二氧化硫的控制方法很多。通常分为:
1.燃烧前脱硫:通过选煤的方法脱除煤中的部分硫份,降低煤中的含硫量。
2.燃烧中脱硫:是在煤的燃烧过程中减少二氧化硫的排放量,例如在循环流化床锅炉中加入石灰石可以降低烟气二氧化硫的排放量。
3.燃烧后脱硫:即烟气脱硫技术,是通过对烟气的处理。如吸收、洗涤等方法降低烟气中的二氧化硫排放浓度的技术。由于脱硫效率高、对燃煤电厂的生产工艺影响小等原因,烟氧脱硫是目前能适应排放限制、应用最广泛的技术。
烟气脱硫:(Flue GasDesulfurization,简称FGD)技术发展至今,已有几十年以上的历史,FGD技术得到了长足的发。根据美国EPRI(电力研究院)的统计,大约有300种不同流程的FGD工艺进行了小试或工业性试验,但最终被证实在技术上可行、经常上合理并且是可承担的、目前在燃煤电厂得到采用的成熟技术仅约十多种。这些工艺已基本解决了结垢、腐蚀和堵塞等问题,基建投资和运行维护价格低、可靠性高,被西方工业国家广泛应用。
由于污染控制和治理所需费用比较昂贵,我国在1991年曾经颁布实施了工业燃煤锅炉SO2排放标准,但没有以实用的治理技术为基础,因此在实施后多年的现在,工业燃煤锅炉的SO2排放问题仍然没有好转。
我国于1989年颁布了“环境保护法”,并逐步颁布了大气污染物的排放控制标准。适用燃煤电厂的标准是1991年的GB13223-91“火电厂大气污染物排放标准”。1995年对该标准作了修订,形成了GB13223-96“火电厂大气污染物排放标准”,并于1996年1月1日起实施。我国现行的大气污染物排放标准体系以国标形式由综合性排放标准与行业性排放标准组成,实行不交叉执行的原则。同时结合国函[1998]5号文《国务院关于酸雨控制区和二氧化硫污染控制区有关问题的批复》对“两控区”的精神。“两控区”内燃煤电厂执行排放总量控制和GB13223-96《火电厂大气污染排放标准》的限制。总量控制由地方环保局依划分份额规定电厂的年排放总量,同时执行标准限制值。排放标准把新建和现有机组划分为三个时段(表2.3-1),执行不同的标准限制。第一、第二时段以烟囱有效高度和烟囱出口环境风速计算的二氧化硫计算排放率为限制值。第三时段新建机组实行排放率和排放浓度的综合限制。为促使燃煤含硫大于1%的机组采用FGD装置,对其浓度限制为1200mg/m3,而小于1%的机组浓度为2100 mg/m3。
我国燃煤电厂SO2排放标准的发展的预测
每个国家排放标准条款的建立和发展,必须以逐步改善环境质量为前提,同时又要符合本国国情以及考虑经济上可承担的实际能力。控制SO2排放是改善大气质量的重要方面,而实施SO2排放控制和治理的计划必须投入大量资金和人力。为了达到促进经济可持续发展的目的,同时考虑二氧化硫控制技术发展的循序渐进性,各国标准基本体现了一个原则:先宽后严,逐步发展:对新建和现有电厂区别对待;对大型机组和小型机组区别对待;逐步向高标准发展。
