PVC胶粒配方设计之增塑剂
增塑剂(Plasticizer)
第一节 概述
一:概念
一些常用的热塑性聚合物具有高于室温的玻璃化转变温度(Tg),在此温度以下﹐聚合物表现为类似玻璃的脆化状态﹐在此温度以上﹐则呈现较大的回弹性﹑柔韧性和冲击强度。要使聚合物具有实用价值﹐就必须使其玻璃转变温度降到使用温度以上。增塑剂就是为了解决这个问题而引入聚合物的一类助剂。增塑剂为挥发性较小之物质﹐将之添加于塑料时﹐能使塑料之弹性率﹑玻璃化转变温度(Tg)下降﹐而于常温时赋予适当之柔软性﹐于高温时减低其熔融黏度使其易于加工。广义地讲﹐凡能与树脂均匀混合﹐不与树脂发生化学反应﹐在成型加工期间保持不变﹐或者与树脂发生化学反应﹐但能长期保留在聚合物制品中﹐并能够改变聚合物某些物理性质的物质﹐都可以称为增塑剂。
聚合物与增塑剂间的作用﹐可简单地看做以下两种方式﹕
(1)树脂分子间偶极--偶极相互作用的抵消而减弱了树脂间的引力﹔
(2)通过简单的稀释作用﹐缩小树脂分子间的距离(自由体积)而形成一定的空间。结果增加了塑料片材的柔软性﹐增强了模塑制品的韧性的冲击强度。
因此可以说﹐增塑剂的主要作用是削弱聚合物分子间的次价键﹐即范德华力﹐从而增加聚合物分子链的移动性﹐亦即增加聚合物塑性。表现为聚合物的硬度﹑模量﹑伸长率﹑曲挠性和柔韧性的提高。
软质配合物的硬度与可塑剂量(参考) | |||||||||
DOP配合量(Phr) | 20 | 30 | 40 | 50 | 60 | 70 | 80 | 90 | 100 |
Shore 硬度(Duro, 25oC) | 96C | 86C | 95A | 88A | 81A | 75A | 69A | 63A | 57A |
使用树脂P=1450 |
我厂规定的P数与硬度对照表
P数 | 20 | 25 | 30 | 35 | 40 | 45 | 50 | 55 | 60 | 65 | 70 | 75 | 80 | 85 | 90 | 95 | 100 |
Shore A | 100 | 98 | 96 | 94 | 89 | 87 | 85 | 83 | 80 | 77 | 75 | 73 | 70 | 67 | 64 | 62 | 56 |
二 ﹑增塑剂应具备的条件
(1)塑化效率(plasticizing efficiency)高,以较少的加入量获得较高的塑化效果.
(2)与树脂相溶性行(compatibility)佳.相溶性不足时,增塑剂会从树脂中分离出来,表现为渗出发汗等情况.
(3)挥发性(volatility)低减少成型加工以及制品存放过程中挥发损失对制品性能的影响.
(4)耐久性好耐水﹑耐油﹑耐有机溶剂的抽出。抽出性是指增塑剂向液体介质中的移动现象,塑料制品和与溶剂或洗涤液接触时,易抽出的增塑剂就会被抽取出来.
(5) 耐迁移性好耐迁移(Nonmigration)指增塑剂由增塑制品中向着与其接触的另一种塑料制品(包括增塑剂种类和用量不同的一种塑料制品)迁移的现象
(6)耐寒性好低温下仍有良好的柔软性
(7)耐热性好在加工温度和使用温度在较高的温度下保持稳定.
(8)无毒﹑无味﹑无臭﹑无色。
(9)耐霉菌性好
(10)具有阻燃性。
(11)电气绝缘性良好。
(12)耐污染﹑耐化学药品侵蚀。
(13)价格低。
没有一种增塑剂能完全符合上述条件。使用时只能根据制品的需求﹑增塑剂的性能和市场情况﹐选择综合性能较优秀的产品。性价比经常作为选择助剂的一个标准﹐性价比越高﹐产品越有优势。
第二節作用机理
一:影响塑化的主要因素
1.聚合物的分子间力
增塑剂加入到聚合物中时﹐增塑剂分子之间﹑增塑剂与聚合物分子之间的相互作用力对增塑作用影响很大。这种相互作用主要是范德华力和氢键力﹐范德华力又包括色散力﹑诱导力和取向力3种。
(1)范德华力色散力存在于所有极性或者非极性的分子之间﹐系同微小的瞬间偶极的相互作用﹐使靠近的偶极处于异极相邻状态而产生的吸力﹐但只有在非极性的体系中﹐其色散力才占主要地位。当一个具有偶极的分子在相邻的一个非极性分子中﹐诱导出一个诱导偶极时﹐诱导偶极和固有偶极之间的分子吸引力称作诱导力。对于芳族化合物﹐诱导力特别强。聚苯乙烯与低分子量的酯的增塑作用主要是诱导力.
当极性分子相互靠近时,由于固有偶极取向,引起分子间产生一种作用力,通常称为取向力.酯类增塑剂与PVC的相互作用就是一个代表例子.
(2)氢键含有-OH基或-NH-基团的分子,如聚XIAN胺,聚乙烯醇等在分子间能够形成氢键.氢键是一种比较强的相互作用键,它的存在会妨碍增塑剂分子插入到聚合物分子间.氢键沿着聚合物分子链分布越密,相应的增塑剂分子插入越困难,因此要求增塑剂与聚合物分子产生类似的强的作用.当温度升高时,由于分子的热运动妨碍了聚合物分子的取向,氢键的作用会相应减弱.
2.聚合物的结晶度±
空间有规结构聚合物的分子链在适当的条件下可以结晶,
增塑剂的分子插入结晶区域要比插入无定形区域要困难的多。因为在结晶区聚合物链之间的自由空间最小。如果增塑剂的分子仅仅能插入部分结晶聚合物的无定形区域﹐则此增塑剂便是非溶剂型增塑剂。如果增塑剂的分子即能插入聚合物的无定形区域﹐又能插入结晶区域﹐则此增塑剂便是溶剂型增塑剂﹐所谓主增塑剂。
二 ﹑增塑剂的作用机理
1.润滑理论
润滑理论认为﹐树脂能够抵抗形变(刚性)是因为分子间有磨擦力。增塑剂能起润滑剂作用﹐促进大分子间或者分子链间的运动。增塑剂仅仅降低分子间的作用力﹐因此只能引起部分增塑。
2.凝胶理论
凝胶理论认为﹐聚合物抗形变由于内部存在着三维蜂窝状结构或者凝胶所致。这种凝胶是由于在聚合物分子链间或多或少发生粘着而形成的。由于分子吸咐点常集中在一块﹐因此软质塑料或者硬质塑料中的蜂窝是很小的。这种蜂窝弹性极小﹐很难通过物体内部的移动使其变形。增塑剂进入树脂中﹐沿高分子链产生许多吸咐点﹐通过新的吸咐而松弛破坏原来的吸引力﹐并替代了聚合物分子内的引力中心﹐使分子容易移动。
3.溶剂化理论
基于胶体化学。增塑剂的溶剂化和溶胀能力取决于3种分子间作用力。增塑剂/增塑剂﹐增塑剂
/聚合物﹐聚合物/聚合物之间的力。增塑剂应该是小分子﹐对聚合物分子应该有一定的吸引力﹐而该力要小于聚合物/聚合物之间的作用力。增塑剂/增塑剂间的力越低﹐越能发挥增塑剂的效能。增塑剂也不应该太小﹐否则容易挥发。
4.极性理论
极性理论认为﹐在增塑剂分子﹑聚合物分子和增塑剂/聚合物分子之间必须很好的平衡﹐以确保凝胶是稳定的。因此增塑剂必须是含有一个或者多个与特定聚合物极性相匹配的极性或者非极性基团。即以上提出的聚合物的结晶度。
三﹕增塑过程
一般认为﹐增塑过程分为以下几步﹕
1.润湿﹑表面吸咐
增塑剂分子进入树脂树脂孔隙并填充其孔隙。
2.表面溶解
增塑剂渗入到树脂粒子中的速度很慢﹐特别在低温时更是如此。一般认为增塑剂先溶解溶胀聚合物表面的分子﹐当聚合物表面有悬浮聚合残留的胶体时﹐能延长诱发阶段。
3.吸咐作用
树脂颗粒由外部慢慢地向内部溶胀﹐产生了很强的内应力﹐表现为树脂和增塑剂的总体积减少。
4.极性基的游离
增塑剂掺入到树脂内﹐并局部改变其内部结构﹐溶解了许多特殊的官能团﹐反应为增塑剂被吸咐之后﹐介电常数比起始混合物高。这一过程受温度和活化能大小的影响。
5.结构破坏
干混料中的增塑剂是以分子束的形式存在于高分子或者链段之间。当体系受到较高能量如加热至160----180oC,或者将其辊炼。聚合物的结构将会破坏﹐增塑剂便会渗入到该聚合物的分子束中。
6.结构重建
增塑剂与聚合物的混合物加热到流动态而发生塑化后﹐再放冷﹐会形成一种有别于原聚合物的结构。这一结构表现出较高的韧性﹐但结构形成往往需要一段时间。比如使用DOP作增塑剂时﹐经过一天才能达到最大的硬度﹐而使用中等分子量的聚酯﹐则需要一周的时间。
第三節增塑剂的性能及评价
一 ﹑塑化效率
增塑剂的主要作用是降低聚合物分子间的相互作用力﹐增加聚合物分子链的移动性﹐即降低聚合物的软化温度﹐这是增塑剂最基本的性能。不同的增塑 剂塑化效能不同﹐其性能优劣通常用塑化效率来表示。塑化效率可理解为使树脂达到某一柔软程度的增塑剂用量﹐它是一个相对值﹐可以用来比较增塑剂的塑化效果。
在实际应用中﹐聚合物塑化的结果表现为玻璃化温度和模量的下降。为此经常为玻璃化温度和模量来表示增塑剂的塑化效率。
1.玻璃化温度
增塑剂作用导致聚合物分子链间的移动﹐其移动性通常用玻璃化温度来度量。在玻璃化温度以上聚合物是柔软的﹐在玻璃化温度以下是坚硬的。可见不同的增塑剂在相同添加量的情况下﹐玻璃化温度越低﹐则塑化效果越好。
一般情况下﹐PVC的玻璃化温度为80oC左右﹐但每加入10PHR的DOP,其玻璃化温度为下降20---25oC﹐若加入50PHR的DOP﹐则PVC的玻璃化温度下降到-60oC.
2.模量
塑化效率不仅可用玻璃化温度的降低来表示﹐而且可用与温度有关的力学性能如模量和阻尼来表示。模量表示比较复杂﹐但比较客观﹐此处不多讲述。
3.影响塑化效率的因素
增塑剂的塑化效率与本身的化学结构以及自身的物理性能有关﹐主要表现为以下几个方面﹕
(1)增塑剂的分子量影响增塑剂的塑化效率。分子量小的增塑剂显示出良好的塑化效率。
(2)分子量相同的情况下﹐分子内极性基团多的或者环状结构多的增塑剂﹐塑化效率较差。
(3)支链烷基结构的增塑剂塑化效率不及相应的直链烷基的增塑剂。
(4)酯类增塑剂中﹐烷基链长增加﹐塑化效率降低。
(5)在酯类增塑剂中﹐烷基部分由芳基取代﹐塑化效率降低。
(6)在酯类增塑剂中﹐烷基碳链中引入醚链﹐能提高塑化效率。
(7)在烷基或者芳基中引入氯取代基﹐塑化效率降低。
(8)增塑剂的塑化效率与自身黏度有关。增塑剂的等效用量是随其黏度上升而增加的。
二.兼容性
作为增塑剂﹐首先要与树脂兼容﹐这是增塑剂最基本的性质之一。如果增塑剂与树脂不兼容﹐塑化效率就无从谈起。增塑剂可能溶解一部分树脂﹐但大部分是渗入高分子链间起溶胀作用﹐因此可以简单的把增塑剂视为溶剂。增塑剂的兼容性可以用溶解度参数﹑相互作用参数﹑特性黏度﹑介电常数等表征。
聚合物和增塑剂的结构对兼容性有很大的影响。结构基本上类似的树脂和增塑剂兼容性良好。作为主增塑剂使用的烷基碳原子数为4----10的邻苯二甲酸酯﹐与PVC的兼容性是良好的﹐但是随着烷基碳原子数进一步增加﹐其兼容性急速下降。因此使用的邻苯二甲酸酯类增塑剂的烷基碳原子数通常不超过13个。酯类增塑剂中烷基为戊基时兼容性最好。
环氧酯类增塑剂中﹐多元醇酯比单酯兼容性好﹔聚脂增塑剂分子量较大﹐故兼容性较差﹐需用较高的温度的强烈机械混炼来补尝。氯化石蜡虽然有较强的极性﹐但单独使用时﹐仍有析出现象﹐只能作为辅增塑剂使用。此外环状结构比脂肪族链烃的增塑剂兼容性好﹔分支结构比直链接构的增塑剂兼容性好。
三﹑ 加工性
选用不同的增塑剂将显著地影响杩脂的加工性能。因此选择增塑剂时必须考虑基加工性。增塑剂的加工性与兼容性密切相关﹐一般来说兼容性好的增塑剂加工性也好。当然也要考虑增塑剂的其它性能参数﹐如黏度﹑闪点等。
加工性柯以通过凝胶化速度﹑凝胶化温度﹑鱼眼状斑点消失速率等参数反映出来。分子量大﹐兼容性差的邻苯二甲酸酯的凝胶化速度较慢﹐反映出这些增塑剂加工差。配合物的加工性同时受稳定剂和润滑剂的影响。使用了兼容性差的润滑剂和较大用量的稳定剂的情况下﹐需要充分考虑混合料的加工性﹐防止增塑剂的渗出。
四﹑耐寒性
所谓增塑剂的耐寒性是指用增塑剂增塑的聚合物制品的耐低温性能﹐反映在低温脆化温度﹑低温柔软性等指标。通常将PVC树脂中加入1%摩尔分数增塑剂报引起的玻璃化温度的下降值﹐称为增塑剂的低温效率值。增塑剂的耐低温性能一方面取决于增塑剂的结构﹐包括链长短﹑分支情况﹑官司能团和种类和多少等﹔另一方面﹐取决于增塑剂进入聚合物链间的极性影响和隔离作用﹐还与增塑剂本身的活化能有关﹐增塑剂黏度越大﹐流动活化能越大﹐则耐寒性越差。
增塑剂的耐寒性与兼容性有相反的关系。以直链亚甲基为主体的二元脂类有良好的耐寒性﹔含有较长的直链的邻苯二甲酸酯类一般耐寒性良好发﹐但随着烷基支链的增加﹐分子链的柔性降低﹐相应的增塑剂耐寒性下降。因此作为主增塑剂的直链醇的邻苯二甲酸酯都具有良好的耐寒性。当增塑剂分子中含有环状结构时﹐耐寒性会显著。目前作为耐寒性增塑剂使用的主要是脂肪族二元酸酯(DOA﹑DOS﹑DOZ等)。
五﹑稳定性
增塑剂本身有很好的化学稳定性﹐在贮存期间几乎不用考虑热和光造成的影响﹐但增塑剂的类型的浓度对聚合物配合物的兴﹑热稳定性影响较大。
1.贮存稳定性
贮存稳定性显示的是增塑剂本身的性能。有杂质会使其降低。
2 . 热稳定性
热稳定性是指制品加工和使用过程中受热时的稳定性。增塑剂热稳定性与增塑剂的结构有直接关系。除了增塑剂的结构外﹐以下因素也会影响热稳定性﹕
(1)增塑剂的纯度对热稳定性有显著的影响。纯度越高﹐热稳定性越好。
(2)增塑剂的润滑性影响其热稳定性﹐润滑性强的增塑剂能明显地改善动态热稳定性。
(3)增塑剂的挥发性影响动态其热稳定性﹐挥发性高的增塑剂会使热稳定性显著降低。
(4)PVC的分解产物HCL对羟酸酯的热分解具有催化作用﹐造成增塑剂本身的热稳定性下降。
3. 抗氧稳定性
增塑剂的抗氧稳定性与其本身的结构有关﹐增塑剂氧化之后﹐反映为酸值增加。
4.光稳定性
增塑剂的光稳定性是指其抵抗光氧老化的性能﹐也可称为耐候性。一般耐寒性优良的增塑剂是不耐候的。环氧化合物可以一很大程度上提高PVC的耐候性。
六﹑耐久性
多数增塑剂与聚合物不能形成化学键合﹐增塑的树脂组成物处于动态﹐其中的聚合物分子不断地结合﹐又不断的分离。因此增塑剂有从增塑组成中移出的倾向。特别是在PVC软制品中﹐或是说增塑剂用量较多的情况下﹐增塑剂移出现象往往比较严重。
增塑制品在使用过程中﹐增塑剂从制品中移出的主要通过以下三个途径﹕
●挥发--------增塑剂从制品表面挥发出来﹐散失在空气中’
●抽出--------增塑剂从制品表面转移至与之接触的液体中。
●迁移--------增塑剂从制品表面转移至与之接触的固体中。
故增塑剂的耐久性即包括耐挥发性﹑耐抽出性和耐迁移性。增塑剂的耐久性与分子量用分子结构密切相关。要得到良好的耐久性﹐增塑剂的相对分子量一般要求大于350。
1.挥发性
增塑剂的挥发性是很增塑剂从塑化物内部向周围空气中逃逸的倾向。挥发过程首先从制品内部向表面迁移﹐然后从表面蒸发逸入空气中。增塑剂的挥发性与分子量用分子结构密切相关﹐一般分子量小的挥发性大。同时兼容性好增塑剂挥发性大。分子内具有庞大的基团的增塑剂﹐由于它们在塑化物内扩散比较困难﹐所以挥发性小。在常用的邻苯二甲酸酯中DOP挥发性较大﹐故使用此增塑剂时应该考虑其挥发性对生产操作造成的影响。
2.抽出性
抽出性是指增塑的聚合物制品与液体介质接触时﹐增塑剂从聚合物内部向液体介质中迁移的倾向。增塑剂能被多种液体抽出﹐因此在增塑制品与液体接触时﹐应该设法使增塑剂保留在制品中。抽出性大小一方面取决于增塑剂的结构﹑极性﹑分子量等因素﹔另一方面取决于同塑化物接触的液体介质的性质。增塑剂的耐水性和耐肥皂水性同耐油性恰好相反﹐分子中烷基比例大的耐水性和耐肥皂水性更好。聚酯增塑剂是耐久性优良的增塑剂﹐其性质随原材料的不同以及端基的不同有一定差别﹐但对其影响最大的还是分子量。高分子量的聚酯增塑剂耐挥发性﹑耐抽出性和耐迁移性良好﹐但耐寒性和塑化效率较差。
3.迁移性
增塑剂的迁移是指增塑剂向固体介质扩散的过程。在此过程上﹐增塑剂从浓度高的塑化物通过一些接触点扩散到另一个与之接触的塑料或者橡胶等聚合物中。增塑剂的迁移性是相对于所接触的固体而言的﹐迁移现象的发生往往导致塑化物出现软化﹑发黏甚至表面脆裂等现象﹐同时还会导致制品污染。
增塑剂的迁移性与增塑剂本身的结构和与塑化物接触的聚合物介质密切相关。邻苯二甲酸酯类的迁移性随脂肪链的长度增加而急剧。增塑剂对硝酸纤维素﹑ABS的迁移性较大﹐而对PP﹑PE和聚苯乙烯迁移性较小。
七﹑绝缘性
纯净的PVC树脂有良好的电气性能﹐硬质PVC制品的体积电阻率是很大的﹐但会随着增塑剂的入而逐渐降低。PVC塑化物的绝缘性通过电阻率﹑介电常数﹑功率因素﹑耐电压击穿强度等参数反映出来﹐其中使用较多的是体积电阻。一般体积电阻随增塑剂的种类不同有明显差异﹐随着增塑剂用量的增加﹐绝缘性逐渐降低。
耐寒性与电性能是成反比的﹐一般耐寒性能好的电性能差。这是因为极性较低的增塑剂允许聚合物链上的偶极有更大的自由度﹐从而使导电率增加电绝缘性降低。另一方面分子内支链较多的﹑塑化效率差的增塑剂却有较好的电性能。DOA会使塑化物体积电阻降低最甚。而氯化石蜡是绝缘增塑剂的典型代表。
增塑剂的纯洁度与塑化物的电性能有密切的关系﹐因为带电的离子性物质容易在塑化物中移动﹐增塑剂含有离子性杂质时﹐电绝缘性会显著下降。
八﹑难燃性
PVC为含氯量56%的聚合物﹐本身具体有阻燃性和自熄性﹐如配合使用阻燃性能好的可塑剂﹐阻燃性更优。但如果配合普通的可燃性增塑剂﹐PVC塑化物就不再阻燃。阻燃性通常可能延燃时间或者氧指数来表示。延燃时间长者难燃性好﹐氧指数高者难燃性能好。一般说来﹐增塑剂的难燃性受以下几个方面影响﹕
(1)增塑剂对于聚合物的挥发性。挥发性越大﹐难燃性越差。
(2)燃烧时产生的分解物。分解物最好不是助燃物﹐如是将使难燃性降低。
(3)增塑剂的化学结构。增塑剂中含有磷﹑氯和芳基结构时﹐难燃性比较好。
目前广泛使用的难燃性增塑剂有磷酸酯类﹑氯化石蜡类和氯化脂肪酸类。磷酸酯类增塑剂的最大特点是阻燃性强﹐广泛使用于PVC的增塑剂﹐单独作为阻燃剂时﹐也能产生较好的阻燃作用。氯化石蜡类价廉﹐大量作为辅助增塑剂使用﹐氯化石蜡的性能与含氯量密切相关﹐随着氯含量的增加﹐阻燃性和兼容性都得到改善﹐但耐寒性却显著变差。氯化脂肪酸类与PVC的兼容性比氯化石蜡好。
九﹑黏度稳定性
黏度稳定性针对增塑糊而言。
十﹑毒性
大多数增塑剂或多或少有一定毒性。DOP用普通包装是安全的﹐但接触高脂肪食品时有被油类抽出的可能﹐应予避免。DOA具有良好的卫生性。磷酸酯类属于毒性较高的增塑剂。
第四節增塑剂各论
一﹑苯二甲酸脂
1.概况
大多数增塑剂在化学上都可归为两类﹐一类是高沸点的脂﹐另一类是某些分子结构﹑形状和大小与增塑聚合物十分相似的物质。不言而喻﹐苯二甲酸脂属于前一类。苯二甲酸脂类是增塑剂中最重要的类别。与PVC有极好的的兼容性﹐是苯二甲酸脂的一大特性。苯二甲酸脂一般都有适度的极性﹐其溶解度和介最常数与PVC都较相近。聚合物和溶剂的溶解度参数相同或者相近时﹐聚合物才能溶入到此溶剂。
2.主要类别及性能特点
苯二甲酸脂类包括邻苯二甲酸脂﹑间苯二甲酸脂和对苯二甲酸脂。邻苯二甲酸脂又有低碳醇酯﹑高碳醇酯﹑侧链醇酯﹑直链醇酯﹑单一醇酯﹑混合醇酯﹐烷基脂﹑芳基脂等等。
(1)邻苯二甲酸脂邻苯二甲酸脂是性能全面的无毒或者低毒的主增塑剂。其中邻苯二甲酸二甲脂(DMP)和邻苯二甲酸二乙脂(DEP)因挥发性大,且具有刺激性﹐不宜在PVC中使用。邻苯二甲酸二丁脂(DBP)虽然挥发性大耐久性差,但兼容性好,塑化效率高,因此有部分使用.邻苯二甲酸脂中应用最多的还是C6—13的,高碳醇酯.其中常用的有邻苯二甲酸二辛脂(DOP), 邻苯二甲酸二庚脂(DHP),邻苯二甲酸二异辛脂(DIOP), 邻苯二甲酸二异壬脂(DINP), 邻苯二甲酸二异癸脂(DIDP)等.
