土霉素为淡黄色片或糖衣片,属于四环素类,可用于治疗立克次体病,包括流行性斑疹伤寒、地方性斑疹伤寒、落基山热、恙虫病和Q热,支原体属感染和衣原体属感染等疾病。以下是小编为您整理的土霉素生产流程,希望对您有帮助。
土霉素生产工艺
2.1 土霉素的生产工艺流程概述
土霉素生产工艺主要分为:发酵、酸化过滤、脱色结晶、离心干燥四个阶段。其生产工艺流程,如图2.1:
2.2 发酵工艺流程
2.2.1 斜面孢子制备
首先培养三支斜面孢子, 斜面孢子的培养基是由麸皮和琼脂组成,用水配制。培养孢子条件:斜面孢子在36.5~36.8℃培养,不得高于37℃。若36℃超过2小时则生产能力明显下降,不可用于生产。而且在袍子培养过程中还需保持一定相对湿度,湿度55%~60%。培养时间96个小时。将三支斜面孢子加入无菌水之后制成悬浮液。将悬浮液放置于4℃~6℃的冰箱中备用。
2.2.2 一级种子罐发酵
一级种子罐采用实罐蒸汽灭菌法灭菌。培养温度为31℃,采用夹套式换热(自动温度调节),罐内生长弱,无动力设备,设备密封。发酵约28h,培养液可趋于浓厚,并转黄色,种子培养液pH值为6.0~6.4时,移入二级种子罐。
2.2.3 二级种子罐发酵
二级种子罐采用实罐蒸汽灭菌法灭菌。培养温度为31℃,采用夹套式换热(自动温度调节),有搅拌动力设备。二级罐发酵约28h,培养液外观深粽、稠、有气泡,pH大于6.0移入三级发酵罐。 2.2.4 三级发酵罐发酵
三级发酵罐采用实罐蒸汽灭菌法灭菌,接种量为15~20%,发酵全程温度控制在30~31℃,分段培养。采用列管式换热(自动温度调节),有搅拌动力设备。发酵过程,菌体大量生长,培养基快速消耗,需要对其进行补料控制。发酵导致pH降低,需补氨水调节pH。产生的大量泡沫,需加消沫剂进行消沫。发酵过程消耗氧气,需通氧补充,通气量为:0.8~1.0v/m。发酵过程通氨、补糖的工艺具体控制的方法不甚相同。接种后发酵pH低于6.4时,开始通氨,通氨量的多少参考pH。要求100h前pH在6.3~6.5,100h后pH6.2~6.3,放罐前8小时停止通氨。根据发酵液的残糖值补入总糖(即淀粉酵解液),一般在100h前残糖控制4.0~5.0%,100h至150h控制3.5~4.0%,150h至放罐前6h控制3.0%。在菌丝接近自溶期前放罐。
2.3 酸化过滤工艺流程
2.3.1 酸化
土霉素能和钙、镁等金属离子,某些季胺益、碱等形成复合物沉淀(即不溶性络合物)。在发酵过程中,这些复合物积聚在菌丝中,在液体中的浓度不高。发酵结束后,土霉素大部分沉积在菌丝中,发酵液中很少。因此,应对土霉素发酵液进行酸化等处理,使菌丝中的单位释放出来,以保证产品收率和质量。
2.3.1.1酸化剂的选择
酸化剂一般可采用盐酸、硫酸、草酸、磷酸等,但根据土霉素滤液质量的要求,若滤液中有钙离子存在,则对直接沉淀是否完全有一定的影响,通过生产实践认为采用草酸作酸化剂较好。因为草酸去钙较完全,析出的草酸钙还能促进蛋白质的凝结,提高滤液质量。草酸属于弱酸,比盐酸、硫酸等对设备腐蚀性较小,但其价格较贵,并可促使差向土霉素等异构物的产生。在采用草酸作酸化剂时,必须降低温度,要求15℃以下,尽量缩短操作时间,避免或减少差向异构化。在有条件的情况下,应进行草酸回收工作。鉴于以上因素,酸化剂采用草酸和盐酸。
2.3.1.2酸化pH的控制
加草酸酸化调pH的目的是为释放菌丝中的单位,同时还得考虑土霉素的稳定性、成品质量及提炼成本,故对酸化pH要严格控制。目前工艺上控制在1.6~1.9范围内,若pH过高,则对释放单位不利,而且会促进差向土霉素的产生;若pH过低,则土霉素的稳定性差,影响成品质量,且草酸用量加大,将增加单耗和成本。
2.3.1.3发酵液的纯化
发酵液中同时存在着许多有机和无机的杂质,为了进一步提高滤液质量,为直接沉淀法创造有利条件,必须在发酵液的预处理过程中添加纯化剂。目前生产上是利用黄血盐和硫酸锌的协同作用来去除蛋白质,同时去除铁离子,并加入硼砂,以提高滤液质量。在不影响滤液质量的前提下,纯化剂的加入量应尽量减少,以降低成本。 2.3.2 过滤
