家里的灯泡坏了,更换一个,这是日常生活中最普遍和简单的操作。但在生产型企业中,就会出现另一副情景。近期我在一个大型能源企业的咨询项目中,通过这件小小的事情,体验了一回客户的风险控制流程。
客户基层站场(生产单位)一个屋里的灯泡坏了,需要更换,整个流程是这样的:
1. 基层站场通过ERP系统向上级分公司提出维修申请(客户单位实行了较严格的“运检分离”,站场运行单位不控制备品备件,任何维检修任务由专门的维修队伍执行);
2. 基层站场在申请表中做“风险识别”及“控制措施”(换灯泡是个标准化的操作,相关条目可由ERP系统从数据库中自动提取形成)。具体风险有:
(1) 触电风险。控制措施是:在更换灯泡之前关闭电闸;
(2) 更换灯泡的作业在高处进行,需要使用梯子,操作人员有从梯子上摔落受伤的风险。控制措施:一人操作(换灯泡),一人监护,监护者在地面扶住梯子;
(3) 操作者手中的工具和灯泡易滑落,砸到下面扶梯子的人。控制措施:穿戴防护器具(比如工服、安全帽等);
3. 上级分公司生产管理部门收到申请后做审核,如认为有其他风险还应在申请表中增加填写,主管领导签字;
4. 上级分公司将申请表转至维修队,维修队对申请表做审核,如认为有其他风险还应在申请表中增加填写,主管领导签字;
5. 更换灯泡。全过程中操作者需对每项风险做出确认,签字。
6. 基层站场验收,并将结果再次反馈至分公司。流程结束。
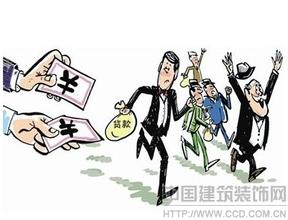
看到这样的流程,我心里产生两个疑问。1.如此繁琐的流程,是否有必要?2.客户是如何保证流程的执行的?第一个疑问旋即被打消,因为万一发生生产事故,出现人员伤亡,其成本将远远高于相比执行流程产生的成本,从理性的、损益计算的角度出发,此种流程完全有必要。但人都有惰性和侥幸心理,有章不循,“两张皮”的现象在很多企业也相当普遍,客户企业是如何做到严格执行风险控制的?仔细回顾上文“换灯泡”的例子,我想已经体现了风险控制的若干重要保障因素:
1. 风险控制的落实需要得到组织结构和运行机制的支撑。可以设想,如果客户单位实行“运检不分”,运行单位自己控制备品备件并执行维修操作。那么完全可能出现这种情况:灯泡坏了就随手换一个,需要的手续回头再补填,所有问题都被闷在一个黑盒里。如此一来,风险控制的各个环节就失去了意义。而在“运检分离”的机制下,流程跨越了各基层组织的边界,运行方和检修方不得不完成相关的手续,否则成本核算就会对自身不利;
2. 信息系统是“持续改进”的重要保障。“换灯泡”是一项最简单的操作,风险的评估还不算太复杂;可以想象在大型的维修任务中,风险项的数量会大大增加。如果没有风险数据库的帮助,每次都要依靠人脑,风险控制将会变得非常随意。回顾以上“换灯泡”的三项风险,(1)、(2)两条还比较容易想到,而第(3)条很容易被忽略。在信息系统比较完善的条件下,一旦在某次执行中此条风险被提及,就会被加入企业的风险数据库,以后无论哪个基层单位执行相同操作时,此条风险都不会被遗漏;
3. 多方位的监督可降低风险发生的概率。上文换灯泡的操作中,主要风险在于维修人员安全,但仅靠维修人员自身的风险防范意识是不够的。全过程中基层站场、分公司人员对操作过程都有直接或间接的监督控制。考核体系在其中也有很多的文章可做。
所以企业欲加强风险控制水平,与其空洞的说“提高风险意识,加强管理”,或者在出现事故后将问题归咎于“人员思想麻痹大意”,倒不如仔细思考研究一下支撑风险控制的种种管理手段更有实效。