挣扎着改变 实现5S
在重新设计之后,虽然整个空间严重受限,但依然足够操作员进行组装工作、运转小推车、寻找工具和部件。这样,生产线的监管人员就只管站在一边看着操作员进行组装,帮助操作员做一些搬运工作即可。我们每3个小时补充一次部件,以便我们有充足的时间来解决出现的问题。改进之后会有很多新程序和规则需要遵循。
由于改进后的生产线上工人不能离开岗位,即使是暂时离开也不可以,所以这种修改遭到了操作员的坚决抵制,有的生产线监管人员也持反对意见。操作员还是会离开岗位去找他们需要的部件,因为生产线监管人员拒绝接受新的工作安排。很多时候操作员在工作区内无所事事地等待,生产线监管人员并不能负起责任,主管也很少来检查监管人员的工作,而产品经理更是对此不闻不问,导致最后的产品出现了很多的质量问题。
作为精益制造工程师,我不停地建议管理层对操作员进行更正规的培训。我解释说,这些工人面临着全新的流程,需要经过培训才能自觉遵守新的规则。生产线面临的问题其实是管理层在之前没有做好培训计划的结果。
离下一次的改进计划还有两个月时间。我们的重点还是放在引擎生产线和其他改进流程的实施上。由于管理层没有部署战略目标,也没有评估我们进展的标准,因此,很难判断我们的经济效果或者改进的等级。但改进还有很大的余地,我强烈地感觉到生产线工人还需要做一些事情,以便更快地进入角色。我决定组织一个小团队来解决这些问题。
改进团队目前所做的还只是在一些地方做上标记,为一些工作区分类划别等。现在,我们要更加详细地实现5S。我的团队由生产线上的制造工程师和质量工程师组成,一共4个人。我安排使用一些地板漆、地板胶带、标签、储物箱和其他东西来获得改进生产线的可视化效果。
我们的时间很紧张,必须等生产线在星期四中午完成他们的工作之后,我们才能开始。在操作员离开之后,我们的团队开始清理地板上所有的物件。由于其他生产线还在运转,我们必须争分夺秒。
团队很快清理了地板,在地板干了之后,我们开始使用地板漆。我选择了一种标准颜色——制造业的灰色。为了让这部分生产线更加醒目,我们为整个引擎生产线的区域都喷上了地板漆。黄色的地板胶带、其他可视化的标记在灰色地板的反差下很容易被识别出来。
我的目标是在下午完成地板喷漆,这样到第二天地板就能干,这样我们才能开始放置其他可视化标志。到星期五的时候,我们花了一整天来布置黄色的地板胶带,为放置组件划分区域,包括储物箱、放置组件的架子、小推车的行进路线、垃圾桶等。我们为每一样东西都做了标记,表示这里应该放置什么东西,必要时还指定了放置的数量。仅仅经过了这一天的工作,整个生产线就显得非常漂亮,而且有条不紊。
我们这一天的工作没有白费。在第二个星期一早上,当生产线操作员看到这些场景时都大为吃惊,他们也最先认识到这样做在实际操作中的好处。几个其他生产线的主管纷纷询问,他们的生产线什么时候也能改成这样。我的经理也对生产线的改进表示赞赏,并希望它能够长久保持。
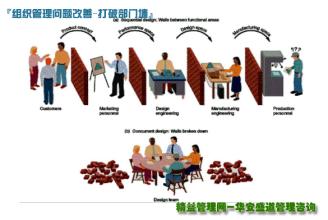
我会见了分管引擎生产线的制造工程师,讨论工作说明要细化到每个操作点的必要性。目前的工作说明非常糟糕,而且由于我们对工作顺序做了较大的调整,也需要对工作说明进行全面的修订。老的模板也很差——页数太多、文字太多。这个模板被记录在一个笔记本上,就放在生产线旁边的一个架子上。我认为我们需要一种全新的方式。我的目标是缩减这个文档——每个工作区的操作只保留两三页就够了,并且使用图案等形象的标志来处理,而不是用枯燥的文字来描述。
