烧结,是把粉状物料转变为致密体,是一个传统的工艺过程。人们很早就利用这个工艺来生产陶瓷、粉末冶金、耐火材料、超高温材料等。一般来说,粉体经过成型后,通过烧结得到的致密体是一种多晶材料,其显微结构由晶体、玻璃体和气孔组成。烧结过程直接影响显微结构中的晶粒尺寸、气孔尺寸及晶界形状和分布。无机材料的性能不仅与材料组成(化学组成与矿物组成)有关,还与材料的显微结构有密切的关系。
烧结_烧结 -烧结
定义
宏观定义:在高温下(不高于熔点),陶瓷生坯固体颗粒的相互键联,晶粒长大,空隙(气孔)和晶界渐趋减少,通过物质的传递,其总体积收缩,密度增加,最后成为具有某种显微结构的致密多晶烧结体,这种现象称为烧结。
微观定义:固态中分子(或原子)间存在互相吸引,通过加热使质点获得足够的能量进行迁移,使粉末体产生颗粒黏结,产生强度并导致致密化和再结晶的过程称为烧结。
正文
不能直接加入高炉的铁(精)矿粉造块的主要方法之一。通过烧结,还可以改善原料的冶金性能。烧结也应用于有色金属冶炼过程。有色金属硫化物精矿的烧结,除造块外,还有脱硫的作用。烧结技术从1911年开始采用,当时主要目的是利用钢铁厂的废弃物。随着选矿和高炉炼铁对精料要求的提高,50年代以来烧结生产发展迅速。
烧结是将贫铁矿经过选矿得到的铁精矿,富铁矿在破碎、筛分过程中得到的粉矿和生产中回收的含铁粉料、熔剂以及燃料等,按要求比例配合,加水制成颗粒状的烧结混合料,平铺在烧结机上,经点火抽风烧结成块。生产烧结矿,以前用过烧结盘、回转窑和悬浮烧结等方法,现在都用带式烧结机。后者单机产量高,产品质量好(图1)。
烧结
国外烧结使用富矿粉为主,而中国以精矿粉为主。中国在细精矿烧结工艺方面有一些自己的可贵经验。
烧结反应过程 是分层依次向下进行的(图2)。抽入的空气通过已烧结好的热烧结矿层预热,在燃烧层中使固体碳燃烧,放出热量,获得高温(1300~1600℃)。根据温度和反应气氛条件,可以进行下列反应:
①分解反应
(1300~1350℃以上)
②还原反应
③氧化和去硫反应
烧结
料层在加热过程中,熔点较低部分首先出现液相,将周围物料浸润和熔融,相邻液滴产生聚合,引起收缩和形成气孔,并在冷却过程中固结和产生结晶,成为具有一定强度的多孔烧结块。烧结过程中基本的液相是硅酸盐和铁酸盐体系。从燃烧层下抽出的高温废气,经预热、干燥层,将热量传给烧结料,使燃料着火,将料中的游离水和化合水蒸发和分解。废气继续下行,温度继续降低,其中水分又重新凝结,使物料过湿。如将烧结料预热到一定温度,可以消除过湿现象。
烧结矿的品种,已由单一的酸性烧结矿发展成为适应不同条件的自熔性烧结矿、高碱度烧结矿和含MgO烧结矿。烧结矿的质量检测项目有:粒度组成、含粉率、冷态转鼓强度、还原性(900~1200℃)、气孔率、落下强度、低温还原粉化率、软化温度、熔化温度和收缩率等。
烧结工艺流程 烧结前原料应当精心处理。铁精矿粉和富铁矿粉应在原料场采用专门的堆料、取料设备进行混匀处理,以保证烧结料的化学成分稳定。石灰石应破碎到粒度2~3毫米以下,以保证烧结矿的强度。用生石灰代替部分石灰石可以强化烧结过程。烧结用的固体燃料(焦粉或无烟煤),应破碎到粒度3毫米以下,但粒度 0.5毫米以下的细粉不能太多。精确配料是保证烧结矿质量的重要环节;现在多用重量配料法。自动配料设备由圆盘(或皮带)给料机和称量装置组成。配好的烧结料通常在圆筒混合机内混合、加水润湿并形成颗粒,以获得成分均匀和透气性良好的烧结混合料。一般分两次混合:第一次是混合和加水润湿;第二次是造球和补充加水。烧结机加料前要先铺底。底料一般为粒度 8~25毫米的烧结矿,厚度在30毫米左右。这样可保证烧透,防止烧坏炉篦。混合料一般用梭式布料器加到烧结机上的矿槽中,然后用圆筒布料器和辊式布料器把料均匀地布在台车上。
烧结
