前期为4周,则提前期中的需求将为4×500=2000件。
期望需求大大超过平均值的机会很可能超过一周是合理的,所以有必要增加原先以
一周的需求为基础的后备库存以便为现在较长的提前期提供等效的保护水平。
另一方面,显然也不宜把适用于1周提前期的后备存货乘以4来确定4周提前
期所需的后备存货;因为需求不大可能;连续4周保持很高。显然后备存货必须随
着提前期的变长而有所增加,但增量不一定直接正比于提前期的增量。当预测间隔
不同于提前时间间隔时,需有某种调整因子,实践中时常就是这样做的。
┏━━━━━━━━━━━┳━━━━━━━━━━┓
┃ 当预测间隔=1 ┃ 标准偏差或平均 ┃
┃ 而提前期间隔为 : ┃ 绝对编差应乘以*: ┃
┣━━━━━━━━━━━╋━━━━━━━━━━┫
┃ 2 ┃ 1.63 ┃
┃ 3 ┃ 2.16 ┃
┃ 4 ┃ 2.64 ┃
┃ 5 ┃ 3.09 ┃
┃ 6 ┃ 3.51 ┃
┃ 7 ┃ 3.91 ┃
┃ 8 ┃ 4.29 ┃
┃ 9 ┃ 4.66 ┃
┃ 10 ┃ 5.01 ┃
┃ 11 ┃ 5.36 ┃
┃ 12 ┃ 5.69 ┃
┃ 13 ┃ 6.02 ┃
┃ 14 ┃ 6.34 ┃
┃ 15 ┃ 6.66 ┃
┃ 16 ┃ 6.96 ┃
┃ 17 ┃ 7.27 ┃
┃ 18 ┃ 7.56 ┃
┃ 19 ┃ 7.86 ┃
┃ 20 ┃ 8.14 ┃
┃ ┃ ┃
┗━━━━━━━━━━━┻━━━━━━━━━━┛
*假设β=0.7
图5-9 提前时间不等于预测间隔时
使用的调整因子表
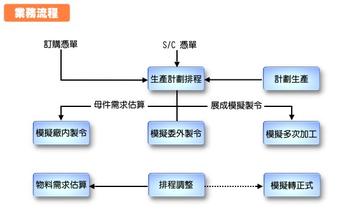
图5-9给出一张提前期不等于预测间隔时调整MAD用的因子表。此表为较
长的提前期间隔确定一等效的偏差提供一调整因子,用此调整因子乘上预测间隔的
MAD,可用来计算后备存货。确定这些因子的公式是:
调整后的MAD=MAD(LT/F)β (5-3)
其中
调整后的MAD=提前期间隔的MAD
MAD=预测间隔的MAD
LT=提前期间隔
F=预测间隔
β=取决于具体行业的需求模式的一个常数
理论上β值应通过使用该公司实际数据的仿真来确定。实践中发现β取0.7
可以给出相当好的结果。事实上,为了拟合公司的实际需求模式,需作大量仿真工
作才能确定一更准确的β值。图5-9中的乘数是根据β=0.7算出的,其用法
如下:
1、将提前期间隔表达为预测间隔的倍数
2、按此倍数查表中第一列
3、将预测间隔的MAD乘上第二列中相应的调整因子,使它转换成提前期间
隔的MAD
使用图5-9与物品X的数据,可计算订货点如下:
1、设物品X的提前时间是4周(预测间隔1周的4倍)
2、倍数为4时,查表知调整因子为2.64
3、提前时间为1周时的MAD是200件
调整后的MAD=2.64×200=528件
所求后备存货=1.60×528=845件
(订货量=2600件,每年允许缺货一次,安全因子为1.60)
订货点=(4×500)+845=2845件
对大多数物品,这种近似法已足够准确。然而,对高价物品,用此表算出的结
果应再用仿真加以核对,以确定一更精确的调整因子或应在提前期间隔上直接计算
出预测误差。
物料经理必须找到常规地更新提前期中预测的需求与重新计算所需后备存货的
手段。图5-10所示为物品X13周的实际需求。第4章讲过的指数平滑法提供
这样一种常规地更新预测的方法;图5-11表示每周使用这种技法与图5-10
中的数据来作一次新预测。在这里,开始的预测是每周500件,而指数平滑法计
算使此预测先是有所下降然后在第6周上升到526件。图5-10表明13周的
平均需求为600件,而指数平滑计算,虽然滞后了,但比原来预测的数字每周5
00件要好些。这表明该技法对校正一显然太低的预测从而使它更符合于实际销售
是有用的。
┏━━━━━━━━━━━━━━━━━━━━━━━━┓
┃ 预测的周需求=500件 ┃
┣━━━━━━━━━━━┳━━━━━━━━━━━━┫
┃ 第几周 ┃ 实际需求 ┃
┣━━━━━━━━━━━╋━━━━━━━━━━━━┫
┃ 1 ┃ 464 ┃
┃ 2 ┃ 330 ┃
┃ 3 ┃ 474 ┃
┃ 4 ┃ 847 ┃
┃ 5 ┃ 618 ┃
┃ 6 ┃ 772 ┃
┃ 7 ┃ 573 ┃
┃ 8 ┃ 432 ┃
┃ 9 ┃ 938 ┃
┃ 10 ┃ 642 ┃
┃ 11 ┃ 750 ┃
┃ 12 ┃ 294 ┃
┃ 13 ┃ 672 ┃
┣━━━━━━━━━━━┻━━━━━━━━━━━━┫
┃ 7806 ┃
┣━━━━━━━━━━━━━━━━━━━━━━━━┫
┃ 平均周需求 =600 ┃
┗━━━━━━━━━━━━━━━━━━━━━━━━┛
图5-10 物品X13周的需求史
┏━━━━━━━━━━━━━━━━━━━━━━━━━━━━━━━━━┓
┃ 新预测=α×实际需求+(1-α)×老预测 ┃
┃ 其中:α=0.1,(1-α)=0.9 ┃