我国二氧化硫排放标准同样具有类似特点,与发达国家相比有两个特点:一是标准颁布的时间不长,二是标准要求不低。从1989年正式颁布“环境保护法”,1991年颁布针对燃煤电厂的排放标准至今,历时8~10年,对污染物的控制迅速纳入轨道,特别在“两控区”执行的总量控制,对特别污染地区提出了更高的要求。从表中可以看出:目前正在执行的“火电厂大气污染物排放标准”(GB13223—96)中制订的1200mg/m3排放浓度在国际标准体系中处于中等水平,即使与一些较为发达国家相比,如美国的SO2排放浓度限制并不宽松。这充分体现了我国控制二氧化硫排放和为全球环境保护作贡献的决心,但是也产生了需要高额环境保护投资费用的困难。
为了在对新建机组和现有机组的烟气脱硫建设项目的脱硫工艺选择中考虑到今后一段时间的SO2排放标准的可能发生的修订,从而有更为严格排放和浓度控制要求,我们必须对今后5-10年的排放标准的可能的变化作出预测,并在烟气脱硫系统的工艺中作出相应考虑,使得所采用的脱硫工艺不但能满足当前排放标准的要求,同时还应具有今后通过增加有限的投资来提高脱硫效率,以满足今后新的排放标准的可能变化的能力。
烟气脱硫技术的发展历史及现状
烟气脱硫技术的发展历史
从18世纪开始的工业革命以来,蒸汽机成为主要提供动力源的机械,煤也成为普遍使用的动力燃料。由于煤在燃烧过程中会产生许多污染物,如SO2、、、NOx、CO、CO2、粉尘以及一些有害的有机物质,因此煤的大量直接燃用造成了大气环境恶化。从19世纪末到本世纪中叶,一些主要的工业城市的空气质量越来越差,最后导致了大规模的空气污染事件等。
SO2是煤燃烧的直接产物,由于大量使用煤作为燃料使局部地区的SO2排放浓度已经远远超过了当地大气的自净能力,造成了严重的煤烟型污染,形成了会破坏生态环境的酸雨。
本世纪60年代,一些发达国家开始认识到对燃煤装置的烟气进行净化处理对于保护大气环境是至关重要的,并开始进行脱除烟气中的SO2以及其它污染物的研究。
实际上最早将烟气脱硫技术应用到燃煤电厂是英国。30年代,英国伦敦市的Bettersea电厂进行了在炉膛中喷入石灰石粉进行脱硫的试验,后来因为第二次世界大战的爆发,试验未能完成。烟气脱硫技术的真正发展始于1970年前后。首批安装烟气脱硫置的国家是美国和日本。当时由于开始实施对二氧化硫的控制标准,促使烟气脱硫技术的发展出现一个高峰。这时采用的FGD装置主要以湿式洗涤法为主。
从80年代开始,越来越多的国家和地区认识到燃煤时的SO2排放对人类健康和生态环境的危害性,因此这些国家和地区相继制定了控制SO2排放的标准和削减措施。这些标准和措施往往要求在一定时间内达到SO2的排放标准和削减量,如原联邦德国政府要求燃煤电厂在从1983年开始的5年内全部安装FGD系统,因此,从80年代的中期开始烟气脱硫技术得到了较快的发展。据统计,到1991年底全世界共有15个国家安装了FGD系统,装有FGD系统的机组的总容量为150GW。其中美国安装的FGD数量最大为273台,共81.5GW,德国174台,共41.7GW,日本45台,共13.4GW/。
从FGD发展的总的过程来看,可以分为三个阶段,或者说已经经历了三代FGD的技术发展历程。每一代FGD技术都有是为了适应当时的SO2排放标准而形成的,因而有其自身的特点。
现在FGD装置已得到越来越广泛的应用。至1998年底,全球使用的FGD装置约760套,半机容量为234GW。其中各类湿式装置约占80%,喷雾干燥装置约占10%,其其它各类工艺占10%。