过滤工艺采用板框过滤机过滤。滤布可以去除一些杂质。正批液经过板框过滤机后直接进入正批液储罐。为了提高过滤机中土霉素的利用率,采用三级过滤和顶洗的方法。顶洗的要求是高于4000单位的滤液才能够进入过滤机后进入正批液的储罐。低于的进入其它储罐以备下一次顶洗之用。
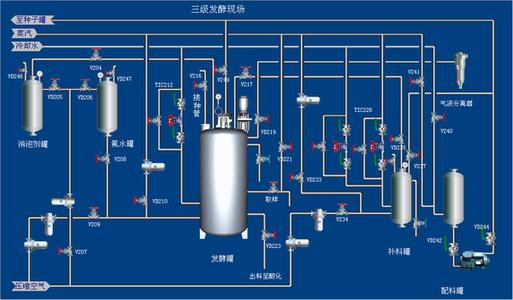
2.4 脱色结晶工艺流程
2.4.1 脱色
为了进一步去除滤液中的色素和有机杂质,以提高滤液质量,将滤液通入脱色罐,由其中的122-2树脂进行脱色。该树脂在酸性滤液中氢离子不活泼,不能发生电离及离子交换作用,但能生成氢键。其生成的氢键可吸附溶液中带正电的铁离子、色素及其它有机杂质,从而提高土霉素滤液的色泽和质量。树脂在氢氧化钠溶液中,由氢型变成钠型,失去氢键的活性,使其吸附的色素和杂质解离出来,再经酸作用可恢复其氢键的活性,重复使用
2.4.2 结晶
土霉素发酵液经过上述预处理后,即可在酸性脱色液中用碱化剂调节pH至等电点,使土霉素直接从滤液中沉淀结晶出来。
2.4.2.1碱化剂的选择
碱化剂一般可采用氢氧化钠、氢氧化铵、及碳酸钠、亚硫酸钠等,各有其特点。例如,氢氧化钠价格便宜、用量少,但由于碱性较强,根据土霉素的稳定性,单独使用会造成局部过碱而破坏土霉素,影响产量和产品质量;又如亚硫酸钠具有抗氧化和脱色作用,可使产品色泽鲜艳,但其碱性极弱,调pH时反应缓慢,用量大,且价格较贵,影响成本;而氨水其碱性较氢氧化钠弱但比亚硫酸钠又强,价格便宜,用量适中等。故目前生产上多采用氨水(内含2~3%NaHSO3,Na2CO3及尿素等)作为碱化剂,这样既能节约成本,又能起到抗氧脱色作用,效果较好。因为亚硫酸钠是弱酸强碱盐,能起部分碱化作用.但它主要是还原剂,在酸性溶液中能防止土霉素遇氧化物被破坏,起稳定剂的作用,同时还起脱色作用。
2.4.2.2 pH的控制与产量和质量关系
在连续结晶过程中,pH的高低对产品质量有一定影响。土霉素的等电点为pH4.6~4.8,在pH4.5~7.5之间,游离碱在水中的溶解度几乎不变。若pH控制在接近等电点时,虽然沉淀结晶较完全,收率也高,但会有大量杂质(主要是接近等电点pH的蛋白质)同时沉淀析出,影响产品的色泽和质量;若pH控制得较低一些,对提高产品质量虽有好处(即上述蛋白质等杂质不同时析出,而残留在母液中),但沉淀结晶不完全,收率要低些,影响产量。因此,在选择沉淀结晶pH值时,就必须同时考虑到产、质量的效果。在正常情况下,工艺上控制pH值在4.7左右。若沉淀结品质量发现较差时,pH值可控制得稍低些,有利于改善结晶质量,但不能低于4.5,否则收率低,影响产量。
2.4.2.3 影响晶体大小的其它条件
要使土霉素高产优质以及所得晶体均匀,好分离,便于过滤和洗涤等操作,除了严格控制pH条件外,对滤液质量、加碱化剂的速度,结晶的温度,搅拌转速和结晶时间等条件都须加以考察,选择最佳条件。
2.4.2.4 连续结晶法
连续结晶的原理是根据土霉素的结晶速度,结晶基本完成一般需要2h,2.5h后母液中土霉素含量下降幅度基本稳定。故可以结晶最大流量为基准,安排一套连续进行2.5h的结晶设备,使调好pH的结晶液在流动情况下有一段晶体成长的足够时间,即可达到结晶完全的目的。
2.5 离心干燥工艺流程
2.5.1 离心
利用多个三足式离心机联合的方式离心。
2.5.2 干燥
2.5.2.1离心工艺出来的湿成品仍含有较多水分,未达到成品要求,因此要经过摇摆机过40目的筛网,制成颗粒后进入三级旋风干燥器中,干燥后得到成品。
2.5.2.2湿成品干燥记录:干燥时间8h;风压0.04MP;投料温度185℃;卸料温度80℃ 。
3、土霉素生产的废水处理
3.1 废水处理原因
联邦制药(内蒙古)厂地位于国家重点保护流域——黄河流域的敏感地区。其生产废水浓度高、色度高,且水质不稳定,为使出水能够达标排放。该工程的废水处理系统是用来处理土霉素生产废水。土霉素生产过程中产生大量的高浓度有机废水(结晶母液),水中有机物来自发酵的残存培养基和发酵代谢产物有碳水化合物、脂肪、蛋白质、纤维素、有机酸、色素、酶、放线酮、残余土霉素碱及其他代谢产物。其中残余土霉素碱、草酸等物质抑菌性较强,干扰蛋白质的合成从而抑制细菌生长,废水需作适当的预处理在降低杀菌性后再进入生化处理系统.