烧结机是由铺设在钢结构上的封闭轨道和在轨道上连续运动的一系列烧结台车组成。近年,烧结机向大型化发展。1911年第一台烧结机面积为8.3米 ,70年代的烧结机面积已达600米 (宽5米、长120米)。现代烧结机生产能力为1.5~2.0吨/(米 ・时)。
烧结料点火一般用气体燃料或液体燃料,点火温度为 1200~1300℃。适当增长点火器和增设低温(600~900℃)保温段,可以提高烧结矿强度、节省固体燃料和降低FeO含量。在改善烧结料透气性的基础上,逐步增加料层厚度,可以降低燃料消耗和改善质量。目前最厚料层达500~600毫米。近代烧结机能耗(包括点火、混合料中固体燃料和车间电耗)为每吨烧结矿(0.45~0.60)×10 千卡。
新建和改建的烧结厂多采用烧结矿冷却工艺,以筒化运输,便于“整粒”。并可使高炉上料设备不易损坏,炉顶密封性好,有利于高压操作。
环境保护措施 烧结厂的粉尘和废气污染环境。应采用水封拉链清灰,用高效的静电除尘代替多管除尘,用密闭运输和采取其他措施减少烧结废气中的硫氧化物、氮氧化物和一氧化碳等有害气体,以保护环境。
制取过程
烧结
在利用固相反应制备无机固体化合物时,反应的速率由扩散过程控制,常常需要较高的温度才能使反应有效地进行。另外一些固体化合物是固液相组成的化合物,在熔化时会发生分解反应,故烧结一般应在产物熔点以下进行,以保证得到均匀的物相。但是烧结温度也不能太低,否则会使固相反应的速率太低。在很多情况下,烧结需要在特定的气氛或真空中进行。控制烧结过程的气相分压非常重要,特别是当研究的体系中含有价态可变的离子时,固相反应的气相分压将直接影响到产物的组成和结构。例如,在铜系氧化物高温超导体的合成中,烧结过程必须在严格控制氧分压,以保证得到具有确定结构、组成和铜价态分布的超导材料。
加工步骤
一个重要的步骤。聚四氟乙烯预成型品必须通过烧结才能成为有用的制品。烧结是将预成型品加热至熔点(327℃)以上,并在此温度下保持一定时间,使聚合物分子由结晶形逐渐转变为无定型,使分散的树脂颗粒通过相互熔融扩散黏结成一个连续的整体。烧结全的预成型品由透明胶状体冷却成坚固的乳白色的不透明制品。
工序
高炉炼铁生产前,将各种粉状含铁原料,配入适量的燃料和熔剂,加入适量的水,经混合和造球后在烧结设备上使物料发生一系列物理化学变化,烧结成块的过程。在生产上广泛采用带式抽风烧结机生产烧结矿。主要包括烧结料的准备,配料与混合,烧结和产品处理等工序。
烧结_烧结 -测定方法
将试条放入烘箱内,在105~110℃下烘干至恒重。在干燥器内冷却至室温后备用。在天平上称取干燥后的试样重。称取饱吸煤油后在煤油中试样重。饱吸煤油后在空气中的试样重。将称好重量的试样放入105~110℃烘箱内排除煤油,直至将试样中的煤油排完为止。按编号顺序将试样装入高温炉中,装炉时炉底和试样之间撒一层薄薄的煅烧石英粉或Al2O3粉。装好后开始加热,并按升温曲线升温,按预定的取样温度取样。
在每个取样温度点保温15min,然后从电炉内取出试样迅速地埋在预先加热的石英粉或Al2O3粉中,以保证试样在冷却过程中不炸裂。冷至接近室温后,将试样编号,取样温度记录于表中,检查试样有无开裂、粘砂等缺陷。然后放入105~110℃烘箱中烘至恒重。取出试样放入干燥器内,冷却至室温。将试样分成两批,900℃以下为第一批,测定其饱吸煤油后在煤油后在空气中重,900℃以上的试样为第二批,测定其饱吸水后在水中重及饱吸水后在空气重。按公式算出各温度点的结果后,以温度为横坐标,气孔率和收缩率为纵坐标,画出收缩率和气孔率曲线,并从曲线上确定烧结温度和烧结温度范围。
烧结_烧结 -应用
烧结