全球安装FGD装置最多是的国家是美国、德国和日本。安装FGD系统的主要国家为工业发达国家,也有部分发展中国家。中国已10套FGD系统投入运行,装有4套石灰石—石膏湿法洗涤装置,2套炉内喷钙加炉后增湿活化(LIFAC工艺)装置,1套海水洗涤装置,一套简易湿法洗涤装置,1套喷雾干燥烟气脱硫装置和1套电子辐照烟气脱硫装置,总容量为2150MW。
美国的FGD技术有以下一些特点:
脱硫技术种类多由于国家疆域辽阔,因此各个燃煤电厂之间的脱硫条件的差异很大,很难用一种或几种FGD工艺来适应各种不同的电厂的要求:高脱硫率和低脱硫率的工艺均得到了发展
脱硫副产品的处理多采用抛弃法由于美国的土地资源比较丰富,对于固体废弃物的处置的限制比欧洲国家要少,加上其天然石膏资十分丰富,因此并不要求脱硫装置必须考虑脱硫副产品的综合利用。而脱硫产品的综合利用所需的投资和运行费用是很高的,因此大部分电厂均采用了抛弃工艺。据统计,在美国的231采用湿法的FGD装置中回收副产品石膏的FGD装置仅仅23个。
不装设烟气再热系统,以求简化系统美国的环境标准中没有提出对燃烧装置的最低排烟温度的要求。因此,在大气环境的最差扩散情况下不会对电厂周围地区的SO2的地面浓度造成超标的前提下,FGD装置一般不安装烟气再热装置,这是由于烟气再热器不但结构复杂、庞大,而且容易腐蚀,给运行和维修带来困难。另外省去烟气再热器可降低FGD投资的10~15%。
德国
德国地处欧洲中央,国土较小,对环境质量十分敏感,因此德国的排放标准的限制大大高于美国,法律规定脱硫副产物必须利用,固体废弃物的堆放要付出十分昂贵的代价。同时,由于天然石膏蕴藏量少、石膏销售市场大等具体情况,使德国FGD装置主要采用湿式石灰石/石膏工艺,这样既可达到很高的脱硫效率,又得到商业应用的石膏产品。
德国的FGD技术发展有以下特点:
FGD装置安装数量增加很快由于70年代初石油危机,迫使原联帮德国的燃煤电厂从原先主要衣靠石油和天然气转向以作为主要燃料。与此同时,也给德国的环境造成了严重的污染问题。1983德国制定的“大型燃烧装置法(GEFAVO)”规定了热功率300MW以上的燃烧装置的SO2的排放浓度不得超过400mg/Nm3,脱硫率必须达到85%以上,对于已运行的机组和新机组的限值要求相同。法规还规定了相应的达标期限,即要求在5年之内补装置脱硫装置或在2年内改用低硫燃烧煤。1983年仅有15%的发电机组容量装有脱硫装置,到1986年约有31%容量的机组装有脱硫装置,到1988年达到95%以上容量的机组装有FGD装置。
99%以上的脱硫装置采用湿法工艺原德国燃煤电厂运行的FGD装置中湿法工艺占有安装脱硫机组容量的99.4%,半干法喷雾干燥工艺占0.16%。这是由于排放标准要求安装的FGD系统必须有85%以上的脱硫率的结果。
90%以上的湿法脱硫系统为石灰/石灰石—石膏工艺德国的湿法FGD系统主要使用价廉、易于获得的石灰或石灰石作为吸收剂和可利用的石膏作为副产品。也曾有一些装置采用氨作为吸收剂,但由于氨的价格太高,未能获得推广。
副产品的综合利用率高由于德国的土地资源贫乏,因此固体废弃物的堆放费用非常高。这就要求烟气脱硫装置的副产品必须得以利用。经过长时间的努力,目前德国采用石灰/石灰石—石膏工艺的烟气脱硫的70%的副产品(石膏)已经得到了利用。据统计,到1995年75%的原联邦德国的工业用石膏是由燃煤电厂的烟气脱硫装置提供的。
