大批量生产硬质零件的新型大机器是朝以塑料为制造汽车的基础材料这个方向发展的一个重大步骤。
如果站在一旁观看有史以来最大的模塑机生产汽车上的塑料零件,你会产生一种眼花缭乱的幻觉,好像眼前这个85英尺长、有两台柴油机车那么宽的庞然大物足以有能力加快或减缓地球转速似的。这台巨型机器脚下是几台液压泵,总功率达1000马力,合模力足足有8800吨,就是这股力把模塑机中上下两个14x8英尺的模具紧紧合在一起。等着加热后的复合材料以每平方英寸三万磅的压力注入其中。在这个压力下生产出来的是坚硬的塑料零件,它们将取代如今仍然在汽车上使用的某些用钢或其他材料制造的零件。
戴姆勒-克莱斯勒汽车公司(DaimlerChrysler)正在试用这台价值数百万美元的机器,看看它是否能像生产糖果的机器喷出口香糖那样大批量生产汽车上的承重零件。这台机器由赫斯基注塑机械制造公司(Husky Injection Molding Systems)拥有,是该公司设在密歇根州诺维的技术中心制造的。眼下,它正用来生产200个安装在牧人吉普车(Jeep Wrangler)上的活动塑料硬质顶盖样品。这批顶盖如果能达到各项预期要求,将被安装在今年秋天投产的牧人吉普车上。
汽车制造商们还在酝酿生产另外一些更加复杂的汽车零件,但他们不愿多说。戴姆勒-克莱斯勒公司一位副总裁托马斯8226;穆尔(Thomas Moore)说:“吉普车顶盖是我们第一个实验项目。如果行得通,我们就搞更大的项目。”该公司在密歇根州麦迪逊海茨设有一个自由技术业务中心(Liberty and Technical Affairs Center),负责研究和开发下一代汽车。中心的车身工程部主任劳伦斯8226;奥斯瓦德(Lawrence Oswald)对自己的想法倒是直言不讳,他说:“我的长远目标是,此举有朝一日能使我们生产出一次成型的车身。”
戴姆勒-克莱斯勒公司并不是唯一一个朝此方向努力的汽车制造商。通用汽车公司(General Motors)卡车分部和福特汽车公司(Ford)的供应商们也正在用别的模塑技术生产不同类型的塑料零件,即一种承重部件——轻型卡车底盘,这种卡车的样车将在今年下半年出现在展示厅里。这种底盘重量轻,耐冲击,不生锈,这些都是传统钢制卡车车身所不具备的。起码来说,这些塑料顶盖和卡车底盘代表了用所谓结构复合材料的轻型材料制造成本适中的零件的新潮流。
诸如仪表板之类的塑料零件和塑料内部装饰在轿车和卡车上的应用已有时日。道奇蝰蛇(Dodge Viper)和通用公司的土星(Saturn)轿车也已用上了塑料外壳。但是,此类汽车(包括其他品牌)仍然要依赖塑料外壳底下的那层金属“空间框架”来维持其强度。由合成树脂构成、用玻璃纤维或其他纤维增加强度的各种结构复合材料远非只起装饰作用。它们有足够的强度承受汽车上路后——甚至包括发生事故时的部分主要负荷。
虽然像日本丰田汽车(Toyota)和本田汽车(Honda)这样的技术领头羊还没有宣布近期将在汽车上使用结构复合材料的计划,底特律的汽车制造商们却已经有所动作了。它们通过成立汽车复合材料联合体(Automotive Composites Consortium)来共享非专利的“竞争前”的知识。在这个成立于1998年的联合体里,一个名叫能源部的分支机构正在和由汽车业资助的全美汽车研究会共同研究一种可乘五人、每加仑汽油可行80英里的汽车的制造方法。
戴姆勒-克莱斯勒公司在研制结构复合材料方面称得上是如醉如痴。它正在冒着很大的技术风险,以图头一个在开发与传统方法大不相同的汽车生产工艺上找到出路。那台生产吉普车顶盖的巨型注塑机需要极大的液压压力——比通用和福特公司用来生产轻型卡车底盘所需的压力要大得多,它生产出来的注塑零件形状之复杂程度也是汽车制造业中前所未有的。戴姆勒-克莱斯勒并非独自在冒这个风险。该公司有一个重点依靠供应商开发新型零件及其制造方法的“扩大经营”战略,按照这个战略,开发项目的大量成本和工作正由一些机械制造商来承担,如设在加拿大安大略省博尔顿的赫斯基公司和安大略省康科德的德科马国际公司(Decoma International),后者是戴姆勒-克莱斯勒最大的配件供应商之一马格纳国际公司(Magna International)的下属机构。如果一切顺利的话,赫斯基和德科马公司便能出售更多的注塑机和塑料零件。