(2) 对苯二甲酸脂对苯二甲酸脂为结晶固体,与PVC兼容性差,但具有一定支链度的C8---9醇酯是液体,与PVC有较好的兼容性.对苯二甲酸脂的挥发性﹑低温性及电性能均优于相应的邻苯二甲酸脂﹐为耐迁移的增塑剂。代表性品种为对苯二甲酸二(2-乙基已)脂(DOTP)。
(3)间苯二甲酸脂间苯二甲酸脂的溶剂化能力﹑挥发性和耐抽出性均优于对苯二甲酸脂。代表品种为间苯二甲酸二辛脂(DOIP).
4.代表性产品
(1)邻苯二甲酸二丁脂(DBP)低碳醇酯的代表。良好的加工性﹑耐低温性﹑耐老化性。但因其挥发性大﹐耐水抽出性差﹐因而不常用。
(2)邻苯二甲酸二(2-乙基已)脂俗称邻苯二甲酸二辛脂﹐常温下为无色或淡色油状透明液体。凝固点-53oC,沸点386oC.DOP与树脂兼容性好,挥发性小,光、热稳定性好,电性能好,耐低温,相当低的毒性;能满足大多数通用制品的要求,可单独便用在许多配方中,是性能全面、应用最广泛的标准增塑剂;缺点: 不耐油。
(3)邻苯二甲酸二异辛脂(DIOP)DIOP的溶点较低,塑化效率与DOP相当,在软质PVC中可与DOP互用.但挥发性﹑低温柔软性﹑电性能比DOP差.
(4)邻苯二甲酸二异壬脂(DINP)一般特性都与DOP相当,但挥发性较低,这不仅仅有利于改善加工环境,且能提高制品的耐久性.特别是耐热老化性能较好.
(5)邻苯二甲酸二异癸脂(DIDP)有较好的挥发性、绝缘性﹐抗雾性佳,移行、耐水、耐油、耐热及电气特性比DOP好,须与耐低温增塑剂(如DOA)同用,否则制品较硬;常用于耐高温或耐低温的制品中。
二﹑脂肪类二元酸脂
1.概况
脂肪类二元酸脂是一类典型的耐寒性增塑剂。常用的脂肪类二元酸脂为已二酸脂﹑壬二酸脂和癸二酸脂。主要产品有已二酸二(2-乙基已)脂(DOA)﹑癸二酸二(2-乙基已)脂(DOS)﹑壬二酸二(2-乙基已)脂(DOZ)等。
2.主要性能特点
同邻苯二甲酸脂类相比﹐脂肪类二元酸脂主要表现出以下特点不。
(1)低温性能优于DOP﹐其中耐寒性最佳的是DOS。
(2)塑化效率优于DOP。
(3)本身黏度低﹐配制塑 料糊的稳定性好。
(4)兼容性差。通常只用作辅助增塑剂。
(5)耐久性差。DOP本身耐久性不好, 脂肪类二元酸脂模拟DOP更差.
(6)电绝缘性能差。 这是因为此类增塑剂极性低﹐允许聚合物链节上的偶极有更大的自由度﹐所以会使PVC的导电率增大﹐电绝缘性降低。
(7)耐旋光性差﹑耐候性差。
3. 脂肪类二元酸脂结构对耐寒性的影响
脂肪类二元酸脂的分子结构对其作为增塑剂的低温性能影响很大。通常分子中脂肪链碳原子数与酯基数的比值(Ap/Po)越大﹐耐寒性越好。
4.代表性品种
(1)已二酸二(2-乙基已)脂(DOA)DOA系耐寒性良好的增塑剂﹐与PVC有良好的兼容性﹐有一定耐热耐光和耐水性且无毒。在押出过程中显示出良好的润滑性﹐制品手感好。抗油性差﹐通常与DOP﹑DIDP共享于耐寒配方。
(2)壬二酸二(2-乙基已)脂(DOZ)近乎白色的透明液体﹐乙烯基树脂优良的耐寒增塑剂。黏度低﹐沸点高﹐增塑效率高﹐挥发性和迁移性小﹐且具有优良的耐光热性﹑电绝缘性﹐耐寒性也优于DOA。
(3)癸二酸二(2-乙基已)脂(DOS)淡黄色或者无色透明油状液体。能在高温下安全加工﹐耐水性优于DOA﹐但耐氧化性﹑耐候性﹑耐抽出性差。使用时与主增塑剂配合﹐用量不得大于主增塑剂的1/3。
三﹑偏苯三酸脂
1.概况
偏苯三酸脂属于苯多酸脂的范畴。这种酯的特点是挥发性低﹑耐抽出﹑耐迁移﹐具有类似聚酯增塑剂的优点﹐同时兼容性﹑加工性﹑低温性能又类似于单体型邻苯二甲酸酯﹐所以兼具有单体增塑剂的聚合增塑剂两者的优点。通常作为耐热﹑耐久性增塑剂使用。
2.主要品种及性能
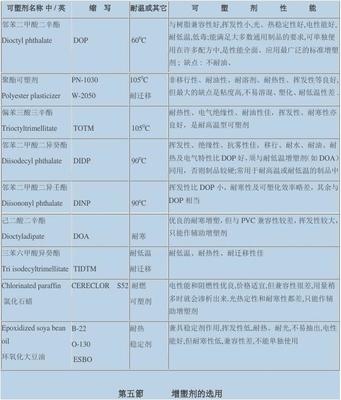
常用的偏苯三酸脂主要有偏苯三酸三(2-乙基已)脂(TOTM)﹑偏苯三酸三异辛脂(TIOTM)﹑偏苯三酸三异癸脂(TIDTM)等。
(1)偏苯三酸三(2-乙基已)脂(TOTM)偏苯三酸脂的代表性产品。偏苯三酸三(2-乙基已)脂(TOTM)属于耐热性和耐久性增塑剂﹐增塑效率与邻苯二甲酸酯相近﹐耐近性可与聚酯媲美﹐但耐油性不如聚酯可塑剂。
(2)偏苯三酸三异辛脂(TIOTM) 主要作耐热性增塑剂﹐性能与用途与偏苯三酸三(2-乙基已)脂(TOTM)相似。
(3)偏苯三酸三异癸脂(TIDTM)性能与偏苯三酸三(2-乙基已)脂(TOTM)类似﹐挥发性更小﹐耐久性优良﹐加工性能也比较好。
偏苯三酸脂的结构与邻苯二甲酸酯相近﹐与PVC的兼容性也很好﹐也可作为主增塑剂。偏苯三酸脂价格较高﹐多采用邻苯二甲酸的高碳醇酯与之配合。即使在建筑用电线绝缘材料这样对耐热性要求严格的场合﹐目前也多采用偏苯三酸三(2-乙基已)脂(TOTM)或者偏苯三酸三异辛脂(TIOTM)与邻苯二甲酸二异癸脂(DIDP)配合使用的做法。
与聚酯可塑剂相比﹐偏苯三酸脂的缺陷是不耐油和溶剂的抽出﹐迁移性也较差﹐因此有些要求耐油耐热的电线料﹐不得不选用聚酯可塑剂。偏苯三酸脂主要用于低挥发性﹑低水抽出性﹑低迁移性﹑耐热性以及良好的电绝缘性能的场合﹐可以作主增塑剂使用。
四﹑磷酸酯
1.概况
磷酸酯是广泛使用的阻燃性增塑剂品种。可作为主增塑剂使用﹐属于多功能新产品﹐通常使用的有4种类型。磷酸三烷基酯﹑磷酸三芳基酯﹑磷酸烷基芳基酯和含氯磷酸酯。有应用的有磷酸三(2-乙基已)酯(TOP)﹑磷酸二苯一辛酯(ODP)﹑磷酸甲苯二苯酯(CDP)﹑磷酸三甲苯酯(TCP)等.
2.性能特点
(1) 兼容性好磷酸三烷基酯的兼容性优于磷酸三烷基酯。
(2) 优良的阻燃性所有的磷酸酯都表现出良好的阻燃性﹐单独使用时更为明显。其阻燃性随磷含量的增加而提高﹐并逐步由自熄转变为难燃性。分子中烷基越少﹐耐燃性越好﹐在磷酸酯引入卤素原子更能提高阻燃性
(3) 耐久性好挥发性﹑抽出性较DOP好.
(4)大部分磷酸酯具有耐菌性和耐候性。
(5)耐寒性差磷酸三芳基酯耐寒性差﹐但挥发性小﹔磷酸三烷基酯耐寒性稍好﹐但挥发性大。
(6)有毒磷酸酯大多有毒﹐仅仅有磷酸二苯一辛酯(ODP)低毒。
(7)价格高常与氯代烃配合使用。
磷酸酯和常用的阻燃剂(例如Sb2O3等)有对抗作用﹐二者不能配合使用。
3.代表产品
(1)磷酸三甲苯酯(TCP) 微具气味的浅色液体。水解稳定性好﹐耐油性和电绝缘性﹑耐菌性优良。耐寒性差﹐配合DOA使用可以改善。
(2)磷酸甲苯二苯酯(CDP)无色无臭的清亮液体。与树脂兼容性好。与磷酸三甲苯酯(TCP)相比﹐耐久性﹑阻燃性的电性能相似﹐但增塑效率高﹐低温特性和制品的耐磨性好。光稳定性差。挥发性大。
(3)磷酸二苯一辛酯(ODP)无毒。磷酸二苯一辛酯(ODP)挥发性低﹐耐寒性和耐候性较好。与DOP或者DIDP配合使用,可提高制品的韧性和耐候性。
五﹑聚酯增塑剂
1.概况
聚酯增塑剂主要用于耐久性要求特别高的制品﹐可用作主增塑剂﹐也可与其它增塑剂配合使用。
2.聚酯增塑剂的品种和性能
制备聚酯增塑剂常用的二元酸有已二酸﹑癸二酸﹑壬二酸﹑邻苯二甲酸酐等﹐常用的二元醇主要有1﹐2-丙二醇﹑1﹐3-丁二醇﹑一缩二乙二醇等。封端用的一元醇包括2-乙基已醇﹑丁醇等﹐封端用的一元酸包括月桂酸﹑辛酸等。考虑到上述原材料的不同组合和分子量之间的差异﹐聚酯增塑剂的品种很多﹐性能差别也较大。
同传统增塑剂相比﹐聚酯增塑剂主要表现为以下几个方面的特点﹕
(1) 兼容性较差。一般已二酸聚酯增塑剂兼容性较差﹐而癸二酸和邻苯二甲酸聚酯增塑剂的兼容性稍好一些。
(2) 塑化效果不如DOP.
(3)挥发性小﹐挥发损失少。
(4)聚酯增塑剂在PVC中扩散速度小﹐因此迁移性小于DOP.
(5)耐各种溶剂的抽提。
(6)电性能略低于邻苯二甲酸酯。
(7)聚酯增塑剂毒性低。
3.化学结构对性能的影响
(1)化学结构对兼容性的影响低碳二元酸制成的聚酯增塑剂兼容性差﹐容易产生渗出﹔高碳二元酸无此现象。当二元酸固定时﹐具有侧链的二元醇可得到较好的兼容性。
(2)化学结构对机械性能的影响当二元醇固定时﹐PVC制品的拉伸强度随二元酸中碳原子数的增加而提高﹔当二元酸固定时﹐拉伸强度与二元醇中碳原子数的增加而降低。
(3)化学结构对抽出性的影响二元醇中碳原子数增加﹐则聚酯增塑剂在PVC中被汽油抽出增加。使用有侧链的二元醇时﹐汽油抽出较少。肥皂水的抽出与之相反。
(4)分子量的影响聚酯增塑剂分子量增加﹐产品黏度增大﹐塑公效率降低﹐兼容性和加工性变差﹐抽出性和挥发性则降低。
六﹑环氧增塑剂
1.概况
环氧增塑剂是含有三元环氧环的增塑剂。大多环氧增塑剂可以作为PVC的辅助稳定剂使用。少量加入就可改善制品对光热稳定性。
2.主要性能
(1)环氧增塑剂用量过高时﹐会产生兼容性差的问题。
(2)光热稳定性能优良。
(3) 耐久性好在常用的环氧增塑剂﹐环氧大豆油挥发性最小。环氧增塑剂的耐抽出性优于DOP。环氧大豆油耐迁移性非常好。
(4)毒性低。
3.代表产品
目前所用的环氧增塑剂主要有3类﹐即环氧化油﹑环氧脂肪酸单酯和环氧四氢邻苯二甲酸酯。
(1)环氧化油环氧化油有化学结构为环氧甘油三羟酸酯。这是使用最多的一类环氧增塑剂﹐主要品种有环氧大豆油和环氧亚麻仁油。环氧大豆油主要成分为十八碳的不饷脂肪酸﹐来源不同组成差异很大。环氧大豆油挥发性低﹐迁移性小﹐具有优良的热稳定性和光稳定性﹐耐水油性和耐油性也较好﹐并可赋予制品良好的机械强度﹑耐候性和电性能。与聚酯类增塑剂并用﹐可减少聚酯的迁移﹐与热稳定剂并用﹐显示良好的协效应。
(2)环氧脂肪酸单酯环氧脂肪酸单酯也是由天然油脂制成的。其性能比较全面﹐增塑效率好﹐兼容性和耐抽出性都很出色。
(3)环氧四氢邻苯二甲酸酯环氧四氢邻苯二甲酸酯是一类合成环氧增塑剂。因为结构的特点﹐这类增塑剂即具有苯二甲酸酯的性能﹐又有环氧酯的性能﹐是一类较理想的多功能增塑剂。
七﹑其它增塑剂
(1)多元醇酯多元醇酯主要包括乙二酯﹑丙三酯﹑一缩二乙二酯﹑甘油和苯甲酸酯等。
与传统增塑剂相比﹐多元醇酯在以下几个方面表现出一定的优势。
1.优良的低温性能与DOA相似了﹐与PVC兼容性差﹐仅用辅助增塑剂。
2.优良的耐热﹑耐老化及耐抽出性 其电性能也很好﹐可作为耐热增塑剂和高温绝缘材料的增塑剂。
3.良好的耐污染性及无毒
(2)柠檬酸酯柠檬酸化学名称为2-羟基-1﹐2﹐3-丙烷三羟酸﹐与适当的碳原子的醇进行酯化。真正的无毒增塑剂。
(3) 氯代烃与非氯代烃相比﹐氯代烃的热稳定性﹑光稳定性略差﹐但其兼容性较好﹐挥发性较低。常用的氯化石蜡根据含氯量不同可分为氯化石蜡-42﹑氯化石蜡-50﹑氯化石蜡-52和氯化石蜡-70。氯化石蜡-42在PVC中配用限度为25-40PHR﹐而氯化石蜡-52可配用35-60PHR。氯化石蜡可用105oC电线配方。氯化石蜡对制品热光稳定性和阻燃性都取决于其氯含量﹐而无分子链长短无关。
八﹑各种增塑剂的性能概括
本厂使用的增塑剂主要使用于PVC电线电缆料﹐其性能要求都应符合电线电缆料的要求。
下表中列出本厂所用的增塑剂及主要性能﹕
可塑剂名称中/英 | 缩 写 | 耐温或其它 | 可 塑 剂 性 能 |
邻苯二甲酸二辛酯 Dioctyl phthalate | DOP | 600C | 与树脂兼容性好,挥发性小,光、热稳定性好,电性能好,耐低温,低毒;能满足大多数通用制品的要求,可单独便用在许多配方中,是性能全面、应用最广泛的标准增塑剂;缺点: 不耐油、 |
聚酯可塑剂 Polyester plasticizer | PN-1030 W-2050 | 1050C 耐迁移 | 非移行性、耐油性、耐溶剂、耐热性、挥发性等良好,但最大的缺点是粘度高,不易溶混、塑化、耐低温性差. |
偏苯三酸三辛酯 Trioctyl trimellitate | TOTM | 1050C | 耐热性、电气绝缘性、耐油性佳,挥发性、耐寒性亦良好,是耐高温型可塑剂 |
邻苯二甲酸二异癸酯 Diisodecyl phthalate | DIDP | 900C | 挥发性、绝缘性、抗雾性佳,移行、耐水、耐油、耐热及电气特性比DOP好,须与耐低温增塑剂(如DOA)同用,否则制品较硬;常用于耐高温或耐低温的制品中 |
邻苯二甲酸二异壬酯 Diisononyl phthalate | DINP | 900C | 挥发性比DOP小,耐寒性及可塑化效率略差,其余与DOP相当 |
己二酸二辛酯 Dioctyl adipate | DOA | 耐寒 | 优良的耐寒增塑,但与PVC兼容性较差,挥发性较大,只能作辅助增塑剂 |
三苯六甲酸异癸酯 Tri isodecyl trimellitate | TIDTM | 耐低温 耐迁移 | 耐低温、耐热性、耐迁移性佳 |
Chlorinated paraffin 氯化石蜡 | CERECLORS52 | 耐燃 可塑剂 | 电性能和阻燃性优良,价格适宜,但兼容性很差,用量稍多时就会渗析出来.光热定性和耐寒性都差,只能作辅助增塑剂 |
Epoxidized soya bean oil 环氧化大豆油 | B-22 O-130 ESBO | 耐热 稳定剂 | 兼具稳定剂作用,挥发性低,耐热、耐光,不易抽出,电性能好,但耐寒性低,兼容性差,不能单独使用 |
第五節增塑剂的选用
为了使PVC制品具有良好的综合性能,一般选用增塑剂应考虑以下几点:
1.与PVC树脂有良好的兼容性,这样有利于获得质量稳定的PVC制品.DOA与大豆油等增塑剂与树脂兼容性不好,只能做辅助增塑剂.
2.对PVC树脂有高的塑化效率,能以少的增塑剂获得最合理的塑化加工条件和最佳的柔软制品.
3.在PVC制品中有良好的耐久性和保留性,包括低的挥发性、对油剂、有机溶剂的水等的抽出性、对性质相似固体物质(例PS&ABS等)的低的迁移性。
4. 耐热性好在加工温度和使用温度在较高的温度下保持稳定.
5.能满足确定用途所需要提供的特效性,如电绝缘性、阻燃性、难燃性和耐寒性等。
6.良好的耐候性和环境作用的稳定性,包括热稳定性、耐霉菌性和对辐射的化学稳定性等。
7.无味、无嗅、无色、无毒和无污染性。
8.容易获得,价格低廉.
除以上因素外,由于使用环境、使用条件以及价格因素等方面的差异,在选用增塑剂时还应考虑其对环境适应性、使用功能性、卫生与安全性,以及经济合理性等方面的要求.在环境与气候因素方面,通常应考虑增塑剂的耐寒性和耐候性,如与PVC混合后的脆化温度(脆点)、光热稳定性、防霉性等;在使用功能因素方面,对特定要求的增塑制品,应考虑增塑剂的电绝缘性、抗电弧性和阻燃性等;对于医疗品及或食品级的制品,应考虑增塑剂的毒性及相关的卫生标准.
电线被覆用PVC配合物可分为绝缘用与保护被覆用。绝缘用者以电气特性最为重要﹐另外机械性能及耐劣化性能亦应列入考虑﹐保护用被覆以机械特性为主﹐对各种劣化之抵抗及某种程度之电气特性仍为必要。任何情况下﹐电气特性受树脂﹑安定剂﹑填充剂等左右﹐增塑剂之量及种类也有很大的影响。一般以邻苯二甲酸酯系为主﹐与其它增塑剂配合使用。现日本及欧洲的一些公司要求电线用PVC无邻苯二甲酸酯系增塑剂,则可以TOTM为主增塑剂,其它增塑剂为辅增塑剂.