┣━━━┳━━━┳━━━━━━━┳━━━━┳━━━━━━┳━━━━━┫
┃第几周┃老预测┃(1-α)×老预测┃实际需求┃α×实际需求┃ 新预测 ┃
┣━━━╋━━━╋━━━━━━━╋━━━━╋━━━━━━╋━━━━━┫
┃ 1 ┃500┃ 450.0 ┃ 464 ┃ 46.4 ┃ 496 ┃
┣━━━╋━━━╋━━━━━━━╋━━━━╋━━━━━━╋━━━━━┫
┃ 2 ┃496┃ 446.4 ┃ 330 ┃ 33.0 ┃ 479 ┃
┣━━━╋━━━╋━━━━━━━╋━━━━╋━━━━━━╋━━━━━┫
┃ 3 ┃479┃ 431.1 ┃ 474 ┃ 47.4 ┃ 479 ┃
┣━━━╋━━━╋━━━━━━━╋━━━━╋━━━━━━╋━━━━━┫
┃ 4 ┃479┃ 431.1 ┃ 874 ┃ 84.7 ┃ 516 ┃
┣━━━╋━━━╋━━━━━━━╋━━━━╋━━━━━━╋━━━━━┫
┃ 5 ┃516┃ 464.4 ┃ 618 ┃ 61.8 ┃ 526 ┃
┣━━━╋━━━╋━━━━━━━╋━━━━╋━━━━━━╋━━━━━┫
┃ 6 ┃526┃ 473.4 ┃ 772 ┃ 77.2 ┃ 551 ┃
┣━━━╋━━━╋━━━━━━━╋━━━━╋━━━━━━╋━━━━━┫
┃ 7 ┃551┃ 495.9 ┃ 573 ┃ 57.3 ┃ 553 ┃
┣━━━╋━━━╋━━━━━━━╋━━━━╋━━━━━━╋━━━━━┫
┃ 8 ┃553┃ 497.7 ┃ 432 ┃ 43.2 ┃ 541 ┃
┣━━━╋━━━╋━━━━━━━╋━━━━╋━━━━━━╋━━━━━┫
┃ 9 ┃541┃ 486.9 ┃ 938 ┃ 93.8 ┃ 580 ┃
┣━━━╋━━━╋━━━━━━━╋━━━━╋━━━━━━╋━━━━━┫
┃10 ┃580┃ 522.0 ┃ 642 ┃ 64.2 ┃ 586 ┃
┣━━━╋━━━╋━━━━━━━╋━━━━╋━━━━━━╋━━━━━┫
┃11 ┃586┃ 527.4 ┃ 750 ┃ 75.0 ┃ 602 ┃
┣━━━╋━━━╋━━━━━━━╋━━━━╋━━━━━━╋━━━━━┫
┃12 ┃602┃ 541.8 ┃ 294 ┃ 29.4 ┃ 571 ┃
┣━━━╋━━━╋━━━━━━━╋━━━━╋━━━━━━╋━━━━━┫
┃13 ┃571┃ 513.9 ┃ 672 ┃ 67.2 ┃ 581 ┃
┗━━━┻━━━┻━━━━━━━┻━━━━┻━━━━━━┻━━━━━┛
图5-11 使用指数平滑法的预测
图5-12显示同一套用于计算MAD与更新MAD的情形。更新用的是指数
平滑法,用MAD替代预测,并用偏差替代需求。在图5-12中,开始时MAD
是200。使用指数平滑公式,老MAD乘上0.9,新偏差乘上0.1,而新
MAD是二者之和,如图5-11一列所示。实践中,图5-11与图5-12中
的计算将同时进行,而订货量可以每周计算一次。即使成千种物品,现代计算机也
能容易地处理这些计算。
┏━━━━━━━━━━━━━━━━━━━━━━━━━━━━━━━━━━━┓
┃ 新MAD=α×偏差+(1-α)老MAD ┃
┃ 其中 =0.1,(1-α)=0.9 ┃
┣━━━┳━━━┳━━━┳━━━┳━━━━┳━━━┳━━━━━━┳━━━┫
┃第几周┃ 预测 ┃ 销售 ┃ 偏差 ┃α×偏差┃老MAD ┃(1-α)×MAD┃ 新MAD┃
┣━━━╋━━━╋━━━╋━━━╋━━━━╋━━━╋━━━━━━╋━━━┫
┃ 1 ┃500┃464┃ 56┃ 3.6┃200┃180.0 ┃184┃
┣━━━╋━━━╋━━━╋━━━╋━━━━╋━━━╋━━━━━━╋━━━┫
┃ 2 ┃496┃330┃166┃16.6┃184┃165.6 ┃182┃
┣━━━╋━━━╋━━━╋━━━╋━━━━╋━━━╋━━━━━━╋━━━┫
┃ 3 ┃479┃474┃ 5┃ 0.5┃182┃163.8 ┃164┃
┣━━━╋━━━╋━━━╋━━━╋━━━━╋━━━╋━━━━━━╋━━━┫
┃ 4 ┃479┃847┃368┃36.8┃164┃147.6 ┃184┃
┣━━━╋━━━╋━━━╋━━━╋━━━━╋━━━╋━━━━━━╋━━━┫
┃ 5 ┃516┃618┃102┃10.2┃184┃165.6 ┃176┃
┣━━━╋━━━╋━━━╋━━━╋━━━━╋━━━╋━━━━━━╋━━━┫
┃ 6 ┃526┃ 等等 ┃ ┃ ┃ ┃ ┃ ┃
┗━━━┻━━━┻━━━┻━━━┻━━━━┻━━━┻━━━━━━┻━━━┛
图5-12 预测的偏差与MAD
使用本章所讲技法来计算订货点的全部过程如下:
1、确定每年允许的缺货次数(在收到订货量之前存货可能被用完的补货期间)。
这是一项管理决策,而不是计算。
2、把年度需求预测量除以订货量,算出每年要发出补货订单(或曝光)的次
数。
3、计算出服务率,表达为一个百分数。这是不希望发生缺货的补货期间数
