浅谈质量管理
质量是企业的根本,如何搞好质量管理,关系到企业的前途与未来。我一直在思考这个问题,也经常与质检员探讨,苦于想不出什么十全十美的办法,要说有一点思路的话,总觉得不成熟。我也曾试探性地与各部门管理人员交流过,反对多,赞成少,许多人对我讲:“我们一直这么做的,不也从8台缝纫机发展到了今天的规模”,许多干部缺乏忧患意识及创新精神,习惯思维占了大多数,而现在国际市场、国内市场又非常不景气,外贸单的质量要求又非常高,面对如此严峻的形势,我们的质量管理该如何搞?下面我把一些不成熟的想法向您汇报,请潘总指导和批评。
首先,我们先分析、总结一下公司目前质量条线现状:
1、小组检验员忙于剪线头、整理衣服,根本无法按照检验规程和程序检验每一件衣服,漏检现象严重。2、小组检验记录不全面、不真实,没有正确反映存在问题,下机正品率甚至能达到95%~98%。3、小组检验员直接受车间主任领导,条线不清。4、小组检验员(质检员)工资按小组(车间)产值计算,没有与其工作业绩直接挂钩,仅仅通过质量扣款体现其工作能力,主次颠倒。5、质检员忙于封样、挑商检,无法顾及整个车间的工道质量,对过程缺乏有效控制。6、主任抓产量,质检员抓质量,这是一对矛盾。产量提高会影响质量,质量提高会影响产量,主任对质检员指手划脚的现象严重,条线不清。7、小组检验员文化层次较低,年龄偏大,接受新事物能力差,培训效果不理想。8、培训频次、力度不够,培训内容单一。9、质检科长忙于应付出厂检验及客户验货,条线管理除了每月三次的旬检外,几乎是空白。10、质量奖惩制度不完善,作用不明显,罚多奖少,甚至有现在罚,年底补现象,造成主任、质检员不重视。11、技术科的工艺纪律检查少之又少,等到大货发现问题互相推脱。12、有的款式因交期紧,排的流水线过多,造成工艺跟单员疲于奔命,指导不周。13、过程控制力量薄弱,人员太少。(一个车间只有主任、质检员两人)14、组长能力有限,一半以上不能独立封样,安排流水线,更谈不上看懂工艺单,无法对小组质量进行有效控制。15、质检员对小组检验员缺乏系统的辅导及管理,或者讲管理不到位。16、样衣确认时,主任、质检员不做记录。针对上述情况,下面谈一下我的想法:
1、理顺条线管理,把生产和质量两条线明确分开。※ 质检科负责质量条线,即质检科长 质检员 小组检验员※ 生产科负责生产条线,即生产科长 车间主任 小组长※ 质检科长、后整主任 后道流水检验员车间主任作为车间的最高领导者,主抓产量,同时兼顾质量,其管理对象为全体车间人员,但管理内容应为生产管理;而质检员的管理对象为小组检验员,管理内容为质量管理,因此车间主任无权对质检员及小组检验员的工作进行干涉,更不能随意安排、调动检验员工作。至于后道流水检验员由后整主任负责日常管理,质检科长负责抽查、监督、指导工作。2、加强外部监督管理※ 公司体系部对所有检验人员质量记录的检查,包括术语使用的准确性,操作的规范性,检验熟练度,记录准确性,检验标准掌握程度,检验及时性等内容。这里有一点需明确,就是检查人员文化层次要高,领悟力强,且必须进行专业训练,熟知检验规程。换句话说,检查人员可以不会做衣服,但必须能找出问题。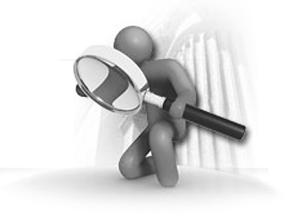
※ 公司技术科的工艺纪律检查。以上部门,发现问题后需及时反馈给质检科长,由质检科长处理。3、改变目前检验人员工资分配方式 组长工资按个人秒数和小组产值(即工作能力)计算,同样检验员工资应按其检验能力评定其工资,不能本末倒置,拿小组产值来计算检验员工资。我们一直提倡后道监督前道理念,因此检验员基本工资(占总收入70%)应以后整流水检验计算的错漏检率来衡量,对应错漏检率6%、7%、8%、9%、10%、11%,设6档基本工资,达到那一级就拿那一级工资,促使小组检验人员不断提高自身技术能力,最终多拿工资;而小组产值(或生产件数)应作为生产奖金(占总收入30%)来看待,多检多得。另外,文明卫生抽查情况或培训考试成绩等等内容以扣款形式体现。同样,质检员、后道流水检验员的工资也可以参照上述方法,只不过定的标准不一样罢了。4、小组检验员的人事安排由质检科统一负责,并且实行轮岗制度,避免后整错漏检的局限性。5、增加质量条线管理人员 目前一个车间仅有车间主任、质检员两个管理人员,我倾向于增加质检员或增加小组半成品检验员(即工道控制员),通过对过程控制来提高下机正品率。因为成衣的检验都是事后检验,只有新款工艺辅导到位,再加上半成品的控制才能切切实实提高下机正品率。6、择优挑选组长 做到个个组长都能独立封样,安排流水线,减轻质检员负担,让质检员有更多精力进行过程控制。同样,通过合理调整后道流水检验员,让经验丰富、技术水平高的检验员脱出来,从事挑商检工作,从而避免因质检员挑商检而发生车间过程失控现象。7、持之以恒开展检验员培训 目前我们已对一至六车间小组检验员进行了一轮培训,从最基本的知识开始,即培训检验操作流程。培训过程中,我们发现有40%~50%的检验员没有按照标准流程来操作,这个部位看一下,那个部位看一下,漏检现象严重,如果连一套标准的检验流程都不能掌握,那可想而知其错漏检率会有多高。培训结束后,立即组织考试,看其对检验流程的掌握程度,不合格的马上再教,直到全部合格。从这次培训的情况来看,我们的检验员确实很不理想,今后一要加强培训;二要择优招聘;三要建立淘汰制度,不合格的坚决不能上岗。8、根据ISO9001∶2000标准的要求,明确岗位职责,引导各个部门按照质量手册开展工作,确保体系运行的有效性。
以上仅是我一些不成熟的看法,谈不上模式。不妥之处,敬请领导批评指正。