热稳定剂(Stabilizer)
聚氯乙烯(PVC)具有优良的耐腐蚀性﹑难燃性和高力学性能﹐但是由于PVC结构中含有双键﹑支化点﹑和引发剂残基等﹐加热到100oC即伴随着脱氯化氢反应降解﹐在加工温度(170oC或者更高)下﹐降解反应加快﹐迅速发生了大分子交联。故在PVC配方中引入稳定剂﹐稳定又叫安定剂﹐广义上讲﹐凡以改善聚合物的热稳定性为目的而添加的物质﹐都可称为热稳定剂。本章所讲的是传统意义上的热稳定剂﹐它是PVC加工必不可少的稳定化助剂﹐能够防止PVC在加工过程中由于热和机械剪切作用所引起的降解﹐同时使制品在加工过程中和贮存使用过程中有良好的持久耐候性。
第一节热稳定剂的分类和性能要求
理想的热稳定剂应该具备如下基本使用条件(稳定剂的选用原则)﹕
(1)热稳定效能高﹐并具有良好之光稳定性。
(2)与PVC兼容性好﹐挥好性好﹐不升化﹐不迁移﹐不喷霜﹐不容易被水﹑油及其它溶剂抽出。
(3)有适当的润滑性﹐在押出过程中没有压析现象发生﹐不结垢。
(4)不与其它助剂反应﹐不被硫与铜等物质污染。
(5)不降低制品的电性能及印刷性等二次加工性能。
(6)无毒﹑无异常气味﹑不污染﹐可以制得透明制品。
(7)加工使用方便﹐价格低。
实际上能完全符合上述条件的单品稳定剂是不存在的﹐因之依需要目的组合及选择稳定剂是非常必要的。用于PVC的热稳定剂品种繁多﹐分类方法不一﹐但一般采用化学组成分类。主要包括铅盐类﹑金属皂类﹑有机锡类﹑有机锑类﹑稀土类等金属化合物及有机辅助稳定剂。
第二节聚氯乙烯的降解与稳定
一﹑PVC的降解现象
从1﹐3﹐5-三氯已烷具有很高的热稳定性来看﹐基本结构与之相似的PVC也应当是十分稳定的。但事实并非如此﹐PVC远不及为种简单的氯化物稳定。PVC加热至100oC时﹐即伴随着脱HCL反应﹐在100—200oC加工时,PVC发生了剧烈降解,除了脱HCL以外,还会发生大分子交联,致使产品变黑,物理性能恶化.PVC的降解伴随着脱HCL而产生的双键﹐使其碳原子上的氯原子即烯丙基氯原子活化而引起HCL分子的脱出。氧气存在在使PVC降解加快。
二﹑PVC的热降解机理和影响PVC热降解的因素
在PVC行业中人们普遍认可的降解理论主要有自由基机理﹑离子机理和单分子机理。其中自由基机理最为流行。影响PVC热降解的因素一般认为共有八个﹐即结构的影响﹑氧的影响﹑HCL的影响﹑金属氯化物的影响﹑溶剂的影响﹑增塑剂的影响﹑临界尺寸的影响用一些不可预见的因素。
三﹑热降解的抑制
要想有效地防止PVC的降解﹐必须控制在某一期间作用在聚合物体系上的降解力的降解历程。稳定剂的目的就是通过降解力和降解历程的控制﹐实现对PVC颜色﹑流变性能﹑机械性能﹑电性能﹑耐化学性能﹑热性能﹑光学性能等综合控制。在实际生产中﹐PVC稳定性的实现主要依据两个途径﹐一是生产过程中严格控制﹐使所得产品本身具有尽可能高的稳定性﹐这种方法一般称作预防性稳定技朮。另一种方法是树脂生产完毕﹐在加工之前或者加工的过程中配合一种或者多种物质﹐对已经开始的降解进行抑制﹐这种方法一般称为终止降解性的稳定技朮﹐这种方法的思路也正是热稳定剂的作用所在。
四﹑热稳定剂的作用机理
1.铅盐
此稳定剂大多是含 盐基(PbO)的铅盐。由于PbO具有极强的中和HCL的能力﹐因此主要作用是中和PVC降解生成的HCL.
3 PbO. PbSO4.H2O+6HCL→3PbCL2+ PbSO4+.H2O
PbO+2HCL→PbCL2+.H2O
2.金属皂
(1)与HCL的反应与HCL的反应是热稳定剂的基本反应,羟酸金属皂中的金属一般为二价,所以有两步反应:
Me(COOR)2+HCL→Me(CL)(COOR)+HCOOR
Me(CL)(COOR)+ HCL→MeCL2+ HCOOR
由于锌有高共价的倾向﹐并含有未共享的电子对﹐另外在聚合物中烯丙基比链上其它地方的仲氯具有更高的反应活性﹐使得烯丙基与不稳定的锌中间物结合在一起。对于镉皂来说﹐也是按类似反应进行的﹐故锌皂和镉皂有较好的初期稳定性﹐初着色比较好。对于钡和钙﹐几乎不能与聚合物链上的氯原子形成共价键﹐而是由于配位数的变化产生不稳定的二聚体。它可通过其它途径﹐使钙的原来配位数得到再生。故钡皂和钙皂具有优良的长期稳定性。
(2)金属皂的色彩稳定机理锌皂与镉皂的复合物能与PVC本色补色,而钙皂与钡皂则起不到这种作用.因为颜色的关系,Ca/Zn复合稳定剂中﹐锌皂与钙皂如配合不适当﹐如引起PVC变色。
3.有机锡
(1)与氯化氢反应不论是羟酸有机锡还是硫醇有机锡都可以和PVC降解产生的HCL反应。
(2)与不稳定的氯原子反应烷基锡能与不稳定氯原子发生反应﹐这样就限制了脱HCL作用的引发区,防止大共轭结构的形成.硫醇有机锡也能置换PVC中不稳定的氯原子.
(3)共轭双键的加成马来酸锡容易与PVC分子中的共轭双键发生“双烯加成”反应﹐结果使共轭双键被双键固定而抑制了共轭链的增长。硫醇有机锡与HCL反应生成的硫醇﹐也能与共轭双键进行加成反应。
(4)有机锡具有捕获自由基的能力﹐当它与大分子自由基反应之后﹐使自由基终止﹐而其本身也成为较稳定的自由基。
(5)分解氢过氧化物含硫有机锡具有抗氧化作用﹐能分解氢过氧化物﹐防止氢过氧化物热解产生新的自由基﹐降低体系中自由基的浓度而起稳定作用。
4.稀土稳定剂
稀土稳定剂具有形成配位络合物的能力﹐在PVC加工中放出HCL时,可大量吸收HCL,能使PVC大分子中的CL-,特别是不稳定的烯丙基氯﹑叔氯原子趋于稳定﹐从而起到对PVC的稳定作用。
5.环氧化合物
环氧化合物可直接与在PVC加工中放出HCL反应﹐并能吸收不稳定的烯丙基氯﹐而且能与双键发生加成反应。
6.多元醇
在锌﹑钙﹑镉等皂中并用多元醇﹐可明显降低脱HCL速度。这是由于多元醇的羟基能够与CdCl2﹑ZnCl2等形成络合物﹐降低了CdCl2﹑ZnCl2的脱HCL的催化作用所致。
7.β-二酮
在ZnCl2存在在﹐β-二酮化合物可以通过碳烷基化置换PVC中烯丙基氯,使共轭多烯烃中断变短.
五﹑热稳定剂的协同机理
1.金属皂的协同作用
根据金属皂在阻止PVC降解中的活性机理,可将金属皂分为两类:一类仅能吸收HCL,防止其对脱HCL反应的催化作用,最具有代表的例子是钡皂和钙皂.这类金属热稳定性一般,初期稳定性不好,但长期受热,PVC稳定变化不大.其稳定化过程中生成的金属氯化物对脱HCL基本无催化作用.另一类不仅能吸收HCL,还能够与烯丙基氯反应从而使PVC稳定,最具有代表的例子是锌皂和镉皂.这类金属皂初期着色性很好,但长期受热,制品急剧变色.尤其是锌皂,极容易出现急剧化,产生所谓的“锌烧”现象。这是因为锌皂和镉皂在稳定化过程中生成的氯化物CdCl2﹑ZnCl2是极强的lewis酸﹐系脱HCL反应的催化剂。基于上述特点﹐单独使用任何一类金属皂﹐都很难达到满意的效果。若将活性高的镉﹑锌皂与活性差的钡﹑钙并用﹐则可以使初期着色性和长期稳定性都得以改善。例如﹐钡撕毁与镉皂并用时﹐镉皂首先与PVC分子中的烯丙基氯发生酯化反应﹐生成的CdCl2与钡皂发生复分解反应﹐使镉得以再生﹐并使CdCl2无害化。钙﹑锌皂之间﹐钡﹑锌皂之间都基于相同原理。
2.亚磷酸酯与金属皂的协同作用
亚磷酸酯与金属皂并用时﹐可以与金属氯化物反应而抑制其对脱HCL的催化作用﹐从而提高体系的热稳定效能。
3.多无醇与金属皂的协同效应
.多无醇与金属皂并同可以明显延长脱HCL的透导期,并能抑制树脂变色。一般认为﹐多元醇是通过与金属氯化物的络合﹐抑制其对脱HCL的催化作用而发挥协同效应的。
4. β-二酮化合物与金属皂的协同效应
β-二酮化合物能够通过碳烷基作用与PVC发生反应﹐从而使其稳定﹐但反应速度缓慢。若与钙/锌等体系并用﹐则可以大大提高稳定化反应的速度。金属锌皂的离子化势能较高﹐与烯丙基氯反应﹐使PVC酯化而稳定。而作为其副产物的ZnCl2是脱HCL的催化剂﹐它的存在是有害的。但是ZnCl2同样是碳烷基化的催化剂﹐β-二酮化合物加入﹐正好利用ZnCl2的这种催化作用﹐使得烯丙基氯的碳烷基化反应得以迅速进行。β-二酮化合物与钡/锌的协同作用与此类似。
5.稀土稳定剂与锌皂的协同效应
稀土稳定剂本身具有置换烯丙基氯的效果﹐但单独使用时PVC制品呈现黄色着色。配合使用锌皂后﹐锌皂稳定化过程产生的ZnCl2与稀土离子的交换反应﹐生成危害较小的ReCl3。另外稀土优先与HCL反应生成稀土氯化的羟酸﹐降低了ZnCl2对脱HCL的催化作用。两组分配合使用﹐得到了较好的初期着色﹐也使长期稳定性大大提高。
第三节热稳定剂的性能
热稳定剂最基本的性能是耐热性﹑耐候性和加工性。另外﹐从PVC制品使用的观点来看﹐还必须考虑热稳定剂的透明性﹑兼容性﹑机械性能﹑电绝缘性﹑耐硫化性﹑毒性等。随着热稳定剂行业的发展﹐复合型稳定剂使用增多﹐同时热稳定剂总是与其它许多助剂﹐如增塑剂﹐加工改性剂等相伴存在﹐在这种情况下就要考虑其它助剂对热稳定剂性能影响等问题。因此掌握各类热稳定剂的基本性能﹐合理选择和使用最适宜的热稳定剂﹐最大限度地发挥其有用的性能﹐避免消极影响﹐对于PVC设计是非常重要的.
一﹑耐热性
热稳定剂的主要作用就是改善其耐热性﹐这也是PVC加工使用热稳定剂的根本原因。
1. 耐热性的概念
(1)能改善PVC制品初期着色的性能﹐称为热稳定剂的初期耐热性。能够使PVC制品长时间在高温下保持原来的颜色﹐称为热稳定剂的长期耐热性。长期耐热性和初期耐热性之间没有必然的联系﹐有的热稳定剂初期耐热性一般﹐而长期耐热性较好﹐那么这类热稳定剂属于持效性。有的热稳定剂长期耐热性一般﹐而初期耐热性优异﹐那么这类热稳定剂属于短效性。
(2)静态耐热性和动态耐热性静态耐热性是指样品在静态条件下受热处理期间的耐热性﹐所反应的是单纯化学反应的耐热性。PVC的浇注熔融成型和模塑制品的加工过程中就有类似的反应。动态耐热性是指样品受到机械剪切力﹑压力﹑和热的作用下的耐热性﹐所反应的不仅仅有化学反应的耐热性﹐而且包括加工的动态耐热性。
2.各类热稳定剂的热稳定性
从动态耐热性的角度来讲﹐金属皂性能良好﹐但其中也有差的﹐所以经常需要配合使用。铅盐类动态和动态耐热性差别不大﹐必须与润滑剂并用。从静态耐热性和动态耐热性的角度考虑﹐各类稳定剂都有其各自的特点。金属皂的稳定性随金属的种类不同而异﹐碱金属和碱土金属皂等属于长期型﹐初期稳定性不好。如铝﹑钙﹑镁﹑钡等。而锌和镉属于初期性﹐长期稳定性不好。铅皂介于二者之间。金属皂的有机酸根对初期型和长期型无影响。
铅盐有初期着色现象﹐属于长期型。其酸根对耐热性产生较大影响﹐在常用的铅盐产品中﹐亚硫酸盐性能最好﹐硫酸盐次之﹐亚磷酸盐最次。盐基性亚硫酸铅在铅盐中耐热性最好。在有机锡化合物中﹐月桂酸酯类初期耐热性较差﹐长期耐热性良好﹔马来酸酯类初期着色性和长期耐热性都很好。硫醇酯没有初期着色性﹐而长期耐热性良好。锑类稳定剂初期着色性和长期耐热性均佳﹐性能和有机锡相似﹐但仍然无法与有机锡相比。与硬脂酸钙﹑环氧化合物﹑亚磷酸酯有很好的协同效应。稀土类稳定剂初期耐热性和长期耐热性均可以﹐各种单一稀土类稳定剂之间性能差别不大﹐而混合稀土类性能不如单一品种。环氧化合物﹑多元醇﹑亚磷酸酯是常用的长期型稳定剂。而β-二酮化合物属于短效型﹐对改善长期稳定性也且定的效果﹐多做辅助稳定剂。
3. 热稳定剂之间的协同作用
热稳定性是热稳定剂的最基本性能。一种好的热稳定剂﹐不但要有优良静态耐热性﹐还要有优良的动态耐热性﹔不但要有优良的初期稳定性﹐还要有优良的长期稳定性﹔不但要经得起加工时高温的考验﹐还要经得起塑料长时间使用的考验。所以需要将不同物性的热稳定剂进行复配﹐利用组分间的协同效应﹐满足不同的要求。
(1)金属皂之间的协同作用碱金属和碱土金属皂等属于长期型﹐锌和镉属于初期性﹐这些化合物并用不仅能得到良好的耐热性﹐而且能得到良好的耐候性和加工性。
(2)金属皂和β-二酮化合物的协同作用β-二酮化合物的存在﹐能够极大限度的改善初期着色﹐对于某些结构的β-二酮化合物﹐在降解初期的30分钟内几乎检不出氯离子。
二﹑加工性
热稳定剂对配制好的PVC物料加工性的影响﹐取决于热稳定剂的添加量和热稳定剂体系的具体的化学性质。
(1)金属皂在金属皂中﹐铅﹑镉﹑锌皂润滑性好﹐抗混炼扭矩值低﹐凝胶化缓慢﹔镁﹑钙﹑锶﹑钡皂凝胶化性能好﹐抗混炼扭矩值高。锌皂延迟凝胶化。对于相同的金属皂类﹐有机酸根不同﹐加工性也不同。脂肪族羟酸皂模拟芳香族皂类润滑性要好。在脂肪酸根中﹐随着分子链的增长﹐润滑性也相应就也。
(2)铅盐类铅盐类相对密度大且易凝集﹐在混料时难于分散均匀﹐加工性较差﹐需要金属皂和润滑并用。
(3) 有机锑有机锑稳定剂润滑性较差﹐通常需要配用大量的润滑剂。
三﹑透明性
1.各类稳定剂的透明性
一般来说﹐有机锡稳定剂透明性最好﹐主要用于透明制品中。其中马来酸锡和硫醇锡是透明性最好的热稳定剂。稀土稳定剂折射率与PVC树脂非常相近﹐因此也具有较好的透明性。在软质透明制品中多使用钡/镉/锌液体复合稳定剂为主﹐要求耐硫污染时多用钡锌稳定剂﹐要求无毒时多用钙/锌金属皂。铅盐类不透明﹐不能用于透明制品中。稳定剂本身的透明性固然重要﹐但稳定剂的兼容性﹑挥发性﹑加工性以及加工操作同样会影响PVC制品的透明性。例如如果在押出的过程中温度过低﹐就会在制品表面出现雾状现象。
2.不透明现象及消除
(1)白化现象透明PVC制品经弯曲﹑拉伸或水浸﹑户外曝晒会使表面呈现白色浑浊状﹐这种现象称为白化。白化现象可能是由于外力作用使得PVC的密度及分子结构发生了变化﹐或是由于水的作用﹑出汗﹑喷霜而产生的表面现象﹐或者由于光降解而引起的着色以及灰尘的吸咐等多种复杂因素促进的。
1.应力白化应力白化是PVC制品在受机械外力作用下的白化现象﹐这是由于PVC分子链沿着张力应力方向取向﹐密度变化﹐同时分子间出现空隙﹐形成光散射而呈现出白色。使用铅盐作稳定剂应力白化特别严重。使用有机锡稳定剂可以减少白化。这是因为添加高表面能的稳定剂﹐弥补由分子链取向而产生的空隙﹐可以有效的减少白化现象
2.水浸白化将透明PVC制品在水中浸渍一段时间﹐会出现白浊不透明现象﹔而且这种现象是可逆的﹐当彻底干透之后这种浑浊的制品会重新恢复到原来的透明度。这种现象是由于存在容易起水合反应的稳定剂或者稳定剂分解物易起水合作用而造成的。而也有人认为这种现象是由于水的浸渍﹐使稳定剂﹑增塑剂等从PVC中析出造成的﹐水浸白化现象与稳定剂的兼容性及水抽提性有关﹐因此兼容性好﹑水溶性差的的稳定剂对于防止水浸白化应该是有利的。实际使用中发现﹐几乎所有的碱土金属皂的配方﹐特别是钡和钙﹐比较容易出现水浸白化现象﹐含有镉皂和锌皂的配方只会偶尔出现这种现象。有机锡就不会出现水浸白化现象。
3.曝晒白化将PVC制品放置在空气中﹐由于大气中的水分﹑二氧化碳﹑二氧化硫和光的作用﹐也会出现白化现象。这与稳定剂的兼容性有关。兼容性好的稳定剂几乎不会出现这种现象﹐而兼容性差的稳定剂如铅盐则极易出现曝晒白化现象。
(2)鱼眼﹑气泡把透明或半透明的PVC薄片对着光线观察时﹐就会发现在薄片中夹杂着透明或半透明的类似鱼眼的小圆颗粒﹐这就是“鱼眼”。有时在透明薄片中也存在气泡。鱼眼和气泡都会影响制品的透明性。一般鱼眼产生的原因大都在树脂本身﹐但如果稳定剂混料不均匀﹐也会产生鱼眼。气泡产生则是由于助剂的挥发分或者是加工性不平衡造成的。可见分散性好﹑挥发性小的稳定剂对于减少鱼眼和气泡是有利的。
四﹑耐候性
在室外长期外用的PVC制品不仅会受日光的作用而引起老化﹐而且会受到风雪雨露﹑昼夜更替﹑季节变化﹑大气污染的影响。通常将这些自然因素综合起来所造成的老化现象称为天候老化。将抵抗天候老化的性质称为耐候性。
1.各类稳定剂的耐候性
铅盐类稳定剂耐候性一般﹐其中亚磷酸盐耐候性最好﹐亚硫酸盐次之﹐硫酸盐最差。金属皂中﹐镉皂耐候性优良﹐锌皂﹑铅皂﹑钡皂次之﹐钙皂耐候性较差。在复合金属皂中﹐钡皂/镉皂﹑钡皂/镉皂/锌皂耐候性优良﹐钙皂/锌皂较差。有机锡稳定剂中﹐马来酸盐耐候性最好﹐月桂酸盐次之﹐硫酸盐较差。有机锑稳定剂耐候性极差﹐本身要求贮存于不透明的容器内。稀土稳定剂具有抗光老化作用﹐其耐候性能优于铅系稳定剂﹐与有机锡性能相当。
不同类型的稳定剂相互作用﹐由于协同作用﹐可大大改善耐候性。紫外线屏蔽剂和紫外线吸收剂能防止由于紫外线所引起降解﹐与其它热稳定剂体系并用能大大提高配合物的耐候性。在软质PVC透明制品中,钡/镉/环氧化合物/亚磷酸酯组合有最优良的耐候性。在此组合中亚磷酸酯对钡/镉体系的耐候性有特别显著的改善﹐而环氧化合物则主要改善其热稳定性。在软质不透明的制品中﹐亚磷酸或亚硫酸的盐基性铅盐具有良好的耐候性﹐如果在三盐基硫酸铅中添加亚磷酸酯或者镉皂﹐可使其耐候性提高到二盐基亚磷酯铅相同的程度。如果使用钡/镉/环氧化合物/亚磷酸酯稳定体系﹐并辅以紫外线屏蔽剂钛白粉时﹐其耐候性要比二盐基亚磷酯铅还好。在不透明制品中﹐盐基性铅盐具有良好的耐候性。由于铅稳定剂和钛白粉并用时在光的作用下容易变黑﹐所以最好不要采用此组合。铅稳定剂老化时还会出现白化现象﹐与锐钛性钛白粉并用时更为明显。
2.耐候性的测试方法
耐候性的测试方法有自然户外大氯试验﹐加速户外大气老化试验﹑实验室加速老化试验。
五﹑相从性
1.不兼容现象
稳定剂在PVC配合物中容易分散,做成制品后经长期使用也不析出,说明稳定剂具有良好的兼容性,这是人们所希望的.但是并不是所有稳定剂都能够与配合物完全兼容,在这种情况下,稳定剂会从制品内部向表面移动,最后从制品析出.如果析出物是粉状的固体物质时,习惯上叫做喷霜;如果析出的是液体物质,就是所谓的渗出(也叫出汗).喷霜和渗出都属于不兼容的现象,它的出现都会影响制品的表面性质的电性能.