安装烟气——烟气再热器德国的烟气排放标准要求烟气排放温度不得低于72℃,因此所有的湿法脱硫装置必须安装非常昂贵的烟气——烟气再热系统。这样使得德国的FGD装置的投资费用很高。
烟气通过冷却塔排放德国有一部分电厂的脱硫烟气不通过烟囱排放,面是通过冷却塔排放。这样做的优点是烟囱无须进行防腐处理。同时由于冷却塔的热释放量大,烟气的抬升高度比烟囱高,可以取消昂贵的烟气再热系统,节省了投资。
脱硫技术的发燕尾服从引进开始由于德国的排放标准要求现有电厂和新建电厂在很短时间内完成烟气脱硫系统的安装,这时德国的制造业界尚未作好充分准备,烟气脱硫技术的开发工作也落后于现实的需要。因此在被期,主要是从日本引进技术。经过消化吸收以及进一步的发展,目前德国的FGD技术的水平已经达到了很高的水平。
日本
二次大战以后,日本的经济得到了急速的发展,能源的消耗也急剧上升。
在石油危机之前,日本电厂的主要燃料为中东石油,中东石油的含硫量很高,造成了日本的大气污染十分严重,公害事件频频发生,便利日本成为世界闻名的公害大国。污染日趋严重的情况引起了日本政府和社会各界的高度重视。经过近几30年的努力,日本已由昔日的公害大国变成了环保先进国家,尤其是在SO2排放治理方面取得了举世瞩目的成就。
1972年日本安装了世界上第一台可商业化运行的烟气脱硫装置,此后烟气脱硫技术得到了长跑的发展,顾为世界上FGD制造商最多的国家之一。虽然日本的FGD技术发展很早,但是也受到其自身国土狭小,资源贫乏的影响,具有很明显的特点:
全部采用湿法工艺据统计,1995年日本共有48台烟气脱硫装置,其中湿法系统45台。
脱硫副产品的综合利用率很高由于日本的天然石膏资源匮乏,因此作为石灰石/石灰——石膏法的脱硫副产品——石膏得到了很好的利用。
脱硫技术大量输出日本的脱硫装置供应商很多,著名的有三菱重工、川崎重工、日立、荏原等。尽管日本国内的FGD的品种十分单一,主要是湿法工艺,但是在世界市场上日本的FGD装置制造商十分活跃,可提供各种类型的FGD装置。在中国市场上,上述这些制造厂分别以技术贸易、合作研究、示范工程等到形式介入到中国的脱硫项目中。日本政府也大力支持这些公司进入中国市场,向它们提供进出口贷款、政府贷款或合作研究项目经费等。
亚洲国家烟气脱硫技术的发展
近年来,亚洲各国经济得到了飞速发展,使得能源消耗急剧增加。在一些发展中国家,如印度、印度尼西亚、泰国、南朝鲜等,煤作为主要的一次能源的使用量正日益增加,与此同时,也加剧了这些国家大气环境的恶化。这些国家已经深刻认识到环境问题的严重性,纷纷通过制定和执行SO2排放标准来逐步控制二氧化硫的排放和酸雨的蔓延。
基于不同的国性情,各国控制二氧化硫污染所采用的政策和方法有所不同,有的正处于探索阶段。尽管采用FGD工艺来控制二氧硫排放的历程还处于起步阶段,但是许多国家的起点比较高。