(总曝光次数减去允许缺货次数)与补货期间总数之比。
4、使用这个百分数去找出(从图5-7中)安全因子──即必须包括在后备
存货中的偏差个数(标准偏差或MAD)。
5、如图5-4或5-5所示地计算出标准偏差或MAD。
6、使用图5-9中的表,计算出调整后的偏差(标准偏差或MAD)去对付
预测间隔与提前期间隔之间的任何差异。
7、将调整后的偏差乘以安全因子,计算出所需的总后备存货。
8、把这一后备存货加到提前期提预测需求(DLT)之上,得出总的订货点。
下面是使用物品X的数据的一例:
年需求=26,000件
订货量=500件
提前期=4周
MAD=200件
则:1、每年允许缺货次数=1 (由管理者决定)
2、每年曝光次数=26,000÷500=52
3、服务率=(52-1)÷52=98%
4、从图5-7,安全因子=2.56(用MAD)
5、MAD=200件
6、调整后的MAD=2.64×200=528件
7、后备存货=2.56×528=1350件
8、订货点=DLT+后备=(4×500)+1350=3350件
这里讨论的技法提供可以频繁到每周一次地来生成修订后的订货点的简单方法。
这些方法在工业中已有相当大的应用而且已被证明是成功的。好处不仅来自测定预
测误差并实际地确定后备存货应有多大,也来自有了一种为成千种物品常规地预测
其需求以及在例行的基础上同时更新预测与对预测误差的估计这二者的手段。这些
统计技法必须以充分理解其基本假设与了解它们的局限性为基础谨慎地去使用。一
切统计技法假设未来将像过去那样。幸运的是,在大多数情况下对最近的将来这是
一个相当有效的假设,但将毕竟总归是有变化的。使用类似指数平滑法、预测跟踪
信号并定期地更新预测误差的度量能够有助于迅速地找出这些变化并作出适当的校
正。
在前面的计算中为了简单起见,只计算了预测误差,而且曾经假设使用一
个不变的提前时间──通常就是平均已计划提前时间。提前时间的变差不可直接同
需求的变差相加,因为最长的提前时间不大可能与最大的需求同时发生。应注意避
免改变已计划提前时间,除非是在受控条件下应用投入/出产控制法去减少在制品
时。第2册第5章叙述由于对已计划提前时间修修补补而引起恶性循环的问题。
即使在具有某些许可的应用场合,统计学的技法也有巨大的价值。像一切其它
的所谓科学的工具一样,正态分布应当带着判断来使用。如果其答案无意义,则该
项计算应请统计学方面内行的人(例如质量控制经理)予以重新审查,并在应用之
前由实际工作者核对其合理性。这类概念只是试图用数学语言描述发生在商业中的
实际事件。实际工作者务必理解它们的局限性与含义,这比他懂得用来推导它们的
所有的数学与统计学的理论要更为重要。
原理17.只有在统计学技法的假设是有效的场合并且在经过测试之后
,才应用统计学技法去设定后备存货。
泊桑分布的使用
对某些需求类型,使用泊桑分布去计算订货点是方便的,因为它具有其标准偏差永远等于其均值的平方根这一性质。泊桑分布的主要应用是在质量控制上与涉及
顾客在超级市场的收银机前或汽车在高速公路收税站前的随机到达问题的研究之中。
虽然它已为实际工作者所熟知有多年了,但泊桑分布在库存控制中并未获得广泛应
用(11)。它最适用于小量、不经常的需求,每一订单的物品数量相当稳定的场
合,这是某些低产量产品与修理用零件的典型情况。
要恰当地使用于订货点的计算,其需求史必须表达为收到的订单数以及每份订
单的物品数。例如,一物品在提前期中的需求可能平均为4000件;要使用泊桑
分布,必须进一步考察这4000件的需求以确定它确实是由40份每份100件
的订单所构成。
使用泊桑分布来计算订货点的公式如下:
OP(订货点)=u(a+f√a) (5-4)
其中,OP=用件数表示的订货点
u=每份订单的平均需求件数
a=在提前期中到达的平均订单数
f=服务因子(类似但并不等于正态分布中所用的标准偏差的个数)
使用上面的数据,此物品的订货点可计算如下:
OP=100(40+2.1√40)
=100(40+13.28)
=4000+1328=5328
服务因子2.1是从图5-13中选用的,图中给出了使用泊桑分布时相应服
务水平的服务因子应取的值。泊桑分布取服务因子2.1将给出98%的服务率。
这一计算表明要这一特定物品给出98%的服务率,需要有1328件后备存货。
┏━━━━━┳━━━━━━┳━━━┓
┃要满足的需┃允许的欠交 ┃ f ┃
┃求的最小%┃订单的最大%┃ ┃
┣━━━━━╋━━━━━━╋━━━┫
┃ 75 ┃ 25 ┃0.7┃
┣━━━━━╋━━━━━━╋━━━┫
┃ 80 ┃ 20 ┃0.8┃
┣━━━━━╋━━━━━━╋━━━┫
┃ 85 ┃ 15 ┃1.0┃
┣━━━━━╋━━━━━━╋━━━┫
┃ 90 ┃ 10 ┃1.3┃
┣━━━━━╋━━━━━━╋━━━┫
┃ 95 ┃ 5 ┃1.7┃
┣━━━━━╋━━━━━━╋━━━┫
┃ 98 ┃ 2 ┃2.1┃