PVC的兼容性程度取决于许多不同的﹑独立的因素﹐这些因素包括稳定剂配方中每种成分各自的兼容性﹐这些成分中每种成分在整个PVC配方中的含量﹐以及构成整个PVC配方组成物的性质﹐另外还包括不同组分之间在加工过程中发生的化学反应。喷霜和渗出常常一种潜伏现象﹐有些时候在配料的加工过程中就可看到﹐而有的要过好久才能看到。
2.各类稳定剂的兼容性
一般来讲﹐铅盐稳定剂兼容性差﹐但三盐基硫酸铅对喷霜无增加或者减轻的倾向。
在金属皂中﹐从属的种类和有机酸的种类都对喷霜有影响。象钡﹑钙等电负性小(化合价低)的金属喷霜就少﹐而铅皂和铝皂则较易产生喷霜﹐但金属皂的喷霜小于相应的酸。从有机酸来看﹐芳香酸比脂肪酸喷霜少﹐脂肪酸中碳链越长﹐喷霜也越厉害。硬脂酸皂极易喷霜﹐月桂酸次之﹐辛酸皂再次﹐丁基苯甲酸皂较少产生喷霜。有机锡稳定剂有极好的兼容性﹐因此一般不会出现象许多铅盐稳定剂﹑钡/镉﹑钡/锌﹑钙/锌稳定体系所常见的喷霜和渗出现象。尤其以硫醇系有机锡性能最好﹐月桂酸有机锡次之﹐马来酸有机锡也容易产生喷霜。亚磷酸酯﹑磷酸酯有增加喷霜的倾向﹐环氧化合物﹑碳酸钙对兼容性没有影响。
产生渗出的制品表面﹐除了感觉油滑或发黏之外﹐常常有一种难闻的气味。渗出物还会使制品的机械强度﹑伸长率﹑耐化学性﹑电绝缘性﹑光学性能﹑耐候性大大受损。为了防止喷霜﹐在使用容易喷霜的热稳定剂时﹐配用少量的喷霜抑制剂是有效的。
六﹑压析性
1.压析及压析性
在塑料加工过程中﹐配合剂组分如颜料﹑润滑剂﹑稳定剂或增塑剂﹐从配合物析出而黏附在压辊﹑塑模等金属表面上﹐逐渐形成有害膜层的现象称“压析”。有时也称为“积垢”或“表面附层”。配和剂组分加工时产生压析的性质称为压析性。
压析现象常常发生在压延后的冷辊和后压花辊上,但有时也出现在混炼机或者压延机上.在押出加工时压析也出现在螺杆﹑机筒壁﹑口模内壁以及押出机以后的牵引装置上﹐积垢会给成型操作带来许多麻烦﹐积垢严重时会造成配合后从螺杆上剥离困难﹐同时使制品表面污染。一般认为原材料的不兼容性是造成压析现象的部分原因﹐但这绝不是唯一的原因。不过在任一类型的成型加工中﹐各种原材料的变化﹐如树脂﹑增塑剂﹑填料﹑润滑剂和稳定剂以及加工条件的变化都会影响到压析的严重程度。通过改变上述条件﹐很可能使以前没有压析的配方或工艺出现压析﹐同样改变上述条件﹐也可能使原来严重的压析现象减轻以致完全消除。
2.各类稳定剂的压析性
各类稳定剂的压析性差别很大﹐一般来说﹐金属皂对压析影响很大﹐而无机铅盐和有机锡稳定剂不会产生压析。稀土稳定剂用量较大时也会出现压析现象﹐物料的离辊性不理想﹐个别配方产生轻微的黏附。在金属皂类中﹐锶﹑镁﹑钙﹑钡﹑镉皂较易产生压析﹐而锌﹑锡相对不易产生压析。另外有机酸根对金属皂的压析性有一定的影响。就同一金属皂来讲芳香酸皂的压析小﹐而脂肪酸皂的压析性大﹐同时随着脂肪酸根碳链的增长﹐相应的压析现象也就更为严重。压析性与稳定剂的用量有关。在一定范围内﹐随着稳定剂用量的增加﹐压析也相应增加﹐但当稳定剂用量超过某一定值时﹐压析却不再继续增加。一般来讲﹐在实际加工中﹐加工温度越高﹐加工时间越长﹐则压析现象越严重。
3.压析的防止
尽管影响压析的因素非常复杂﹐但是在长期的加工实践中﹐人们也总结一些基本规律的一套防止压析的具体措施﹐以最大限度的减轻压析。
(1)压析通常只出现在同时含有一种碱土金属盐和一种重金属盐的PVC配方中﹐碱土金属可能来自于填料﹑稳定剂或者润滑剂(硬脂酸钙)﹐而重金属可能来自颜料(钛﹑锰﹑铅)﹑稳定剂(镉﹑锌﹑铅)或者来自其它方面。
(2)积垢的形成速度取决于PVC制品的生产速度﹑配方中的金属的百分比以及所加入金属的化学形态。
(3)调节碱土金属稳定剂的浓度是控制压析产生的有效方法。在符合稳定作用需要的前提下﹐应把用量降低到最低限度。用碱金属盐部分或者全部取代碱土金属有利于减轻压析。
(4)稳定剂的并用可以减轻压析。硬脂酸钡﹑硬脂酸钙等压析性大﹐如果与硬脂酸锌﹑硬脂酸镉等并用则可有效在减少压析。除硬脂酸锌﹑硬脂酸镉外﹐也可用硬脂酸铅﹑硬脂酸铝等。
(5)加入某些压析防止剂可以防止压析现象。加入阳离子或阴离子表面活性剂﹐常常有助于降低或消除压析﹔加入硬脂酸或硬脂酸锌为基础的稳定剂﹐尤其是配制成液体的锌稳定剂则可有效的减少压析﹔加入氧化铝﹑硅胶﹑亚磷酸三苯酯等都有抑制压析的作用。
(6)有机锡稳定剂﹐不管用在那一种配方中﹐也不管那一种加工方法﹐都 不会引起压析。
(7)辊或螺杆的表面状态与压析有微妙的关系﹐因此应使辊面保持光洁﹐注意防止各种异物﹑腐蚀性物质等损伤辊或螺杆表面。在更换配方时要把加工设备清洗干净。
(8)压析程度与空气中的水分有关﹐水分多时易造成压析现象。
七﹑电性能
1.电绝缘性和抗静电性
在进行电线电缆等绝缘材料的配方设计时﹐要求物料不能含有离子型材料。物料中稳定剂不单要求能够防止PVC降解造成的颜色变黑﹐而且要确保稳定化过程中为非离子型产物。不具备这种作用的稳定剂﹐不能使用于有电性能要求的制品。稳定化过程中生成非离子型化合物﹐因而不导电的性能﹐通常称为稳定剂的电绝缘性。与上述情况相反﹐在制造地板﹑地毯等制品时﹐为了防止制品事静电﹐往往要求使用的稳定剂在稳定化过程中生成可导电的金属氯化物﹐以防止静电积累﹐这种情况称为稳定剂具有抗静电性。
2.电性能的评价
用作电气绝缘材料的一些配方﹐必须考虑到材料的电性能﹐包括体积电阻率﹑介电强度﹑介电常数和功率因子等。
3.各类稳定剂的电性能
一般的无机盐﹑金属皂类电绝缘性好﹐适用于电线外被和绝缘配方。有机锡﹐液体钡/镉复合稳定剂的电绝缘性低﹐可以用在防止静电的配方中。
八﹑毒性
(1)铅盐铅盐的毒性很强﹐属于剧毒稳定剂。长期接触者应该注意以下几点﹕1.使用有效的防尘口罩。2.用3%的硫代硫酸钠或者0.5%的食盐水与薄荷醇的稀溶液漱口。3.进行彻底的沐浴。4.服用维生素害药物。
(2)镉皂镉皂一种毒性很强的环境污染物质﹐每人每日摄镉超过300μg就会有骨痛病的危险。
(3)钡皂钡的毒性很强﹐不能使用于无毒配方中。
第四节热稳定剂各论
一﹑有机锡稳定剂
1. 有机锡稳定剂的结构与分类
有机锡稳定剂一般可用以下结构表示﹕XnSnY(4-n)(n=1---3)
其中﹐X基团可以是烷基﹐如甲基﹑丁基﹑辛基﹐也可以是酯基。根据X基团的不同﹐有机锡稳定剂可分为烷基锡和酯基锡﹐烷基锡又可根据烷基的不同分为甲基锡﹑丁基锡﹑辛基锡等。Y可以是脂肪酸根﹐如马来酸根﹑月桂酸根﹑也可以是硫醇根。根据Y基团的不同﹐有机锡稳定剂可分为有机锡马来酸盐﹑有机锡月桂酸盐﹑有机锡硫醇盐等。
2. 有机锡稳定剂的性能及应用
有机锡稳定剂最大的优点是具有优良的透明性﹐使用有机锡稳定剂的PVC配方﹐可得到结晶般的制品。有机锡稳定剂具有超凡的热稳定性﹐目前没有任何其它类型的热稳定剂能超过它。在押出过程中﹐加工温度可达到200---230oC.大多数有机锡稳定剂是无毒的﹐加之有机锡稳定剂在PVC中迁移极微﹐因此有机锡稳定剂是PVC加工首选热稳定剂。
有机锡稳定剂与PVC有极好的兼容性﹐一般不会出现像铅盐稳定剂﹑金属皂稳定剂体系所常见的在金属表面析出用压析等现象。有机锡稳定剂不会提高液体状PVC的黏度﹐也不会对液体体系的表面特性或对熔融的PVC制品表面产生不利影响。含硫的有机锡稳定剂自润滑性较差﹐要使制品的透明性好﹐就得提高加工温度。但总的来说﹐有机锡稳定剂同其它任何类型稳定剂来比﹐其综合性能更接近于理想中的稳定剂。但所有的有机锡稳定剂﹐主要缺点是成本高。
二﹑铅盐稳定剂
1.概况
铅盐稳定剂是最古老的稳定剂之一。铅盐稳定剂一般都具有很强的结合氯化氢的能力﹐对于PVC脱HCL无抑制作用,也无促进作用.氧化铅与氯化氢的结合能力很强﹐如果作为稳定使用﹐会造成制品着色﹐所以人们就开发了一系列带“盐基”(PbO)的白色铅盐﹐稳定剂行业所说的铅盐就是指的这一类结合有机盐的无机或有机酸铅盐。其中无机酸包括硫酸﹑亚磷酸﹑亚硫酸等﹐而有机酸包括邻苯二甲酸﹑硬脂酸﹑水杨酸﹑马来酸等。铅盐稳定剂最大的特点是耐热性和电绝缘性好﹐成本低﹐最大的缺点就是毒性高和透明性差。三盐基性硫酸铅的分子式为3PbO.PbSO4.H2O.
2. 铅盐稳定剂的性能及应用
铅盐稳定剂的优点是耐热性优良﹐特别是长期热稳定性良好﹔电气绝缘性优良﹔具有白色颜料的性能﹐覆盖力大﹐因此耐候性也良好﹔可做发泡剂的活性剂﹔价格低。但其缺点是相对密度大且易凝集﹐因而配料中难以分散均匀﹔毒性大且有初期着色性﹐给配色带来困难﹐故难得到鲜明色彩﹔缺乏润滑性和透明性﹔容易产生硫化污染。
(1)耐热性好在盐基性铅盐中﹐起稳定作用的仅仅是盐基﹐能够发生反应的盐基的质量分数(%)称为“有效铅含量”。有效铅含量高者﹐耐热性高。三盐基性硫酸铅的有效铅含量较高﹐故比其它产品表现出更为出色的耐热性。
(2)电绝缘性优异由于铅盐是非离子的﹐且不导电﹐因而是惰性的。这就是铅盐类稳定剂有优异的电绝缘性﹐在电线﹑电缆行业有很大用途的原因。
(3)耐候性优异﹑透明性差﹐这是相关联的问题。根据铅盐的具体结构﹐有些能起白色颜料的作用﹐而透明性好的也只能达到浑浊或者乳白色的半透明﹐都表现出强烈的覆盖力﹐因此具有较强的耐候性。
(4)分散性差及毒性 这是铅盐的主要缺点。
(5)大多数铅类稳定剂是不可溶的﹐不能从PVC中萃取出来﹐故铅不存在诸如稳定剂挥发等问题。铅盐的光稳定性极好。
三﹑金属皂稳定剂
1.概况
金属皂稳定剂是稳定剂中的一大类﹐它是高级脂肪酸金属盐总称。
2.金属皂的性能特点及应用
(1)镉皂稳定剂镉皂是金属皂中性能最好的一类。其优点主要体现在﹕1.良好的热稳定性﹔2.无初期着色﹐可制得无色透明产品﹔3.优良的光稳定性﹔4.有防止析出黏附的效果。镉皂中应用最广乏的是硬脂酸镉。
(2)锌皂稳定剂锌皂稳定剂对PVC的热稳定性极差﹐添加锌皂的样片﹐加热时急剧变黑﹐产生“锌烧”现象﹐因此锌锌皂稳定剂不能单独使用。因为它与镉皂具有相同的反应性﹐作为无毒产品与碱土金属皂和辅助稳定剂并用﹐可替代镉类稳定剂的配方。锌皂的主要优点有﹕1.初期着色性优良﹔2.防止积垢效果好﹔3.可提高耐候性﹔4.许多锌皂被认可为无毒稳定剂﹐与钙皂配合用于无毒配方﹔5.锌系稳定剂用于糊状树脂显示出理想的稳定效果。锌皂的代表产品为硬脂酸锌。
(3) 钡皂稳定剂钡类化合物热稳定性好﹐以金属皂和液态稳定剂的形态广泛应用。其代表性产品为硬脂酸钡。这类化合物加工时产生红色的初期着色﹐这容易引起压析现象﹐因此钡皂也不单独使用﹐经常与镉锌皂并用于软质制品配方中。钡皂最典型的应用是与镉皂配合使用﹐几乎是复合金属皂的典型代表。由于毒性较大﹐钡皂有一天也会走出人们的视野。钡皂稳定剂的优点主要为﹕1.良好的热稳定性﹔2.良好的润滑性。
(4)钙皂稳定剂钙皂稳定剂以硬脂酸钙为代表。这类稳定剂稳定性差﹐但无毒﹐具有良好的润滑性﹐与铅盐﹑锌皂﹑有机锡具有协同作用﹐应用前景十分广阔。钙皂稳定剂最典型的应用是与锌皂配合使用用于无毒配方﹐用于电线电缆方面有上乘表现。
(5)其它金属皂稳定剂硬脂酸铝﹑硬脂酸镁﹑硬脂酸钙﹑硬脂酸锌均为无毒稳定剂﹐都需要与其它稳定剂配合使用。
金属皂的性能与所含金属的种类有很大。一般情况下﹐镉皂﹑锌皂初期耐热性好﹔钡皂﹑钙皂﹑镁皂﹑锶皂长期稳定性好﹐铅皂处于中间。镉皂﹑锌皂﹑铅皂﹑钡皂﹑锡皂耐候性好﹔铅皂﹑镉皂的润滑性好﹔钡皂﹑钙皂﹑锶皂润滑性较差﹐但凝胶化性能好﹔钡皂﹑钙皂﹑镁皂﹑锶皂容易产生压析现象﹐而锌皂﹑镉皂则不容易出现压析﹔铅皂﹑镉皂毒性大﹐有硫化污染﹐钙皂﹑锌皂可用于无毒配方。
金属皂的羟酸部分也对其性能产生一定的影响。在相同情况下﹐一般酸根碳链增长﹐润滑性变好﹐兼容性降低﹐压析现象严重﹐喷霜也变得厉害﹔但被水的极性溶剂抽出减少。
3.复合金属皂稳定剂
加工行业对稳定剂的性能要求是多方面的﹐而单一的金属皂往往满足不了使用要求﹐因此复合金属皂稳定剂的使用已成为一种趋势。金属皂的复合使用﹐不是性能的简单相加﹐而是利用了组分之间的协同作用。复合金属皂稳定剂的组成一般是不公开的。但基本组成包括稳定剂主体(即金属皂)﹑溶剂(有机溶剂﹑增塑剂﹑液态非金属稳定剂)﹑功能助剂(辅助稳定剂﹑透明改良剂﹑光稳定剂﹑润滑剂等)。根据形态来分﹐目前使用的复合稳定剂主要有固体复合稳定剂和液体复合稳定剂。液体复合稳定剂具有以下优点﹕1.与PVC树脂﹑增塑剂兼容性好﹐凝胶化迅速﹑透明性优良﹔2.无飞散性﹐作业环境好﹔3.与亚磷酸酯﹑环氧化合物容易实现“一包装”﹔4.与有机溶剂兼容﹐黏度稳定性好。固体复合稳定剂具有以下优点﹕1.润滑性优良﹔2.不降低PVC的维卡温度。
(1)钡/镉复合稳定剂钡/镉复合稳定剂是性能优良的稳定剂。钡化合物和镉化合物并用﹐能产生协同效应。羟酸镉具有优异的初期着色性﹐但长期稳定性差﹐而钡化合物与之相反。两者并用能获得良好的长期稳定性。其优点为﹕1.无初期着色﹐热稳定性优良﹔2.无析出和喷霜﹔3.加工性优良﹔4.耐候性优良。
钡/镉复合稳定剂的成分除了金属皂外﹐还有多元醇﹑受阻酚抗氧剂﹐在许多配方中还含有液体亚磷酸酯和液体环氧增塑剂。这是因为镉盐在稳定化过程中生成氯化镉﹐该物质对脱HCL有极强的催化作用﹐亚磷酸酯﹑多元醇等物质的配合﹐可螯合或钝化有害的氯化镉。有时为了改善初期着色性和透明性﹐还配合有金属锌皂。以下是一个钡/镉/锌复合稳定剂配方的实例﹕
水解亚磷酸二苯二异辛酯8.6苯甲酸镉8.3
季戊四醇3.0脂肪酸锌4.4
双酚A2.8亚磷酸一苯二异辛酯57.4
脂肪酸钡15.5
(2)钡/锌复合稳定剂钡/锌复合稳定剂是为了取代镉盐而开发的稳定剂。以下是一个钡/锌复合稳定剂配方的实例﹕
烷基酚钡33.7水解亚磷酸三苯酯2.3
液体石蜡19.3双酚A0.8
高极脂肪醇19.3双亚磷酸酯19.4
苯甲酸锌4.3季戊四醇0.9
β-二酮化合物作为初期着色防止剂的使用﹐使钡/锌复合稳定剂性能更加完善。其主要优点是﹕1.耐候性优于钡/镉复合稳定剂﹔2.耐寒性得到改良﹐可减少磷酸酯类辅助增塑剂用量。钡/锌复合稳定剂光稳定性方面稍差﹐可通过配合使用环氧增塑剂和紫外线吸收剂来补偿。
(3)钙/锌复合稳定剂钙/锌复合稳定剂是为无毒应用领域而开发的稳定剂。以下是钙/锌复合稳定剂的配方实例﹕
硬酯酸钙25固体亚磷酸酯5
硬酯酸锌5β-二酮化合物3
钙/锌复合稳定剂的性能可以通过调节钙/锌比来实现。钙含量增加﹐长期稳定性变好﹐透明性增强﹔锌含量增加﹐初期着色减少﹐而长期稳定性降低。
四﹑有机锑稳定剂
有机锑稳定剂的优势在于﹕稳定性能好﹐成本较低﹐产品无毒﹔它的缺点是﹕透明性差﹐光稳定性差﹐润滑性差﹐与某些有产生交叉污染等。充分了解产品的特性﹐最大限度地发挥其优势﹐克服其缺点﹐对于稳定剂的合理选用是非常重要的。
五﹑有机辅助稳定剂
(1)亚磷酸酯亚磷酸酯是应用最广泛的有机辅助稳定剂,在液体钡/锌、钙/锌类稳定剂中是一种不可缺少的成分,在镉/钡/锌体系中作用更为明显。根据其结构特点,亚磷酸酯可分为亚磷酸单酯、亚磷酸二酯和亚磷酸三酯。一般亚磷酸单酯表现出优良的耐析出性的透明性,亚磷酸二酯和亚磷酸三酯则表现出优良的耐候性、热稳定性和着色性能。在硬质PVC中加入某些亚磷酸酯可以改善光稳定性,此外亚磷酸酯的加入可以降低熔体黏度,从而使PVC的加工比较容易进行。
在PVC制品配方中,亚磷酸酯的作用首先表现在置换烯丙基氯,在金属皂存在下,亚磷酸酯可与某些金属产生螯合或者与金属氯化物生成亚磷酸盐,从而抑制其在脱氯化氢中的催化作用.一般亚磷酸烷基芳基酯性能优于亚磷酸烷基酯.亚磷酸酯一般用于液体稳定体系,一般添加量为10%-30%(在稳定剂中的质量分数).
(2)环氧化合物环氧化合物也是无镉配合中不可缺少的并用助剂,具有改善热稳定性、耐候性和透明性的作用。环氧化合物的辅助稳定效果取决于稳定体系,一般说来对钙/锌和钡/锌稳定性影响最大,对钡/镉和铅盐也有一定影响,但对有机锡稳定性丝毫没有改进。液体的环氧化合物还起到增塑剂和滑剂的作用,因此在使用环氧化合物的软质PVC配方中,主增塑剂的用量可在一定程度上减少。环氧化合物还可以改善钡/锌、钙/锌体系的光稳定性。此外,环氧油酸酯黏较低,能赋予良好的低温柔顺性,环氧化油挥发性低,可改善耐抽出性。
环氧化合物的氯化氢反应生成氯乙醇,在钙、锌等金属皂催化下,取代PVC中不稳定的氯原子而发挥稳定作用。在静态实验中,环氧化合物的作用是抑制PVC的变黄,单独使用效果不佳,当环氧化合物与亚磷酸并用时,其效果可得到明显改善。
(3)多元醇多元醇可以螯合金属离子,防止氯化物催化降解,可以置换烯丙基氯,从而使PVC稳定.一般使用的多元醇易溶于水,
六、螯合剂
螯合剂几乎全是亚磷酸的烷基或芳基酯类,与金属盐成络合物。其性能具体表现如下:
1.阻止聚氯乙烯树脂催化降解。
2.阻止变色至最低程度.
3.阻止起霜
4.改善制品透明性.
5.因其本身是还原剂,故又能抗氧.但是耐热性不强.
6.使用螯合剂可以减少主稳定剂用量.
7.不能单独使用,必须与主稳定剂并用.一般用量为0.1%-0.5%(质量份)
螯合剂中用量最多的是亚磷酸三苯酯(C6H5O)3P,它是无色或微黄色透明油状液体,不溶于水.