根据资料表明:印度、印度尼西亚、泰国、南朝鲜、我国和我国台湾省都有FGD装置投入运行,特别是台湾省已安装FGD装机容量达2100MW,南朝鲜已有两台500MW的机组采用日本三菱重工技术的湿式脱硫装置投入运行,另外还有4台500MW机组的湿法脱硫装置在建设中。越南在其新建的河内电厂的两台300MW机组上也从美国公司引进了石灰石—石膏湿法烟气脱硫装置,而其锅炉的含硫量仅为0.3%。
这些情况表明,随着人们对生活质量要求的不断提高,烟气脱硫将与电除尘器一样成为发电机组的必须的生产设备和环保设备。
烟气脱硫技术的发展趋势
烟气脱硫技术经过30年的发展和大量使用,其中一些工艺由于技术和经济上原因被淘汰了,而另一些工艺,如石灰石—石膏湿法、喷雾干燥法、炉喷钙加炉后增湿活化工艺(LIFAC)和烟气循环流化床(CFB)得到了发展,逐步趋于成熟,称为了主流工艺。这些工艺有以下的特点:
—高脱硫率目前,经优化设计的湿法工艺脱硫效率可以达到95%以上,喷雾干燥工艺可达到85%~90%,改进的LIFAC工艺可达到80%,CFB工艺可在与湿法工艺相同的吸收剂的利用率条件下达到90%~95%的脱硫率。
—高可利用率由于对脱硫过程化学反应机理的深入理解,使地反应过程有更合理的控制和对结构材料的正确选择,以及脱硫装置制造厂严格的质量控制,使得脱硫系统的可利用率已经达到了很高的水平。据统计,湿法脱硫系统的可利用率已经达到98%以上,有的制造商甚至可承诺100%的可利用率。也就是说,可以保证和锅炉同步运行。
—工艺流程简化原本工艺比较复杂的湿法脱硫工艺最近十年来得到了很大程度的简化。从原来的三个塔体减少到单塔,取消了备用塔。有的工艺采用了塔内烟气流速很高的设计,使得塔体体积大大减小。同时单塔所能处理的烟气处理量增大。湿法单塔最大烟气处理量已经达到850Nm3/s,相当于600MW机组。并较多趋向于采用结构简单、压降小的空塔结构。
—系统电耗降低脱硫系统本身的电耗过大曾经是困扰电厂的一个问题。在70—80年代,湿法脱硫工艺电耗一般要达到3~4%。由于强调了节能设计和脱硫系统本身的简化,目前先进的湿法脱硫工艺的电耗大约在1.5%,这样就大大降低了系统的运行费用。
—降低投资和运行费用由于脱硫系统流程的简化以及设计参数的优化,在最近几年内,烟气脱硫系统的投资费用有了明显的降低。90年代初湿法脱硫系统的投资约占电厂投资的15%以上,而目前国内湿法烟气脱硫系统的投资仅占电厂投资的10%左右。
—各种SO2/NOx复合工艺的出现和使用由于发达国家大气污染物排放控制的重点已经转向氮氧化物的控制,许多燃煤电厂被要求安装脱硝装置以降低氮氧化物的排放。因此,一批新的可同时解决燃煤SO2和NOx达标排放的烟气处理工艺已经得到了应用
烟气脱硫工艺的分类
我们按照吸收剂和脱硫产物的状态进行分类,一般可以分为三类:湿法、半干法和干法工艺。
定义:
湿法烟气脱硫工艺:吸收剂以浆液状态进入吸收塔(洗涤塔),脱硫所产生的副产品是湿态的工艺流程称为湿法烟气脱硫工艺。
半干法烟气脱硫工艺:吸收剂以浆液状态进入吸收塔(洗涤塔),脱硫所产生的副产品是干态的工艺流程称为湿法烟气脱硫工艺。
干法烟气脱硫工艺:吸收剂以干粉状态进入吸收塔,脱硫所产生的脱硫副产品是干态的工艺流程称为湿法烟气脱硫工艺。
主流烟气脱硫技术
“主流烟气脱硫技术”是指那些发展历史长,使用台套多,而且在大容量机组(≥100MW)上有较多实际业绩的工艺。其工作原理、工艺特点及优缺点。