┣━━━━━╋━━━━━━╋━━━┫
┃ 99 ┃ 1 ┃2.3┃
┣━━━━━╋━━━━━━╋━━━┫
┃ 99.9┃ 0.10 ┃3.1┃
┗━━━━━┻━━━━━━┻━━━┛
图5-13 泊桑分布的服务因子f
如果另一物品在提前期中也有4000件需求,但此物品是卖给少数分销商的,
他们大量订货但并不经常,答案就将大不相同。如果他们一份订单的平均订货量是
1000件,而在提前期中只收到4份订单,计算将是:
OP=1000(4+2.1√4)
=4000+4200=8200
对这一更为飘忽不定的需求,将要求有4200件后备存货才能达到98%的
服务率。
许多作者推荐使用泊桑分布来计算订货点。重要的是要记住:泊桑分布不能被
用来描述提前期中需求的总件数。它可以用来近似地表示提前期中将收到的个别订
单的份数。
使用泊桑分布时所得结果的准确性直接取决于这些订单所涉及的该物品的平均
订货量能被确定到多大准确度。
使用泊桑分布去计算订货点时必须记住的限制性假设如下:
1、订单的到达必须符合泊桑频率分布曲线。当每一提前期间的到达数相对地
小时,通常就符合得更好些。
2、订单的到达是随机而独立的。当客户订单要经销售办公室过滤时,他把同
类物品的订单累积一段时间然后成批地发放它们,这一条就不成立了。
3、对平均订货量要能作出准确的预测。预测中的误差将在订货点与后备存货
中引起相应的误差。
4、订货量不得与平均值有很大差异。要作一些研究以确定可以容许的变差有
多大,但已知变差大时结果是不好的。
5、最后,要记住一切这类统计学方法的基本假设──未来将类似于过去。
正确使用时,计算订货点的泊桑公式有两个明显的优点:
1、它给出前后一贯的有用的结果,远比某些常用的经验法则要优越,诸如设
定后备存货为1个月的供应量或提前期中需求的10%之类。
2、它不要求准备与分析大量统计数据。更为精确的订货点计算方法将给出更
为准确的结果,但将要求昂贵与详细的数据分析。
服务的概念
前面讨论中所使用的服务的度量──每年缺货一次──是一个统计学上处理起来相当简单而且容易联系实际商业情况的度量。如果由于订货量是1周的供应量故
每年要交货52次,则每年一次缺货的服务水平将要求交货率为51/52或98
%。如果订货量是4周的供应量,每年曝光于缺货的次数是13次,则每年缺货一
次的服务水平将要求交货率为12/13或92%。这不过是用统计学语言来表达
这一明显的事实,即收货越频繁而且库存越是频繁地消耗到后备水平,则缺货的机
会也越大。
这一服务的度量如何使用于实践之中?每年的缺货次数并不度量缺货量也不度
量缺货的持续时间,然而,这一度量满有意义而且可以成为很有用的。如果一个包
括相当大数量个别物品的产品组被每周核查并计数缺货的物品数,该结果可被相当
好地同每年的缺货次数这一统计概念联系起来。
如果,例如,此产品组中有120种物品,而且服务的目标水平是每物品每年
一次缺货,则每月平均总缺货次数不应超过10种物品。这提供去证实安全存货是
足够的或要求更好的作业控制的一种简便方法。
另一常用的客户服务的统计度量规定需求总件数将被货架上现有存货满足的一
个百分比。例如,如果该年度总需求被期望达到26,000件,而希望欠交订货
只限于1000件,则服务百分数就是25/26=96%。这一客户服务的度量
通常必须设置得比使用每年缺货次数作服务──度量百分数时要高得多,以便提供
足够的后备存货去生成相当的服务水平(3).以缺货次数或欠交件数为基础的服
务度量并不度量缺货期的长短,它们也并未指出重要的客户正得到服务或有利可图
的物品正在被发运。倘若要求这样的度量,可在计算安全存货时通过调整个别物品
的服务百分数而得到。这样的度量也涉及跟踪实际绩效方面大得多的开支。
在应用新的度量或改变客户服务的度量之前,应注意下列:
1、仿真受控库存的实际作用以确定所建议的统计度量当前使用得如何。没有
一种服务的统计度量能够完善地使它与实际完善地互相关联,为了在日常的库存情
况下达到实际所要求的服务水平,永远应将统计的服务水平设置得稍高一些。这种
仿真可用手工来做,但大多数实际应用将要求采用计算机。
2、实际达到的服务水平通常略低于统计的服务水平。这是因为统计服务水平
通常只度量一个特征,譬如欠交的总量或缺货次数;而其它特征(譬如缺货的持续
时间)也对不良的客户服务起着作用。还有,理论上的基本假设在实践中往往被违
反。
3、使用所建议的统计服务水平,开始使用控制系统并在经验表明只需较
少后备时就削减后备存货。
4、一旦统计服务度量已经建立并运行起来,其实际威力可用来说明将一系列
物品从一个服务水平改变到另一服务水平的经济性(详见第8章)。
5、客户服务的统计度量只对付正常提前期上需求中的变差,它们并不考虑机
器故障、罢工或质量问题等因素,而这些因素对补货提前期影响极大。反之,由于
正常提前期通常是在服务的统计概念中被采用的,一位好的主管人往往能使他的部
门表现得比统计量所指示的要好得多,因为该部门对客户需求的变化反应极快。该
