世界上没有永动机,在中国经济增长数字逆势上扬的背后,激烈的全球化市场竞争正在让中国制造腹背受敌。人口红利缩水、生产原料价格上扬、低质廉价印象的影响仍未彻底消除、低廉的加工费难以发展成为企业核心竞争力……种种原因亟待中国制造提高质量控制,将企业的核心竞争力从微笑曲线的中间部分向两端提升。
要提升产品质量,就一定会接触到统计过程控制(全拼Statistical Process Control,简称SPC)。这是一种借助数理统计方法的过程控制工具。它强调对生产过程进行分析评价,根据反馈信息及时发现系统性因素出现的征兆采取措施消除其影响,使过程维持在仅受随机性因素影响的受控状态,以达到控制质量的目的。针对以下企业里常见的对SPC操作中的疑惑,我们展开讨论一下,如何理解SPC? Q1:统计过程控制SPC与ISO9000标准体系、全面质量管理、六西格玛有何联系与区别? 统计过程控制的目标是预防原则,换言之,它的目标是实现一次合格率高(满足客户)而且稳定,简称过程稳定。并能够同时实现数据追溯能力,这与ISO9000标准体系、全面质量管理和六西格玛(DMAIC中的C阶段的主要工具就是SPC)中对过程监控、预防原则是一致的。或者说SPC是实现这些管理体系要求的一种合适的工具和方法。 它们的区别在于,SPC是利用数理统计的原理对过程数据加以监控分析的一个工具,而实现ISO标准体系等相关要求并非仅仅靠一个SPC工具就能够实现。 Q2:SPC作为一个企业生产过程中的质量控制手段,请分析一下企业在对过程监控时应该如何选择正确的控制点? 每个企业的生产过程都有很多道工序,其每个工序又有很多质量特性需要关注,如果把所有的质量特性都进行SPC控制,这样下来仅收集数据这项就需要企业投入巨大的资金,大大增加了企业的成本和负担,所以我们决不能把所有的质量特性数据都用来进行SPC监控。那么如何正确的选择控制点呢?简单的说,我们可以从以下几个方面来进行控制点的筛选: (1)关注客户对产品质量的相关要求,选择与客户要求密切相关的质量特性来做SPC控制。 (2)如果过程中存在因果关系的,优先控制“因”,或者控制工艺参数。 (3)选择容易采取调整措施的质量特性。 (4)选择容易得到精密、精确的数据的质量特性。 (5)尚属试产阶段的产品可以通过QFD、DOE、FMEA等手段来选择控制特性。 Q3:企业应用如何用好控制图,才能使控制图上的信息有效地反馈到生产现场? 首先,企业各相关人员(从高层管理员到现场的操作工人)都应该认识控制图的作用,并且深刻理解,把它当成一个过程信息的平台,依靠它来管理和改进过程,确保动态图能够实时动态地完成。接下来不仅要把控制图带到到生产现场,让现场的工人参考,更应根据控制图上显示的信息及时向现场的相关人员做好解读工作,这样才能做到控制图信息能够在企业相关人员中间做到人人理解、人人尊重、人人依靠。 Q4:常用的控制图有哪几种?企业应该如何针对自身的特点进行选择? 常用的控制图(又叫休哈特控制图)共有8种,它们分别是-R、-S、-R、X-MR、P、NP、C、U,其中前四种属于计量型数据控制图,后四种属于计数型数据控制图。 企业在选择合适的控制图时首先要根据数据属性判断数据属于计量型还是计数型。如果属于计量型,再根据样本容量的大小进行选择,X-MR适合样本容量为1的质量特性,如化学溶液、破坏性实验等很难用几个数据组成一个子组的特性;-R控制图最好处理样本容量为10以下的特性;-R控制图比较粗糙,目前已经淘汰;-S可以用于只要样本容量不为1的质量特性,但计算量比较大,手工做不现实,如果有专业的SPC软件工具,这个图是几个图中最精确的控制图。如果是计数型数据,还要看是以计件还是计点的方式控制这个质量特性,计件的P、NP图,计点的用C、U图,但NP、C图需要固定样本容量,即每次抽样检验数目必须相同才可使用。 Q5:SPC是过程管理的重要工具,企业实施SPC有无条件限制?企业应该做哪些准备? 其实企业运行SPC并没有苛刻的条件限制,企业只需要做好以下几点工作就可以运行SPC: (1)高层管理人员要支持、关注SPC工作的开展,中层管理人员要理解SPC的理论知识; (2)数据收集能够达到MSA[ MSA(Measurement System Analysis)使用数理统计和图表的方法对测量系统的分辨率和误差进行分析,以评估测量系统的分辨率和误差对于被测量的参数来说是否合适,并确定测量系统误差的主要成分。]