选择脱硫工艺时,要考虑其性价比,既要满足符合排放标准的脱硫率,又要考虑改造费用。
烟气脱硫系统按脱硫率来分主流脱硫工艺:
——低脱硫率,≤70%,主要为炉内喷钙,管道喷射工艺;
——中脱硫率,70—90%,主要为喷雾干燥工艺,CFB工艺,LIFAC工艺和电子束辐照工艺;
——高脱硫率,90%以上,主要是湿式洗涤工艺,如石灰石—石膏,镁加强石灰工艺等。
逆流塔在大部分设计中均为内部是空的,叫空塔,但有些设计中安装了一些带孔的托盘有的采用了一个漏斗隔板等,主要是为了增加气液的接触面,或者是便于反应的控制。
塔内从上到下布置了除雾器、喷淋联箱,烟气入口和浆池。烟气经由气-气交换器降温后从浆池上面的烟气入口进入吸收塔,与喷淋层喷下的液滴逆流混合,吸收烟气中的SO2。洗涤后的烟气通过除雾器除去液态雾滴,再经过烟气交换器加热后通过烟囱排出。
制备好的石灰石浆液补充到浆池中,由循环浆泵送到喷淋层。喷淋层由2~4层或更多层的喷嘴组成,每层上的喷嘴的布置都经过特殊设计使得喷嘴喷出的浆液能均匀地覆盖吸收塔的断面。
吸收SO2之后的液滴返回到浆池中,液滴中的反应产物以亚硫酸钙为主,其中一部分由烟气中的氧气氧化成硫酸钙。如果工艺需要产生商品石膏,那么在浆池中还要布置氧化风机或压缩空气喷嘴,把空气鼓入浆液中使浆液中的亚硫酸钙氧化成硫酸钙。
为了保持浆液中硫酸钙的平衡不致浓度过高析出,形成结垢,必须从浆液池中抽出部分浆液。这部分浆液经一级旋流脱水后,成为含固量为40~50%的厚浆,再经脱水机或离心脱水机,使脱硫产物中的含水量降低到10%左右。经脱水脱硫产生主要成份是二水石膏。
烟气脱硫技术指标
为了对各种烟气脱硫工艺进行技术上分析和比较,必须首先明确那些是烟气脱硫系统的主要技术指标,这些指标的意义是什么,这些指标的变化对于电厂方面会带来什么影响。只有掌握了这些住处才能在脱硫工艺选型过程中做到突出重点抓住关键。
在进行各种脱硫工艺的性能比较时,下列技术指标十分重要的:
1) 脱硫率;
2) 吸收剂的利用率;
3) 吸收剂的可获得性和易处理性;
4) 脱硫副产品的处置和可利用性;
5) 对锅炉和烟气处理系统的影响;
6) 对机组运行的影响;
7) 对周围环境的影响;
8) 占地大小;
9) 流程的复杂程度;
10) 动力消耗;
11) 工艺的成熟程度;
12) 总的投资和运行费用;
脱硫率
脱硫率的定义:
脱硫率=(脱硫前烟气中SO2浓度-脱硫后烟气中的SO2浓度/脱硫前烟气中的SO2浓度
脱硫率的高低表示脱硫能力的大小。对于电厂来说,安装烟气脱硫系统的唯一目的就是脱除烟气中的一部分SO2,以满足排放标准的要求。因此脱硫系统必须有足够高的脱硫效率。
在进行脱硫工艺选择时应对脱硫率作以下考虑:
—该脱硫工艺在锅炉正常运行(包括各种负荷条件下)所能保证的最低脱硫。
尽管脱硫效率的定义十分简单,但是实际的考虑还是十分复杂的。因为许多FGD供应商在介绍或报价时,有意或无意地不加任何条件地说系统的脱硫效率可达到多高,例如可达到90%以上。实际上,脱硫系统的脱硫效率是由很多因素决定的,除了系统本身所采用的工艺的脱硫能力外,还取决于烟气的状况,如:烟气量、烟温、烟气中的含水量等。而SO2的浓度或总量在任何情况下均不得超过规定的控制值(如“火电厂大气污染物排放标准”GB13223-1996)。因此,在选择脱硫工艺,以及在此后工程的合同中均应保证:在锅炉的最差工况下,脱硫系统保证的最低脱硫率仍能满足排放标准的要求。