主管人控制提前期从而也控制了客户服务。
统计量的价值
虽然订货点的统计学计算在概念上是简单的,但它比直觉方法要费劲得多。这是否值得?回答是断然地值得,因为统计学技法实际地把后备库存分配到最需要的
地方而不是将它平均地分配到全部库存中去。
图5-14所示为根据经验法则分配后备库存的一例,例中对物品P.Y与Z
的后备水平都设为1周的供应量,它们的平均周需求相等。物品P销售给许多客户,
其销售史的标准偏差为261件。物品Y的预测平均需求与物品P相同,但它卖给
少数客户,所以其需求更不稳定,它的标准偏差是551件。物品Z的周平均需求
同物品P与Y一样,标准偏差同P一样,也是261件。它是低值物品而生产调整
成本是高的,因此,其订货量大,等于6500件。所有物品都假设要有1周的补
货提前期。
┏━━━━━━━━━━━━━━━━━━━━━━━━━━━━━━┓
┃ 经验法则=1周的供应量 ┃
┣━━┳━━━━┳━━━┳━━━┳━━━┳━━━┳━━━┳━━┫
┃物品┃周需求 ┃订货量┃标准偏┃1周储┃标准偏┃交货* ┃缺货┃
┃ ┃预测(件)┃ (件) ┃差(件)┃备(件)┃差个数┃服务率┃次数┃
┣━━╋━━━━╋━━━╋━━━╋━━━╋━━━╋━━━╋━━┫
┃ P ┃ 500 ┃ 500 ┃ 261 ┃ 500 ┃ 1.92 ┃ 97.2 ┃ 2 ┃
┣━━╋━━━━╋━━━╋━━━╋━━━╋━━━╋━━━╋━━┫
┃ Y ┃ 500 ┃ 500 ┃ 551 ┃ 500 ┃ 0.91 ┃ 81.9 ┃ 9 ┃
┣━━╋━━━━╋━━━╋━━━╋━━━╋━━━╋━━━╋━━┫
┃ Z ┃ 500 ┃ 6500 ┃ 261 ┃ 500 ┃ 1.91 ┃ 97.2 ┃ 0 ┃
┣━━┻━━━━┻━━━┻━━━┻━━━┻━━━┻━━━┻━━┫
┃总计 1500 11 ┃
┣━━━━━━━━━━━━━━━━━━━━━━━━━━━━━━┫
┃ 每年缺货2次时要求统计后备 ┃
┣━━┳━━━┳━━━━━━┳━━━━┳━━━┳━━━┳━━━┫
┃物品┃每年订┃ 交货服务率 ┃标准偏* ┃标准偏┃要求的┃ 缺货 ┃
┃ ┃货次数┃ ┃差个数 ┃差(件)┃后 备┃ 次数 ┃
┣━━╋━━━╋━━━━━━╋━━━━╋━━━╋━━━╋━━━┫
┃ P ┃ 52 ┃50/52=96% ┃ 1.75 ┃ 261 ┃ 460 ┃ 2 ┃
┣━━╋━━━╋━━━━━━╋━━━━╋━━━╋━━━╋━━━┫
┃ Y ┃ 52 ┃50/52=96% ┃ 1.75 ┃ 551 ┃ 965 ┃ 2 ┃
┣━━╋━━━╋━━━━━━╋━━━━╋━━━╋━━━╋━━━┫
┃ Z ┃ 4 ┃ 2/ 4=50% ┃ 0 ┃ 261 ┃ 0 ┃ 2 ┃
┣━━┻━━━┻━━━━━━┻━━━━┻━━━┻━━━┻━━━┫
┃总计 1425 6 ┃
┗━━━━━━━━━━━━━━━━━━━━━━━━━━━━━━┛
* 取自图5-7 安全因子表
图5-14 确定后备存货时统计量的价值
如图5-14所示,所有物品都设1周的供应量作为后备存货水平将引起每年
约11次缺货。为这些物品各自计算出统计的后备存货将使缺货次数降为每年6次,
同时总后备量可降为1425件。每一物品的后备要求都与经验法则所设定的不同,
这是因为:
1、物品P的订货量很小,所以缺货曝光次数大(每年52次)。
2、物品Y需较大的后备存货,因为其需求更不稳定。这一较大的变化导致较
大的标准偏差。
3、物品Z订货量为6500件;每年只有4次曝光于缺货。事实上,物品Z
要保持每年缺货不超过2次无需在预期的需求之外再增加后备存货。
统计法结果更佳是因为直觉技法不能考虑确定后备存货所要求考虑的全部因素。
它们是:
1、预测误差
2、提前时间
3、订货量
4、所希望的服务水平
此例说明虽然有困难而且开销大,采用统计方法去控制库存还是值得的。用这
些技法更好地去分配后备存货,从而获得在不增加缺货次数的条件降低库存的1/3
或更多、或者在不增库存的条件下减少缺货次数到原来的1/3这样的结果,并非罕
见的事。
对成千种物品应用统计技法进行计算所需现代计算机与软件程序都很容易弄到
而且相当便宜。由于不能恰当地去应用它们而带来的过量库存与不良的客户服务,
其代价要昂贵得多。
原理18.用经验法则来设定后备存货不行,因为这些法则忽视了需要它们的
理由。
虽然统计订货技法能在公司的经营中产生相当大的进步,它们应该被谨慎地、
具有常识地去应用。思想上要牢记库存的ABC分类法。高价物品应受到最紧密的
注意。有时甚至把A类物品隔离为“顶A”(“TopA”)类物品, 它将受到物料
控制经理个人的经常注意。这些物品当然应该具有定期地使用统计技法把它计算出
来的浮动的订货点;有时,采用更为精确的技法去得到这些库存控制中的最大节约
也是值得的。另一方面,即便有计算机可用,可能也不使用统计技法去控制低价物
