其实我们(www.yunhewj.com)都知道 PCB导线是通过化学五金蚀刻而形成的。由于蚀刻液是从露铜表面开始向内部(或下面)逐步进行蚀刻的,所以向内部(下面)垂直腐蚀的同时,也向侧面铜箔进行水平腐蚀,形成所谓的腐蚀侧蚀现象。
为了定量比较蚀刻线的蚀刻质(侧蚀大小), 我们定义了蚀刻因子,用其作为定量衡量蚀刻质量和蚀刻线蚀刻能力的指标。然而,对于蚀刻因子的实际计算却一直存在多种理解,本文在理论与试验相结合的基础上,对蚀刻因子的不同计算方法进行了探讨,并提出了对五金蚀刻因子计算方法的一点看法。
1.五金蚀刻因子计算方法1
1 .计算公式
方法1是部分人对蚀刻因子的理解结果,计算法是以蚀刻过程完成后蚀刻线的上线宽和下线宽为计算依据的,具体计算公式如下:蚀刻因子=蚀刻线厚/f(下线宽.上线宽)/2】蚀刻因子计算方法1
1.2 计算方法分析
由于设备和操作等因素的影响,蚀刻过程通常会呈现三种可能状态:蚀刻不足、正常蚀刻和过度蚀刻。正常蚀刻状态(理想状态)是指蚀刻后蚀刻下线宽与蚀刻抗蚀层宽度相等的状态,此时按方法1公式计算出的蚀刻因子为理想蚀刻因子,可以真实反映蚀刻线的蚀刻能力。但是,对于我们实际蚀刻过程中经常出现蚀刻不足或过度蚀刻(过蚀较常见,以此为例),如仍使用方法1计算就会造成蚀刻因子的计算偏差。分析偏差原因可知:从蚀刻到露基材起,蚀刻线路后续形成过程中,由于线路上表面有抗蚀层的保护,不易受药水侵蚀,药水交换不好,所以蚀刻反应速率比较慢;而线路下表面与药水充分接触,交换很好,所以蚀刻反应速率比较快。随着蚀刻的进行,上下线宽之间的线宽差异(下线宽.上线宽)慢慢缩小,在过蚀情况下,如果仍然使用方法1的公式计算,相当于减小了上下线宽之差,也就等同于“提高”了蚀刻因子。而且过蚀越严重, 上下线宽差异就越小, 以致“蚀刻因子”也就越大。
五金蚀刻的三种状态本文试验分析了不同铜厚板(0.5oz、loz、2oz)蚀刻后的蚀刻因子。使用方法1计算,试验结果显示:过蚀越多,蚀刻因子越大。对于正常蚀刻的0.5oz薄铜板计算蚀刻因子为2.5,而过度蚀刻的厚铜板(1OZ和2oz)蚀刻因子高达5.6和6.0,差异很大,这与业界经验:蚀刻因子一般在2—4之间(参见《高密度封装基板》)相悖;同时, 如果此结论成立,反推过来, 提高蚀刻线能力(得到大的蚀刻因子)只需严重过蚀即可,这不符合常理,所以方法1存在很大的局限性,只能用于正常蚀刻状态。
2 蚀刻因子计算方法2
2.1 l pC标准概念(J PC一600G)
蚀刻因子是指垂直蚀刻深度与横向侧蚀宽度(侧蚀量) 两者之间的比值(如图3(1))。侧蚀是指导线每侧平行板面的最外缘(含抗蚀层)与导线内缩后的最内缘对比时两缘之空间距离。
2.2 计算方法分析
在IPC标准概念的理解基础上,计算方法2的
公式应为:
蚀刻因子=蚀刻线厚,【(抗蚀层宽度一最窄线宽)12】。结合文献资料可知:使用方法2计算蚀刻因子涵盖了蚀刻过程的三种状态是:过度蚀刻、正常蚀刻和蚀刻不足。IPC标准中蚀刻因子的计算示图显示的是轻微过度蚀刻时的状态:《高密度封装基板》中蚀刻因子的计算示图显示的是正常蚀刻的状态;而《现代印制电路原理与工艺》对于蚀刻因子的计算示图显示的是轻微蚀刻不足的状态。
摘录蚀刻因子计算方法示意图对上述同一试验,使用方法2来计算蚀刻因子,试验结果显示: 正常蚀刻的薄铜板蚀刻因子为
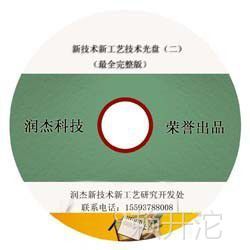
2.7,而过度蚀刻的厚铜板蚀刻因子分别为2_3和2.0,差异较小,且蚀刻因子都在24之间,符合业界经验。试验证明:在保证线宽,间距要求和蚀刻线质量的前提下,使用方法2计算出的不同蚀刻状态下
的蚀刻因子能够近似反映蚀刻线的蚀刻能力。而正常蚀刻状态是一种理想状态,在此状态下计算的蚀
刻因子最能真实的反映蚀刻线的蚀刻能力。故建议蚀刻因子的计算前提最好是在正常蚀刻状态下。此外,摘录蚀刻因子计算示图中均假想线宽横截面呈梯形(最常见),此时线宽最窄处为上线宽侧蚀量= (抗蚀层宽度.上线宽),2而在实际生产中,线宽横截面不全是梯形, 可能斜边会有一定弧度,此时线宽最窄处就不是上线宽,而是线宽腰部两弧度之间的最小距离(图4):而当线宽横截面出现倒梯形,此时的线宽最窄处就是下线宽了。故应根据具体情况, 灵活运用公式。