对公司的工作说明做如此重大的修改,我向高层管理者做了汇报,说明我们的目的和这样做的好处,并获得了批准。管理层对此感到很兴奋,认为这个想法非常好。每个人都认同我们需要新的精益制造文档。他们承诺,在我们修改完成了引擎生产线的工作说明之后,工作说明模板也会据此重新设计,变得更加标准化。
这份新的工作说明在大约两周之后完成。经过了一些审批流程之后,这份工作说明被放置在引擎生产线的工作区。我们感觉到改进5S和这个文档对工人们改变思想起到了重要的作用,让生产线主管和员工充满了责任心。
第一次的改进还没有稳定,生产经理已经在讨论第二次改进计划了。尽管我也主张要进行持续的改进,但我认为我们更有必要先解决好当前的问题,让公司能够看到实际可计量的效果之后,再进入到下一步的改进之中。
缺乏责任心
引擎生产线遵照新的流程使用了大约一周时间后,出现了新的问题。尽管这个生产线比以前更加有条理,工人们也有了所需要的工具、部件和文档,但生产线的效率依然很差。操作员对标准化工作的实现和更快生产节奏的需求有抵制情绪。他们抱怨节奏太快了。在老的生产线上,他们可以按照自己喜欢的速度做事,而且还能够随时停下来休息。他们很顽固,甚至不想作为一个团队来工作。而且,产品主管并没有强迫他们实行新流程,而是继续允许操作员随心所欲。在新的标准中,他们的行为显而易见,人们都能看到哪里出现了减产、堆积和质量问题。
新的引擎生产线设计为每天生产65件产品,平均每件用时6.46分。实际上,引擎生产线每天的平均产量只有55件左右,而且还有减少的趋势。责任被推给了改进小组/制造工程师和我。作为一个团队,我们再次向管理层说明了事实,点明是生产线监管人员和产品主管没有让操作员负起责任,任由他们破坏流程和产品标准所导致的。
为了解决这些问题,我计划要与相关人员进行多次会谈。有时候,会议临时被取消,原因是该出席的人没有到,或者讨论毫无进展。参与者只是口头答应而不付诸于实际行动。情况日益恶化,我感到非常担心。高层管理者决定先停止引擎生产线的改造,原因是进展并不顺利。管理者试图通过第二次改进计划,让公司重新走上正确的道路,而引擎生产线的问题被延后解决,但最终这个问题被遗忘了。
第二次改进计划的曙光
至此,X公司在精益制造方面已经投入了大量的时间和金钱,但是得到的回报却还很少。到了7月,第一次改进计划已经过去3个月了。X公司依然没有如我所希望的那样步入正轨。在第一次改进计划中做过的一些修改又慢慢地回到了原来的状态,原先所取得的改进成果荡然无存。回到原来效率低下工作模式的一个原因是新员工在上岗之前没有接受精益制造的培训。
正如我前面所提到的, 对所有的员工都进行培训是非常有必要的,至少他们应该知道一些精益制造的基础知识,知道在减少浪费的标准化流程中应该如何行动。但在X 公司,新的操作员只要完成了针对公司整体情况的介绍就被立即放到生产线上去。由于产品主管和老的操作员都不遵从新的精益制造流程,新员工自然也不会遵守。当很多公司进行精益制造转变时,企业文化不服从于流程是一个很大的障碍。
我依然对引擎生产线的成功很有兴趣,并继续关注着他们。虽然要从我自己的岗位上离开是很困难的,但我还是尽可能地给他们提供帮助。
第二次改进计划很快就开始了,这次X公司依然请了一些咨询师。这一次,我希望能够进一步地参与并给予成员指导。我们注意到这次公司请的咨询师不是第一次来的那些人。X公司的职员至今依然对第一次改进计划的咨询师感到不满,因为他们缺乏与队员的交流和指导。一个有组织的改进计划项目需要非常明确。因此,我们迅速组建了团队。