七、主要安定剂分类列表
分类 | 安定剂名称(中/英) | 缩写 | 安定剂性能 |
盐 基 性 铅 盐 | 三盐基性硫酸铅 Triabsic Lead Sulfate | TS | 三盐的耐热性和电绝缘性优良,耐旋光性尚好,特别适用于高温成型的配方.三盐无润滑性,须与滑剂与金属皂并用,与硬脂酸铅并用,比例:TS/PbSt不能大于1/4,否则有析出现象,三盐对紫外线有保护作用. |
二盐基性亚硫酸铅 | DBL | 二盐具有突出的耐候性,有抗氧化和屏蔽紫外线的能力,热稳定性和绝缘性也较好,耐寒性较好,与三盐并用有相乘效果.二盐的耐热性不如三盐,但对硬脂酸铅好 | |
复 合 安 定 剂 | 镉钡锌稳定剂 Cadmium-Barium -Zinc Stabilizers | Cd-Ba-Zn | 复合安定剂与树脂及可塑剂的混合分散性好,透明性好,用量较少,不易析出,可避免粉尘中毒.是运用最广泛的安定剂.其中: Cd-Ba-Zn:光稳定性热稳定性透明性较好,是当今透明性最好的安定剂之一.硫化污染,低析出性较差,有毒. Ca-Zn: 光稳定性热稳定性透明性较好, 低析出性较差,无毒 Ba-Zn:光稳定性热稳定性透明性较好, 低析出性较好,低毒,有滑性 |
钙锌稳定剂 Cadmium--Zinc Stabilizers | Ca-Zn | ||
钡锌稳定剂 Barium -Zinc Stabilizers | Ba-Zn | ||
金 属 皂 盐 合 安 定 剂 | 硬脂酸铅 Lead Stearate | Pb-St | 有很好的润滑性和较好的光热稳定性,有毒,易受硫化污染,不能用于透明制品中. |
硬脂酸镉 Cadmium Stearate | Cd-St | 与铅系钡系皂盐并用作为PVC安定剂具有广泛效果,镉皂在透明性和改善耐候性方面具特别效果,单独使用时缺乏热安定性,热加工时使PVC配合物急遽产生黑化现象,与Ba皂并用,利用其相乘效果即有卓越之安定性能. | |
硬脂酸钡 Barium Stearate | Ba-St | 耐热优秀,但单独使用时会使制品呈现红色,因此要与其它安定剂并用,尤其与镉皂并用有相乘效果.Ba系稳定剂与Cd系和Zn系稳定剂并用时不但红色消失,且使Cd系和Zn系稳定剂的耐热性大大增强. | |
硬脂酸锌 Zinc Stearate | Zn-St | 无毒性,耐候性较好,但对PVC的降解有明显的催化加速作用,应严格控制用量,不宜单独使用. | |
硬脂酸钙 Calcium Stearate | Ca--St | 无毒性,不含硫化污染、滑性佳、胶化优良,与Cd-St、Pb-St、Zn-St并用时有相乘效果,与Zn系并用为无毒配合。与有机锡、Zn并用于耐硫化配合。 | |
硬脂酸铝 Aluminium Stearate | Al-St | 无毒性,可用于色粉分散。 | |
有 机 锡 | 有机锡 Maleate Tin | M-Tin | 与金属皂一样,有机锡即能与氯化氢结合,又能与不稳定的氯离子作用;还能与多烯进行反应,它的热稳定效果很高,但它与含铅化合物发生硫化污染,应避免二者并用。有机锡多单独使用,是透明性最好的安定剂之一。 |
环 氧 系 | 环氧化大豆油 Epoxidized soya bean oil | ESBO | 与Ca-Zn并用有相乘效果,无毒性。 |
阻燃剂(Flame ratardant)
第一节概述
大多数高分子材料,无论中天然的,还是合成的,遇火都会燃烧.阻燃剂就是一类能够防止材料被引燃或者抑制火焰传播的助剂.阻燃剂主要用于合成高分子材料或天然高分子材料的阻燃.在高分子材料中加工入阻燃剂﹐能够减少高分子材料的可燃性﹐能使高分子材料接触火焰时﹐燃烧迅速变慢﹐离开火源后能较快的自熄。注意﹐含有阻燃剂的材料并不能成为不燃材料﹐它们只能减少火灾危险﹐而不能消除火灾危险。对阻燃剂的要求是多方面的。人们希望阻燃剂能在用量很低的情况下具有持久的阻燃作用﹔希望阻燃剂无毒﹐不会在燃烧时生成有毒气体和浓烟﹔希望阻燃剂具有较高的热稳定性﹐在遇火情况下不会分解或者挥发﹔希望基础树脂的力学性能和物理性能不会由于阻燃剂的使用而损失或降低。应在材料的阻燃性及其它性能之间寻求最佳的性/价比(effectratio/cost)﹐而不能过多地降低材料原有的良好性能为代价﹐来一味地满足阻燃性能过高的要求。除此之外﹐在提高材料阻燃性的同时﹐应尽量减少材料的热分解或燃烧生成的有毒气体信发烟量。在阻燃剂领域﹐阻燃和抑烟是相辅相成的。
阻燃剂主要是含磷﹑卤素﹑硼﹑锑﹑铅﹑钼等元素的有机物的无机物。根据其使用方法﹐阻燃剂一般分为添加型和反应型两类。添加型阻燃剂是在塑料加工过程中简单参加和混合在塑料中﹐主要用于热塑性塑料。反应性阻燃剂是在聚合物合成过程中﹐作为一个组分参加反应﹐并键合到聚合物的分子链上﹐多用于热固性树脂。有些反应型阻燃剂﹐也可在塑料的加工过程中添加。
按照化学结构﹐阻燃剂又可分为无机阻燃剂和有机阻燃剂两类。无机阻燃剂包括铝﹑锑﹑锌﹑钼等金属氧化物﹑磷酸盐﹑硼酸盐﹑硫酸盐等﹔有机阻燃剂包括含卤脂肪烃和芳香烃﹑有机磷化合物﹑卤化有机磷化合物等。阻燃剂按照起阻燃作用的主要元素还可分为卤素系阻燃剂﹑磷系阻燃剂以及铝﹑锑﹑硼﹑钼等金属氧化物阻燃剂﹔也可以按大的类别分为溴系﹑磷系﹑氯系和铝基﹑硼基﹑锑基阻燃剂等。反应型阻燃剂与树脂起一定的化学反应﹐即阻燃剂与树脂之间有键的结合﹐因此反应型阻燃剂在树脂中比较稳定﹐它对火焰的抑制作用通常比添加型的持久﹐对材料的性能影响较小﹐但操作和加工工艺较为复杂。而添加型阻燃剂只是与树脂物理混合﹐没有化学反应﹐使用量较大﹐操作也比较方便﹐因此成为一种广泛采用的阻燃剂体系。
第二节聚合物的燃烧与阻燃剂的作用机理
一﹑聚合物的燃烧
(一)聚合物的燃烧过程
阻燃剂的燃烧是一个非常复杂的急剧氧化过程﹐从材料的吸热分解到剧烈的氧化发光发热﹐包括一系列的物理变化和化学变化。聚合物在受到外部热源的作用时﹐首先被加热﹑进而降解﹑生成挥发性的可燃气体和其它热分解产物。随着可燃性气体浓度的增大﹐当达到某一极限时聚合物开始燃烧。这一燃烧模式中﹐聚合物在热源的作用下﹐首先分解产生可燃性气体﹐可燃性气体从固相扩散到气相﹐气相中可燃性气体与氧气反应而开始燃烧﹐燃烧产生的热量向聚合物表面国辐射并传至聚合物内部﹐聚合物由于热的作用继续分解﹐形成燃烧的循环过程。因此阻燃也就是抑制这个燃烧的循环过程。
不同聚合物热分解生成的产物决定了聚合物燃烧的难易程度﹐因此不同的聚合物具有不同的燃烧性能。同一聚合物由于加入不同的助剂其燃烧的难易程度也有变化﹐当PVC中加入增塑剂后制品往往变得容易燃烧﹐而加入阻燃剂则使制品难以燃烧。阻燃的目的是为了提高制品的难燃程度﹐减少发生火灾的可能性而使制品变成不燃材料。聚合物阻燃后虽然可以降低发生火灾的危险性﹐但不能完全消除火灾危险。阻燃后的聚合物在大火中仍能猛烈燃烧。
(二)影响聚合物燃烧的主要因素
1. 聚合物的热分解特性
聚合物的热分解特性决定了聚合物的燃烧性能。聚合物吸收足够的能量后开始分解﹐生成分子量比较小的可燃性气体﹑不燃性气体和炭化残渣。不同的聚合物由于组成和化学结构不同﹐具有不同的热分解性能﹐即不同的热分解温度和不同的分解产物。热分解温度高﹐说明聚合物的热稳定性好﹐需要供给较多的热量才能使其分解。聚合物分解产物决定着聚合物引燃的难易程度﹐分解产物中含有可燃性气体越多越易燃烧。
2.燃烧温度和着火温度
燃烧温度对聚合物的燃烧过程有着明显的影响﹐燃烧温度越高﹐聚合物燃烧的速度就越快﹐释放出的热量也越多。实际上聚合物的燃烧速度还受氧气扩散速度的控制。
聚合物的着火温度对燃烧也起着至关重要的作用。聚合物的燃烧依赖于热分解产生的可燃性气体﹐可燃性气体的着火温度受燃烧活化能的制约﹐因此可燃性气体的着火温度与其化学结构之间并不存在对应关系。
3.燃烧热
聚合物的稳定燃烧主要依靠释放出的热量(燃烧热)来维持﹐若燃烧热向周围的散失大于燃烧释放出的热量﹐则一旦撤去热源﹐燃烧就难于维持下去﹐反之燃烧进一步加剧。如果两者达到平衡则进入稳定燃烧状态。
4.氧气的浓度
聚合物的燃烧需要有充足的氧气﹐否则燃烧就不能发生或难于维持稳定的燃烧﹐并产生大量未充分燃烧的烟尘。不同分子结构的材料﹐燃烧时要求的氧气浓度也不同。实际应用是﹐不少氧指数大于21的材料﹐在空气中燃烧而不能自熄。因此通常讲的阻燃并具有自熄性的材料氧指数至少大于27。
(三)聚合物燃烧的发烟性
聚合物燃烧时不仅释放出大量的热能﹐而且常常产生大量的渐尘及有毒气体。烟雾中既有黑烟也有白烟﹐有的刺激性很大。烟雾中含炭微粒越多﹐颜色越深﹔含HCL﹑*氢﹑氨等成分越多﹐刺激性越大。
抑制聚合物燃烧烟雾方法主要有物理方法和化学方法。物理方法重要有隔热﹑降温﹑其实质是抑制聚合物的燃烧。由于抑制燃烧便抑制了烟雾的产生﹔化学法则是采取添加“抑烟剂”的方法﹐根据其作用原理可分为吸咐型和反应型两种。吸咐型使分解或燃烧生成的炭质或石墨状微粒不至扩散在空间形成烟雾。反应型则通过催化分解或燃烧的反应模式﹐改变聚合物燃烧时的产物组成﹐从而达到抑制烟雾的目的。碳酸钙﹑氢氧化镁﹑氢氧化铝等都具有抑烟作用。碳酸钙的抑烟作用主要是捕捉烟雾中的氯化氢气体﹐使之生成稳定的氯化钙而残留于燃烧后的炭化层中。
(四)聚合物燃烧的毒性
聚合物的燃烧是一个非常复杂的过程﹐燃烧产物随着聚合物的组成﹑燃烧条件﹑阻燃体系的不同而不同﹐燃烧过程随着外界因素的变化而变化。故产生的毒性各种各样。
二﹑阻燃剂的作用机理
阻燃剂的作用机理比较复杂﹐相同的阻燃剂在不同的聚合物中的阻燃机理有时也存在一定的差异。阻燃机理的分类归纳起来有以下几种模式﹕1.抑制效应﹐捕获聚合物燃烧生成的活性自由基﹐从而抑制产生活性自由基的链锁反应﹐使燃烧减弱﹔2.链转移效应﹐改变聚合物材料的燃烧模式﹐抑制可燃性气体的产生﹔3.覆盖效应同﹐阻燃剂受热释放出的隋性气体在气相中隔绝可燃性气体与氧的接触﹐或者聚合物表面形成固态的炭层或液体的膜﹐阻止可燃性气体的逸出﹔4.稀释效应阻燃剂受热分解产生的不可燃性气体稀释氧和可燃性气体的浓度﹐使其达不到继续燃烧所必需的条件﹔5.吸热效应﹐阻燃剂受热分解吸收大量燃烧热﹐使聚合物材料温度上升困难。
(一)卤系阻燃剂阻燃机理
单独使用卤系阻燃剂时﹐主要在气相中延缓或者阻止聚合物的燃烧。卤系阻燃剂在高温下分解生成卤化氢﹐可作为自由基终止剂捕捉聚合物燃烧链式中的活性自由基OH.﹑O.﹑H.,生成活性较低的卤素自由基﹐从而减弱或终止气相燃烧中的链式反应达到阻燃的目的。
HX+H?→H2+X?
HX+O?→OH+X?
2H?+ZnMoO4→ZnO+Mo4+O2+H2O
卤化氯还能稀释空气中的氧﹐覆盖于材料表面阻隔空气﹐使材料的燃烧速度降低。
卤系阻燃剂与氧化锑具有显著的协同作用。卤化氢与氧化锑反应生成卤化锑﹐其是决定阻燃作用的关键因素。卤化锑具有优异的阻燃作用表现如下﹕1.卤—氧化锑为分解为吸热反应﹐可降低聚合物的燃烧温度和分解速度﹔2.卤化锑蒸气能较长时间停留在气相中﹐有效稀释可燃性气体。同时覆盖在聚合物表面﹐可隔热﹑隔氧﹔3.液态及固态卤化锑微粒的表面效应可降低火焰能量﹔4.在火焰下层的固态或熔融态聚合物中﹐卤化锑能促进成炭反应﹐相对减缓聚合物分解生成可燃性气体的速度﹐同时生成的炭层又可将聚合物封闭﹐阻止可燃性气体逸出和进入燃烧区﹔5.三卤化锑在燃烧区可捕捉气相中维持燃烧链式反应的活性自由基﹐改变气相燃烧的反应模式﹐减少反应热而使火焰猝灭。五溴苯与氧化锑的比例在(1—3)﹕1的范围内阻燃效果最好。
(二)磷系阻燃剂阻燃机理
磷系阻燃剂阻燃的材料燃烧时可生成较多的焦炭﹐减少可燃性气体的生成量﹐使被阻燃材料的质量损失率大大降低﹐但燃烧时生成的烟量较大。有机磷系阻燃剂可同时在凝聚相及气相中发挥阻燃作用﹐但以在凝聚相中为主。有机磷系阻燃剂的阻燃机理随着其结构﹑聚合物类型及燃烧条件的不同也存在一定的差异。有机磷系阻燃剂在高聚物受热被引燃时﹐首先分解生成磷酸﹐磷酸脱水生成偏磷酸﹐偏磷酸聚合生成聚偏磷酸﹐这类酸对含羟基聚合物的脱水成炭具有催化作用﹐加速了成炭过程。成炭的结果是在材料表面形成石墨状的焦炭层﹐这种炭层难燃﹑隔热﹑隔氧﹐从而使传至材料表面的热量减少﹐热分解缓慢﹔其次羟基聚合物的脱水系吸热反应﹐脱水形成的水蒸气又能稀释大气中的氧气及可燃性气体﹐有助于使燃烧中断﹔燃烧生成的聚偏磷酸可在材料表面形成一层覆盖于焦炭层的液膜﹐降低焦炭层的透气性并保护焦炭层不被继续氧化﹐也有利于提高材料的阻燃性。有机磷系阻燃剂的凝聚相阻燃机理基本是基于羟基聚合物的﹐故有机磷系阻燃剂在环氧树脂﹑聚氨酯中阻燃作用较大﹐而对不含有羟基的聚合物作用较小。磷系阻燃剂与卤系阻燃剂有协同作用﹐并且依赖于聚合物的类型。
(三)膨胀型阻燃剂阻燃机理
膨胀型阻燃剂克服了传统阻燃技朮的缺点﹐具有高阻燃﹑低烟﹑低毒﹑无腐蚀性气体产生﹑无熔滴行为等特点。膨胀型阻燃剂通过形成多孔泡沫炭层在凝聚相起阻燃作用﹐炭层经以下几步形成﹕1.在较低温度(150oC左右﹐具体取决于酸源和其它组分的性质)下﹐由酸源放出能酯化多元醇和作为脱水剂的有机酸﹔2.在稍高温度下﹐无机酸与多元醇(碳源)进行酯化反应﹐而体系中的胺则作为酯化反应的催化剂﹐使酯化反应加速进行﹔3.体系在酯化反一色前或酯化过程中熔化﹔4.反应过程中产生的水蒸气和由气源产生的不燃性气体使已处于熔融状态的体系膨胀发泡﹐同时﹐多元醇和酯继续脱水炭化﹐形成无机物及炭残余物﹐使体系进一步膨胀发泡﹔5.反应接近完成时﹐体系胶化的固化﹐最后形成多孔泡沫炭层。
(四)无机阻燃剂的阻燃机理
氢氧化铝与氢氧化镁在高温下通过分解吸收大量的热量﹐生成的水蒸气可以稀释空气中的氧气浓度﹐从而延缓聚合物的热降解速度﹐减慢或抑制聚合物的燃烧﹐促进炭化﹑抑制烟雾的形成。
2Al(OH)3→Al2O3+3H2O
Mg(OH)2→MgO+H2O
根据这一原理﹐选择金属氢氧化物时﹐其分解温度和吸热量是两项重要的指标。碳酸钙虽然也有较高的吸热量﹐由于其分解温度比聚合物的分解出很多﹐故不能做阻燃剂用。即使与聚合物分解生成的HCL反应﹐由于碳酸钙在固相﹑HCL在气相﹐两者的反应速度和进程受到制约﹐没有明显的阻燃作用。虽然氢氧化铝和氢氧化镁比碳酸钙的阻燃效率要高的多﹐但仍需要加入60%才能起到明显作用.硼酸锌作为阻燃剂可同时在凝聚相和气相中发挥作用。在凝聚相中﹐硼酸锌在火焰作用下能熔化﹑脱水形成玻璃态的包覆层﹐进一步生成无机炭层﹐同时可促进聚合物成炭﹐从而减缓聚合物的分解及可燃性气体的生成速度﹐达到阻燃和抑烟的效果﹔气相中﹐硼酸锌由于分解产生水蒸气而吸热﹐当与卤系阻燃剂并秀或用于含卤树脂时﹐生成卤化锌﹑卤化硼﹐在气相中捕获自由HO.﹑H.发挥气相阻燃作用。
2ZnO.3B2O3+12HCL→Zn(OH)Cl+ZnCL2+3BCl+3BHO2+4H2O
锌的固体熔体对PVC有抑烟作用﹐体系中含有3.5%---4%的锌有很好的抑烟性能﹐这是在燃烧过程中生成的刘易斯酸ZnCL2能促进PVC有脱氢反应形成反式的烯烃结构﹐有利于分子间的成环作用及炭化物的生成。
(五)抑烟作用机理
聚合物的发烟性是由于燃烧不完全或生成石墨状微粒而引起的﹐阻燃性能越好﹐聚合物的燃烧越不完全﹐生成的烟就越多﹐因此阻燃和抑烟本身就是一对矛盾。一是聚合物燃烧时﹐本身就释放出大量的烟雾﹔二是由于加入卤—锑阻燃剂或者磷酸酯阻燃剂后﹐使发烟量增大。前一种情况需要加入抑烟剂来抑制其发烟过程﹔后一种情况应该尽量不使用发烟量增大的阻燃剂。根据聚合物燃烧成烟机理可知﹐抑制燃烧产生的烟雾实质上就是抑制聚合物分解的可燃性气体向空。气中的扩散﹑加速气相中可燃性气体转化为水和CO2的过程﹐液相中促进成炭反应并将成炭微粒吸咐在燃烧物表面的过程。
第三节阻燃剂各论
一﹑溴系阻燃剂
溴系阻燃剂是卤素阻燃剂中最重要和最有效的一种﹐由于溴系阻燃剂具有阻燃效果好﹑添加量少﹑兼容性好﹑热稳定性能优异﹑对阻燃制品性能影响小﹑具有价格优势等优点﹐一直很受市场欢迎。不过溴系阻燃剂也有严重的缺点,即降低了被阻燃材料的抗紫外线光稳定性,燃烧时生成较多的烟﹑腐蚀性气体和有毒气体。溴系阻燃剂一般与氧化锑并用﹐使得生烟量更高。
(一)阻燃机理
所有的高分子材料都具有可燃性﹐完全防火的树脂是没有的。可以通过加入阻燃剂可以使树脂获得阻燃性和自熄性。当树脂一旦离开火源后就会停止燃烧﹐叫做自熄。燃烧一般需要具备以下三个条件﹕1.可燃物质﹔2温度﹔3.氧气。只要缺少其中任何一个条件火就会熄灭。
溴系阻燃剂的阻燃作用主要是要气相中进行﹐其主要原因是溴系阻燃剂受热分解﹐生成HBr,而HBr能捕获传递燃烧链式反应的活性自由基(如OH.﹑O.﹑H.),生成活性较低的溴自由基,致使燃烧缓慢或终止.反应式如下:
RBr→Br.+R.
Br.+RCH3→HBr+RCH2.
HBr+H.→H2+Br.
HBr+O.→OH.+ Br.
HBr+ OH.→H2O+ Br.
此外﹐HBr为密度大的气体﹐且难燃﹐它不仅能稀释空气中的氧﹐而且能覆盖于材料表面﹐排除空气﹐致使材料的燃烧速度或自熄。
就阻燃效率而言﹐脂肪族溴化物>脂环族溴化物>芳香族溴化物﹐而热稳定性恰恰相反。
当溴系阻燃剂与氧化锑并用时﹐具有明显的协同作用。
(二)溴系阻燃剂主要品种
1.多溴二苯醚类
多溴二苯醚包括十溴二苯醚(DBOPO)﹑八溴二苯醚(ODPO)﹑五溴二苯醚(PBDPO),它们均为添加型阻燃剂。只有十溴二苯醚是单一的化合物﹐其它两者都是混合物。分子式分别是C12OBr10﹑C12H2OBr8﹑C12H5OBr5。十溴二苯醚(DBOPO)是一种添加型阻燃剂﹐该产品具有极为优异的热稳定性熔点为304---309oC,溴含量为83.3%。
2.溴化邻苯二甲酸酯
代表产品DP-45﹐其阻燃效率高于氯化石蜡和磷酸酯﹐且发烟量低于磷酸酯。
二﹑氯系阻燃剂
氯系阻燃剂阻燃机理与溴系阻燃剂相同﹐就阻燃效率而言﹐氯系阻燃剂远远逊色于溴系阻燃剂。
(一)氯化石蜡
氯含量为70%的氯化石蜡是一种白色粉未﹐化学稳定性好﹐常温下不溶于水和低级醇。氯含量为52%的氯化石蜡为油状液体,在气相中起阻燃作用.氯化石蜡通常和三氧化二锑协同使用,因其价格低廉,并有良好之可塑剂性能,尤其适用于考虑成本和产品加工性的场合,此为最有利之耐燃化学配方,适用于硬质和软质制品.但氯化石蜡不易多加,否则容易溢出.
(二)双(六氯环戊二烯)环辛烷
该品是一种添加型阻燃剂﹐分子式为C18H12Cl12.该品优点极多﹐例如初期着色性好﹑电性能优异﹑阻燃性能好﹑热稳定性高﹑低生烟量﹑协效剂的可选择性﹑抗紫外线性能良好﹑耐水解性能良好﹑无毒等等。
三﹑磷系阻燃剂
磷系阻燃剂并不是什么新型阻燃剂﹐但它作为无卤体系﹐在阻燃剂领域现在颇受欢迎。有机磷系阻燃剂包括磷酸酯﹑膦酸酯(包括其含卤衍生物)﹑亚磷酸酯﹑氧化膦﹑含磷多元醇/氮化物等。但作为阻燃剂﹐应用范围最广泛的是磷酸酯和膦酸酯﹐尤其是含卤的磷酸酯的膦酸酯。磷酸酯和含卤的磷酸酯兼具阻燃剂和增塑剂功能﹐以阻燃剂为主﹐称为增塑性阻燃剂﹔而非卤磷酸酯的主要功能是增塑﹐兼具阻燃剂作用﹐称为阻燃性增塑剂。
(一)阻燃机理
磷系阻燃剂的阻燃机理并非单一的。一般认为有机磷系阻燃剂可同时在凝聚相及气相发挥阻燃作用。不过阻燃机理也因磷系阻燃剂的结构﹑聚合物类型及燃烧条件而不尽相同。
1.凝聚相的阻燃机理当含有磷系阻燃剂的聚合物受热时﹐可分解生成磷酸或多磷酸。这类酸能催化含羟基化合物的吸热脱水成炭反应﹐生成水和焦炭。含羟基化合物炭化有结果﹐是在其表面形成石墨状的焦炭层﹐此炭层隔氧﹑隔热﹐使燃烧窒息﹐从而达到阻燃的目的。
2.气相的阻燃机理有机磷系阻燃剂受热分解的产物中含有PO.游离基用OH.游离基,从而使火焰中的H.及OH.浓度大大减小,起到抑制燃烧的作用.