品;因为有秩序地去应用较简单的技法就已经非常有效了。
统计的概念不仅有助于实际工作者去降低库存,而且懂得这些概念可使他们更
好地把握库存系统的日常作用。大多数物料控制人员经常面临的问题之一就是库存
中必须持有的物品的品种数目日益增多。更好地了解库存的行为特征当然不会消除
这一趋势,但更好地了解库存系统的作用有助于实际工作者去对付这种趋势。下面
举一简单例子。
在大多数企业中需求的特征之一就是较活跃的物品具有较稳定的需求,而较不
活跃的物品具有变动不定的需求。存货记录通常表明,平均需求为每月10件的物
品往往很少有哪个月份的需求会接近于10件──它很可能是0或30,虽年度需
求量的平均值是每月10件。另一方面,如果需求为每月平均2000件,则很可
能很少月份的需求会超过3000或──最多──4000件。对于大众喜爱的物
品,需求很少会超过平均需求的两倍,而对于活动性低的物品,其需求可能时常达
到平均需求的三至四倍。
随着更多品种物品的加入库存,几乎总是需要提高总库存水平。不熟悉库存控
制的人员不会立即理解这一点,因而时常提出这样的问题,如果我们去年每月出售
1000件红色附件而今年我们仍将每月出售1000件,不过要分红、白、兰三
种颜色,为什么你的库存必须增加呢?实际情况可能如下表中所示:
─────────────────────────────
库 存 提前期中的需求 后备存货
─────────────────────────────
A.只存红色附件 1000件 300件
B.红色附件 160件 100件
白色附件 420件 200件
兰色附件 420件 200件
──────── ────────
总计 1000件 500件
─────────────────────────────
在这一假设的例中,用三种产品替代一种产品要求增大后备存货才能提供同原
来一样的服务水平,因为三种产品的需求量都较低,其结果是需求的变差性增大了。
有一组作者(9)注意到如果一家公司增多分支仓库──库存分家的极好例子
──则库存后备将随所包含的分配点数目的平方根而变。若一家公司使用300件
后备存货,今若增设两个仓库(设它们平均分担需求的供应),则达到与原先同样
服务水平所要求的后备是:
1个分配点的后备
后备(每一分配点)=───────────
√分配点的数目
300
=─────=173
√ 3
增多产品大类中品种的数目也会加重批量大小的问题。倍增通过一个部门的品
种数意味着或者要运用大于经济批量的批量或者要倍增生产调整小时数或者在这两
种方案之间采取某种折衷。这就进一步强调缩短生产调整时间的必要,详见第二册
(6)。
这些是物料控制实际工作者每日面临的问题的典型例子。知道了库存的行为特
征,这些实际工作者至少可以了解可能会发生什么问题,而他们如果在应用统计概
念方面足够机灵的话,就可以向管理者提出每种情况下的有效替代方案。他们可以
在知道所有的后果的情况下去作出决定,而不是在事后再去了解这些后果或者误认
为库存的增加是由于物料控制不好引起的。
对于任何类型的订货系统,要牢记最重要的一点是它应该管用。统计学能为实
际工作者提供有用的工具,但其结果将取决于他们的良好的辨别力以及在应用这些
工具中的判断力。详见第2册(6)。
使用的注意事项
第一次应用统计技法时,建议实际工作者在应用到整个大类产品之前先在一些样本物品上做试点以熟悉这种技法的概念及局限性。然后,实际工作者可能要在把
它们应用到B类物品之前先扩展到计算全部A类物品的订货点。把它们应用到C类
物品需要慎重──事实上,可能永远也不值得花这样大力气去弄低价库存物品。
使用指数平滑法预测提前期中的需求并使用更新了的MAD去确定后备存货,
这样定期地重新计算订货点是可行的。在工业中广泛地使用计算机为成千种物品每
周地更新着订货点。计算机制造商与软件商提供有可立即被实际工作者使用的程序,
让它们用这些技法去作试验并确定它们如何能应用于他们自己的公司。这些程序于
是就可用来形成计算机应用程序的核心。这一办法把编计算机程序的工作,获得有
用结果所需的时间以及所涉及的费用降低到最小限度。这些技法可以每周地应用,
然而,并不是说它们就应该这样去使用;专业工作者最怕的是不加人工评审或控制
地去应用一种机械的技法。
除非一种技法的基本假设被人们理解,否则它不会被成功地应用。各种订货点
技法的变体都假设:
1、使用将是连续的而且希望在发生缺货之前立即补货
2、以相当均匀的速率实际地使用
3、提前交货是允许的但延迟交货是不允许的因而应尽可能地避免
4、安全存货将对缺货提供足够的保护
5、能力与物料将足以用来处理已发放的订单
定期评审技法
另一主要的库存控制工具是定期评审技法,它往往被称为固定周期技法。此法中,库存记录被定期地评审而且每次评审时为每种物品办理补货订单。评审周期可
以是1周、2周或1个月,看情况而定。订货时,把存货提高到使现有总量或已订
货总量达到一预定的目标水平。
