精益生产的流程分析
流程分析的主要目的是准确掌握全部生产流程,即生产工艺流程、检验过程、运输过程的实际状况,发现并去除过程浪费和不合理。1、作业流程分析 作业流程分析是将作业人员的工作流程进行分析,它的目的是明确操作者的作业流程,分析作业者不同工序的分布状态与时间分配状态,发现问题并改善,制定科学合理的作业标准。(1)、作业者作业动作的标准 通过对生产活动中的全部作业动作进行逐一分析、发现并改善无效动作或浪费,制定省时、省力、安全、经济并有效的标准作业方法。(2)、作业时间的合理分配 通过对人与人、人与机械的组合作业时间过程分析,发现人及设备的等待、空闲时间,并进行有效的改善。使操作方法和作业流程更有效,现场资源得到有效利用,对作业负荷、操作设备台数及共同作业的人数进行合理分配。在上述各生产要素的基础条件具备的情况下,运用精益生产的管理工具与方法进行改善活动。2、工序间在制品的物流存储 (1)、在制品存储场地原则上集巾于生产现场,并要明确在制品最大存储量与最低订货量。其中,工序问在制品的存储量分别由:后道工序需求量、生产批量、生产周期、生产保证周期等冈素决定。对于在制品存储场地及生产现场要按“5S”要求进行定置管理。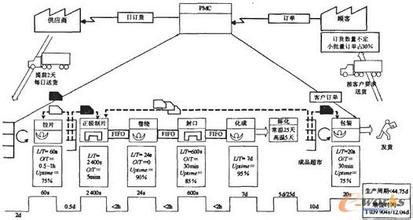
(2)、精益生产模式下生产组织的核心内容是实现工序间的“一个流”生产,它是企业管理水平的标志,是创造企业最大效益的主要手段,是工厂各项方法配套实施的一个重要内容。所谓“一个流”生产,是指生产线内部相邻上下工序之间流动的在制品数量。在任何时候不超过紧前工序的装夹数量,在运动状态上,不间断、不超越、不落地的运动过程,为此要求操作者,必须严格按节拍生产。同时,前后工序产能匹配应尽量合适,避免出现设备产能富余,造成闲置和浪费。