自上世纪70年代以来,我国铁矿粉造块工业取得了很大的成就。1970以前,我国烧结机的机型都在75m2以下。70年代以后,特别是1985年宝钢从日本引进的450m2大型烧结机投产以及依靠和组织国内的烧结厂设计、生产制造了130m2烧结机、抽风环式冷却机和相应的20多种配套设备,使我国烧结机的大型化上了一个台阶。在此期间,进行了烧结矿冷却(振动式冷却和盘式冷却)及加设铺底料的攻关,同时在全国烧结厂推广生产高碱度烧结矿和厚料层烧结技术。1958年“大炼钢铁”时期,在铁矿山比较集中的龙岩地区,开始发展鼓风土烧结,俗称“平地吹”。1968年3月,三钢第一台18平方米烧结机动工兴建。1970年4月,建成投产。现代烧结生产是将铁矿粉、熔剂、燃料、代用品及返矿按一定比例组成混合料,配以适当的水,经混合及造球后,在抽风烧结机的台车上自上而下进行烧结。整个烧结料层(600mm~700mm)可分为:烧结矿层、燃烧层、预热层和冷却层。从1989年至2007年,我国烧结行业迅速发展,大量新工艺、新技术、新设备陆续推出。我国己跨入世界烧结行业的先进行列。其发展情况和相关成就如下
(1)自1978年马钢冷烧技术攻关成功后,“六五”、“七五”期间一批重点企业和地方骨干企业基本完成热烧改冷烧工艺。相当部分企业建成并使用原料中和混匀料场,绝大部分厂家实现了自动化配料、混合机强化制粒、偏析布料、冷却筛分、整粒技术及铺底料技术等。
(2)“七五”、“八五”以来,在传统烧结工艺基础上发展了一批新工艺和新技术,并在国内各大钢铁企业推广应用,如高碱度烧结技术、球团烧结技术、小球团烧结技术、低温烧结技术、低硅烧结技术等。
(3)设备大型化和自动化。20世纪70年代初以前,我国最大烧结机为75m2,80年代初,我国在宝钢引进了450m2的大型烧结机及其配套设备,同时引进了烧结机的制造技术。至2007年,我国已先后在宝钢、鞍钢、武钢等地建成了180m2的烧结机及其配套设施72台套。烧结面积总计达到221216m2,烧结机单台平均面积为295m2。我国自1989年以后投产的大中型烧结机的工艺技术装备和自动化水平得到提高,实现了较为完善的过程检测和控制,并采用计算机控制系统对生产过程自动进行操作、监视、控制及生产管理。
(4)烧结生产指标及产品质量的提高。我国烧结矿质量明显提高,烧结工序能耗大幅度降低,1986年至2007年期间,我国烧结行业得到了更进一步的发展,主要体现在:设计和制造了大型烧结机成套设备;大中型企业建成了综合原料场,使烧结原料中的化学成分稳定;大量新工艺、新技术、新设备得到开发(直拖式自动重量配料设备、各种烧结增效节能添加剂、燃料分加、小球烧结、各种形式预热烧结混合料、新型节能点火保温炉、高铁低硅烧结、超厚料层烧结等)。我国烧结矿质量有了大幅度的提高,国内如宝钢、武钢四烧、济钢等发展较先进的企业已将烧结矿FeO含量控制在7%左右。不少烧结厂烧结矿FeO含量为8%~10%、TFe达到57%~60%、SiO2含量降到4.5%~5%,实现了低硅烧结;ISO转鼓强度为79%~83%。
我国的钢铁企业还有较大的发展空间,但是国内和国际竞争激烈,同样烧结厂也面临市场经济调节。当前急待解决的问题是提高烧结矿的质量;烧结生产发展趋势是逐步实现烧结机的大型化;采用原料混匀技术,提高烧结的精料水平;提高自动化水平和生成率,努力降低烧结矿的成本;加强环保治理;加速增加球团矿用量,改善我国高炉的炉料结构;采用小球烧结工艺,进一步强化烧结生产;继续对老旧设备进行改造更新;坚持生产高碱度烧结矿;充分利用国内国外的铁矿资源;调整和改善烧结生产布局;实施可持续发展战略,建设清洁式工厂。
烧结_烧结 -排放
烧结出的地板
广义钢铁工业企业包括的烧结生产线,其主要原料为铁精粉和煤。由于煤中含硫,所以烧结会排放出有害气体产物二氧化硫,必须进行烟气脱硫处理。其他气体排放物主要为氮的氧化物和二氧化碳。
使用袋式除尘器或电除尘器,正常工作时能达标排放。除尘后排放物基本为小于PM2.5的粉尘。标准只是宏观经济和国民健康、环境的调和产物。达标不表示对人类和环境没有影响。
很少或不排放污水。
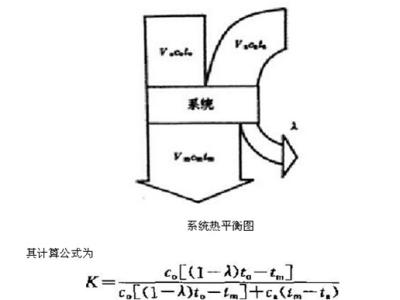
由于烧结温度很高,烧结矿不能热送高炉,即使回收部分馀热,还是要排出大量废热。