克莱斯勒公司早在1994年就开始大规模开发结构复合材料,它在那一年上马了一个研究项目,目的在于研制一种低成本汽车,拿到中国等地去生产。该项目的研制成果就是在1997年法兰克福汽车展上露面的“复合材料概念车(CCV)”,其外形很像雪铁龙公司(Citroen)的“双马(Deux Chevaux)”型汽车。尽管这个在第三世界生产汽车的想法后来被束之高阁,复合材料概念项目却表明,很大的零件的确可以用注塑法来制造,并且可以在汽车承重结构中占有很大的部分。尽管它里面仍然需要用一个重140磅的梯子型钢管框架,但比起原先用300磅重的框架来承担全部重量的方法则要简单得多。戴姆勒-克莱斯勒公司的奥斯瓦德说,按照CCV制造的汽车全部重量要比全钢汽车轻20%至50%。
鉴于复合材料汽车的重量较轻,人们提出了种种有关乘车者遇到事故时的人身安全问题。戴姆勒-克莱斯勒公司的工程师进行的冲撞实验表明,一辆同样大小的汽车能经受住时速33英里的撞击。不过,这项实验不是在一辆CCV车上进行的,而是在车上某些部位的塑料零件里添了加固钢材。该公司的工程师在提到空间框架时玩弄了一下字眼,说这种由两种不同材料结合的结构是“罕见框架”,它可能是奥斯瓦德设想的那种一次成型车身的基础。
奥斯瓦德说,通过研制CCV车,“我们已经证实,可以用注塑的方法制造汽车内的各种零件。”CCV车车身的四个大型复合材料部件是用通常用来制作饮料瓶的聚对苯二甲酸乙二酯(PET)做的,里面添加了短玻璃纤维以增加其强度。克莱斯勒公司当时用的大型注塑机为生产塑料垃圾桶的大急流城喀斯喀特工程公司(Cascade Engineering)所拥有,而赫斯基公司最近制造的巨型注塑机则使汽车制造商们得以用CCV注塑模具进行试验,以改进彩色注塑工艺,提高产品的表面光洁度。
奥斯瓦德说,如果能够做到这一点,复合材料注塑车身可以使装配厂取消喷漆车间,还能大大减少劳动量和工具使用数量。用奥斯瓦德的话来说,一家完整的发动机和车辆组装厂,包括一个把80至120个钢制冲压零件组装出车身的焊接车间和一个喷漆车间,目前的占地面积为200万至400万平方英尺,所需设备的成本为10亿至30亿美元,而一个制造类似CCV车的彩色注塑车身的工厂占地面积只有前者的四分之一,生产成本也只有钢制车身的三分之一。
戴姆勒-克莱斯勒公司眼下的任务是:掌握注塑吉普车顶盖的生产方法。赫斯基和德科马公司的技术人员们正在把短玻璃纤维分别同其他两种材料混合到一起,用赫斯基公司的巨型机器“喷出”顶盖样品,其中一种材料是密歇根州特洛伊的蒙特尔北美公司(Montell North America)生产的聚丙烯和聚苯乙烯的混合物,另一种是新泽西州萨米特的蒂考纳公司(Ticona)生产的PET。奥斯瓦德说:“聚丙烯比较容易成型,而PET有较高的表面光洁度,所以我们进行对比。在这两种材料里分别加上35%的玻璃纤维(这种纤维极其纤细,长度不到一毫米),这样更便于熔化后的复合材料流进模具中的每一个角落。在这两到五分钟的注塑过程中,复合材料冷却成型后,混在里面的玻璃纤维便互相交叉的固定下来,从而大大的增加啦材料的强度。”
吉普车的硬质顶盖被注塑成两部分,一个内层和一个外层,用来替代目前用另一种名叫片料成形复合材料的塑料制造的,由五部分组成的顶盖。这种新方法使顶盖的重量减少了30%,成本降低了10%,而且无需上漆。还有一个与旧方法不同的地方是,这种注塑零件的边缘不用打磨,因而不产生废料。如果试验成功,戴姆勒-克莱斯勒公司将买下这种模塑机,安装在它设于托莱多的吉普车制造厂里。