(二) 磷系阻燃剂的主要品种1.磷酸三(α-氯乙基)酯磷酸三(α-氯乙基)酯(TCEP)为添加型阻燃剂,分子式为C6H12O4Cl3P.磷酸三(α-氯乙基)酯为无色透明液体,不溶于脂肪烃,微溶于水.磷酸三(α-氯乙基)酯具有优异的阻燃性、优良的抗低温性和抗紫外线性。其蒸气只有在225度用直接火焰才能点燃,且移走火焰后即自熄。以TECP为阻燃剂,不仅仅可以提高被阻燃材料的阻燃级别,还可以提高其耐水性、耐酸性、耐寒性及抗静电性。TECP在阻燃不饱和聚酯中用10%-20%,在软质PVC中作为辅助增塑阻燃剂使用时为5%-10%.
2. 磷酸三(1,3氯乙-2-丙基)酯磷酸三(1,3氯乙-2-丙基)酯(TDCPP)为添加型阻燃剂,分子式为C9H15O4CL6P .TDCPP在软质PVC中的添加量不超过15%.
3.亚磷酸酯以.亚磷酸三苯酯(TPP)和.亚磷酸二苯异辛酯(DPIOP)为主
四﹑膨胀型阻燃剂
膨胀型阻燃剂是以磷氮为主要成分的阻燃剂﹐它不含卤素﹐也不采用氧化锑为协效剂。含有膨胀型阻燃剂的高聚物受热时﹐表面能生成一层均匀的炭质泡沫层﹐该泡沫层隔热﹑隔氧﹑抑烟并能防止产生熔融滴落﹐而形成良好的阻燃性能。
膨胀型阻燃体系一般由三个部分组成﹕
(1)酸源(脱水剂)一般可以是无机酸或加热至100-250oC时生成无机酸的化合物﹐如磷酸﹑硫酸﹑硼酸﹑各种磷酸盐﹑酸酸酯和硼酸盐等。
(2)炭源(成炭剂)它是形成泡沫炭化层的基础﹐主要是一些含碳量高的多羟基化合物﹐如淀粉﹑季戊四醇和它的二聚物﹑三聚物以及含有羟基的有机树脂等。
(3)气源(氮源﹑发泡源) 常用的发泡源一般为三聚氰胺﹑双氰胺﹑聚磷酸胺等。
膨胀型阻燃剂对于不同的聚合物体系﹐有时不需要几个组分同时并用﹐只需要加入其中的一种或者几趾﹐聚合物本身也可以充当其中的某一角色。
由于膨胀型阻燃剂需要适应聚合物的加工温度﹐因此不能象膨胀型阻燃涂料那样只覆盖于被阻燃材料的表面﹐所以膨胀型阻燃剂应具备以下性质﹕1.热稳定性好﹐能够经受聚合物加工过程中200oC以上的高温﹔2.由于聚合物热降解要释放出大量挥发性物质亲形成残渣﹐因而该过程不应对膨胀发泡过程产生不良影响﹔3.尽管膨胀型阻燃剂可均匀分布在聚合物体系中﹐但在材料燃烧时要能形成一层完全覆盖于材料表面的膨胀炭层﹔4.膨胀型阻燃剂必须与被阻燃物有良好的兼容性﹐不能与聚合物和添加剂发生不良作用﹐不能过多恶化材料的物理机械性能。也就是说﹐阻燃剂必须与聚合物相匹配才能有效的发挥其阻燃作用﹐这种匹配包括热行为﹑受热条件下的生成物质等。
五﹑无机阻燃剂
(一)氢氧化铝(Al(OH)3)
氢氧化铝又名三水合铝﹐三水合氧化铝﹐简称ATH.分子式Al(OH)3.用于阻燃用的氢氧化铝一般是α晶型﹐因此也可表示为α-Al(OH)3。氢氧化铝开始分解的温度为205oC。在205---230oC时﹐α-Al(OH)3部分失水﹔在530oC左右﹐进一步分解转化为γ-Al2O3.整个过程要吸收大量的热量.
单独使用氢氧化铝﹐添加量需要在60PHR以上﹐这必然要影响到树脂的加工性能和物理性能﹐为了克服上述缺点﹐对氢氧化铝进行超细化处理并用偶联剂进行表面改性。目前氢氧化铝的改性主要集中在粒度分布的控制﹑偶联剂的表面处理上。使用的偶联剂有硅烷﹑钛酸酯等。此外也可以采用硬酯酸锌﹑硬酯酸钠进行表面处理。为了改善氢氧化铝的阻燃性能﹐提高其耐热性﹑消烟性﹑耐湿性﹑与被阻燃基材的兼容性及电绝缘性等﹐可使粒径细微化和超细微化﹐控制合理的颗粒分布﹐降低氢氧化铝中的Na+含量等。
氢氧化铝与卤锑﹑硼酸锌﹑红磷等多种阻燃剂有协同作用。单独使用氢氧化铝添加量需要在60%以上时才能达到较好的阻燃效果。氢氧化铝用于PVC软制品和半硬制品时﹐通常与氧化锑﹑硼酸锌并用﹐不但可以提高阻燃性还可以抑制烟雾的产生。氢氧化铝用于PP﹑PE时,一般与红磷﹑季戊四醇﹑聚磷酸胺等组成膨胀型阻燃体系。
(二)氢氧化镁
氢氧化镁与氢氧化铝有许多相似之处﹐同样具有无烟﹑无毒﹑无腐蚀等优点。氢氧化镁为白色粉未﹐分子式为Mg(OH)2﹐体积电阻108--1010Ω。分解温度为340oC﹐更适合于某些需要加工温度较高的聚合物。在部分情况下,高填充的氢氧化镁和氢氧化铝对氧指数的提高也许会有帮助,但无助于水平燃烧性能(如UL94)的提高.氢氧化镁具有优异的抑制HCl生成的能力,这方面远远优于CaCO3和氢氧化铝.
(三)红磷和包覆红磷
红磷和聚磷酸铵是磷系阻燃剂中具有独特性能的两种阻燃剂.随着近年来膨胀型阻燃剂的发展,聚磷酸铵已成为其中不可或缺的重要组分.而红磷由于其优异的阻燃﹑低毒性能和与多种阻燃剂的协同作用﹐成为非卤阻燃剂中的重要品种。红磷由于仅含有磷元素﹐因此比其它磷系阻燃剂阻燃效率高﹑添加量低﹐较少降低材料的力学性能。红磷做为阻燃剂缺点也较突出﹕1.红磷在空气中很容易吸收水分,生成磷酸﹑亚磷酸等物质﹐因此红磷在聚合物中经过较长时间后,制品表面的红磷吸潮氧化﹐使制品表面被腐蚀而失去光泽和原有的性能﹐并慢慢向内层深化﹐尤其对电子组件有绝缘性能影响更大。2.红磷与树脂兼容性差﹐不仅难以分散﹐而且会出现离析沉降﹐使树脂的黏度上升﹐给树脂的操作带来困难﹐导致性能下降。3.红磷长期与空气接触的过程中﹐除生成各种酸外﹐并会释放出有剧毒的PH3气体。4.红磷易为冲击所引燃﹐干燥的红磷粉尘有燃烧及爆炸危险。5.红磷的紫红色易使被阻燃物着色。
为了克服以上缺点﹐将红磷用有机物或者无机物包覆起来﹐为包覆红磷。红磷包覆按照包覆的材料分为三种,无机包覆﹑有机包覆﹑有机-无机复合包覆。无机包覆法是以无机材料为包覆材料的方法。例如以氢氧化铝包覆时﹐可将红磷悬浮于含硫酸铝的水溶液中﹐再加入氢氧化钠调节溶液的PH值﹐以生成氢氧化铝沉淀在红磷表面并形成均一而致密的保护层.无机包覆红磷在着火点﹑吸湿性和PH3发生量等方面都得到了不同程度的改善﹐但仍与树兼容性差﹐着火点不够高﹐仍产生一定量的PH3.无机包覆材料还可以是氢氧化镁﹑氢氧化锌等。有机包覆法是以有机物包覆红磷﹐目前多采用热固性树脂﹐如环氧树脂进行包覆。有机-无机复合包覆是指先包覆一层无机物﹐再包覆一层有机物。包覆红磷对制品的物理﹑机械性能影响小﹐赋予被阻燃材料较好的抗冲击性能﹐改善了与树脂的兼容性﹔同时包覆红磷的热稳定性好﹐可用于某些需要高温加工成型搞聚物制品﹐且低烟低毒﹐与树脂混合时不放出PH3﹐也不易被冲击引燃﹐粉尘爆炸危险性大为减少﹔此外包覆红磷在耐候性﹑电气性能﹑稳定性等方面也有较好表现。
除包覆外﹐铝锌也能降低红磷氧化速度。金属氢氧化物是红磷氧化的抑制剂﹐因此红磷中常常加入氢氧化铝以使红磷稳定化。红磷的阻燃效果与被阻燃物有关。例如红磷阻燃非含氧聚合物HDPE的氧指数与红磷的用量成正比﹐而阻燃含氧聚合物PET的氧指数与红磷用量的平方根成反比。红磷在聚合筘的用量有一极限值﹐通常在8%-10%之间﹐用量再高可能引起阻燃性能的下降。红磷虽然有较高的阻燃效率﹐但单独使用红磷很难达到阻燃要求﹐所以通常与其它阻燃剂配合使用。聚铣胺是红磷阻燃的主要对象之一.
(四)聚磷酸胺(APP)
聚磷酸胺通常简称APP,其通式为(NH4)n+2PnOn+1,当n足够大时,可写为(NH4PO3)n,当n=10—20时,为短链APP,相对分子量约1000—2000;当n>20时,称长链APP,相对分子量在2000以上。APP为白色粉未﹐接近中性﹐短链APP具有水溶性﹐长链APP难溶于水﹐溶解度随温度升高而很快增高。APP的吸湿性随聚合度增加而降低。APP热稳定性良好﹐热分解温度通常在250oC﹐分解时释放出氨和水并生成磷酸。
尽管APP的热分解温度高于大部分热塑性树脂的加工温度﹐常规品种在实际使用过程中往往不能满足要求﹐这与其粒度和小量分解生成物磷酸有关。因此用于热塑性塑料的品种大多是包覆改性的品种。
(五)氧化锑(Sb2O3)
锑系阻燃剂是最重要的无机阻燃剂之一﹐单独使用时作用小﹐但与卤系阻燃剂并用可大大提高卤系阻燃剂的效能。锑系阻燃剂的主要品种三氧化二锑(Sb2O3)﹑胶体五氧化二锑及锑酸钠。通常所说的氧化锑一般是指Sb2O3。三氧化二锑(Sb2O3)分子量为291.60﹐理论锑含量83.54%。三氧化二锑为白色结晶﹐受热时显黄色。为了降低三氧化二锑的成本﹐可将三氧化二锑/二氧化硅=50/50混合。
(六)硼酸锌
硼酸锌(简称ZB)是一种多功能添加剂﹐具有阻燃﹑成炭﹑抑烟﹑抑制烟燃和防止熔融滴落多种功效。主要品种有3.5水和7水两种,其分子式通常为2ZnO.3B2O3.3.5H2O或2ZnO.3B2O3.7H2O.所说的硼酸锌一般是指2ZnO.3B2O3.3.5H2O。2ZnO.3B2O3.3.5H2OO为无规则或者菱性白色粉未﹐熔点980oC﹐300oC以上开始失去结晶水。其中Firebrake ZB为标准阻燃剂硼酸锌﹐Firebrake ZB-XF为超细粉,Firebrake415为高脱水硼酸锌。硼酸锌在软质PVC制品中﹐阻燃效果较差﹐最好与氧化锑(Sb2O3)并用。硼酸锌具有较强的成炭性﹐可降低材料的发烟量﹐也是一种有效的抑烟剂。硼酸锌与氢氧化铝具有极强的协同作用﹐两者在硬质PVC中并用代替氧化锑﹐烟密度显著下降。实际使用过程中﹐硼酸锌往往与其它阻燃剂并用﹐以发挥阻燃协效作用和抑烟功能。
(1)PVC中的应用PVC硬制品中﹐硼酸锌可全部代替氧化锑达到相近的阻燃效果。以50%的硼酸锌取代氧化锑﹐烟密度显著下降﹐但氧指数变化很小。在仅以磷酸酯增塑的软PVC中﹐当硼酸锌由0.5PHR增加到5PHR时,不仅材料作用密度大大下降﹐而且氧指数也随硼酸锌用量的增加而升高﹐说明此时单一的硼酸锌也同时具有阻燃和抑烟作用。
(2)无卤阻燃系的应用在大多数无卤阻燃体系中﹐硼酸锌与氢氧化镁并用可提高阻燃性能。
(七)本厂用阻燃剂列表
阻燃剂类型 | 本厂所用牌号及等级 | 主要性能 |
氧化锑 | Sb2O3 , 0级 | 白色粉状物,添加时会使制品呈不透明,不能用于透明配方中;在气固相起阻燃作用,耐燃效果好但有浓烟产生;故只限于特定用途,添加量为树脂100中添加5 %以下. |
三芳基磷酸酯 | Reofos 65 含磷量为7.9% | 阻燃性增塑剂﹐可单独使用于PVC配方,如与硼酸锌并用效果更佳,不但阻燃效果,而且抑烟效果更好. |
硼酸锌 | Firebrake ZB 2ZnO.3B2O3. 5H2O | 可用于无卤阻燃体系,一般不单独使用,与氢氧化铝或氢氧化镁有协效作用﹐在PVC配方多与氧化锑配合﹐有很好的抑烟和阻燃作用。 |
氯化石蜡 | PARAFFIN 52L 含氯52% | 液体阻燃剂,在气相中起阻燃作用.氯化石蜡通常和三氧化二锑协同使用,因其价格低廉,并有良好之可塑剂性能,尤其适用于考虑成本和产品加工性的场合,此为最有利之耐燃化学配方,适用于硬质和软质制品.但氯化石蜡不易多加,否则容易溢出. |
四溴邻苯二甲酯 | DP-45 ,含溴45% | 液状阻燃剂,兼具可塑性能, 在气相中起阻燃作用.阻燃性能好,但价格昂贵. |
聚磷酸胺 | APP | 多用于无卤阻体系,膨胀型多功能阻燃剂 ﹐一般用于PP的阻燃﹐用于PE和PVC效果不佳。 |
氢氧化镁 | Mg(OH)2 | 同氢氧化铝有相似作用﹐可用于无卤料的阻燃。无烟﹑无毒﹑无腐蚀的白色粉未。体积电阻108--1010Ω。分解温度为340oC﹐更适合于某些需要加工温度较高的聚合物。在部分情况下,高填充的氢氧化镁对氧指数的提高会有帮助,无助于水平燃烧性能提高.氢氧化镁具有优异的抑制HCl生成能力,这方面远远优于CaCO3和氢氧化铝 |
氢氧化铝 | H-42M | 氢氧化铝由于热容很大,能够迅速吸收燃烧区域的热量,而产生的水也能吸收部分热量,并稀释降低燃烧气体和氧化剂的浓度,从而减少了可燃气体和烟的生成,起到阻燃作用;由于需加入之量很大才可达到一定的阻燃效果,因此常用作填充剂。 |
填充剂(Filler)
填充剂又称填料﹐泛指被填充于聚合物中增加容量﹑降低成本的一类物质。在PVC中其主要作为增量剂(extender)﹐以增加体积降低成本为目的﹐因此填充剂不但须价廉﹐有一定的质量﹐且须有丰富之来源。随着塑料﹑橡胶等加工技朮的发展﹐填充剂的内涵和外延都发生了根本性的变化﹐重要体现在以下两个方面。1.填充剂的主要功能从增加容量﹑降低成本的传统概念向改善聚合物性能﹑赋予聚合物新功能的方向发展﹐如用钛白粉改性提高聚合物耐性等。2.填充剂生产中超细化技朮﹑表面改性技朮和纳米技朮的应用﹐也赋予了填充剂新的功能。
填充剂作用机理大致归纳为以下几种﹕
1.填料粒子与聚合物相互作用﹐形成一定量的化学键﹑次价键。
2.填料表面与聚合物通过次价键或范得华力相连﹐形成海—岛结构﹐当受到外力作用时﹐将应力传递到填料与聚合物之间的结合部位﹐次价键断裂使间隙增大﹑形成微小裂纹﹐这一过程可以有效地吸收一部分外部能量﹐避免应力集中﹐从而改善力学性能。这类填充剂的粒径通过要求在1μm以下﹐并且有一个最佳用量﹐用量太大或太小都不能得到最佳效果。
3.对于玻璃纤维﹑碳纤维以及长径比较大的填料来说﹐其填充体系受到外力时﹐外力首先作用到填充剂上﹐由于这类填充剂比聚合物有更高的力学性能﹐可以发挥增强的作用。
以上机理都是以填充剂的充分分散为前提。通常﹐改善填充剂的分散性有两种途径﹕一是减小填充剂的粒度﹐在一定范围内﹐粒度越小﹐分散性也越好﹔二是对填充剂进行表面处理。如果填充剂的粒度小于0.5μm﹐由于表面能较高﹐又会导致粒子间团聚﹐使分散性下降﹐因此填料的表面处理显得更为重要。
第一节填充剂的性能及选择条件
一﹑填充剂的性能
聚合物改性用的填充剂无论来源和加工方法如何﹐最终都以颗粒的形式出现﹐这些颗粒的几何形状﹑粒径大小及其分布﹑物理化学性质都将直接影响填充聚合物的性能﹐这也关系到填充改性技朮的成败和优劣。
(一)几何特征
粒子是填充剂存在主要形式﹐不同填充剂的粒子形态具有明显的差别﹐不同矿物在加工粉碎后的几何形状用长径比也不相同。
(二)粒径
聚合物改性所用的填充剂粒子的粗细即粒径大小是根据具体要求确定的。填充剂粒度越小﹐则填充材料的力学性能越好﹐但同时填充剂粒度越小﹐要实现其分散均匀越困难﹐需要更多的助剂和更好的加工设备﹐而且填充剂粒度越小所需要的加工费用越高。通常填充剂粒径可以用它的实际尺寸来表示﹐也可以用多少目的筛来表示。以下为对应关系。
目数是指分级筛6.45cm2面积筛网上的筛孔数。
(三)表面形态与性质
填料粒子的表面的粗糙程度不同,其表面积也不同。填料粒子的表面积不仅与粒子的几何形状有关﹐而且与其表面的粗糙度程度有关。比表面积是指填料单位质量的表面积﹐比表面积的大小对填料与树脂之间的亲合性﹑表面处理的难易程度以及成本有着密切的关系。填料粒子的表面能的大小关系到填料在基体树脂的分散程度﹐当比表面各一定时﹐表面能越大﹐粒子相互间越容易凝聚﹐越不容易分散。在处理填料表面时﹐降低其表面能是主要目标之一。
(四)物理性质
