在丰田的生产现场,我们会很容易地看到包含“5S”看板在内的一套精益工具。但只有深入地了解这些工具背后的原则,才能体会到,“消除一切可能的浪费”的精益理念,如何渗透到企业日常工作的点点滴滴之中。
要尽量剔除看板
走进一汽丰田天津第二汽车制造厂的总装车间,第一印象就是整洁、有条理,各类区域划分清晰,物料堆放量很小。门边的配货区整齐地码放着装满零部件的物料筐,每个物料筐上都有一个用透明胶带粘贴着一张装在小小的透明塑料袋中的纸卡片。每个筐里工件的种类和数量都和那个纸卡片相对应,同类的被码放在一起。旁边有好几个工人在忙碌,将物料筐移到推车上,装满一辆车后整装待发。那些装在袋子里的纸卡片就是丰田生产线上最典型的一种“看板”。
这种看板上标明了供应商的名称,生产厂的收货部门,使用该工件的场所,零件的编号、名称及数量。看板上还有条形码以便实施自动化分拣。
每一个或一箱工件在整个供应链当中传递时都带着各自的看板。从配货区被运到生产线上的物料筐都放在紧挨着生产线的补料区。当一个筐里的第一个工件被生产线上的工人取走时,看板就从物料筐上被摘下,并放入手边的看板信箱里,表示需要从配货区再补一筐该工件。没有被启用的物料筐的看板则不会被摘下来。工段的班长隔半个小时就将整个工段内所有看板信箱里的看板收集起来,放到该工段的看板收集箱中。配货区的值班邮递员每隔半个小时就会骑着自行车沿着生产线依次收走各个收集箱中的看板,送回到配货区的分拣处,自动分拣机依照各个看板上的条形码对看板进行分拣,一个条形码对应一个供应商。如果是提取看板,则在配货区被粘贴在一箱新的零部件物料筐上;如果是生产指令看板,那么从供应商那里来送货的司机在卸完货之后会到分拣室取走相应的看板,带回他们的工厂,供应商根据收回的生产看板将新的零件交付给看板上标明的工厂。
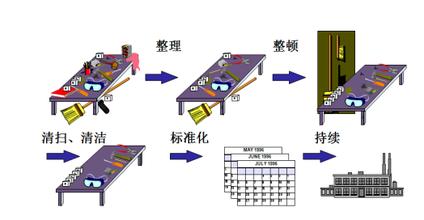
传统的生产系统是一种“推进式”系统,只能根据预测进行不均衡的生产。丰田的精益生产方式则是依靠且只依靠客户的真实需求拉动、运行生产系统。其无浪费的理想状态是形成一个不间断的价值流,只在客户需要的时候才提供其所需数量的产品。
然而,现实情况是,从原材料到交付最终产品给客户的过程中总是不可避免地存在一些中断,因此必须在必要的环节保留一些必要的存货,作缓冲用,以便能够在还没有用完之前就进行补货,只要是根据使用情况确定的缓冲就是精益的拉式制度。由于工厂可能占地相当大,工件的供应者相距可能甚远,为了设法让组装线开始使用某个工件、需要再补货时能够发出信号给相关人员,丰田当年才引入了看板的概念。
其实,看板泛指能够发出信号的各类标示板、公告栏、卡片、空物料筐、空推车等。在丰田,使用各种看板的所有操作被视为看板制度,用以管理并确保在准时生产制度下材料的递送和生产。据说,在丰田的每个大装配车间都有两个以上的看板站,每个看板站在每一轮班上需要传递的看板数目大约10000个。而且利用看板传递需求信息,可以将需求的放大率控制在最小范围内,最大限度地保证了需求的传递准确性。
“看板制度是在无法实现真正的零库存不间断生产的情况下,不得已采取的一种在必要的地方建立缓冲存货的有组织的制度。”精益管理专家杰弗里·莱克曾这样提醒道,“真正的挑战在于必须建立起一个懂得寻找方法,减少使用看板制度,以降低存货,且最终解除缓冲库存的学习型企业。”
机器只是人力的延续
在我们所参观的总装车间发动机生产线上,我们发现在距离作业工人头顶不远处有一条黄色的绳子从生产线的一头贯穿到另一头。这条绳子被称为“生产停止拉线”。在这条生产停止拉线上,每隔一定距离就有一个警报灯,每当被拉动时,那些警报灯就会在不断闪动的同时发出洪亮的警报。