奥斯瓦德认为,这次吉普车车顶制造实验“对我们来说是一个极好的学习过程。它有种种困难,你必须在一个大的平面上推动塑料,然后再拐几个弯。我们充分利用了模塑机的全部合模力。”他又说,考虑到要留出车窗和其他一些特点,“机器上还有一套复杂的滑动平台和升降装置,以便我们做好顶盖后能打开模具,取出里面的配件。从我们为使这一切步骤实现机械化所做的工作上来看,这的确是世界上最复杂的注塑模具。”
戴姆勒-克莱斯勒公司在批准使用复合材料大批量生产汽车构件之前,要求把各种材料的成本降低到每磅1.25美元以下。如果用量不大,目前的材料价格是每磅1.50美元左右,如此看来,全面投产后,这一目标是有可能达到的。研究人员正在致力解决的另一个难题是,确保用这些复合材料制造的零件能适应各种不同的气温——从明尼苏达州40华氏度的严寒到死亡之谷的酷暑(在那里,涂了黑色的复合材料表面温度到中午可达250华氏度)。戴姆勒-克莱斯勒公司的复合材料之所以称为热塑性塑料,因为其熔点相对较低。人们担心的不是这些复合材料会在炎热中熔化(其熔点至少要达到440华氏度),而是恐怕它们在高温中变形或强度下降。为此,复合材料生产商们都在纷纷进行试验,以便生产出各种化学“变性剂”,它们能使复合材料具备所需的硬度和塑性,而且价格也能接受。
与此同时,通用和福特汽车公司也在全力研制它们自己的复合材料零件。通用汽车公司卡车分部对轻型卡车车主所做的调查表明,这些人头一个愿望就是底盘不再叮当乱响,也不早早就生锈。根据这个要求,产品设计师们恢复了在80年代搁置的一个复合材料底盘的研制项目,当时公司的经营情况很糟,新的想法很难在公司内部推行。
如今的情况是产销两旺,截至去年12月,通用公司全年轻型卡车的销售量有望比1998年增加30万辆。为了与像福特和克莱斯勒这样的竞争对手抗衡,很重要的一点就是要吹捧自家产品的优点。另一个要考虑的因素是汽车的自重。尽管美国人现在显然并不在乎每天耗费大量的汽油,汽车制造商们仍然不得不担心政府实行的企业平均燃料消耗经济(CAFE)标准,违反此项规定者将被课以高额罚金。
今年秋天,购买和原先同样大小的雪佛莱牌Siverado轻型卡车的人可以选择一种Pro-Tec复合材料底盘的车型。托马斯8226;詹森(Thomas Jensen)是通用公司的密歇根州庞帝亚克市卡车生产中心领导研制这种底盘的工程小组经理,他总是喜欢抡起一人多高的大铁锤猛砸他们的产品,以显示这种材料有多大的抗冲击力和抗破碎力。
两年来,通用公司对48辆安装了复合材料样板底盘的卡车进行了耐久性试验,试验地点是一些条件恶劣的地方,如硫矿和沥青砂岩地面。这种底盘是用添加了催化剂后凝固的“热固”塑料制成的,通用公司的实验人员用沉重的尖头钢对它进行百般蹂躏,但毫毛未损。这种已投入生产的地盘要比钢制底盘轻50磅,其中有15磅的重量是从后挡板上减下来的,这样一来,抬起和放下后挡板显然要省力多了。
印第安纳州亨廷顿的坎布里奇工业公司(Cambridge Industries)将用一种短玻璃纤维和聚氨酯塑料各占一半的混合材料生产底盘的内层配件,这是一种6.5英尺长的整体部件。该公司将使用一种名叫结构反应注塑法的工艺,它是由俄亥俄州阿什塔比拉的玻璃纤维塑模公司(Molded Fiber Glass Co.)最先开发出来的。该工艺的第一步是,由机器人用粉碎枪把玻璃纤维喷到一个做成卡车底盘形状的金属筛上,然后用高速穿过的空气把经过粉碎的玻璃纤维吸附在筛子上,形成一层膜垫。粉碎枪里装的是由欧文斯-科宁公司(Owens Corning)生产的玻璃纤维卷,里面交织着捆扎剂,即一种纤细的塑料丝,它在加热炉里加热到400华氏度达四分钟后熔化,把玻璃纤维粘结到一起。
这一步骤的产品是一种海绵状“预塑件”,硬度足以将其从金属筛上剥离下来,送到注射压缩成型机上。在两片模具完全合到一起之前,还要稍稍加压注入由拜耳公司(Bayer)提供的液状聚氨酯树脂和一种催化剂。等模具完全扣合后,这种加了催化剂的树脂就会充斥到预塑件纤维之间的所有空隙中,并且在短短九秒钟后开始凝结。在室温下经过四分半钟的化学固化处理之后,就可以把零件从模具中取出来,打磨边缘,最后再刷上一层黑色抗磨漆。
