为确保追溯信息的完整性、数据采集的高效性、准确性以及数据采集的可行性,追溯数据采集将采用条码技术以及布局合理的采集点来完成追溯信息的采集。小编给大家整理了关于产品追溯流程,希望你们喜欢!
产品追溯流程1、目地
通过对产品进行标识和控制,确保要需要对产品质量形成过程时实施追。
2、范围
适用于来料、制成品、成品的标识追溯控制。
3、职责与权根
3.1QC部:负责产品标识使用的制定以及质量异常的追溯归口部门。
3.2生产部:实施对库房来料、成品的标识以及生产过种中半成品、成品的标识,并对标误解使用进行管理和监控。
3.3跟单部:依据客户反馈的内容,组织进行核查产品标识以及产品的相关记录,进行原因的追溯并向相关部门进行反馈。
3.4相关部门:发生不符合事项时,控照《产品的标识和可追溯性程序》进行,实施纠正、预防措施。
4、定义
标识:物质的标志和标签具有唯一性,以确保在需要追回或进行特别检验时能够识别出具体的产品的情况。
5、工作程序
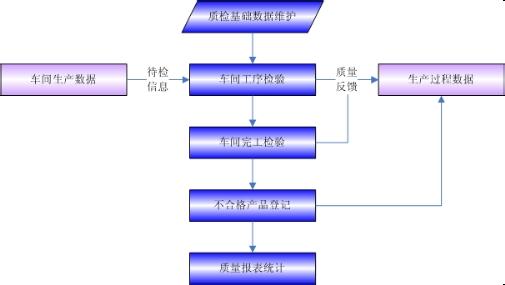
5.1来料的标识
来料入厂后由原材料检验员依据相应的程序进进行检验,根据检结果给出判定意见,按下列规定动作依次进行标识。
5.1.1来料检验合格的,填写相应的采购产品检验报告给仓库办理入库手续,按照回货的清单填写来料标签。
5.1.1.1对来料要求供应商提供详细的物料资金料,内容包括:内附产品的出厂检验报告、产品的批号、每个产品的编号;装箱需要注明内装物料的生产批号、产品的编号、生产日期。
5.1.1.2仓库根据检验报告填写来料标识单,对应张贴到相应的物料醒目的地方。
5.1.2来料检验不合格的,放置不合格区域等待进一步的处理意见。
5.1.3来料需要紧急特采使用,在料标识单标注“特采”字样。
5.1.4为了更有效的便于追溯,实行物料“先进先出”原则。
5.2物料标识的核对。
5.2.1生产车间开具领料单领取相应的物料,特料聘为时发一张相应的来料标识单,填写相应在的物料情况。
5.2.2过程检验员对上线的物料进行标识单内容核对,内容填写完整、清楚、准确,方可投入生产线使用。
5.3成品标识:成品检验员在进行出货前检验时,首先需要核对流程单上的内容是否填写完整、正确,再核对是否与合同订单要求的一致。
6、当产品发生不合格需要进行追溯,以生产流程单为线索进行追溯,追溯的路线是:出厂成品—出厂检验报告——来料标识单——物料检验报告。
7、本厂生产的产品的标识和可追溯性。
7.1批次管理:本天长让产品以每天生产为单位批次进行编号管理,批号的规定办法为:产品名称+月+日+序列号。
7.2设计相应的“流程单”贯穿整个生产过程,流程单需要标注的内容:产品型号、生产日期、产品批号、工序操作者、数量、检验装态、流程单后附相应的“来料标识单”。
7.3产品转入下一道工序,相应的流程单随同产品一起移动。
追溯管理系统功能简介追溯采集方案
为确保追溯信息的完整性、数据采集的高效性、准确性以及数据采集的可行性,追溯数据采集将采用条码技术以及布局合理的采集点来完成追溯信息的采集。
条码规则
通过条码扫描可实现数据的快速、准确的采集,为了结合条码扫描采集,XX科技需要形成自己的产品条码规则以及关键物料的条码规则,形成的物料条码中包含追溯件的关键物料代号、供方代号、物料批次号等信息。
条码生成规则
