FMEA的历史和几个实施中的误区
深圳市智杰科技信息有限公司资深管理咨询顾问 苏铁军
FMEA(Failure Mode EffectAnalysis——故障模式影响分析)是最常用的一种设计分析方法和质量管理工具,在多个行业(如军工行业、通讯行业、汽车行业)和多个专业领域(如可靠性管理、质量管理、风险管理)都能看到FMEA的身影。
FMEA由两部分工作构成,即故障模式影响分析(FMEA---Failure Mode and EffectAnalysis)和危害性分析(CA---CriticalityAnalysis)。实践中一般统称FMEA,有人将其发音为“飞吗”。
FMEA起源于美国。50年代初,美国格鲁门飞机公司在研制飞机主操纵系统时采用了FMEA方法,当时只进行了故障模式影响分析,而未进行危害性分析,但取得了良好的效果。60年代初,美国NASA(NationalAeronautics and SpaceAdministration)将FMEA用于航天飞行器,取得很好的效果。到了60年代后期和70年代初期,FMEA方法开始广泛地应用于航空、航天、舰船、兵器等军用系统的设计研制中,并逐渐渗透到机械、汽车、医疗设备等民用工业领域,取得显著的效果。70年代,美军标MIL-STD-1629(《实施故障模式影响及危害性分析的程序》)颁布,1984年该军标的改进版MIL-STD-1629A/notice2颁布,其中明确规定了对系统进行FMEA的基本方法。
国内在80年代初期,随着可靠性技术在工程中的应用,FMEA的概念和方法也逐渐被接受。1985年10月,国防科工委颁发的《航空技术装备寿命和可靠性工作暂行规定(试用)》中肯定了FMEA的重要性。1985年和1992年我国相继颁布了进行FMEA和FMECA的国家标准(GB7826)和国家军用标准(GJB1391)。目前在航空、航天、兵器、舰船等军工领域,FMEA方法均获得了一定程度的普及,为保证军工产品的可靠性发挥了重要作用。
在民用领域,FMEA应用得更广泛,特别是在台资企业。随着人员交流,FMEA方法也逐渐被其它民营企业接受和应用。
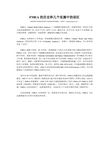
但FMEA方法在工程实践中也存在一些误区,例如:
1、做FMEA只是为了满足认证要求或者客户检查,或者应付流程规范的要求,而没有真正对设计产生促进作用。
2、分析质量低,包括分析不全面和不深入,这使得FMEA结果不受信任,加剧了“分析质量不高——没有人看——对设计没有帮助——更不重视这项工作”的恶性循环。
3、 版本升级不及时,不能和设计同步进行。
如果不能很好的解决上述问题,FMEA就成了企业可靠性管理和质量管理工作中的“鸡肋”,最终的结果是劳民伤财,没有实际效果,而且损害了FMEA的声誉。
对于企业如何应用好FMEA,深圳市智杰科技信息有限公司的资深顾问给出如下建议:
l坚持“谁设计、谁分析”的原则。FMEA是设计过程的一部分,设计者对设计最了解,因而也就对可能的故障及影响最有发言权。FMEA必须是由设计者亲自进行分析,而不能把FMEA作为一项独立工作或者“不得不”做的工作,安排一些“边缘”岗位进行。当然设计者可能对FMEA方法本身不是很熟悉,需要可靠性人员进行辅导,甚至组成FMEA小组共同进行分析,但主导者和主要负责人一定是设计人员。
l在项目开发流程中,把FMEA和设计进程紧密结合起来。设计更新升版,FMEA也要及时进行相应的更新升版,把FMEA纳入到每个环节的重要评审活动中,真正把FMEA变成设计工作的一部分,真正起到保证设计质量的作用。
深圳市智杰科技信息有限公司的资深顾问在可靠性设计分析和质量管理领域有多年的企业实践经验,可以在FMEA方法应用上提供专业的指导和咨询服务。