—系统脱硫的确定应在各种工况下均能满足当前国家和地方所规定的允许排放浓度和排放量:并优先考虑选用那些有可能通过简单改造来进一步提高脱硫率的工艺,以满足未来可能的更严禁严格的排放标准的要求。
由于脱硫系统的投资和运行费用均很高,因此脱除每一吨SO2的成本也很高,在当前中国的条件下,利用烟气脱硫装置每脱一吨SO2的成本大约在1500无以上,要比规定的SO2排放费200元/吨高好多倍。因此,在没有实行“排放权交易”制度情况下,燃煤电厂的脱硫系统一般不会在低于排放标准控制值的状态下运行。
但是,排放标准的不断修订,允许的SO2排放浓度或总量会有所下降,排放收费将会越来越昂贵,这也是必然趋势。因此在为脱硫系统选择脱硫工艺时,充分考虑到这种趋势是明智的和前瞻性的。实际上,在考虑如何满足未来排放标准的要求时,可以有两种做法:
—在设计脱硫系统时留有充分的脱硫能力的裕量;
—选择那些经过简单的改造即可提高系统脱硫的工艺。
如果单纯采用第一种方法会增加脱硫系统的投资和当前的运行费用,如果能在选择工艺时做到未雨绸缪,优先选用脱硫效率可“升级”的工艺,那么,可以减少未来的投资,延长烟气脱硫系统的寿命。实际上符合这种要求的工艺是存在的。例如炉内喷钙加炉后增湿活化工艺可以分三步实施:
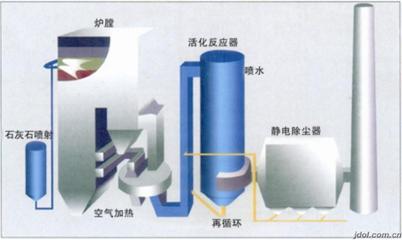
如果只用炉内喷钙可以满足排放标准,可以先只安装炉内喷钙部分,这时的脱硫率约为30%,这部分的投资仅占完整系统的投资的20%左右;
在排放标准趋严后可增加一个炉后烟气活化塔,将脱硫效率提高到75%。这部分投资约占总投资的60%;
如需要进一步提高脱硫效率可增加一套再循环灰的湿化处理系统,将脱硫效率提高到85%。这部分的投资约占到总投资的20%。
其它还有一些工艺也具有类似的特点,如电子束辐照烟气脱硫工艺可以通过增加电子枪的方法来提高脱硫效率。
—考察一种脱硫工艺的脱硫率时,必须了解此脱硫率是在什么条件下,例如在多少钙硫比(或钙的过剩率)的条件下达到的;
—一般情况下,供应商所给出的是针对锅炉燃用给定煤种时的脱率效率。
钙硫比
钙硫比的定义:
Ca/S=参加脱硫反应的钙吸收剂的摩尔数/原烟气中的SO2的摩尔数
有些国外供应商对钙硫比的定义为参加脱硫反应的钙吸收剂的摩尔数与已脱除的烟气中SO2摩尔数之比。因此在了解钙硫比时,必须明确其定义,并折算到相同的定义下来进行比较。
烟气脱硫副是烟气中的SO2与吸收剂反应,生成稳定的、不易分解的、无害的脱硫副产品的过程。对于使用钙基吸收剂的烟气脱硫工艺,SO2气体被吸收剂吸收的基本化学反应式可表述如下:
干法:CaO+SO2+1/2O2→CaSO4
半干法:Ca(OH)2+SO2→CaSO3"1/2H2O+1/2H2O
湿法:CaCO3+SO2+1/2H2O→CaSO3"1/2H2O+CO2
