精益生产和全面质量管理类似,都强调企业全员参与的概念,推崇持续改进的理念。因为企业经营效率的提升、产品质量的改进、成本的减少、交货时间的缩短等等运作的改善,都需要通过全体员工的共同工作和努力来实现,如果内有员工的积极参与并努力实施,这类管理活动往往达不到预期的效果和目的。
精益生产之所以能够做到尽善尽美,在于能够把责任下放到运作执行层,并通过执行层不断改善企业中存在的各种问题,极大调动员工的积极性,在日常工作中实现持续改进的良性循环。小组工作法则是实现这一目标的组织基础。
小组工作法源于日本五十年代开始逐步流行的“质量管理圈”活动,早期更多是以QC小组的身份出现, 21世纪50年代起,日本开始对现场负责人进行质量管理教育,并出现了名为“现场QC讨论会”的组织,1962年正式改名为QC小组”,开始在全国注册登记,当时第一个注册登记的是日本电电公社松山搬运机QC小组。1964年以后,QC小组支部,日本科技联建立了QC小组本部。日本是世界上按职工比例计算QC小组最多的国家,现在,QC小组在世界上发展十分迅速,已遍及五大洲的40多个国家和地区。随着QC小组的深入人心,这样的团队工作方式逐步得到大家认可,并在理论层面不断总结,是形成小组工作法的基础。应该说小组工作法是精益生产方式对传统管理模式在劳动组织体制方面的重大变革和延续;是为达到精益生产的目标,贯彻精益生产以人为中心的管理思想而采取的劳动和工作组织方法。
小组工作法的应用能够带来很多优势和好处:
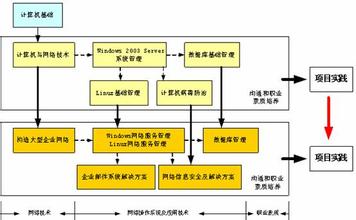
1.调动员工积极性,发挥员工的潜能,提高员工的素质
2.预防和改进问题的及时性
3.实现全员参加管理
4.改善员工之间的工作关系,增强团结协作精神
5.通过小组工作提高员工管理水平,培养管理人才
6. 减少管理层次、提高管理效率、增强企业组织的活力。
小组工作法的工作形式十分灵活,可以根据不同情况进行调整和适应:在解决技术难题时,可以组成攻关型的工作小组,有内外部专家组成,充分利用各种资源解决问题;在解决管理问题时,可以有部分管理人员和相关的人员组成小组,通过流程的优化、工作方式的改进等等手段提高管理水平,增强企业运营效率……。
需要说明的是,小组工作法本身而言也有着先天的劣势,非正式组织的身份使得工作开展十分困难,需要企业有着开放、合作的工作氛围和企业文化与之适应,同时在激励机制方面也展开相应的配合,小组工作法才会具有生命力。