在丰田的生产线上,所有工人都有权利和义务在发现任何自己无法决策的异常情况时拉动这根生产停止拉线。警报就相当于给整个生产线传递了一个请求帮助的信号,悬挂在车间通道上方的电子信号显示板就会明确地用信号灯指出有问题的工位编号。不久工长就会闻声赶来,提供必要的帮助并对问题加以解决。而工人之所以能够判明异常,是因为丰田在自己的机器设备上设计了当探测到异常情况时可以自动报警的自动停止装置,从而让工人无须不停地盯着设备监视,也能及时察觉异常情况的发生。
丰田有一个理念,坚信机器只是人力的延续,所以人们应该致力于使机器更加适应站在机器旁边的操作者,而且所有的工人有责任和义务让自己和他们的设备确保不将次品传递到下一道工序。
这和国内许多企业的做法形成了鲜明的对比。在许多标榜“以人为本”的企业里,机器、设备是企业集体的财产,当机器出现异常时,机器的真正使用者,生产第一线的工人没有权力擅自排除故障,必须遵守一定的程序,要向专门的维修部门报修,等待专门的维护人员来处理问题。
精益生产方式有两大支柱,一个是JustinTime(即时生产),一个是Jidoka(自化)。很多人把Jidoka理解为“自动化”(Automation)。实际上,日语“Jidoka”包含“主动”的意思,中间那个字“”比汉语的“动”多了一个偏旁,表明了人的存在。丰田用这个词是为了强调给机器以类似人的智能这一概念。也就是说,只有建立在能够发挥工人主动性的即时生产的基础上,才能实现真正的精益化。
通常,人们都会想当然地以为一旦工人拉响那根生产停止拉线,整个生产线就会立刻停止下来。这就曲解了设置这个拉线的初衷——当问题出现时必须能够有处理、解决的时间。如果拉线会马上停止生产线,工人就会下意识地容忍一些微不足道的缺陷,而不愿承担停止生产线的责任。而如果拉线后生产线继续移动,工人就会更愿意在出现无法拿定主意的情况时提醒大家注意那些可能出现的问题,从而就能够调动起工人的积极性,实现更严格的质量控制。
所以,丰田为每个工序都清楚地标明了固定位置线,在拉线后生产线继续保持移动,直到抵达规定的位置,从而给工人和工长提供了解决问题的时间。只有在已经抵达该工序的固定位置而依然没有解决问题时,生产线才会停止在固定位置上。
并非为了整洁的整洁
据说,20世纪七八十年代,去日本的丰田工厂参观的美国人,第一反应高度一致,全是感叹车间的干净、整洁。有的甚至使用了这样的话语:“哇,这个车间干净得你可以把掉在地板上的东西捡起来吃!”这也是我们踏入总装车间之后的感受。不过,对于丰田人而言,他们在这方面的重视和努力可并非只是为了维持工厂的干净整洁而已。
干净、整洁、有条理的生产现场,是实行“5S”方案的一个表征。这里的“5S”代表日文的seiri、seiton、seiso、seiketsu、shitsuke,分别表示整理(整理分类,只留下需要的,去除不需要的)、条理(为每个工具、零部件规划固定的摆放位置)、整洁(保持洁净)、标准化(制定规范,以完成前3个“S”)、维持(定期检查以维持一个稳定的工作场所)。
推行“5S”是支持无间断流程与生产间隔时间,让损害品质或者导致机器故障的异常情况尽早浮现的一种视觉管理工具。
“5S”方案的一项重要工作就是设置工具图像告示牌。比如,当某个工位的工人因为发现异常而拉响生产停止拉线时,和生产停止拉线相连的悬挂在车间安全通道上方的电子显示屏上对应的工位就会变成红色。
整个车间里到处可见各种体现“5S”的指示标示,清晰的操作规范示意图、工人的健康检查结果都张贴其间的告示板等。如果对应位置上缺少东西,就会立即被发现并纠正。其实,看板也是这种视觉管理制度的一个典型范例,最终都是为了让一切问题和异常浮现出来、无处可藏,以第一时间支援一线的工人,让他们有最佳机会把工作做好。
正如天津大学经济管理学院院长齐二石所言:“丰田管理方式由管理模式和管理工具两大部分组成。其中,管理工具是可以被模仿的,无法复制的是丰田生产的管理模式。”丰田生产方式使所有人对自己的工作负责,鼓励人们去不断发现更好的方式完成自己的工作。也正是因为给人们创造了发挥自己最大潜能的机会,丰田生产方式才得以成功。