这一技法应当同传统的订货点法作对比。在传统订货点法中,每作一次登录都
要评审一次库存记录,当现有量与已订货量的余额达到某一预定的订货点时就办理
一个补货订单。在订货点法中,订货量是固定的,通常就是EOQ。
定期评审法的适用场合是:
1、需多次小量从库存提货,以致每次提货都登入记录是不实际的。食品超级
市场、汽车零件供应店以及类似的零售业属于这一类型,例如电子的与机械的机器
制造业中的服务零件业务。
2、订货成本比较小。这发生在从一个来源收到许多不同物品的订单或写出了
从一个中心仓库向一分支仓库转移许多存货物品的订单的场合。
3、在一次订货许多物品以构成一生产日程是值得想望的场合,例如,可使该
系列物品的设备调整组合起来或通过一组合订单能从一供应商获得折扣或通过定期
发运满载车皮而降低运费。
目标水平是下列需求之和:
1、提前期中的预测需求(DLT)
2、评审周期中的预期需求(DRP)
3、后备存货(R)
其中的第一项与第三项与订货点的要素是相同的。显然,倘若两周内不再评审
库存记录,则这一期间中的预期使用量必须加到提前期中的需求上去,因为只有经
过了这两周之后提前期才能开始。后备存货可用本章前面讨论过的方法来计算。
目标库存计算的一个简单例子如下:
提前期 = 1周
提前期中的预测需求 =20件
评审周期 = 2周(平均订货量=2周的供应量)
评审周期中预测需求 =40件
后备存货 =30件
目标库存水平(件) =DLT+DRP+R (5-5)
=20+40+30=90
使用这一库存目标,存货将每两周评审一次而且通过订货使总量达到90件。
例如,在首次评审时现有库存与已订货量的总计可能为70件,于是将再订货20
件。在下两周内,需求可能总量达45件,这就是第二次评审时将要订货的数量,
因为要恢复总计90件的目标水平。关于定期评审应注意下列要点:
1、总的提前时间实际上等于交货提前期加上评审周期
2、延长评审周期就等于延长提前时间并将要求持有较大量的后备存货
3、订货量等于刚刚过去的评审周期中的实际需求
4、平均库存水平等于评审周期中需求的1/2加上后备存货。
两种简单订货方法
对于工业库存中常见的许多低年值物品,往往不值得采用前面讨论过的正规方法。有两种常用方法可用来控制这些无记录的低值物品:两箱法与目视评审法。
两箱法:把相当于订货点的一部份存货存放在第二只箱子或容器中隔离起来,
然后加上封条。当第一只箱子中的全部开放存货被用完时,打开第二箱或后备容器
并通知物料控制人员订货。这是对低值物品保持控制的实用方法。应用中最常遇的
问题是:
1、缺乏足够的训练与恰当的纪律时,这种系统很快地变坏。不懂这种办法的
人员将把后备存货用完也不通知任何人,或者收进补充物料而不正确地去区分开放
存货与后备存货。
2、一旦被确定之后,永远不再去评审第二箱中要放多少物料。随着该物品需
求的改变,这一数量不再足够或变得太大了。
两箱法最好应用在补货与库存维护有专人可以委托的受控存货室中。这样做时,
此办法叫做银行存货法。若物料存放在车间里放开使用,此法很难行得通。
目视评审法:存货被定期地核对(也许每周一次或每两周一次)并把每物品订
货到一预定的存货水平。这些水平被陈述为一看就明白的数量如“1/4箱”与“
6个深”作为重订货点而且通常规定的订货量是大的。当保管存货的责任不能委派
到个别人时,此技法远比两箱法成功。它对邻近使用地点的车间存货很管用。在提
前期短而且供应商要末发货要末就取消(欠交订单)从而除了最后一份订单之外无
保留前已订货的物料的任何记录之必要的场合尤其管用。当然,这是许多零售商店
──特别是大的食品超级市场──所采用的主要技法。使用这种方法时涉及三个主
要问题:
1、必要的定期评审存货水平的工作没有做
2、由于现场管理不好,存货未被放在恰当地点,评审者未能发现实际在手头
的全部库存
3、没有经常核对订货目标,当需求改变时,使它变得过时了或无用了。
倘若注意了下列各点,则只需最小限度记录保管工作的低值物品控制方法可以
得到非常成功的使用:
1、ABC库存分类法的基础是持有较高库存水平的低值物品而且化费最小限
度的力气来控制它们。然而,必须记住,一条装配线或包装线可以因为缺乏一种C
类物品(同缺乏一种A类物品一样地)而停工。不要忘记控制低值存货的基本规则
是要有足够的数量。
2、倘若对高值存货更紧的控制并不能补偿由于低值存货较松的控制而增多的
库存,则此法并未带来好处。后者节省下的时间必须用来降低高值库存。
3、目视控制时常用于松控制而永续记录常用于紧控制:但没有哪一个是必须
如此的。工业中一个普通的事例是飞机工业中的铆钉。铆钉单价很低,但年度使用
量巨大,使它们成了A类物品。使用目视技法控制此类物品可节省许多登记记录的
时间,但其库存水平可以应该被控制得非常紧。
4、把一切低年度金额使用量物品都应使用目视评审技法来控制作为一般规则
是不好的。一种只在一个产品中每年使用一次的组件是否也要每周去目视核对它呢?