1.密度填料的密度与相对应的矿物是一致的﹐而且当填料粒子均匀分散到基体树脂中﹐给填充材料的密度带来的影响的也是它的真实密度。由于填料的粒子在堆砌时相互间有空隙﹐不同形状粒子的粒径大小及分布不同﹐在质量相同时﹐堆砌的体积不同﹐有时差别会很大﹐因此它们的表观密度是不一样的。
2.吸油值填料与增塑剂并用﹐如果增塑剂被填料所吸咐﹐就会大大降低增塑剂对树脂的增塑效果﹐而不同填料在等量填充时因各自的吸油值不同﹐对体系的影响也不同。例如重质碳酸钙的吸油值是轻质碳酸钙的4--5倍﹐故在达到同样增塑效果的情况下﹐使用重质碳酸钙可减少增塑剂的用量。由于重质碳酸钙的粒径比轻质碳酸钙大的多﹐因此虽然吸油值可减少增塑剂的用量﹐但其强度也相应变差。
3.硬度填料粒子的硬度对塑料加工设备的磨损关系重大﹐但硬度高的填料可以提高填充制品的耐磨性能。对同一种填料﹐加工设备金属表面的磨损强度随着填料粒径抚养加而上升﹐当粒径大到一定程度后﹐磨损强度趋于稳定。
4.颜色及光学特性为了对所填充的塑料基体的色泽不产生明显的变化或避免对基体的着色带来不利影响﹐通常希望填料是无色的﹐但这对大多数填料是不可能的﹐但至少应该是白色的﹐而且白度越高越好。填料的折射率和塑料的基体折射率有所不同。对多数填料来说﹐其折射率不只一个。填料的折射率和塑料的基体折射率之间的差别使填充塑料的透明性受到显著影响﹐对塑料着色的色泽深浅及鲜艳程度也有影响。
5.热性能填充与加工大多都涉及到加热﹑熔融﹑冷却定型等过程﹐填料本身的热性能及其与塑 料基体之间的差别同样也会对加工过程产生影响。
6.电性能金属是电的良导体﹐因此金属粉未作为填料使用可影响填充基材的电性能﹐但只要填充量不大﹐树脂基体能包裹每一个金属填料的粒子﹐其电性能不会发生突变。只有当填料用量增加致使金属粒子达到互相接触的程度时﹐填充塑料的电性能将会发生突变﹐体积电阻显著下降。非金属大多都是电的绝缘体﹐但是碳黑经处理以后填充塑料也会使其体积电阻显著下降。
7.磁性能具有磁性的粉未物质可用来作磁性塑料。
(五)热化学效应
高分子聚合物容易燃烧﹐大多数填料本身有不燃性﹐加入到聚合物中后可以起到减少可燃物浓度﹑延缓基体燃烧的作用。有的还可以与其它阻燃剂起到协同阻燃作用。氢氧化铝与氢氧化镁可以独立答为塑料的阻燃剂用。
二﹑填充剂的选择条件
由于填充剂种类繁多特性各异﹐制品所要求的特性也不同﹐因此无法以一种填充剂来满足所有制品的要求﹐在一般情况下﹐填充剂应具备以下条件﹕
1.价格低﹑来源丰富﹑质量一定﹔
2.分散性好﹐填充量大﹐相对密度小﹔
3.不降低树脂的加工性能及制品的物理化学性能﹐最好具有广泛的改性效果﹔
4.本身的耐水性﹑耐油性﹑耐化学腐蚀性优良﹑不被水和溶剂抽出﹔
5.不影响其它助剂的分散性﹐不与它们发生有害的化学反应﹔
6.纯度高﹐不含有对树脂有害的杂质﹔
7.对增塑剂吸收量小﹐无曲折白化现象。
三﹑使用填充剂的目的
1.增大容积﹐降低成本﹔
2.改进混炼胶性能﹐如调节可塑度﹑黏性﹑防止收缩﹑提高表面性能等﹔
3.改进硫化胶性能﹐如增加拉伸强度﹑抗撕裂强度﹑而磨耗性﹔调节硬度﹑弹性率﹔改进耐热性﹑耐油性﹑耐候性等﹔
4.提高电性能﹑导热性﹑耐水﹑耐溶剂性﹔
5.赋予阻燃性﹔
6.抑制树脂硬化时的发热﹑防止龟裂﹔
7.赋予隐蔽性﹑粘结性﹑粘合性﹔
8.发挥其它作用﹐如减少硬橡胶硫化时的发热收缩﹐调节胶乳﹑胶浆的稠度等。
第二节主要填充剂
一﹑碳酸钙
化学名碳酸钙 ﹐重质碳酸钙﹑轻质碳酸钙﹑活性碳酸钙﹑沉淀碳酸钙﹑双飞粉﹑水应石粉﹑胶体碳酸钙﹑胡粉。
分子式CaCO3
碳酸钙是一种物美价廉的填充剂﹐橡胶和塑料都大量使用﹐有的用量可高达70%,但多数添加量为30%以下。
1. 制法
重质碳酸钙是由天然石灰石经机械粉碎制得。具体制法可分为干法和湿法两种﹐干法是将石灰石用冲击式粉碎面粉碎后﹐用空气分级机分成适当粒度﹔湿法是用轮碾机或球磨机等机械加水粉碎﹐最后用渤水流将粒度分级。塑料使用的碳酸钙主要是用干法制造。轻质碳酸钙可用沉淀法制取﹐即用纯碱副产物沉淀制得﹐该方法少用。普遍使用的是二氧化碳合成法﹐将石灰石高温锻烧﹐然后经一毓化学反应而成。
为了改善碳酸钙在橡胶和塑胶中的分散性﹐提高补强性和其它性能﹐可用硬脂酸﹑胺类等各种有机表面活性剂进行处理。经表面处理的碳酸钙称活性碳酸钙或胶体碳酸钙。现大多采用钛酸酯偶联剂处理碳酸钙粒子表面﹐它不仅可以改善熔融流动性﹐而且可以增进物理性能。
2. 性质
重质碳酸钙粒子的形状不规则﹐相对密度2.710﹐折射率1.65。加热到898.6oC开始分解。轻质碳酸钙多呈纺锤形﹑棒状和针状﹐粒子较细。相对密度2.65﹐折射率1.65。分解温度为825---896.6oC。二者在空气中稳定﹐有轻微的吸潮能力。
3.用途
酸钙是塑料中使用最广泛的填充剂之一﹐其价格低廉﹐来源丰富﹐相对密度小﹐在塑料中不但具有增量作用外﹐还有改善加工性能和制品性能的作用。碳酸钙质地软﹐对加工机械和成型机械磨损小。一般轻质碳酸钙的粒子比重质碳酸钙细﹐纯度高﹐含无机杂质少﹐在同样用量﹐填充轻质碳酸钙的制品表面划伤性和折弯白化性比填充重质碳酸钙小。轻质碳酸钙的最大特点是补强作用﹐可提高制品的冲击强度。轻质碳酸钙在某些软质PVC中有热稳定作用﹐它的使用可热稳定剂的用量﹐允许使用比较价廉的稳定剂或稳定性相对较差的稳定剂﹐如钙锌﹑钡锌等。
碳酸钙主要用于PVC﹐可提高制品的色调稳定性。由于碳酸钙吸油值较高﹐吸收增塑剂的量较大﹐在软质PVC中的分散均匀性较差﹐配合量多时﹐会降低押出制品的表面光滑性。与白炭黑并用﹐可提高分散均匀性。重质碳酸钙作为填料加入塑料中﹐不仅起到增容﹑增量﹑降低成本的作用﹐作为功能性填料﹐还可以提高加工性能﹑提高充填塑料的加工性能。此外加入重质碳酸钙﹐可改进塑料的散光性﹐起遮光或消光作用﹐提高塑胶制品的印刷性能和尺寸稳定性。它可作为PVC的次级稳定剂﹐受热时重质碳酸钙能阻止烟雾的产生。
二﹑碳酸镁
碳酸镁商品名为轻质碳酸镁﹐成分为碱式碳酸镁。多用于橡胶的填充剂。
结构式为x MgCO3.yMg(OH)2.zH2O
1.性质
外观为白色单斜结晶或无定形粉未﹐无毒﹑无味。加热至300oC开始分解。碳酸镁是由数个结晶重合而成﹐折射率为1.520---1.530。
2.用途
碳酸镁的折射率与硫化胶相近﹐故多用作透明橡胶的填料。碳酸镁可作为橡胶制品的优良填充剂和补强剂﹐使用碳酸镁作为填充的硫化胶耐热性能好﹑生成热量小﹔缺点是撕裂强度较低﹐压缩永久变形大。
三﹑陶土
陶土又叫高岭土﹑白土﹑瓷土。陶土是一种自然界存在的水合硅酸铝矿物﹐主要成分是水合硅酸铝(Al2O3.2SiO2.H2O)。作为PVC的填充剂﹐最广泛使用的陶土是高岭土﹐其组成是含有不同结晶水的氧化铝和氧化硅结晶物﹐一般为纯高岭土和多水高岭土的混合物。高岭土可分为水合级﹑层离级﹑煅烧级和表面处理级几类。
1. 用途
高岭土用途广泛﹐当选择一种合适的高岭土来满足混合物料的应用需求时﹐应注意下列因素﹕1.必须确定混全物料中是否加入高岭土﹐在确定加入后﹐应考虑混合物料希望达到体何种性能﹐一般增加细度﹐有利于提高体系中的拉伸强度﹑模量﹑撕裂强度﹑硬度﹑冲击强度等﹐同时也有利于尺寸稳定性。2.扁平状的形态有利于改善制品的尺寸稳定性和阻隔性能﹐但缺点是会降低合缝线强度和抗冲击性能。3.对于较长的矿物质﹐能改进拉伸强度和模量﹑弯曲模量和定向冲击强度﹐但较长的填料易使制品翘曲。4.高岭土表面处理可以改善它在树脂母料中的润湿和分散程度﹐提高冲击强度﹑模量和撕裂强度﹐还可以改善电性能﹔5.对于对水分敏感的聚合物﹐应选用含水低于0.5%的锻烧高岭土。锻烧高岭土还具有化学惰性好﹐具有高亮度等优点﹐适用于电线胶料和要求色度保持也的塑料制品。
(1)在橡胶工业中的应用配合本品的胶料易于加工﹐胶料表面光滑。经锻烧除去水分的锻烧高岭土是较好的白色补强填充剂。其胶料硬度﹑拉伸强度﹑电阻率均比普通高岭土的胶料要好﹐特别是颜色和介电性能很好。
(2)在塑料中的应用锻烧高岭土可作为PVC的填充剂。它能使PVC制品的冲击强度﹑拉伸强度和电性能得到理想的平衡。此外高岭土对红外线的阻隔作用显著。在PP中除提高常规性能外﹐还能直到成核剂的作用﹐即在PP从高温状态冷却时﹐高岭土的存在可促使PP围绕高岭土颗粒结晶﹐其晶粒微细﹐数量增多﹐有利于提高PP的刚性和强度。
四﹑滑石粉
滑石粉的主要成份是水合硅酸镁。分子式为﹕3MgO.4SiO2.H2O或H2Mg(SiO3)4。滑石粉作为塑料用填充剂可提高制品的刚性﹐改善尺寸稳定性﹐防止高温蠕变﹐提高电性能。具有润滑性﹐可减少对成型机械或模具的磨损﹐但用量太多时不利于塑料的焊接。滑石粉适用于PVC胶料﹐因核本品的折射率(1.57)与PVC相近﹐故可用于半透明制品。
五﹑填充剂列表
填充剂类型 | 本厂所用牌号及等级 | 主要性能 |
重质碳酸钙 | MLT-2500 | 相对密度小﹐在塑料中不但具有增量作用外﹐还有改善加工性能和制品性能的作用,可提高制品的色调稳定性。由于碳酸钙吸油值较高﹐吸收增塑剂的量较大﹐在软质PVC中的分散均匀性较差﹐配合量多时﹐会降低押出制品的表面光滑性。作为功能性填料﹐还可以提高加工性能﹑提高充填塑料的加工性能。可改进塑料的散光性﹐起遮光或消光作用﹐提高塑胶制品的印刷性能和尺寸稳定性。它可作为PVC的次级稳定剂﹐受热时重质碳酸钙能阻止烟雾的产生。 |
轻质碳酸钙 | CCR | 补强作用﹐可提高制品的冲击强度。有热稳定作用。 |
高岭土 | SP-33 | 电气绝缘性能好﹐可用电源线胶料。抗红外线性能显著。 |
氢氧化铝 | 107/LE | 阻燃型填充剂. |
氢氧化镁 | Mg(OH)2 | 阻燃型填充剂. |
第三节填充剂对软质PVC改性的结果
软质PVC使用填充剂的主要目的是降低成本,此外也为了改善某些性能,如改善押出时的操作性能,增加制品的尺寸稳定性,赋予制品隐蔽性﹐提高电绝缘性能等。在选择PVC使用的填充剂时就考虑以下几点﹕在树脂中的分散性﹔增塑剂的消费量﹔对热光的稳定性﹔色调﹑隐蔽力及光泽﹑配合物的机械强度﹔耐药品性﹔配合物的电性能等。
1.拉伸强度
软质PVC中配合填充剂时﹐其拉伸强度一般随着配合量的增大而降低﹐特别是使用1μm以上的粗填充剂时﹐拉伸强度下降更快。使用1μm以下的细填充剂时﹐强度下降较少﹐有时却可随着配合量的增加而增大。槽法炭黑﹑合成硅酸钙或硬质陶土等填充剂配合量较小时﹐拉伸强度呈最低值﹐随着配合量的增加强度增加﹐而且增加的比例较大。在碳酸钙中﹐粒子细的碳酸钙也是在高配合量时能使拉伸强度增大﹐而某些表面处理的碳酸钙在高配合量时拉伸强度基本不增加。拉伸强度随填充剂的种类而异。一般能导致拉伸强度增大的填充剂其表面活性较强﹐因此要注意对PVC树脂热稳定性的影响。
2.伸长率
配合有填充剂的软质PVC伸长率比没有填充剂的低﹐其降低率随填充剂的种类不同有着很大差异。一般说来﹐粒子细的﹑增塑剂吸收量大的填充剂降低率大﹐粒子粗的﹑增塑剂吸收量小的填充剂降低率低。
3.硬度
软质PVC的硬度随着填充剂配合量的增加而增大。一般伸长率下降越大的填充剂其硬度的增高越大﹐即硬度和伸长率的变化呈相反关系。粒子细的﹑增塑剂吸收量大的填充剂﹐硬度的增长率大﹐反之﹐粒子粗的﹑增塑剂吸收量小的填充剂﹐硬度增长率小。在软质PVC制品大量使用的碳酸钍中﹐以重质碳酸钙的硬度增长率为最小﹐轻质碳酸钙次之。欲要抑制软质PVC制品因配合填充剂导致硬度增大﹐使其保持与无填充剂制品同样的硬度或柔软性﹐需要增加增塑剂的用量。增塑剂的用量究竟以多少为宜﹐应视具体情况而定。下表中列出配合各种填充剂的软质PVC中增塑剂的必要量。
4.耐寒性
耐寒性为软质PVC制品一个不可缺少的性能指针。填充剂对软质PVC耐寒性影响较小﹐一般随着填充剂配合量的增加而耐寒性降低。对增塑剂吸收量小的填充剂﹐对耐寒性影响较小﹐而炭黑﹑硬质陶土等吸收增塑剂较多的填充剂﹐则能相当的降低耐寒性。
5.撕裂强度
在填充剂配合量少﹐软质PVC的撕裂强度与无填充剂时相比变化不大﹐当填充剂配合量多达某一程度后﹐撕裂强度下降。高温下的撕裂强度显示不同的倾向﹐无一定之规。
6.耐水性
软质PVC中加入炭黑﹑碳酸钙时﹐吸水率几乎不变﹐但硅酸钙﹑高岭土等填充剂显示较大的吸水率。(高岭土不耐水,要求耐油或耐水配方不要使用高岭土)。
综上所述,填充剂的使用对体系的影响是全面的,在配方设计时应全面考虑,不可一味的追求低成本而盲目增加填充剂用量.
润滑剂(Lubricant)
第一节概述
润滑剂是一类用来改善塑料﹑橡胶等聚合物的加工性能和表观性能的助剂。除一般意义上的减少磨擦﹐提高树脂或胶料加工过程中的流动性和脱模性作用外﹐润滑剂的功能还可延伸到增加制品的表面光洁性﹑防止制品之间相互粘连等界面性能方面。就加工改性作用而言﹐润滑剂在聚合物加工过程主要降低树脂或胶料与加工设备之间和聚合物分子之间的相互磨擦﹐进而达到降低扭矩﹑节约能耗﹑促进流动和提高质量的目的。作为理想的润滑剂﹐一般及应当具备如下性能要求﹕
1.易分散性和其它助剂一样﹐润滑剂在聚合物中必须具有良好的分散性。如果润滑剂在树脂中分散性差﹐其结果导致熔体局部过润滑或欠润滑现象发生﹐熔体流动性不均﹐制品的形状或外观不良﹐甚至加工过程难以控制。
2.与基础聚合物适当的兼容性润滑剂与基础聚合物的兼容性对其性能发挥至关重要。如果兼容性过大﹐润滑剂在聚合物中起到增塑剂的作用﹐结果制品的软化点降低﹔如果兼容性极小或没有兼容性﹐往往在制品成型后容易产生喷霜现象。
3.良好的热稳定性和高度的润滑性润滑剂的结构稳定﹐在加工温度下不分解﹐不变色﹐挥发性较小﹐而且希望在较高温度范围内与树脂的兼容性随温度变化的梯度较小﹐以满足高温﹑高速加工条件下稳定操作的要求。
4.不影响制品的最终应用性能润滑剂属于加工改良剂的范畴﹐在改善制品加工性能抽时﹐力求不损害其力学和外观性能﹐如强度﹑热变性温度﹑透明性等。
5.不引起颜色的漂移﹐甚至改善颜料或填料在聚合物中的分散性。
6.无毒和卫生性。
7.配合成本较低。
第二节润滑剂的功能和作用
一﹑润滑剂的功能
就聚合物加工而言﹐磨擦主要包括聚合物树脂或胶料与加工机械表面和聚合物内部分子之间相互磨擦两方面的内容﹐即外部磨擦和内部磨擦。与之相对应﹐外部润滑作用用来减少外磨擦﹐内部润滑作用旨在降低内磨擦。具有外部磨擦作用的润滑剂称为外润滑剂﹐具有内部润滑作用的润滑剂称为内润滑剂。通过内外两种润滑作用﹐聚合物加工过程不仅可以防止树脂熔体或胶料粘附在加工机械表面﹐提高流体速率﹐降低剪切扭矩﹐节能降耗和增加产能﹐而且由于磨擦生热的降低能够有效的抑制树脂或胶料的降解﹐提高稳定剂的效率。对于一个完整的聚合物加工过程来说﹐内部润滑作用和外部润滑作用是不可分割的﹐理想的润滑剂应当同时兼备良好的内润滑性和外润滑性。通常内部滑与外部滑只是相对而言,无明确界限,内部滑剂略为增量便有外部滑性效果,外部滑剂相对材料也有内部滑性存在;选择时不必斤斤计较如何划分滑剂类别,应视加工设备、加工温度,以及材料配合剂的不同,适材适量才是要点.内滑用量过多时会渗析出来而推迟塑化时间;外滑剂过量时会导致物料对机筒打滑,容易出现不稳定流动,影响制质量量.