3.2该生产废水处理方案
废水的治理难点在于:制药废水对废水处理过程中的生物菌种有很强的杀伤力,含有部分不可生化和对微生物有抑制作用的有机物,进水有机浓度、色度高,水质不稳定;同时受现场占地面积小的限制,导致改造难度增大。通过分析,确定了工程处理方案,决定采用“高压脉冲电凝系统物化处理一合絮凝技术(气浮)一组合兼氧一A/ 一加药沉淀一生物活性炭滤池”为主要处理单元的组合工艺路线。
3.2.1 高压脉冲电凝水处理技术进行预处理
高压脉冲电凝法(HVES)采用设计独特的高电压、小电流的电解技术,利用电化学原理,借助外加高电压作用产生电化学反应,把电能转化为化学能,经单电凝设备即可对制药废水中的有机或无机物进行氧化还原反应,进而凝聚浮除,将污染物从水体中分离,可有效去除废水中的SS、油、磷酸盐等各种有害污染物。采用高压脉冲电凝技术具有的特点是:①酸性条件下的有机废水可直接电解,出水pH接近中性,可大幅度降低加碱量,进而减少污泥量,降低运行费用;②集电解与气浮作用于一体,不需另外加药;③与传统的低电压、大电流的电解模式不同,极板消耗较少,更换方便,池内设搅动设施预防堵塞;④运行稳定,治理效果好,占地少,沉渣量少;⑤电凝设备的运行费用略高于生物法但比化学法低得多,且污泥量远低于化学法。但电凝设备的一次性投资稍大。
3.2.2 复合絮凝(气浮)技术降低抗生素残余效价
该废水中含有土霉素,具有一定毒性,抗生素残余效价会影响生物生化,在本工程中,采用复合混凝技术去除抗生素残余效价,即采用硫酸铝、聚硫酸亚铁、PAM及石灰对土霉素废水进行絮凝气浮预处理。其作用机理是絮凝剂中的Ca抖、AI计、Fe。+及其氢氧化物和有机聚合物PAM等,与抗生素分子的活性基团,如一NH。、一OH等,形成难溶复合体理后,会使废水中的微生物种类和数量增多,生长正常,废水性质趋于普通有机废水。同时,通过混凝气浮除渣后,为后续好氧生物降解减轻有机负荷。在本工程中,采用一体式自吸高效气浮系统实现固一液分离。该系统主要由一体式自吸高效溶气机、箱体、刮渣机、电控无堵塞释放器和排渣系统组成,它利用高效紊流容器装置,产生强烈负压,同时将空气和水吸人主机的溶混室内,在压力的作用下,形成优质溶气水,并由无堵塞释放器将溶气水直接释放到接触室内,再将絮凝后的污水引人分离室,在分离室内使溶气水与污水混合吸附,并把悬浮物浮至水面,固液分离后,由刮渣机把悬浮物刮人排渣槽,处理净化后的水经集水管排出。
3.2.3 组合兼氧技术进行水解酸化
采用推流式兼氧接触池,把反应控制在水解酸化阶段。内部悬挂组合填料,可根据水质水量情况,调整DO及回流值。兼氧阶段有中温菌和低温菌进行协调作用,故受外界气温和水温的影响小,且兼氧菌不同于专性厌氧菌种甲烷菌它是一种兼性菌种,在自然界中存在的量较多,容易培养,一旦废水中有机物发生变化,处理装置也能很快适应。这完全不同于厌氧处理中的甲烷菌,对于甲烷菌而言,由于它是单一性菌种,只要底物发生变化,甲烷菌就要衰亡。对于企业而言,其产品有可能不断更新转换,废水中的有机物成分亦会相应发生变化。兼氧菌种的易殖性及其强适应性,使兼氧工艺较厌氧工艺更能适应企业产品结。
3.2.4生物活性炭滤池进行深度处理
本工程出水要求达到GB8978一l996一级标给水排水准,若完全使用生化处理至达标,则投资成本很高,且占地面积很大。考虑到经济性和土地限制,采用生物活性炭滤池进行废水深度处理,利用活性炭的巨大比表面积,使微生物生长在活性炭表面去除生化工艺中未去除的微量污染物,确保CODcr%100 mg/L。
3.3 生产废水处理设备及参数
4 、讨论
根据对联邦制药土霉素生产工艺的分析,土霉素的生产工艺流程主要经过发酵、酸化过滤、脱色结晶、离心干燥四个阶段。其提取工艺为用草酸(或磷酸)做酸化剂调节pH值,是通用黄血盐-硫酸锌作净化剂协同去除蛋白质等高分子杂质,然后用122-2树脂脱色进一步净化土霉素滤液,最后调pH至4.8左右结晶得到土霉素碱产品。并了解了主要生产设备,并搜集了大量生产相关数据