对这种物品应该用物料需求计划。
原理19.简单实际的技法可能提供更为经济的库存控制。
分时段订货点法
传统的订货点技法有几个主要问题:1、它缺乏提出被修订的订单“需要”日期的能力。
2、在发放当前的一个订单之后,它不提供将被发放的未来订单的信息。
3、它难于处理已知的特定时间的未来需求。
4、它难于处理季节性或周期性的需求。
5、它不给出提前的警告就触发订货。
把订货点数据按时间分段可以克服这些困难并提供额外的利益。物品Z的数据
如下:
预测=20件/周 订货量=100
提前期=2周 后备存货=55
现有库存=80件 已订货量=第2周到期100件
订货点O.P.=(2×20)+55=95件
为提供更有用的图形,该数据可分时段显示如图5-16。此显示的逻辑是采
购与制造的基本逻辑:
1、要求是多少?(预测)
2、现有存货是多少?(现有量)
3、已订货多少?(已订货量)
4、必须于何时得到更多的?(已计划订货到达期)
5、它们必须于何时订货?(已计划订货开始日)
周 次 1 2 3 4 5 6 7 8 等等
──────────────────────────────────
预测 20 20 20 20 20 20 20 20
已发放订单 100
推测的可用数 60 140 120 100 80* 60 40**100
已计划订货:到期 100
已计划订货:开始 100
*已到达订货点
**后备存货被打入
──────────────────────────────────
图5-16 分时段订货点法──备货生产产品
注意新订单是计划在推测的可用库存将降到订货点(95件)的那一周发放的,
虽然这并不是用来确定订单发放日期的方法。没使用计算得来的订货点。该技法使
用后备存货(55件)作为目标去建立订货到期日,然后扣去提前期就得到订货开
始日期。它安排一批收货去应付已计划的需求以保护后备存货。如果像许多用户已
经做的那样,先从现有数字扣去后备存货,再去计算订货开始时的可用总量,其结
果将是一样的。
由于实际需求是按每一期间对照预测而记录的,被推测的可用存货数字可以被
重新计算。因此该技法能指出已发放订单现在需要比原计划提早或推迟,也可在必
要时挪动已计划订单。供方(供应商或工厂)更快地响应这类信号会允许以较低的
安全存货来维持客户的交货。
利用这种分时段的格式克服了前述的传统订货点法的五个困难:
1、可以提出不同于发放订单时所定应交货日期的订货需用日期。
2、只要预测被相信是可靠的,就可以把未来的订货推测到同样远的未来。
3、已知的未来需求“块”可以插入(或替代)任一期间的预测之中。
4、季节性或周期性的预测可直接被使用。
5、未来活动、已发放订单的状态以及已计划订单全部都表示在分时段显示中。
原理20.分时段的订货点数据大大地增强了此技法的威力。
这些好处的代价是数据处理的要求要大得多,而且当需求围绕预测平均数变动
时可能带来“摇摆不定”。该技法作出反应去保护已计划的后备存货;它不使用后
备存货去阻尼实际需求中的变化。
图5-16所示为一备货生产产品的分时段订货点法。此技法也可应用于订货
生产产品,如图5-17所示。在这里,预测被收到了实际订货所替代,而制造被
安排得去适应实际情况。
预测=20件/周 提前期=2周 订货量=批对批
周 次 1 2 3 4 5 6 7 8 等等
───────────────────────────────────
实际─预测 18 15 21 19 20 20 20 20
已发放订单 18 15
推测的可用数 -21 -19 -20 -20 -20 -20
已计划的订单:到期 21 19 20 20 20 20
已计划的订单:开始 21 19 20 20 20 20
───────────────────────────────────
图5-17 分时段订货点法──订货生产产品
服务件需求的处理
在服务件库存的补货中,需求来自客户而且必须被预测,分时段订货点法非常有用。它能处理间歇性的需求,也能处理各期间都有需求的预测。它可应用于保管
在同生产性存货相隔离的存货室中的服务件,也可应用于现行生产中已不再使用的
服务件,即使它同现用物品存储在一起。
服务件与现用物品完全相同而且二者存储在一起时,可通过把前者的预测需求
与后者的计算需求相结合的办法得到控制。这要靠第六章所述的MRP技法来完成。
分支仓库需求的处理
许多公司有广泛分布的分配网络,成品库存被存储在邻近客户的分支仓库中。分支仓库由地区仓库供应。地区仓库可能是单独的设施,或可能位于一家制造工厂。
地区仓库由一家或多家制造工厂供应,它们既满足客户的订货也发货给分支仓库。
分时段订货点法为分支仓库的库存补充计划提供了一种良好的工具。更好的一种技
法是本章前面详述过的固定周期──可变订货量(目标)法。它同定期评审分支仓
库的存货水平以及正规地安排给分支仓库的交货一道工作得很好。这种技法详见附
录Ⅶ。这些技法的成功应用详见第二册。
独立/相关需求
1965年J.A.Orlicky建议在制造业中区分两种类型的需求。他用独立需求来描述对于与一家公司的库存中其它物品的需求无关的成品或组件需求。这种独立
需求的特征是客户对成品、中介体或服务件的订货。他用相关需求来描述直接由生
产一母物品或其它伴随物品的日程计划所确定的物品的任何需求。相关需求的典型
是原料、采购的或自制的零件或成份以及自制的子装配件、附件与附属品。
Orlicky建议将这种区分作为确定选用什么订货技法的一条准则。 独立需求必
须被预测,传统的或分时段的订货点技法是正当的(而且是唯一的)可用技法。相
关需求可以计算,物料需求计划是正确的技法。这一一般准则,或原理,是一有用
的指导,但并非必须不惜一切代价去服从的牢不可变的定律。在其基本假设为有效
的而且必要的纪律被维持的场合,比较简单的、不大昂贵的传统订货点法、两箱法
或定期评审法均可被非常有效地使用于相关需求物品。详见第二册。
原理21.Orlicky的独立/相关需求准则提供选用订货技法的良好指导。