美国金融危机暴露出美国一味强化的精英数字管理错了。中国企业界从美国那里移植过来的一整套数字管理体系也错了。错就错在只关注员工按规程做正确的事,却没有赋予一线员工独立思考和追求最佳的权利,以便挖掘、开发现场员工的创造力。
2008年,应华制国际教育集团和日本中产连MIC精益生产研究所的邀请,我随一个由20名企业家和高管组成的考察学习团,去日本名古屋岐阜丰田公司参观学习丰田生产方式。坐在飞机上,我还在想,中国民营企业家够虔诚的,在中国制造业寒冬即将来临的危机时刻,还能抽身到日本学习。
到了那里才知道,韩国企业界比我们更为重视学习丰田。与我们同时受训的还有另外5个班100名的韩国学习团队。在休息室我们看到,世界一流公司三星电子派往岐阜受训的人员已经超过20000名。受训对象已经从高管到了班组长和现场员工。为此,韩国总统卢武玄还给丰田岐阜MIC丰田方式研究所颁发了韩国国家贡献奖。韩国人明显比中国人刻苦。晚上在酒店的大堂里,每个人都展开教案和练习纸在认真做作业。而中国人则习惯于聚在一起,高谈阔论。
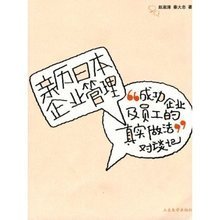
高谈阔论也是学习。与20位企业家和高管一起度过7天是非常有意义的。半天听日本老师讲课,半天参观。先后参观了8个工厂。课上课下,企业家们兴致勃勃,反复对照现场,分析自己企业的真问题。交流和碰撞,每天都延续到深夜。单是日本老师讲课和参观工厂,可能还有雾里看花不得其解。而我与20位带着企业真问题的企业家和高管之间的碰撞激荡,才使得许多看上去一般的东西,具有了独特的意义。
我日本之行的最大感受是,中国管理错了。以丰田为代表的一大批日本公司,实际上把握住了未来一流企业的本真。它们都注重领先时间,都注重育人,都注重现场解决问题。而中国企业界从美国管理那里移植过来的一大堆东西,可能需要重新反思。
没有资本,丰田公司不得不最大限度使用人工杠杆
1929年丰田喜一郎首次造访欧美大陆,他花费了四个月的时间,走访了英、美尤其是美国的汽车生产企业,弄清了欧美国家的汽车生产状况。他被马路上奔跑的汽车深深震撼了。在回程的船上,他伫立船头任凭海风洗面。那一刻,他意识到汽车会改变未来社会。他立志要造出日本人自己的汽车。丰田喜一郎的想法得到了纺织大王——父亲丰田佐吉的支持,成立了汽车研究所。丰田汽车部由丰田喜一郎1933年创立。1937年8月成立“丰田汽车工业株式会社”。从零开始跌跌撞撞。战后重新起步也异常艰难。1949年,公司已经到了山穷水尽的地步。订单缺乏,银行资金抽紧,公司经营危机,银行强行要求裁减3000人,否则就断贷。社长丰田喜一郎不得不裁减1600名员工。接着,他主动承担责任,辞去了社长职务,以谢顾全大局的员工。
接任社长丰田英二带着高管去美国考察12周。他们原本预期会对美国工厂制造流程与方法的进步感到惊叹,但事实不然。他们惊讶地发现,大规模生产方式自1930年到1950年,根本没有太大的改变。这个制度本身存在许多缺点:许多生产设备制造了大量库存,稍后才会被运送到另一个部门。接着需要更大的设备流程处理这些库存,然后又被运进了仓库堆放。过一阵子再送到下一个流程。大规模生产、各步骤中断,导致了大量材料变成等待输送的存货。设备不停的生产,员工不停的工作,最后就是制造出一大堆在制品存货。
丰田公司没有本钱负担这样的浪费。于是丰田英二授权大野耐一以美国为借鉴,彻底改造丰田生产线。大野耐一不辱使命,带领工程师、员工和经理人,开展了几十年的“亲自动手”之旅,发展成闻名世界的“丰田生产方式”。大野耐一可以说是丰田生产方式之父,但是他却把一切成功都归结为丰田两位元老的思想。丰田喜一郎当年提出了“只生产必要的东西”,丰田喜一郎的父亲丰田佐吉,由纺织机想到了“一有问题就停止生产”。丰田父子的想法,还带有农民的朴素直觉:没钱囤货,不生产次品。
就是这样两条普通的常识,在大野耐一的强力推行下,1970年代末演化成闻名世界的丰田生产方式TPS的两大支柱:“准时化生产”和“自动化”。TPS从1950年代开始摸索,到1980年代蜚声世界。
在创建这一系统时,大野耐一遇到了无法想象的抵抗。而他以自己独特的强势管理,和绝妙的造人之道,将所有抵抗一一化解,从而成功确立起了TPS。后来又经过丰田内外研究者的广泛提炼和推敲,有了一个简单的定义:
丰田生产方式TPS =准时化生产 +自动化 +造人
丰田生产方式改写了全球产业的历史,它带动几乎所有产业转型、实行丰田的制造与供应链管理理念与方法,促成了全球制造业与服务业的经营管理变革。
丰田生产方式离中国很远
日本距中国很近,丰田方式却离中国很远。
在欧美与日本公司因为资源价格上涨而日显疲态的境况下,丰田公司却因丰田生方式TPS逆势而上。中国企业与日本公司面临着同样严酷的环境。按理说,在困境中突围的丰田生产方式应该为中国企业所效法。每年到丰田公司参观考察的人车水马龙,可是迄今中国企业学丰田成功的案例很少。为什么?