改进计划被安排在8月。在正式开始之前,我组织我的队员开了一个会来分析我们的流程。这个生产线被称为1065生产线,生产的是暖气和空调设备中的一个小部件,用在小货车上进行制冷。这些部件大概有25英寸的电视那么大。我让每个成员分别收集数据,用来做时间管理、库存分析、在线数量分析和浪费分析。这一次我下定决心要做好充足的准备,全力投入战斗,没有人能够阻止我。我感到现在是时候将精益制造带回到正路上去了。我打算让我的小组负起必要的责任,真正实现好精益制造的流程并坚持下去。
在第一次改进计划时,我们被告知不要做任何提前计划,完全都集中在改进计划这一周来完成。显然,这个方法的效果非常糟糕,因此我让我的小组提前悄悄地展开工作。随着时间的推移,计划正式开始的时间就要到了,我又花了些时间在引擎生产线和其他第一次改进计划涉及的生产线上面。很明显,管理层在这方面缺乏责任心,任由第一次改进之后的生产线自生自灭。引擎生产线的5S流程也慢慢地作废了。工作区再次变得杂乱无章,标签和指示也完全不起作用,操作员依然自由散漫。就算产品主管就站在旁边,也没有人遵守新的标准化操作流程。有的时候,主管会与操作员进行一二十分钟的谈话,而任由生产线在这个地方阻塞。作为一个精益制造工程师,我正在丧失耐心,并且不知道怎样才能扭转这种局面。同时,我还要尽量让新的小组继续积极地进行数据采集工作,为第二次改进计划做好准备。
第二次改进计划正式开始了。X公司把所有人集中在一个培训教室与新的咨询师见面。我的小组已经准备好了,组员们已经收集了大量关于1065生产线的信息。我们已经准备好了一散会就立即开始行动。这个新的咨询师做了一个演讲,但听起来和第一次咨询师所讲的内容如出一辙,依然是关于浪费、改变和改进计划的陈词滥调。X公司的生产经理正式启动了计划,我们就开始行动了。
其他小组带着剪切板和秒表出发,而我们则是带着执行计划和工具。在这一周时间里,我们还产生了无数的想法和解决方案。我们非常兴奋——我们已经得到了需要的数据,走在别人的前面了。
我们小组在绘制新的生产线设计图以及进行评审和向操作员与产品主管调查时,经常就地开会。让生产线上的人也参与到我们的设计中,对我们最后取得成功至关重要,因为这让整个生产线从头就开始接受我们的思想。
随着改进计划的推进,我们小组非常确信这个流程会取得成功——也许这不是从设计的角度来看,而是从企业文化改变的角度感到自信。我们团队慢慢地拼装这个生产线。我们将工作区的数量从10个减少到了7个,减少了其间走动带来的浪费,平衡了工作内容,并实现了单品流程。我们还提前考虑了5S,把一切问题都搞清楚透彻。
这是一个令人满意和兴奋的转变。作为一个精益制造工程师,我希望整个生产流程和所有的小组都取得成功。我们最开始指望引擎生产线成为标准和示范生产线,但是管理层和产品主管让这个生产线重新回到了以前糟糕的状态。现在1065生产线又给了我们另一个成功的机会。
团队成员在一起工作得很好。他们能产生很多有创意的想法来修建工作区,用来陈列工具和原材料。我的经理对我的工作进展表示非常满意。我直接告诉她:“这就是提前计划能够为你带来的好处。”
X公司的第二次改进计划接近尾声了,1065生产线看起来非常出色。当然,实际的测试效果还要等到下个星期一投入正式使用时才知道。在改进计划的最后一天,我让我的队员向公司展示成果。我们已经为1065生产线做了很大的改变,同时我们还取得了操作员和产品主管的极大信任,他们将把我们的设计思想坚决地付诸实践。他们对于如何处理新的流程都已经成竹在胸,我也相信我的团队成员在返回他们各自的工作岗位之后,还能继续为生产线提供帮助。