区 分 | 滑 性 | 用 途 |
内部滑剂 | 在加工温度能减少材料内部磨擦力,增加材料的流动性 | 透明用滑剂 |
外部滑剂 | 加工温度时材料与机器接着面间粘着防止 | 粘着防止剂 |
软化点以下温度与金属模具间的附着防止 | 内部离型剂 |
以PVC加工为例。PVC树脂与其它配合组分和配合体系首先在混料锅中进行充分混合﹐之后将其投入到押出机的喂料斗中。在押出螺杆旋转的推动作用﹐配合物由供料段向压缩段﹑计量段前进﹐伴随物料的行进过程﹐树脂开始熔融﹑混炼﹑直到最后押出成型。在整个成型工艺中﹐润滑剂一方面起到减少塑化物与押出机筒和螺杆表面之间的磨擦作用﹔另一方面又要承担减小塑化物内部分子之间相互磨擦的功能。如果润滑剂配合得当﹐则物料自供料段进入时即开始凝胶化﹐且在计量段前端完全凝胶化。相反如果配合不当﹐就会出现凝胶化不足或凝胶化过头的问题。凝胶化不足是指塑化不完全﹐其根本由于润滑剂太多﹐即“打滑”现象造成的。润滑剂太多时螺杆旋转所产生的剪切力在物料中不能充分传递﹐物料熔融混炼不均匀﹐其中包含部分尚未塑化的树脂或黏度不同的树脂熔体﹐这些均化的树脂熔体通过螺杆送入模塑部分必然影响制品的外观性能和力学性能。凝胶化过头反映体系中润滑剂不足的本质﹐由于内外润滑性不足﹐磨擦生热量大﹐所以在压缩段物料已经凝胶化﹐同时基于温度﹑黏度的进一步升高将会引起树脂的分散和变色。根据押出加工的特点﹐将润滑剂的润滑作用按阶段分为初期润滑效果﹑中期润滑效果和后期润滑效果等个部分。所谓初期润滑性是指从供料段到压缩段初期润滑剂所发挥润滑作用﹔中期润滑性是指从压缩段到计量段区间润滑剂发挥的润滑作用﹔面后期润滑性是指从计量段到模塑成型为止润滑剂所发挥的润滑作用。
润滑剂在聚合物加工中的作用往往表现为内润滑性和外润滑性﹐其功能和作用楞归纳为如下几个方面。
1.降低熔体黏度热塑性聚合物树脂熔体的黏度是表征其加工流动性的重要参数。一般随着加工温度的升高﹐熔体黏度降低﹐流动速率增加。对实际加工而言,由于受树脂热稳定性等因素的局限,加工温度不可能夫限度的升高,尤其是象PVC这样的热敏性树脂.而且依赖加工温度降低熔体黏度还会增加能耗,降低产量.除提高加工温度外﹐降低熔体黏度有选择较低分子量树脂的措施,但同时又会带来最终制品维卡温度和强度下降的问题.具有内润滑作用的润滑剂能够在较低配合量下改变树脂熔体的流变行为﹐达到降低熔体黏度﹐提高熔融流动性之目的。这是因为润滑剂分子与聚合物树脂在较高温度下具有一定的兼容性﹐进而插入聚合物分子链之间﹐削弱分子链间的作用力﹐促进高分子链之间的滑动和旋转﹔或者包覆于聚合物树脂初级微粒的表面﹐通过向名伸展的长碳链脂肪基改善PVC初级微粒间的相互滑动性。
2.减小内生热内生热即聚合物树脂内部的磨擦生热。对于高速成型工艺来讲﹐高剪切将使大量的机械能转化为热能﹐熔体黏度越大﹐剪切力越强﹐因此产生的内生热越多。内生热是导致树脂熔体局部过热﹑热稳定性下降的主要因素之一。借助于内润滑剂降低熔体黏度的途径固然能够在一定程度上减小内生热﹐但因此带来的低熔融黏度常常使注塑成型等加工难以进行﹐因为许多加工方式往往需要树脂熔体具有足够高的熔融黏度。考虑内生热是由熔体内部的磨擦引起的﹐如果润滑剂能够赋予树脂内部结构单元足够高的润滑性﹐同时又对聚合物溶剂化作用极小﹐就可以通过减少树脂内部界面的磨擦生热或将已产生的内生热尽快散逸而提高加工稳定性﹐也避免了熔融黏度的降低和制品热变形温度下降等问题。
3.脱模作用聚合物树脂熔体对加工机械金属表面的粘着性在制品加工成型的不同阶段具有不同的意义。在树脂塑化阶段﹐熔体对加工机械表面的粘着性有助于树脂微粒的打开﹐能够促进熔融﹔在制品成型后期﹐这种粘着性往往容易导致制品表面均匀剥离困难﹐甚至造成表观性能的损坏。脱模作用是润滑剂外润滑性具体表现﹐具有脱模作用的润滑剂多是极性化合物﹐它们与树脂兼容性有限﹐能够从熔体迁移到表面﹐极性基团与金属表面具有一定的亲和性。﹐这样在熔体和金属表面之间形成一层相对稳定﹑互为隔离的分子层﹐因此抑制聚合物熔体与加工机械表面之间的粘着。对于极性树脂而言﹐非极性的烃蜡类化合物也具有脱模作用﹐但由于与金属表面之间缺乏亲和性﹐脱模效果一般。聚乙烯蜡属于非极性烃类润滑剂。
4. 延迟塑化作用延迟塑化作用是外润滑性在塑料加工中的另一种表现形式。在PVC加工中﹐PVC树脂是在剪切形变作用下熔融并与各种助剂均匀混合的﹐在具体情况下对树脂熔融的要求并不一致。例如在成型过程的初级阶段往往并不希望树脂微粒过早熔化﹐有时为了获得最终制品的最佳力学性能并不要求树脂完全熔融﹐这在高抗冲聚氯乙烯加工中表面的尤其明显。通过在树脂中配合兼容性较低的润滑剂﹐可以在加工温度下迁移到树脂微粒或熔体表面﹐从而在树脂微粒或熔体表面与加工机械金属表面形成润滑层﹐使之产生良好的滑动﹐削弱剪切变形作用﹐达到延缓树脂塑化的目的。
5.防止熔体破裂在高速剪切速率下的高黏度会导致所谓熔体破裂的表面现象﹐这是因为押出物质在流道内经历规则的粘附/滑动转变。
6.改善制品的自润滑性许多塑料制品要求有很好的表面润滑效果﹐例如齿轮﹐具有外润滑效果的润滑剂往往可以通过向制品表面的迁移或渗出形成自润滑层同﹐产生永久的润滑作用。
7.爽滑和防粘连作用对于比表面积较大的塑料制品﹐表面粘连往往会给其生产或应用带来诸多困难﹐许多具有外润滑作用的润滑剂向制品表面迁移较大﹐而且冷却后能够形成一个分布均匀的薄涂层﹐由于两个界面插入隔离层﹐因此既赋予制品的表面滑动性﹐又不致造成表面粗糙﹐这种功能助剂称为爽滑剂。
二﹑润滑剂的作用机理
1.内润滑剂的塑化或软化机理
内润滑剂的主要功能是削弱聚合物熔体内部分子间的相互磨擦﹐降低内生热和改善熔融流动性﹐这就要求润滑剂与聚合物树脂必须具有一定兼容性﹐能够在熔融状态下插入聚合物分子间﹐削弱其分子间相互作用﹐相当于增塑作用。考虑到内润滑剂对制品最终热变形温度的影响﹐内润滑剂对树脂熔体的增塑作用只有在熔融状态下才能显示出来﹐因此与增塑剂相比﹐内润滑剂一般极性较低﹑兼容性有限﹐结构中的碳链较长。
2.外润滑剂的界面润滑理论
聚合物加工过程的外润滑功能主要体现在树脂微粒﹑熔体表面加工机械的金属表面﹐润滑剂通常附着在树脂微粒表面﹑熔体表面﹑加工机械表面和模具表面﹐形成一层润滑剂的分子层﹐这是由于润滑剂分子层存在在树脂微粒之间和聚合物熔体与加工设备之间形成一个润滑界面﹐结果降低了熔融前树脂粒子与机械表面之间和熔融后树脂熔本与加工机械表面之间的磨擦。例如当使用脂肪酸类化合物作为PVC加工润滑剂时﹐在高温下脂肪酸与活性金属表面反应﹐结果所生成相应金属皂膜附在金属表面上﹐而且这种金属皂膜的熔点远远高于对就的脂肪酸熔点﹐因此即使在较高的加工温度下仍然显示良好的润滑性。
第三节润滑剂的分类和性质
一﹑润滑剂的分类
1. 润滑剂的化学结构分类方法
(1)烃类化合物液体石蜡﹑天然石蜡﹑微晶石蜡﹑聚乙烯蜡(低分子量聚乙烯)﹑氧化聚乙烯蜡和卤化烃等﹔
(2)脂肪酸类化合物 高级脂肪酸﹑羟基脂肪酸等﹔
(3)脂肪酸皂类化合物硬脂酸钙﹑硬脂酸锌﹑硬脂酸铅﹑褐煤蜡酸钙等﹔
(4)脂肪胺类化合物高级脂肪铣胺和亚烷基高级脂肪酸双铣胺﹔
(5)脂肪酸酯类化合物 高级脂肪酸的高碳醇酯和低碳醇酯﹐高级脂肪酸的多元醇酯﹔
(6)高级脂肪醇类化合物如硬酯醇等。
(7)聚硅氧烷类化合物 主要用作外脱模剂﹔
(8)复合润滑剂由不同类型化合物复配而成的润滑剂品种。
2.润滑剂绵作用方式分类方法
润滑剂依其作用功能可以分为内润滑剂﹑外润滑剂﹑脱模剂和爽滑剂等。作为聚合物加工润滑剂﹐内润滑剂和外润滑剂只是功能上的定性分类﹐两者之间并无严格的界限可言﹐一方面一种润滑剂在一种结构的聚合物中可能显示内润滑性﹐在另一种结构的聚合物中可能显示外润滑性﹔另一方面即使是在同一种润滑剂应用顼一种结构的聚合物中往往同时兼备内润滑性和外润滑性。
对PVC而言的润滑剂之润滑性顺序
二﹑润滑剂结构与功能关系
润滑剂化学结构对润滑性能具有如下的几个方面的影响;
(1)脂肪链影响显著﹐具有12个碳原子以上的脂肪链就显示出润滑性
(2)脂肪链的长度与结构脂肪基碳链越长﹐极性越小﹐其与极性聚合物树脂的兼容性越低﹐外润滑倾向越强。作为润滑剂﹐通常希望长链的脂肪基结构是直链接构﹐因为支链化结构的存在并不利于润滑界面的形成﹐而作为内润滑剂使用时﹐支链化将促进树脂的塑化﹐其结果可能导致制品维卡温度的降低。
(3)润滑剂的极性基团极性基团在树脂表面具有取向作用﹐有助于在聚合物树脂粒子或熔体表面形成润滑界面。
(4)脂肪铣胺的爽滑作用。
(5)氟聚合物LLDPE的专润滑剂。
三﹑润滑剂各论
1.烃类润滑剂
烃类润滑剂包括液体石蜡﹑天然石蜡﹑微晶石蜡﹑聚乙烯蜡(低分子量聚乙烯)﹑氧化聚乙烯蜡和卤化烃等。它们润滑效率较高﹐具有内外两种润滑性﹐但一般与PVC兼容性差﹐多数表现为外润滑性。在押出工艺世中﹐它们的初期润滑性和后期润滑性差﹐中期润滑性显著。
(1)液体石蜡液体石蜡是石油裂解产物﹐俗称“白油”或“矿物油”﹐凝固点为-15oC_-35oC的液体石蜡在PVC加工和注射成型中广泛用作内润滑剂﹐由于其与树脂的兼容性较差﹐因此添加量受到限制﹐用量一般以0.3---0.5phr为宜。在押出工艺中﹐液体石蜡的初期润滑性较好﹐且不影响热稳定性。
(2)天然石蜡在PVC硬制品加工中呈外润滑性﹐特别适用于改进押出物的表面平滑性﹐其降低熔融前树脂微粒之间磨擦﹐延缓树脂熔融的作用随分子量的增加而提高。
(3)微晶石蜡微晶石蜡是石油的产物﹐碳原子数为32---72。其对PVC的润滑效果突出﹐热稳定性好﹐尤其是具有高硬脂酸钙的稳定体系中﹐支链化的微晶石蜡较直链烃蜡的效果为优﹐其原因归根于支链化增加了它们与树脂的兼容性﹐在不析出的前提下能够经较高的用量添加到树脂中﹐为了弥补微晶石蜡在PVC押出工艺中初期润滑性和后期润滑性的不足﹐最好在配方设计时与硬脂酸丁酯﹑酯蜡和高级脂肪酸并用。
(4)聚乙烯蜡聚乙烯蜡是指分子量在1000-2500之间的低分子量聚乙烯。一般由高分子量的聚乙烯树脂热解或由乙烯聚合工艺合成而得。聚乙烯蜡化学性质稳定﹐电性能优良﹐与PVC等级性树脂的兼容性差﹐呈外润滑性。在PVC加工中﹐聚乙烯蜡以减小熔融前树脂微粒间的磨擦﹑调节塑化时间和提高制品表面光洁性为主要功能。由于聚乙烯蜡与PVC树脂的兼容性极小﹐因此添加量大有影响制品透明性的倾向。只有较高分子量和较高结晶度的聚乙烯蜡能够赋予制品良好的透明性﹐可以用于透明制品的加工。
(5)氧化聚乙烯蜡氧化聚乙烯蜡是聚乙烯蜡氧化的产物。与相应的聚乙烯蜡相比﹐氧化聚乙烯蜡的极性增加﹐因而和PVC等极性聚合物树脂的兼容性得以改善。氧化聚乙烯蜡在PVC加工中呈现外润滑特征﹐由于其极性基团对金属表面具有良好的亲和性﹐因此脱模效果非常突出﹐而且基本不影响制品的透明度。
(6) 氯化石蜡氯化石蜡属于卤代烃类润滑剂﹐与PVC树脂相容好﹐呈中等润滑性﹐初期和后期润滑性不足﹐必须与其它润滑剂并用。为了不损害制品的透明性﹐其用量通常控制在0.3phr以下。
2.脂肪酸类润滑剂
脂肪酸类润滑剂包括饱合脂肪酸﹑不饱合脂肪酸和羟基脂肪酸类化合物等。
(1)饱合脂肪酸碳原子类达到12个以上饱合脂肪酸都具有润滑性。饱合脂肪酸润滑剂主要包括硬酯酸﹑软酯酸和花生酸等。一般由相应的油酯氢化水解而得。作为PVC硬制品加工用润滑剂﹐随碳链长度的增加﹐润滑性能由内向外转变。硬酯酸呈内外润滑性﹐并倾向于内润滑。饱合脂肪酸类润滑剂一般以碘值和皂化值低者为优﹐这对提高制品的耐热性和耐候性大有裨益。
(2)不饱合脂肪酸类化合物不饱合脂肪酸类润滑剂的重要品种是油酸﹐由于结构中含有不饱合双链﹐易氧化变色﹐且有导致制品维卡温度降低的倾向。
(3)羟基脂肪酸类化合物羟基脂肪酸类化合物润滑剂挥发性较硬酯酸为低﹐由于结构中羟基的存在﹐使基极性增强﹐因此与PVC等极性树脂兼容性好﹐显示出内润滑作用﹐但热稳定性较差。
3.脂肪酸皂类润滑剂
高级脂肪酸的金属盐类化合物俗称金属皂。脂肪酸皂类润滑剂的润滑作用随金属种类和脂肪酸根的种类不同而异。就同一种金属而言﹐脂肪酸根的碳链越长(即金属含量越低)﹐润滑效果越好。硬酯酸钙在PVC加工中是典型的内润滑剂﹐硬酯酸铅是良好的外润滑剂。
4.复合润滑剂
对于PVC加工而言﹐任何一种结构的润滑剂都不可能同时满足内润滑性与外润滑性和初期润滑性﹑中期润滑性与后期润滑性的完全平衡﹐而将具有不同润滑功能和行为的润滑剂组分配合在一起﹐使之形成能够满足加工工艺要求的完整润滑体系是润滑剂品种开发之有效途径。此外还可以将润滑剂与稳定剂进行复合﹐形成润滑—稳定“一包装”(onepackage)产品。一方面﹐润滑剂与稳定剂之间的配合具有协同作用﹐尤其是分子内磨擦的降低有效的减少内生热﹐这有利于减少热稳定剂的配合量﹐对于复合铅盐稳定剂来说可以相对降低铅含量﹔另一方面﹐润滑剂多为油脂化学品﹐它们在铅盐等复合稳定剂中有粘接剂的作用﹐有助于防止稳定剂组分在生产﹑配合中的粉尘飞扬。
第四节润滑剂的应用
一﹑润滑剂的选择
润滑剂在热塑性聚合物加工中对于制品加工和应用性能的改善具有非常重要的作用。然后由于聚合物加工过程十分复杂﹐影响润滑作用颇多﹐诸如聚合物的结构﹑加工机械﹑成型方法﹑加工条件﹑制品形状﹑复合组分之间相互影响等﹐同时考虑到最终制品所要求的性能﹐因此方设计时润滑体系的选择必须从整个配方出发综合各种因素全盘考虑。以下是PVCl加工成型时润滑剂的选用要点﹕
(1)加工机械压延加工重点放在外部润滑性上﹐押出﹑注射成型时重点放在内部润滑性上。
(2)树脂种类和均聚物相比﹐共聚物要多用一些外部润滑剂。
(3)配合剂的种类和用量
1.增塑剂和软制品相比﹐硬制品要增加润滑剂的用量
2.需要注意稳定剂本身的润滑性﹐其润滑性顺序为﹕含硫有机锡<有机锡<无机稳定剂<液体复合稳定剂<金属皂。含硫有机锡在配方中需要与外部润滑剂并用﹔有机锡需要与外部润滑剂或内外润滑剂并用﹔无机稳定剂和液体复合稳定剂需要与内外润滑剂并用﹐金属皂需要与外部润滑剂并用。
3.填充剂填充剂用量大时﹐要多用内部润滑剂。
4.注意内部润滑性与外部润滑性的平衡。
(4)制品所要求的性能
外观上要考虑喷霜﹑颜色漂移﹑迁移性等。表面性应考虑印刷性﹑光泽性等。机械强度应考虑强度﹑层间剥削性等。
二﹑PVC加工用润滑剂
聚氯乙烯润滑剂的选择首先依据其相应的稳定体系和加工方式而确定。对于押塑﹑压延﹑注塑等成型工艺来讲﹐润滑剂的工艺必须满足其相应的剪切速度范围和某些特定的要求﹐诸如熔体的流动﹑防止设备表面粘附﹑延缓树脂塑化等﹐并且必须考虑到配方体系中润滑剂与其它组分之间的相互作用。稳定体系对润滑剂的选择亦相当重要。钙锌稳定体系是目前取代重金属稳定剂的重要类型﹐但一般来讲其热稳定效率低﹐内润滑剂将有助于降低PVC树脂分子间磨擦﹐减少内生热﹐提高热稳定效率﹐因此需要配合较为大量的脂肪酸多元醇等内润滑剂﹐与之相对应的外润滑剂主要是部分皂化的褐煤蜡和复合酯类外润滑剂。为了改善脱模性﹐可适当使用氧化聚乙烯蜡。透明PVC制品的抗冲改性剂﹐一般对具有脱模作用的润滑剂具有溶胀作用﹐因此需要增加润滑剂的添加量﹐而且不会发生原本在这个浓度下可能出现的浊化现象。在增塑PVC中﹐增塑剂能够赋予树脂熔体良好的流动性﹐含皂稳定剂组分可提供必要脱模润滑作用﹐如果添加0.2%--0.5%浓度的硬脂酸的氧化聚乙烯蜡﹐则脱模作用更加显著。
电线电缆料的加工通常需要使用较大量的石蜡和聚乙烯蜡(PE-WAX)﹐以改善其表面光洁度和脱模性﹐并增加押出速度﹑提高生产效率。对于高速押出的薄壁电线绝缘层的加工﹐有时还需要配合褐煤蜡酯。
五﹑滑剂列表
填充剂类型 | 本厂所用牌号及等级 | 主要性能 |
硬脂酸 | H-ST | 内部滑剂,具内外滑性. |
聚乙烯蜡 | A-C307A/PE-WAX | 外部滑剂,具内外滑性. |
硬酯酸正丁酯 | BU-ST | 与PVC兼容性好,具有良好的内润滑性和初期润滑性,不影响制品的透明性,但中后期润滑性差,与硬酯酸配合使用能够进一步提高润滑效能. |
硬酯酸锌 | ZN-ST | 内部滑剂,兼具稳定剂作用.可提高制品初期稳定性与润滑性.用量不宜过大,否则易有”锌烧” |
环氧化大豆油 | B-22 | 内部滑剂,但润滑效果一般.可用做稳定剂与增塑剂. |
着色剂和配色(Pigment&Colormatching)
第一节 概述
凡用以改变塑料﹑橡胶等聚合物制品固有颜色的物质均称为着色剂。一般用于塑料着色剂主要有无面颜料﹑有机颜料和染料。以下是三大色料的比较。
从性能上比较﹐虽然有机颜料在耐热性﹑耐候性和遮盖力方面不如无机颜料﹐但具有相对密度小﹐吸油量大﹑色泽鲜艳和色谱齐全的特点。
一﹑颜色的基本概念
物体的颜色和光分不开的﹐颜色是大脑对投射在视网膜上不同性质光线进行辨认的结果。光是一种电磁波﹐可以用波长来表示。人眼可以察觉的兴是可见光﹐波长从380-780nm。物体在光照射下之所以所呈现不同的颜色是因为与它对光波的吸收和反射特性相关。在日光的照射下﹐如果物体同等的吸收整个可见光波长的光线﹐就是黑色﹔如果同等的反射整个可见光波长就是白色﹔如果吸收可见光的一部分﹐而反射或透过其余的光线﹐就呈现彩色。用着色剂来改变物体的颜色﹐实际就是改变物体固有的吸收和反射波的特性。
颜色分为彩色和非彩色两种。非彩色就是通常所讲的黑白色。彩色指非彩色以外的各种颜色。颜色有3种视觉属性﹕色调﹑饱合度和亮度。色调又称色相﹐它是颜色的基本特征﹐用以区分颜色的视觉特性﹐取决于颜色光源的光谱组成及物体表面对可见光的反射比例。饱合度又称色度﹐是指彩色的纯洁性﹐如单色的可见光是最饱合的彩色﹐掺入白光的成分越多就越不饱合﹐也就是指颜色的深浅﹐即淡﹑浓。饱合度取决于颜料表面对光的反射选择程度。若对某一很窄波段的光有很高的反射率﹐而对其余波长的光反射率很低﹐则说明其反射选择程度高﹐颜色的选择度也高。高度又称色值﹐指色彩的明暗程度﹐是人的视觉对物体反射光强度的感觉。
二﹑着色胶料的光学性能
第二章着色用颜料的主要性能
一着色力
颜料的着色力(Tintingstrength)是指某一定颜色颜色制品所需的颜料量,用标准样品着色力的百分数来表示.即取1g标样,加入A克白色颜料(钛白),调配成一定颜色的混合物;然后取1g待测颜料,加入白色颜料调配,直到在标准光源下,观察到的颜色与标准样品混合物相同时,设此时所用的白色颜料为B克.则此种颜料的着色力I=B/A*100%.此种着色力计算方法不准确,不能用于测试高着色力的有机颜料的着色力.
颜料的着色力不仅仅与其性质有关,而且还与颜料的分散程度与关.分散程度主要是指颜料细化程度,分散程度越大,其着色力越高,但有一个极大值,超过此值着色力迅速下降,例如偶氮类颜料粒径在0.1μm为其极值.
二 耐热性
塑料用的颜料的耐热性是指其在加工和使用温度下颜料的颜色或性能变化程度.在PVC和PE中颜料至少应该能耐180度高温.在ABS和PS中需要耐250-280度,PP、PA和PET中则需要耐280度以上。因塑料在加工成制品时,加工方法不同,受热时间不同;在使用的用途中,用途不同,受热时间也不同,所以要求颜料耐热时间至少为4-10分锺。通常温度上升,耐热时间减少。
颜料的耐热温度及耐热时间的检测方法有以下几种:
1.着色塑料在180度下分别塑炼5、10、15和20分锺,观察其色调的变化。
2.着色塑料分别在160、180、200、220度下塑炼五分锺,比较其色调的变化。
3.着色塑料用柱塞式注塑机,分别在180度、230度、250度、280度的温度下,注塑周期为10分锺,观察其色泽变化。或色差ΔE=3时的温度称之为耐热温度。
以上试样与GB250-84灰色样卡对比,第五级为最好。
颜料的耐热性也可以用热失重测定,热失重越小耐热性越好。
三 耐迁移性
颜料的耐迁移性是指着色塑料制品与其它固液气等状态物质长期接触或者在某种特定环境下工作,有可能和上述物质发生物理和化学反应,表现为颜料从塑料内部迁移到制品自由表面上,或迁移到相邻的塑料或溶剂中。着色塑料中的颜料的迁移性和塑料材料分子链的刚性和分子间的紧密性相关。当塑料中增塑剂用量增加时,分子距离加大,结构更为松散,因而减少了聚合物链的相互作用,从而使颜料迁移速率增大。PVC颜料迁移性测试方法如下:
用100PHR的PVC、65PHR的DOP,两分的安定剂和1PHR的待测颜料制片,同样取得未着色的PVC片,并使两片接触,放入恒温恒湿烘箱,此两片材在70度湿度70%下放置72小时,根据未着色的PVC的污染情况,具体分为五级。GB251-84对此有规定,一级是最差的,五级是最好的(无迁移)。PVC用颜料对迁移性要求是最高的。
四耐旋光性和耐候性
某些颜料在光的照射下,颜色会有不同程度的变化。无机颜料大多数耐旋光性好,仅有少数品种在受光照后,因其晶型或化学组成发生了变化而变暗。有机颜料光照后,会引起颜料分子构型的变化等原因而影响饱合度下降,甚至会褪色成灰色或白色。
ISO规定,以一种标准的蓝色颜料(一般用Victoriablue)受氙灯照射,用其颜色变化来确定耐光牢度的等级.称ISO蓝色牢度
氙灯照射的耐光牢度ISO的蓝色标准
耐光牢度等级12345678
开始褪色的照射时间h484080140200340 700-800
耐候性是指颜料在大自然条件下的颜色稳定性,一般把样品色片放在室外倾角45度正面朝南,定期进行对比测试观察其颜色变化.耐候性GB与ISO都是分为五级,国内多拿到广州市晒场来确定耐候等级.国际上则以悉尼邻海晒场为准.
五 耐化学药品性
着色塑料制品中颜料的耐化学药品性应包括耐酸碱性、树脂的分解产物,制品中其它的助剂,如抗氧剂、分散剂等。
六 毒性
一般包括重金属、偶氮、二恶英等。
七混合性
塑料制品着色时往往采用两种以上颜料配色,因此必须了解它们之间的混合性能,同时还需要了解颜料是否与塑料中的助剂是否起化学反应。
凡含有Cu或Pb的颜料与含S的颜料混合后,颜色会变暗黑色,这是因为生成了CuS或PbS的原因,含铬的颜料通常含铅,因此不能与PP中的热稳定剂硫化二丙酸二月桂酸酯DLTDP和硫化二苯酚之类的含硫稳定剂一起作用,以免生成PbS变黑。
某些色淀、偶氮类有机颜料与铬黄混合后,红色会渐渐减退,是因为铬黄中的铬酸根具有强氧化性,能使有机颜料氧化降解或发生其它变化而变黑。
八遮盖力
着色剂的遮盖力是指其遮盖物体表面底色的能力,遮盖力可以用数值来表示,即底色完全被遮盖时单位面积所需要的着色剂的克数,单位面积一般为平方米,所需要克数越小遮盖力越大。着色剂中的无机颜料遮盖力最大,而染料具有透明性而无遮盖力,要与染料具有遮盖力,一般与钛白粉相混合即可。一种着色剂的遮盖力与下列因素有关:
1.吸光特性一般着色剂的吸光能力越强,其遮盖力也越大,如炭黑可吸收全部用射光,其遮盖力极大。
2.折射率的差别 着色剂的折射率与树脂的射率相差越大,则着色剂对树脂的遮盖力越大。
3.粒度着色剂粒度越大,其遮盖力越大。粒度对遮盖力的影响同着色力一样,有一个极限值,超过此极限值反而下降,一般着色剂的粒度在0.1-1μm为最佳.
4.晶型 (1)结晶度高遮盖力大.(2)晶型呈片状比棒状遮盖力大. (3)分子结构对称性较高比对称性较低的晶型遮盖力低.
九 分散度
着色剂的分散度是指其在树脂中的分散均匀程度,分散度对着色质量、色彩、色素等影响较大。