从上面的化学反应式可以看出:无论是干法、半干法、还是湿法工艺只要有一外钙基吸收剂分子理论上就可以吸收一个SO2分子,但实际上由于反应时的传热传质的条件并不是处于理想状态,因此往往需要增加吸收剂的量来保证吸收过程的顺利进行,即在实际的吸收过程中,钙基吸收剂的分子数要大于SO2的分子数。钙硫比就是用来表示在达到一定脱硫时所需要的钙基吸收剂的过量程度。
很显然由于湿法工艺中的反应是在气相、液相和固相之间进行的,反应条件十分理想,因此湿法工艺的钙硫比(Ca/S)非常接近于1,一般为1.05左右,而干法和半干法的钙硫比要高得多。
从原理上看:适当提高钙硫比可以一定程度地增加脱硫率。例如炉内喷钙工艺在钙硫比利时3时可以达到30%的脱硫率,如果提高钙硫比达到5,则脱硫效率可以达到40%~50%。同样,对于半干法和其它一些脱硫工艺都有相同的结果。因此在考察一个脱硫工艺,或者进行不同脱硫工艺的脱硫性能比较时,必须注意达到该脱硫率所需的钙硫比数值。在相同的脱硫率下,钙硫比高的脱硫工艺的运行费用高,因为需要消耗更多的吸收剂,和处理更多量的脱硫产物。
吸收剂的利用率
吸收剂利用定义:
吸收剂的利用率是用来表示在脱硫系统中被用来脱除SO2的吸收剂的重量占加入脱硫系统的吸收剂的总量的百分比。它可以用下式表示:
吸收剂利用率(%)=脱硫效率/钙硫比(%)
例如,对于某应用钙基吸收剂的脱硫装置其脱硫率为80%,相应的钙硫比为2,在这种工况下,钙的利用率为:
钙利用率(%)=80/2=40%
40%的钙基吸收剂参加了吸收SO2的反应,其余的吸收剂作为副产品的一个给份排出了脱硫系统。
吸收剂的利用率与钙硫比有密切的关系,达到一定的脱硫率时所需要的钙硫比越低,钙的利用率越高,也就是说,所需要的吸收剂的数量以及所产生的脱硫产物也越少。这样可以大大降低脱硫系统的运行费用。
在主流烟气脱硫工艺中,湿法的吸收剂利用率最高,一般可以达到90%以上,半干法在60%左右,而干法中的炉内喷钙工艺最低,约在30%以下。
石灰石用作吸收剂时必须先要磨成粉末。由于石灰石无毒无害,在处置和使用过程中十分安全,因此是烟气脱硫的理想吸收剂。但是,在选择作为吸收剂的石灰石时必须考虑以下二点:
—石灰石的纯度,即CaCO3的含量;
—石灰石的活性。
石灰石中CaCO3的含量越高,就表明石灰石的有效成份越高,如果石灰石中CaCO3的成份很低,那么就必须使用更多的石灰石作为吸收剂,这样不但增加石灰石的费用,同时还会增加石灰石粉和脱硫副产品的处理量,结果会增加设备容量和运行费用。对于石灰石—石膏湿法工艺来说,还会因为吸收剂纯度过低使脱硫副产品—石膏中的杂质含量过高而降低质量。
石灰石的活性对于作为吸收剂的石灰石来说是一个特殊的、但同时又是十分重要的性质。这个物性在选取石灰石作脱硫剂时往往会被忽视。石灰石的活性是指石灰石吸收剂在与SO2发生反应速度。这主要取决于石灰石粉的颗粒度和石灰石粉颗粒的表面积。石灰石粉颗粒的表面积主要取决于石灰石的生成年代与晶体化程度。生成年代越近、晶体化程度越低的石灰石制成粉后的活性越高。因此,为了得到有高活性的石灰石粉作为吸收剂,必须在选择石灰石矿源时对各种石灰石的脱硫活性进行试验。在纯度相同的情况下,活性高的和活性差的石灰石粉在达到相同脱硫率的情况下,其用量差达10%。对于每年用量达几万吨的大型FGD装置来说,选择活性高的石灰石矿源可以节省很大运行费用。