最近,重庆长安铃木汽车有限公司的IT部门特别忙,业务部门期望获知来自终端市场更多的信息,同时也提出降低内部成本的需求。作为长安铃木信息系统总监的丁江马不停蹄,不断与各个业务部门进行密切的沟通。 在丁江的回忆里,2001年进入这家日资企业后,精益化生产便是这家公司永恒的主题,他的工作也紧紧围绕这个主线展开。 残酷的低成本后端 低成本,在长安铃木内部,近乎残酷。对于这样一家日资背景的企业来说,首先想到的是日企一贯的压低库存。
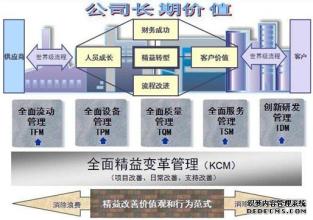
不过,可以改善的空间已经被压缩得很小。公司在生产组织上,长安铃木引进日本铃木公司的科学管理模式,推行国际通行的“精益生产”方式,实行“准时制”生产和“零库存”管理。 通过几年来的优化,长安铃木对供应商发布的供货计划已经可以做到三个周期的排货计划:第一层,长期预测计划,即3个月的长期预测。第二层,中期计划,即N+5天的整车排序计划。计划中包含这N+5天之内要生产的品种、颜色和每天生产数量,是供应商在这N+5天内的交货计划。第三层,现场拉动计划,依据生产现场的数据采集信息。将物料拉动信息发布给最近的供应商或者附近的第三方仓储公司,要求前者按照顺序给工厂供货。 对于第三层的时间,主要依靠JIT(Just in time)的“准时制”拉动,为了进一步降低库存成本,长安铃木对这一系统不断优化,以期对库存的管理再次优化。在长安铃木,有两类零部件被列入优化计划,一类是那些当天生产现场的一些变化,颜色零件、保险杠、门把手等与车的外观颜色和车型紧密结合的零部件,另一类是占地体积较大的零部件。 这部分零部件从原先一到两天发布一次的生产计划的时间再次被精简。最终做到两个小时左右发布一次计划,现场的库存时间控制在2小时左右。据丁江的粗略估计,将一天的库存成本下降到2、3个小时,库存成本约为原来的1/4。 不过,这还不算。后端供应链的成本压缩还继续推演到物流这一环节,这是一个名为“供应链优化”的计划。长安铃木下达送货指令后,各种零部件供应商分别送货或集中到第三方仓储公司由其送货,不过,有的车并没有满载。在长安铃木看来,零部件厂的物流成本最终将转化在其零部件的价格上,为了提高对零部件的议价力。他们督促第三方仓储公司改变管理方式,采取长安铃木提出的“循环集货”的方式管理物流。 与此同时,这项计划还将把仓储公司、零部件供应商的库存信息涵盖在内。JIT帮助长安铃木做到了信息的推送,但是生产物流人员还期望获得仓储公司的库存、零部件供应商的库存、以及零部件供应商的在途零部件的数量等信息。这样生产物流人员在对生产计划的安排以及调整上便能做到合理的调配。 通过IT系统的延伸,将信息收集的链条延展到这些环节,后端的供应链成本进一步得到了压缩。 精益化管住前端 除了在后端的精益化管理,这一改变还延伸到了前端。对于前端管理的环节在这一时期显得越发重要。对于长安铃木来说,一味地拼价格的时代已经过去,而营销的手段也很有限。当下,公司内部开始将注意力转向终端的管理、用户忠诚度的管理上。 早在2004年,和很多当时的整车厂一样,长安铃木也开始关注终端的管理。那时候,IT部门通过上线了一套整车销售系统,来了解整车的社会库存及终端销售情况。 2009年初,为了规范4S、2S经销商、服务站的售后服务及售后备件管理,长安铃木开始推行客户服务系统。通过规范、高效的服务管理提升用户的满意度。