通过配置条码生成规则,如前缀代号、起始序号、生成数量等,系统可实现快速、批量的生成所需的条码,并实现条码的导出与打印,以此可大大缩减条码管理的工作量,同时针对产品和物料可按不同规则生成条码。
采集点布局
确保追溯信息的完整性以及采集效率的高效性,系统实施过程中将设计完整的采集点布局以完成数据的采集,如下图所示。涉及XX科技采集点的布局将根据实际应用场景以及采集内容,调研时展开采集点评估,最后形成完整的采集点布局图。
追溯信息采集内容
结合客户需求,并确保质量追溯数据的贯通以及质量信息的完整性,系统将采集生产过程5M1E信息以及影响产品质量的关键信息,采集内容如下:
1:生产计划订单信息
2:供应商物料批次信息
3:进货检验报告制造过程5M1E(人、机、料、法、环、测)
4:制造过程检验信息
5:不合格品处理信息(含进货检验及制造过程)
生产计划订单信息采集
系统具备生产计划管理功能,包含了订单号、生产指令号等信息,系统支持计划的在线制定、审核与发布,并可导出至EXCEL。系统可通过集成现有订单管理系统,采用定时自动或手动刷新导入生产订单及批次信息,为质量追溯贯通客户订单、生产批次以及产品编号的衔接。 进货检验信息采集
在进货检验环节IQC需要按批次记录物料名称、物料批次、供应商名称、来料数、抽检数、抽检检验数据信息、检验的合格状态等信息,当检验发现物料不良时需要明确记录物料的不良项以及批次不良的处理结果,包括挑件、退回供方或降级使用等,当在制造过程或售后发现物料不良后可通过物料批次号快速追溯到进货检验报告、不合格处理结论以及库存量等。
制造过程信息(5M1E)采集
追溯过程中为了还原生产环境,挖掘产生产品质量异常的原因,需要在生产过程中采集制造过程的5M1E信息,包括人、机、料、法、环、测等,系统在采集过程中将按采集点布局进行采集,采集内容及方式如下:
物料信息:
在关键工序设置采集点,采集该工序产品所装配的关键物料的批次号、物料代号、供应商代号等信息。为了快速、准确的记录物料批次信息,系统将采用条码扫描技术来完成物料批次信息的记录,操作员扫描产品条码后,系统自动导入产品编号、订单号、产品型号等信息,同时扫描物料条码后,系统将自动记录物料代号、物料批次号、物料供应商代号信息与产品编号关联。系统将通过条码扫描技术快速、准确的完成供应商物料批次信息的采集。
人员信息:
系统设置工序与人员绑定,扫描产品条码后系统自动保存当前工序人员与时间信息;
方法:
记录关键工序的加工工艺、工装选择、操作规程以及相关工艺参数等;
环境:
记录当时工作地的温度、湿度、照明和清洁条件等;
使用仪器设备
制造过程检验信息采集
制造过程检验信息为反应产品质量的关键信息,系统将在关键工序配置采集点采集检验信息,但采集过程中往往录入的工作量较大,考虑到实际应用场景,系统将采用条码扫描以及实现仪器接口等方式完成检验信息的采集。
采集信息包含:
半成品测试
老化测试
成品测试
出货检验
不合格品处理
采集方式有:
1:检验信息
扫描产品号条码后,系统自动导入产品型号、订单号、批次号等信息,检验人员只需要填写数量,工序与不良设定关联,检验员只需要录入对应不良数量即可。
2:产品关键检测数据
可以对检测设备展开集成,通过RS232、485通讯接口自动导入检测数据,并关联产品号进行匹配保存。
不合格品处理信息采集:
当检验员发现不合格品时,检验人员可以在线填写不合格处理单,并由相应权限人员填写不合格品处理结论,通过在线完成不合格品的审理记录。