随后,坎布里奇工业公司把这种复合材料底盘内芯和钢制外加固层用胶水和泡沫块固定到一起,送到通用公司设在韦恩堡附近的卡车装配厂。在通用公司的装配线上,工人们给底盘套上弹性外壳,这种外壳使用的是一种抗冲击的复合材料,是由密歇根州特洛伊的巴德公司(Budd Co.)用另外一种名叫反应注塑法的工艺生产的。据说,这种不透明外壳的抗磨损性要比目前用在雪佛莱牌Corvette型和庞帝亚克牌火鸟型车身上的复合材料片料模塑外壳高出一倍。
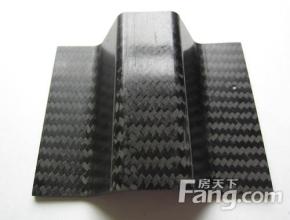
詹森说,在选择材料方面,他们并不墨守成规,老是用某一种材料,而是从成本、重量和性能几个方面来综合考虑,找出最合适的材料。他指出:“我们生产的底盘确实集中了各种材料的优点。我们在后挡板的上缘用不锈钢条加固,因为我们了解到人们经常用水泥块把这个部位砸得伤痕累累。玻璃纤维复合材料做的底盘内芯具有足够的韧性,固定在底下的钢筋则使其具备了所需的强度。”詹森有一台试验设备,它能把一个拴在绳子上的重达17磅的保龄球砸到底盘的外壳上,以表明那外壳有多大的“弹性和韧性”。
不甘落后的福特汽车公司将在2000年下半年推出它自己的复合材料卡车底盘。实际上,早在1989年福特公司就用复合材料生产了5000件漫游者(Ranger)轻型卡车的底盘。福特公司在迪尔伯恩负责重力工程的经理汤姆8226;斯韦德(Tom Sweder)说:“我们当初生产这些底盘是为了取得加工复合材料的经验,但后来由于成本太高,决定不再生产了。”
福特公司生产的一种长度较小(四英尺)的复合材料底盘将于明年安装在“探索者”卡车(Explorer Sport Trac)的样车上。这种新型底盘和原先生产的底盘一样,都是用片料模塑复合材料制造的,但它的成型性和抗紫外线性能近来都有所提高,成本也有所下降。斯韦德指出,黏合剂的耐久性增加了,凝固时间也缩短了,这样就能跟上生产线的输送速度。巴德公司将为福特公司生产这种底盘。
用来生产片料模塑底盘的复合材料成本大约为每磅90美分,而钢材的成本大约为每磅35美分。但斯韦德说,要考虑的不知是价格问题:“福特已经改变了权衡各种利益的方式。我们如今不再单单考虑成本问题,而是注重以下一些因素:汽车外壳是否经久耐用,外观漂亮,具有更高的刚性——最后一点有利于降低噪音。”
尽管人们在研制结构复合材料方面取得了长足的进步,钢材仍然是可以与之匹敌的材料。如果某种材料的生产商有所改进,它的对手也不会裹足不前。斯韦德说:“面对塑料制品和铝制品的挑战,钢铁业的确作出了反应,他们研制了一系列价格低廉、性能却是四五年前所没有的钢材。我不得不提醒我的设计人员,要重新学习如何运用钢材,因为这不是他们早先所了解的钢材。”
据《沃德汽车世界》(Ward’s Auto World)杂志报道,过去的二十年里,在汽车制造业,某些材料(如制造汽缸盖的铸铁、制造散热器的铜和制造门把手所用的锌等)的用量大幅减少,铝的用量却增加了,而钢的用量只是稍有下降:1979年,在北美生产的汽车中,钢材所占全车的重量比为55%。如今则为54%。显然,主张使用复合材料的人每走一步都得拼命为自己辩护,而主张使用其他材料的人也会寸步不让。
双方的观点能否站得住脚,一个关键的因素是:材料能不能回收利用。如今汽车上的钢制配件到一定时候就要送回炼钢炉。戴姆勒-克莱斯勒公司料到环境保护主义者会提出批评,便宣称它使用的结构复合材料是易于熔化的热塑性塑料,因此不存在回收利用方面的问题:废零件里的材料是可以再利用的。汽车使用寿命到期后,用热塑性塑料制造的零件可以熔化后生产出其他产品,如塑料家具和仿真木材等。用来制造卡车底盘的热固塑料虽然无法融化,但通用公司正在研究一种方法,把废旧卡车底盘磨碎后用作铺路的骨料。
用巨型模塑机生产一次成型汽车车身的时代可能还没有到来,但是汽车制造商们显然已经离它越来越近了。