有人说,丰田方式是专为日本人设计的。日本这个大和民族,在骨子里就有一种很强的团体观念,即使有很优秀的人并且做出了很优秀的成绩,他也不会独占好处,反而会心甘情愿的与他人分享。丰田方式可以说是日本人的人性、心智、理念的整体体现。丰田生产方式完美的让人心动,一旦转换文化背景,就难免水土不服。可是,丰田中国、丰田美国、丰田巴西、丰田印度等等全球丰田厂家,不同国家的人性与心智差异很大,丰田生产方式都能畅行无阻。其实,在后面的分析中我们会看到,并不是丰田生产方式难学,而是丰田生产方式的本真,并不会使所有的人都获益。丰田生产方式所侵害的正是那些企业掌权者的利益。
有人说,丰田生产方式过于微观,中国现在的机会很多,许多公司处在战略定胜负的阶段,“精益生产”还排不上队。而丰田汽车却因为全球实施丰田生产方式,抓住了一个又一个战略机会,使得在混合动力等一系列汽车先进技术和工艺上,持续领先,丰田系列产品更是琳琅满目。原来,一种在企业战略与关键现场没有断点的完美构造,使得丰田公司与众不同。
有人说,丰田生产方式只适用于品牌确立、订单不愁、销售渠道畅通的公司,因为它们可以静下心来练内功。而中国中小企业还存在吃饭难题,不全力搞销售怎么生存?实际上,丰田生产方式的起步是“没有钱,想制造汽车”的艰难阶段,“如果公司有钱,谁不知道引进一流生产线更为有效”!真正有了钱的公司,可能不会在运营现场“深耕”。产品战略和制造、销售、技术现场没有断点的丰田生产方式,正是强化营销力度的工具。
有人说,丰田生产方式,要求的流水线作业要求太高,一般公司达不到那样的标准。而丰田汽车实施看板目视管理,一目了然,诺大的车间没有一台电脑,只要能板着手指头数到1-10的人,就可以导入TPS。因为看板管理让一切都简单直接。同行的一位企业家感叹,这些年他不会英语却一个人跑遍了世界,就是因为目视标志一清二楚。
有人说,丰田生产方式对员工动作的研究非常精细,以至于在考虑如何节省0.1秒这样的事情,员工紧张不得闲。而在生产线上,员工在一个马蹄形的空间,有节奏的在几个加工动作中串换,像是在打太极,没有紧张这回事。相反,TPS所着意的正是员工可以有空闲将运作搞得更有效。现在的做法是最坏的,一直是员工不断寻求改善的激励器。
2000年6月,丰田和夏利折半出资成立“天津丰田”,日本丰田专家来考察后得出的结论是,丰田生产方式在中国的可移植性很小。因为当时销售信息和生产信息没有对接;与少量、高频率进货正好相反,多量、低频率进货和大量的中间库存非常普遍;比较严重的封闭“系统交易”和“杀价购买”,再加上“延期支付”横行,使得TPS落地前途渺茫。2002年,天津丰田和长春一汽合资重组,成立“天津一汽丰田”,运营由丰田主导,导入TPS成为可能。当时采取的关键措施有两条,一是从零开始,招聘新员工所占比例为95%,一张白纸可以画最新最美的图画;二是从日本派出了豪华专家团:从初期的50名,到顶峰时的260名,一对一进行集中灌输。
看来,丰田生产方式落地核心还是造人。习惯了零和游戏的中国人,没有点从零开始的意志和团队协作新思维,怕是没法掌握丰田生产方式的本真,更没办法使之落地。一个更大的障碍是,引入丰田生产方式,就是在企业中重新确立对与错的标准,就要赋予现场员工独立思考和追求最佳的权利,这首先侵害的是企业当权者的利益。或许这是丰田生产方式在中国没能铺开说不出的理由。
这是中国管理的问题!