的要求; (3)制定能够长期运行的可执行的控制计划。 Q6:企业应该如何挑选SPC系统? 根据目前中国企业的现状,企业挑选SPC系统应着重考虑以下几个方面: (1)系统功能要能够满足企业对SPC的需求,并且要有一定的成长性; (2)系统软件要简单易学、易用,不能太复杂,要考虑工人理解接受能力; (3)尽量选择成熟的商品化软件工具,因为这样的软件工具兼容性较强,用起来不会经常出现打不开等各种软件质量问题; (4)数据录入要有多样性,比如支持手工录入、自动化测量仪器导入、从其它系统中导入等; (5)软件厂商应具备咨询服务、培训指导能力,单纯卖软件的厂商很难让企业构建一套适合自己的SPC系统的。 Q7:企业实施SPC有哪些步骤?应该注意哪些问题? 企业实施SPC可以通过以下8个步骤完成: (1)识别关键过程: 一个产品品质的形成需要许多过程工序,其中有一些过程对产品品质起着至关重要的作用,这样的过程称为关键过程。SPC控制图应首先着眼于关键过程,而不是所有的工序。因此,实施SPC首先需要识别出关键过程。然后,对关键过程进行分析研究,识别出过程的结构(输入、输出、资源、活动等)。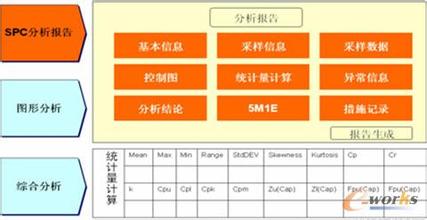
(2)确定过程关键变量(特性): 对关键过程进行分析(可采用因果图、排列图等),找出对产品质量影响最大的变量(特性)。 (3)制定过程控制计划和规格标准: 这一步往往是最困难、最费时的,可采用一些实验方法参考有关标准。具体操作时一定要使用专业的SPC软件做支持,否则仅大量的计算工作就会让人头疼不已,更不要说后面的做图分析以及实时监控工作了。 (4)过程数据的收集、整理: 在这一步工作中关键是要保证数据的真实性和可靠性,否则所做的一切分析都是没有意义的。 (5)过程受控状态初始分析: 采用分析用控制图分析过程是否受控且稳定,如果发现有不受控或变差的特殊原因,应立即采取措施。(注意:此时过程的分布中心(Xbar)和均差σ、控制图界限可能均为未知。) (6)过程能力分析: 只有过程是受控、稳定的,才有必要分析过程能力,当发现过程能力不足时,应及时采取措施。 (7)控制图监控: 只有当过程是受控、稳定的,而且过程能力足够时才能采用监控用控制图,进入SPC实时监控阶段。 (8)监控、诊断、改进: 在监控过程中,当发现有异常时,应及时分析原因,采取措施,使过程恢复正常。对于受控、稳定的过程,也要不断改进,减小变差的普通原因,提高质量降低成本。 Q8:我国在过程质量管理方面的研究处于国际领先地位,然而中国企业实际的过程管理水平离国际水平还相去甚远,请问是什么原因造成的? 这个原因很复杂,大致可以分为以下几个因素: (1)在计划经济时代,企业最注重的是产量而不是质量,对于质量的把关还只停留在检验阶段,而中国加入WTO的时间又很短,企业的竞争多是在国内的竞争,很少有企业参与国际竞争,就算是有企业参与国际竞争,也是因为中国的劳动力低下,企业的成本相对较低,在国际竞争中靠的是价格取胜而不是质量,我想这个原因可以说是时代造成的原因; (2)中国大多数企业的高层管理人员并不注重和不懂质量,他们普遍认为质量是靠检验出来的,他们更注重市场、销售、财务的数据和能力,所以无形之中在企业形成了“质量孤岛”,其质量部门也形同摆设; (3)国内几乎没有大学开设质量专业,所以造成了企业相关部门的质量技术人才不足。五年多来,我曾经拜访了600多家客户,80%以上的企业质量部门或者质量负责人员不懂质量技术,有的甚至都不知道SPC是什么。试想这样的质量部门能够很好的应用质量技术吗? (4)同样由于上述这些原因,造成了中国市场上缺乏优秀的、专业的、本土化的质量工具,大量的数据统计计算离开了专业的软件工具也很难长期帮助企业把质量管理技术应用起来。 随着市场竞争的日益激烈,上述问题迟早会一一解决,相信中国企业的实际的过程管理水平也会在不久之后迅速的赶上日、美等国家。