不去现场不知道丰田是凭借末流厂房和设备,生产出世界一流的汽车。诺大的车间,连一台电脑都看不见,到处是原生的“看板”。一如大野耐一所说,“能够扳手指头从1数到10的人,就可以导入TPS”。丰田生产方式,是管理的一种简单回归,回归到现场的创造力。
起步时,没有一个企业家不知道现场的意义。他们自己就是一线技工、研发或销售人员,那时他们对手中的绝活有一种激情和追求。但是,当公司有了规模,引进豪华的职业管理团队,一切听凭处理数据的电脑指挥了,他们在经营管理上也就出现了迷失。他们开始怀疑起先前做法的意义,怀疑起那些原生的价值了。
同行的久立集团董事长周志江,就是这样一个从现场起家的老板。当公司销售收入超过40亿元以后,身边各种各样的规模企业、规范管理的声音越来越多,他不信邪,还是照样带领高管每个月至少到车间像个普通工人那样值一个夜班。从一线摸爬滚打出来的他,还是被丰田注重一线员工的智慧发掘深深震撼了。
他反复问讲课的日本高木老师,一般日本一线员工跟高管的收入差距有多少?他得到的回答是,一线员工与工长、科长的收入差距2倍左右,与董事、工厂总经理的差距最多不超过3倍,一线员工与公司最高级别董事副社长、总裁、专务等的收入差距在7倍左右。周志江不由得回应,我们的收入差距都是几十倍上百倍呀!老师说,“这是你们从美国搬用的做法,不创造价值的高管拿很高的薪水。这是美国公司的问题,这也是中国公司的问题!”
是的,这是中国管理的问题。中国企业界跟强调“权力与利益”的美国管理更为亲近。美国管理骨子里面是精英文化,管理者是上智,员工是下愚。高管可以拿到比一线员工高几百倍、几千倍的薪酬,而员工还要接受随时的裁员,以承担高管决策失误的风险。
或许美式管理强调的个人英雄主义,常常能化腐朽为神奇,挽狂澜于既倒,最适合中国公司权力人物的心态。还有庞大的美国“海龟军团”,渐渐统摄了中国公司高层,体现着“权力与利益”的美式管理,很容易成为中国公司权势人物心有灵犀的圣经。美国高管的高额年薪,更是受人青睐,以至于公司还没有搞出点名堂,甚至严重亏损,公司高管的薪酬都可以几百万、几千万元。公司经营状况一看好,就更不得了。一家上市公司董事长,一年下来,奖金一项就高达1亿元人民币,而一个时常在不同公司晃悠的美国“海龟”,居然可以拿到号称10亿元的年薪。一般员工的年薪也就是2万元,是员工薪酬的5万倍!不是企业昏了头,就是中国管理悲哀到了极致,竟然把公司命运押在虚无缥渺的花瓶上!
日本高木老师的话,震撼了我们在场的每一个中国人。回国后,我又托日本朋友找了一些资料,得出日本丰田公司的初略年薪序列:其中现场员工工作2-3年的年薪400万日元,工作9-10年的700万日元,工长、科长年薪为1600万日元,公司各部部长年薪为2500万日元,董事工厂总经理为3000万日元,集团公司副社长和各职能部门总监年薪5000万日元。社长、CEO年薪与公司经营业绩挂钩,变化幅度较大,具体数据不详。而据说,东芝CEO的年薪是5000万日元。
需要说明的是,不能机械地对比中日员工与高管的薪金差距。日本经济在1950-1980年的30年增长中,日本员工收入的增长速度很快,从不到美国人的10%一下子与美国人并驾齐驱,而中国经济在1978-2008年的30年增长中,工人的年薪增长极其缓慢,现在依然不足美国工人收入的10%。或许,从整个国家的意识和政策中,就没有把工人工薪增长,看成是一国竞争力增长的关键。在这样的背景下,说“中国工人的收入太低”,可能更为现实。中国面临一个大的转换,要把迅速增长的政府财政收入转换成工人工资的增长,在这个过程中,工人与高管的收入差距,自然也就降下来了。
丰田员工与高管年薪差距
l现场员工:400万—700万日元;
l工长,课长:1600万日元左右;
l各部的部长:2500万日元左右;
l董事工厂长:3000万日元左右;
l副社长总监:5000万日元左右;
l社长、CEO:8000万日元